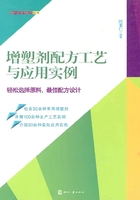
1.6 三羟甲基丙烷
一、综述
三羟甲基丙烷又名三甲醇基丙烷或2,2′-二羟甲基丁醇,简写为TMP。外观为无色或白色结晶粉末,无臭、有甜味,易吸潮,吸湿性约为甘油的50%。密度134.17g/cm3,沸点292℃,熔点61℃。TMP易溶于水、乙醇、甘油、低碳醇、N, N′-二甲基丙烯酰胺等,部分溶解于乙酸乙酯和丙酮,微溶于四氯化碳、乙醚和氯仿,但不溶于脂肪烃和芳烃、氯代烃。
三羟甲基丙烷是一种稳定的三元醇,对人和动物基本无毒,对皮肤也无刺激性。
二、生产技术
生产实例一:醛加氢还原法
醛加氢还原法于20世纪70年代开始研究开发,80年代实现工业化生产。由正丁醛与甲醛在三烷基胺(如三乙胺)催化作用下反应得到羟醛缩合产物2,2′-二羟甲基丁醛,然后在催化剂存在下,2,2′-羟甲基丁醛在115℃、6MPa条件下进行水相加氢反应,水和过量的三乙基胺通过真空蒸馏分离出去后,加入甲醇形成甲酸甲酯,在10~200℃条件下可将其分离出来,最后得到产品。对2,2′-二羟甲基丁醛进行水系加氢生产TMP。
在羟醛缩合时,主要采用三乙基胺做催化剂,用三乙基胺做羟醛缩合反应的催化剂,能控制反应的选择性,抑制副反应的发生,减少甲酸盐的生成。水系加氢催化剂主要是分布于载体上的镍或氧化镍,以氧化铜或铜-铬为助催化剂。
该法甲醛利用率高,加氢技术性强,可以节省大量的甲醛和碱,副反应产物相对较少,产品质量好,提纯精制较为简单,设备少,生产成本低,但需加氢装置,采用高压设备,对加氢设备和催化剂要求较高,生产技术要求也较高,比较适合大规模的连续化生产。目前欧美国家的一些TMP生产厂家主要采用此法进行生产。
催化氢化法的第一步与康尼扎罗反应法基本相同,也是醇醛缩合反应。只是选择的缩合反应的催化剂有所不同。若用NaOH做催化剂,用量少,所需反应温度低,但易引发坎尼查罗、基辛科等副反应,即使生成少量的钠盐,也将会影响到后一步的催化氢化反应,因为钠盐在镍基催化剂中的积累是使后者活性下降的主要因素。德国巴斯夫(BASF)公司采用叔胺,如三乙醇胺做醇醛缩合反应的催化剂,控制反应选择性高,可抑制副反应。则采用离子交换树脂做缩合反应的催化剂,由于催化剂可以循环使用,在大规模生产中可大大降低成本。
第二步为催化加氢反应,即对2,2′-二羟甲基丁醛进行水系加氢生成三羟甲基丙烷,根据目前发展的一些专利来看,催化氢化的温度一般在200℃以下,压力在5~10MPa左右,使用的催化剂主要是分布于载体上的镍或氧化镍,以氧化铜或铜-铬为助催化剂,日本三菱公司最新报道采用Cu-Zn-Zr催化剂具有高活性和使用寿命长等特点。
催化氢化法可以节省大量的甲醛和碱,副反应产物相对较少,提纯精制较为简单,设备少,成本低。但对加氢设备和催化剂要求较高,比较适合大规模的连续化生产。
生产过程为:将甲醛、正丁醛和三乙胺送入高压釜中,在90~95℃氮气氛中反应20min,反应完成后,在0.2MPa压力下除去反应产物中的甲醛、水和三乙胺,然后把浓缩物加入装有Kaney镍催化剂的加氢反应器中,在3.0MPa氢压和100℃下反应。加氢完毕,冷却分离催化剂。溶液经离子交换树脂处理后,减压蒸水得TMP产品,收率99%,纯度99.40%。
催化加氢法第一步和康扎罗尼路线基本相同,为了提高产品质量和保证加氢的顺利完成,因此国外生产与研究中缩合反应所选用催化剂一般是三乙胺或阴离子交换树脂;第二步催化加氢反应,反应条件为温度200℃左右,压力5~10MPa,加氢催化剂一般选用NiO-Al2O3体系、Cu-Cr体系、Ni-Cr体系或Cu-Zn-Zr体系等。其中德国巴斯夫公司就采用催化加氢路线在路德维希港建有2万吨/年的工业化装置。催化加氢路线作为新发展起来的技术,与康扎罗尼路线相比可以节省1/3的甲醛和大量的碱,副产物少,提纯精制容易,产品质量好,工艺路线紧凑,无三废产生,加氢催化剂寿命一般为2~3年,适合大规模工业化生产,是非常具有发展前景的合成路线。
这种方法适用于小批量间歇化生产。它的缺点是:
①为使反应完全,采用甲醛过量三倍的办法,甲醛消耗过高,致使成本提高;
②副产甲酸钠多且销路不畅;
