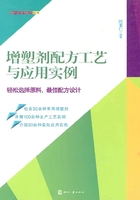
1.5 2-乙基己醇
一、概述
2-乙基己醇俗称辛醇,分子式为CH3(CH2)3CH(C2H5)CH2OH,分子量130.23。辛醇也称正辛醇,具有伯醇的性质,外观为无色透明液体,有类似柠檬的气味,沸点195℃。2-乙基己醇沸点略低,为183.5℃。密度0.8234~0.8325g/cm3。辛醇闪点为91℃,2-乙基己醇闪点为85℃。辛醇与2-乙基己醇能与醇、醚、氯仿等多种有机溶剂混溶溶解橡胶、树脂、蜡、植物油、矿物油、染料等。几乎不溶于水。
辛醇主要生产方法有:以丙烯为原料的羰基合成法,以乙醛为原料的醇醛缩合法,粮食发酵法等。
二、生产技术
羰基合成法或称为一步法工艺,是当今最为先进的生产工艺,新建装置大多采用这种工艺。
壳牌公司开发的低压羰基合成工艺(LPO)使丙烯直接转化成丁醇、异丁醇和2-EH(异辛醇)。
CH3CH2CH‖CH2+H2O→CH3CH2CH2CH2OH
CH3CH2CH2CH2Cl+H2O→CH3CH2CH2CH2OH+HCl
CH3CH2CH2CHO+H2→CH3CH2CH2CH2OH
采用油溶性三苯基膦(TPP)配体改性的铑为催化剂,产物丁醛靠大量未反应的合成气和丙烯从反应釜中带出,从而实现产物和催化剂的分离,称为气相循环工艺。为减少大量气体循环而带来的能量消耗,低压羰基合成液相循环工艺,即反应产物丁醛和催化剂溶液一起自反应釜中排出,然后对产物丁醛和催化剂溶液进行气化分离。该工艺开发的吸附回收液相工艺采用的是铑/亚磷酸盐络合环氧化物催化剂,在相接近的反应温度下的反应压力更低,由于原料转化率极高,故可使烯烃氢甲酰化反应实现一次性转化,而不必循环。所述催化剂为最新一代催化剂。
将丙烯与一氧化碳/氢气在复合催化剂存在下,用甲苯为溶剂,在16kg/cm2、100℃条件下进行羰基合成反应,生成正丁醛。为了生产辛醇,应使用沸点为115~320℃的馏分,将部分C4羰基液送去分离,在理论塔板为20~30的分离塔内,以0.3~0.27m3/s的流速在塔内进行分离,从塔顶得到正丁醛。
丁醛的醛醇缩合反应在不同温度下进行,液体流速为0.33mL/min,气体流量为250mL/min,通过10mL的固定床,在3bar(表压)的压力下对催化剂进行测试。
正丁醛在稀碱存在下,于塔式缩合器内发生缩合反应,生成2-乙基己烯醛。碱液是由循环的3%稀碱液与新鲜碱液混合配成浓度为6%的碱液。缩合后产品分层,大部分稀碱液循环使用,2-乙基己烯醛在含镍催化剂作用下,在110~210℃、10~20MPa压力下进行液相加氢,生成高纯度的2-乙基己醇。
低压羰基合成液相循环工艺,即反应产物丁醛和催化剂溶液一起自反应釜中排出,然后对产物丁醛和催化剂溶液进行气化分离。该工艺为双釜串联工艺,采用铑/TPP为催化剂。
一种两相工艺,以三苯基膦-3-间磺酸盐做配位体对铑催化剂改性,称为水溶性铑催化剂。这种催化剂具有催化剂与产物容易分离、产物正异构比例高的特点,而且用水做溶剂既便宜、安全,又有利于环境保护。但这种两相工艺也有不足之处,主要是由烯烃原料在水介质中比在有机相中溶解性低,所以催化剂反应速率有所降低。同时由于这一反应是多相的,所以催化剂活性相当低,因此水溶性催化剂工艺的操作压力和温度比油溶性工艺高,还需要较高的铑浓度。对此,采用在均相反应使用超声波以增加界面的表面积、按分离步骤使用极性有机溶剂和特制的配体以使反应均匀进行等改进方法。
辛醇生产关键是开发更好的催化剂以减少副产物、提高目标产物产量,达到绿色、高效的目的。采用丙烯低压羰基合成铑膦络合催化剂、合成气净化催化剂和丙烯净化催化体系用于丙烯羰基合成反应。与铑-单膦催化体系相比,铑浓度由200ppm降到80ppm,配体浓度由12%降到1%~2%,正丁醛与异丁醛的比例由10∶1提高到21.5∶1。
生产实例一:高效催化剂技术
所述专利系列催化剂的制备是通过浸渍二氧化硅的凝胶,球直径为2~4mm,纯度超过99%,总表面积约300~350m2/g。用孔直径为723nm的凝胶配制成质量分数为76%的碱金属硝酸盐的水溶液,在450℃下煅烧3h,提供的孔径体积为1.04cm3/g,得到含有各种催化剂负载的碱金属氧化物。
