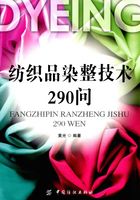
35.如何对前处理质量进行有效控制?
答:前处理的质量问题具有很大的隐蔽性和滞后性,因此,前处理的质量只能通过加强工艺管理来实现,建立“机台自查、班组检查、技术中心抽查”的三级工艺监督体系,使所有的工艺参数都处于可控状态是前处理质量控制最基础的工作。
(1)染色对前处理半制品的质量要求:染色布最基本的质量要求是左中右颜色一致,前后批次的颜色一致,布面颜色均匀而饱满。染色时,条件稍有变化即会在颜色上反映出来,技术人员可根据颜色变化及时纠正工艺偏差,而前处理的条件变化很难察觉,然而就是这些察觉不到的变化,在染色时就能造成颜色上的波动和其他瑕疵的产生。
过去普遍对半制品质量要求是透和匀,白度和毛效是一种模糊的概念,而现在对成品色差4.5级的要求,则需要对前处理工艺条件和操作要求与染色工序同样进行严格控制,而且由于它的不易察觉性和呈现的滞后性,更需要在操作上严格按工艺要求加以控制,确保半制品生产工序的各项工艺参数的前后一致性和稳定性。
半制品要求前处理匀和透,半制品加工条件稍有变化,便会在染色色泽上反映出来。同一品种也可能因坯布产地、上浆品种、上浆率、棉花品质和配棉、纺织厂生产工艺不同,造成半制品品质不同。
平时所强调的织物半制品前处理效果好,并非只是讲退浆除杂净、毛效高、白度好,而首先要强调的是“匀”,也就是指半制品质量的一致性和稳定性。
在生产过程中,设备状态、工艺条件以及工艺参数等因素的波动,都会影响织物半制品质量的一致性。水洗轧车的左右压力差异较大或轧辊凹心严重,都会造成织物两边和中间水洗效果有较大的差异,染色时则会因织物毛效、白度不一致,导致织物左中右色差。同样轧料轧车的左右压差或凹心会造成织物两边和中间的轧液率不一致,使织物染色后出现色差。
在前处理工序中化学和助剂的追加量不均匀、水洗温度忽高忽低、车速忽快忽慢都会导致前处理半制品毛效、白度的不一致,进而造成织物前后色差。特别是直接性高的染料,则更容易产生色差,即使是直接性不太高的还原悬浮体、涂料、分散染料也会因为渗透性和扩散性的差异而产生明显的色差,因为毛效高的半制品吸湿性较好,上染率较高,得色就深;而毛效低的半制品吸湿性较差,上染率低,得色浅,由此造成织物在染色时上染率不匀而产生色差疵布。
需要强调的是,待染半制品白度不一致,也会对织物的色光造成很大的影响,在生产漂白和染鲜艳的浅色品种时,则更加明显。生产过程中经常会遇到小样与大样工艺差别很大的主要原因就是半制品的差异所造成的,生产过程中反复强调要用待染半制品放样也就是这个道理。
织物前处理效果好,退、煮、漂做到匀、净、透,毛效、白度一致,丝光足,pH稳定在6.5~7.0,这是织物染色成功的根本所在。必须强调的是,染同一颜色的织物,要用相同的前处理工艺,并尽量选用同一厂家的坯布。另外,染浅色和染鲜艳色时,要尽量选择白度一致的染坯,因为染色坯布的白度决定了染色成品的色光。
(2)前处理要点:纯棉织物前处理的基本要求可概括为“匀、透、净、白”四个字。
①匀:是指煮练均匀,织物匹与匹之间毛效基本一致。
②透:是指煮练充分,无“夹生”现象。
③净:是指煮练后棉纤维上的果胶、棉蜡、灰分、棉籽壳等杂质被充分去除。
④白:是指经过前处理,织物已具备染色需要的白度,而不是指越白越好。
并不是所有的颜色都需要染前漂白,但是织物底色的白度会影响颜色的重现性,所以,“白”还要求经过煮漂后的织物有均匀一致的白度。
“匀、透、净、白”只是对半制品质量要求的一个基本概括,实际生产中则需要通过具体的检测手段来检验和控制半制品的质量。
(3)前处理工序中几个关键问题:
①碱与酸可以用于淀粉浆料的退浆,但对PVA浆料的退浆效果是很不理想的。
②棉籽壳和杂质是通过碱煮使其发生溶解或溶胀而脱落,而织物上的色素则是依靠漂白工序完成的,前处理工艺要采取重煮轻漂的原则,尽可能降低织物的强力损失。
③白度是双氧水(或其他漂白剂)漂白的,但退浆不尽,煮练不透,退浆、煮练过程中的再沾污会影响织物的漂白。
④氧漂工序中出现的针眼破洞主要是重金属离子造成的,而很少是因为金属氧化物分子造成的,这些重金属离子中,铁离子又是最主要的。酸洗是除去织物上所含重金属盐最有效的方法之一,从而可以降低或除去织物上带来的重金属离子。螯合剂是屏蔽漂液中重金属离子最有效的方法之一,以达到降低重金属离子对双氧水的催化而产生无效分解,螯合剂在不同的pH条件下其对金属离子的螯合能力是不同的,在实际生产中这一点值得重视,很多针眼破洞往往是因为忽视了这一因素而造成的。
⑤硅酸钠和各种螯合剂可以去除一部分金属离子,但不同的工艺条件应选用与其相适应的络合剂,漂液中pH对络合剂的络合效果影响是非常大的,不同的络合剂最适宜的pH区间各有不同,同一络合剂针对不同的金属离子,其最佳pH范围也是不同的,在选择和使用络合剂前,一定要对络合剂性质和工艺条件有所了解,否则络合效果不好,易产生破洞。