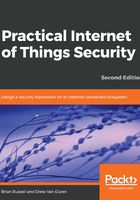
Smart manufacturing
The term Industry 4.0 is used to describe CPSes that enable smart factories through automation and data exchange. Sensor data is fused and processed by data analytic systems, and machine learning algorithms are trained on smart manufacturing use cases such as remote monitoring and control, smart energy consumption, predictive maintenance, and human-robotic collaboration. These capabilities provide business value through the minimization of downtime or the optimization of processes and reduction of costs. For example, a Jeep Wrangler production facility in Toledo, Ohio, introduced connectivity for over 60,000 IoT endpoints and 259 robots on the assembly line (source: https://customers.microsoft.com/en-us/story/the-internet-of-things-transforms-a-jeep-factory). This implementation provides flexibility to modify manufacturing plans on demand, based on real-time data collected from sensors. The result is cost reduction and profit increase.
Industry 4.0 is also leading the way toward the adoption of robotics within manufacturing. There are many types of robotic platforms, including vision-capable robots, that can capture and analyze video streams in real time, and collaborative robots that can be guided by humans toward accomplishing a task. Robotic systems rely on many types of sensors, including motion sensors, accelerometers, temperature sensors, pressure sensors, and proximity sensors. These platforms can incorporate computer vision capabilities and make use of complex algorithms that support guidance and path planning.