③由于生成了与TMP几乎同等量的甲酸钠,致使分离操作变得比较复杂。从反应生成液中分离TMP和甲酸钠是生产工艺中的关键的一步,即使TMP粗晶中混有少量的甲酸钠,精馏精制时也会引起TMP的严重分解,从而降低TMP晶体的产量和质量。用Ca(OH)2代替NaOH,其产率虽然不及用NaOH高,但粗晶收率仍可达到70%,而产品纯度比用NaOH制得的高,重要的是副产物是以甲酸钙的形式存在,比较容易除去。采用三氯甲烷重结晶一次能制得精晶,其收率可达60%左右。
该法具有醛利用率高、节省原料、副产物少、产品质量好等特点。同时其产品提纯精制较为简单,所需设备较少,这些都大大降低了生产成本。但此工艺加氢过程需要高压设备,且对催化剂的要求较高,因此目前只有欧美一些国家的TMP生产厂家主要采用此法进行生产,未得到广泛的推广。最近德国巴斯夫公司曾对外宣称其新建在路德维希港生产区的TMP装置开始投入生产并采用了独特的加氢工艺,由于采用了此独特的加氢工艺使产品的纯度特别高,并且生产过程中没有盐类副产,同时新工艺使产品能耗大大降低,原料甲醛用量减少了三分之一。
生产实例二:三羟甲基丙烷的制备
将216g正丁醛、1.2kg甲醛(浓度30%)、450g三乙胺投入装有搅拌器、温度计的三口反应瓶内。再加入1kg水,搅拌均匀后,将液温加热到70℃,在70℃下反应4h后,再在2kPa下减压蒸馏脱水,脱除游离的三乙胺与生成的三乙胺甲酸酯(沸点110℃、2.7kPa)。向残余液中加入等量的水,在120℃、6MPa下连续氢化(加氢催化剂为Cu与Al原子比为0.75∶1的CuO与A12O3复合体),在沸点153℃、0.4kPa下蒸馏得三羟甲基丙烷(TMP)。产物按正丁醛计,收率85%;副产双三羟甲基丙烷(沸点185℃、0.4kPa) 28g,按正丁醛为原料计,收率76%。
生产实例三:制备高纯度三羟甲基丙烷
向装有悬吊式搅拌器、惰性气体吹洗装置和回流冷凝器的三颈圆底反应瓶中,投入正丁醛1069.3g、多聚甲醛1223.4g、水132.4g和三乙胺75g。将反应瓶置于50℃温度的水浴中,用2h时间将浴温升到80℃,直到99%以上的正丁醛反应掉。用甲醇稀释产物,使甲醇溶液中醇醛缩合反应产物的含量为50%(质量分数)。控制操作条件为温度160℃、液体空速0.5h-1、压力6.9MPa的氢压。采用使醇醛缩合产物的甲醇溶液向上穿过亚铬酸铜固定床的方法进行连续加氢。然后用长度为0.2m的填充柱将加氢产物进行间歇蒸馏,回收高纯度的三羟甲基丙烷产品。纯度99.18%,回收率73.3%。
三、应用技术
增塑剂在塑料及薄膜中的应用
应用实例一:三羟甲基丙烷酯
向配备搅拌器和冷凝器的2L的四口玻璃圆底烧瓶内加入268.36g的三羟甲基丙烷、576.84g的2-乙基己酸、366.39g的苯甲酸与5050g的二甲苯作为带水剂及2.83g的酞酸四异丙酯催化剂混合物,将液温提升到220℃,在此温度下反应10h,反应完成后,在2mmHg真空、200℃下脱除未反应的酸,之后用5%的氢氧化钠液水洗和干燥得三羟甲基丙烷混合酯,加入吸收剂过滤得成品。
将所得的三羟甲基丙烷酯增塑剂的混合物60份,钙锌稳定剂3份,硬脂酸0.2份与聚氯乙烯树脂100份混合,在辊轧机内于165℃预热3min,再加热3min至185℃并在此温度下冷却,制成1mm厚的板材。
应用实例二:三羟甲基丙烷复合酸酯
向配备搅拌器和冷凝器、氮气导管、水分离器、接触式温度计、回流冷凝管的四口玻璃圆底烧瓶内加入464.1份的三羟甲基丙烷,464.1份的苯甲酸和440.7份的月桂酸和120份的二甲苯为带水剂及钛酸四异丙酯TETRA3.4份催化剂。将混合物在190℃下回流搅拌反应25.5h之后,分出水103份。在190℃和3MPa条件下反应3h得产物,检测分析酸值。
应用实例三:三羟甲基丙烷三苯甲酸酯
向装有四流冷凝器、分水器、温度计、搅拌器、取样管的500mL四口瓶中,按苯甲酸∶三羟甲基丙烷摩尔比为3.35∶1的比例投料,再加入微量阻聚剂对苯二酚及占总量1%的对甲苯磺酸和1%的磷酸,加热至回流。在分水器中不断有水珠生成。当分水器中无水珠生成,反应液温度不再上升时,停止加热。放出分水器中水分,计量,然后把试验装置改为蒸馏装置。分析馏出液含量,收率96%以上。
使用SnCl2·2H2O为催化剂,确定合成的最佳工艺条件为:催化剂用量为4.0%,醇酸摩尔比为1∶3.2,反应温度在170~180℃,反应时间为3.5~4.0h之间。所得到的产品为浅黄色液体,酸值为6.52mgKOH/g。