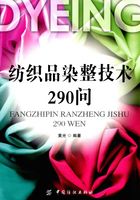
53.如何控制丝光工艺参数的稳定性?
答:丝光工艺条件及参数的不稳定,对织物染色的影响非常明显,如轧碱槽碱液浓度的大幅波动、生产加工过程中车速的忽快忽慢,都会影响棉纤维的丝光效果,并由此造成织物染色色差。
丝光工序对染色产生影响的主要因素为:丝光效果的差异、织物带碱的差异、织物幅宽的差异等。
(1)烧碱浓度对丝光效果的影响:丝光碱浓度对织物丝光效果的影响是很大的,烧碱浓度高,则丝光效果就好,一般丝光轧碱槽的烧碱浓度控制在220~270g/L,由于烧碱对棉纤维的直接性,织物经过轧碱槽时所带走的烧碱比例要大于轧槽内的烧碱浓度,因此,高位槽内的配碱浓度必须高于轧碱槽内的烧碱浓度才能保证轧碱槽内的碱浓度达到工艺要求。高位槽的烧碱浓度一般控制在高于轧液槽中烧碱浓度30~50g/L为宜。
丝光碱浓度越高,织物脱碱压力越大,织物脱碱不匀的概率越高,因此,碱浓度越高,越应重视织物脱碱的效果。
(2)织物差异对丝光效果的影响:粗厚织物、紧密织物、环纺纱织物丝光时对碱的渗透性要差一点,在制订丝光工艺时要作适当调整,增加渗透剂,降低车速,延长绷布辊上织物的带碱时间都有利于降低表面丝光现象的发生。
同理,粗厚织物、紧密织物、环纺纱织物的脱碱难度也比稀薄织物大,渗透到纤维内部和里层纤维之间的烧碱清除也不容易,织物带碱的可能性增加。
(3)丝光车速:丝光车速太快则烧碱的渗透时间缩短,渗透性必然降低;扩幅时间缩短,扩幅过程中,局部张力加大,容易出现掉铗、高堂疵布;水洗时间缩短,水洗压力增大,容易出现脱碱不净、不匀的现象;车速加快,织物经向张力增加,产生皱条的概率增加。
(4)均衡供料:均衡供料是保证丝光效果稳定性和一致性最基本的要求,前后供料出现波动,则织物的前后丝光效果必然会有所差异,染色时将产生前后色差;左右供料不匀,染色时织物将出现左右色差。
丝光过程中,要严格控制织物前后带液率的差异和轧辊整幅带液的均匀度,补充碱液的齿形溢流槽应全幅均匀加入,采用循环泵和过滤器设施的轧碱槽内浓度比较均匀。严格控制工作液槽的液位,最好采用自动加液,否则均匀加液将变成空谈。
(5)张力控制:丝光过程中如果不对织物施加张力,则纤维只有溶胀,而没有排列上的梳理。因此,上染率可提高,而织物表面光泽度则没有提高,体现不出“丝光”的特征。
经向张力过大,容易造成经向的受力不匀,加上设备上平行度的差异,织物在运转过程中出现皱条的概率增加,适当增加织物的柔软度,能够降低生产过程产生皱条的概率。
(6)水洗脱碱:织物经丝光后pH不稳定,即丝光后织物的去碱不净、水洗效果差或者不稳定,也会对织物染色产生不良的影响。尤其在生产涤/棉染色织物和对碱较为敏感的活性染料染色时,pH偏高或者不稳定,会使织物染色后色光变化加大,造成色光萎暗、色相不稳定、明艳度较差,使织物符样率大大降低。
半制品带碱对乙烯砜和双活性基团染料的染色产生很大的不稳定因素,用于活性染料轧染的半制品,布面、布芯都不能含碱,pH控制在为7±0.5时比较适宜,并且要烘干,保证含湿一致。
水洗的目的是除去织物上的带碱,目前丝光后的水洗,除直辊去碱槽外,高效水洗箱增加到了5~7个,但丝光织物还是存在带碱问题,因此,丝光后只用水洗去碱的办法并不是最科学和最经济的方法。
丝光水洗要注意以下问题:
①加强织物在脱铗前的去碱,用加热的淡碱进行五冲五吸,要保证其去碱的一致性和去碱的有效性。
②水洗槽要采取逐格溢流,提高水洗温度对去碱效率有很大的提高。
③将丝光织物酸洗一遍后再染色,能较好地解决织物带碱的问题,但生产成本有所增加。
④在丝光设备上采取酸洗措施是去碱最经济和最有效的办法之一,而酸洗最关键的问题是如何保证织物去碱效果一致性的问题。
(7)门幅控制:对于稀薄织物来说,丝光后织物的门幅要达到工艺要求往往比较困难,生产过程中可以从三个方面来改进:一是在织物脱离布铗前加强去碱,保证五冲五吸的实际效果,冲洗的淡碱要加热;二是适当降低丝光碱浓度,增加布铗宽度,降低车速,防止织物脱铗破边;三是适当降低洗水部分的张力,减少门幅收缩。
(8)轧辊要求:丝光机两台浸轧碱液的重轧车如果带液率不匀将会给染色工序造成严重的质量问题。要经常保持辊面平整,两根橡胶辊必须车成中高(1.0~1.50mm)形,以抵消轧辊在重压下产生的挠度。保证织物均匀一致的带液量是对所有轧辊最基本的要求,当然,染色机的均匀轧辊则是例外。
将进布铗前面的轧辊换成高效轧辊,能有效地降低织物的带碱量,从成本和去碱效果等诸多方面来考虑都是值得改进的。