生产实例二:制备高效催化剂技术
向带有加料漏斗、温度计、机械搅拌器和一个加热套的2L三颈圆底烧瓶中,加入含有610g的水溶液、60g的Na2CO3·H2O和71g的NaOH后将物料冷却至小于5℃。向加料漏斗中装入345g的水、77g的(NO3)2·6H2O溶液和75g的Al(NO3)3·9H2O,用超过4h的时间加入此溶液。溶液的温度保持小于5℃。将所得的淤浆在小于5℃下搅拌1h后,用回流冷凝器替换加料漏斗,将浆液用1h时间加热至60℃,然后将该浆状物冷却至室温,通过过滤回收固体。固体用热去离子水10L洗涤后于100℃下干燥16h,再将此产品破碎后,所得固体在马弗炉中与空气流于450℃下焙烧12h。此产品用色谱分析为MgO-Al2O3固熔体(Mg/Al为1.5), BET表面积为285m2/g。仅改变的相对摩尔比的Mg(NO3)2·6H2O和Al(NO3)3·3H2O。可通过类似的装置制备不同的Mg/Al比的材料。
生产实例三:改良工艺
将正丁醛加入到一个大约3%的氢氧化钠水溶液中,比例为9份重量的氢氧化钠溶液与1份重量的醛,并充分混合,在100~130℃下生成2-乙基己醛,然后通过加水,在固定床镍催化剂存在的气相环境氢化,产物包含下列组分。

反应器段是一个垂直的7/8英寸的不锈钢管,长约3英尺,下段具有螺旋预热器。在反应器中,使丁醛在200psi的压力和反应器的温度150℃下进行。在丁醛和2-乙基-2′-己烯醛加氢的醛醇缩合反应中,2-乙基己醛的选择性超过80%,转化率接近90%。
生产实例四:氢化技术
粗辛醇液相加氢精制反应的加氢催化剂及其适用的加氢精制反应工艺中,加氢催化剂的活性组分为镍,稀土金属作为促进剂,载体为氧化铝,并可加有硅作为助剂。该催化剂综合性能优良,具有较好的孔结构和合理的孔分布,比表面积高,机械强度好。催化剂适应工艺条件的能力强,加氢活性高、选择性高、稳定性高,产品辛醇收率大于100%,大大提高了产物辛醇的纯度和色度。该催化剂所用于的粗辛醇液相加氢精制反应工艺的温度为80~260℃,压力为常压至6.0MPa。
生产实例五:庚烯一步氧化合成工艺
该法采用有机金属络合物催化剂,在低温且温和条件下进行反应,所用原料和催化剂为液体,溶解在烯烃内,形成均相反应体系,不需加入溶剂。
催化剂为Ni及其他过渡金属Ti、Rh、Ru、Pa、Fe、Co组分,各种不同配比的催化剂各自具有高的催化活性和选择性,由于避免使用Rh、Ru等贵金属,催化剂生产费用较低。
生产实例六:庚烯一步氧化合成催化剂技术
用庚烯一步氧化生产正辛醇所采用的催化剂为Rh2AcO4和[Rh (NH3)2Cl]Cl2。在高压反应釜内使正庚烯(2mL)、Rh2AlO(4 11mg)、EtOH(8mL)和PBu3在合成压5.0MPa,温度120℃, H2与CO比为1∶2, P-Rh的摩尔比为4∶1的条件下,经24h后反应生成醇,产率95%,正辛醇与异辛醇的比值为2.0∶1。
三、应用技术
增塑剂在塑料及薄膜中的应用
应用实例:生产环己烷二羧酸二(2-乙基己)酯技术
环己烷二羧酸酯是邻苯二甲酸二(2-乙基己)酯的改性产品,最大的特点在于将邻苯二甲酸二(2-乙基己)酯氢化后纯度几乎高达100%,产品不含苯。经环化后的分子量加大,稳定性更好。反应可一步完成,是一种绿色工艺。作为无毒增塑剂,比邻苯二甲酸二(2-乙基己)酯的品级更高。
向一个装有搅拌器、温度计、分水器、通氮导管的1000mL四口烧瓶中加入154g的六氢化邻苯二甲酸酐(HHPA),370g的2-乙基己醇(2-EH),并滴入2.6g的酞酸四异丙酯催化剂,控制反应温度为200℃、压力为5~760mbar,通氮气反应7h。此期间反应不断脱除生成的水。在反应过程中每隔0.5h测定1次反应体系的酸值,酸值按照GB/T 1668—2008计算,当酸值低于1.0mgKOH/g时酯化反应完成,随后用氢氧化钠中和,直到酸数量减少至低于mgKOH/g。中和后将反应混合物分离,采用水蒸气蒸馏法蒸馏脱除残余的2-EH,减少至少于300ppm。之后将粗酯干燥过滤。获得环己烷-1,2-二羧酸二(2-乙基己)酯反应混合物。颜色10APHA,酸值0.07mgKOH/g,纯度99.6%。由此产生的混合物可以用作增塑剂。
环己烷-1,2-二羧酸二(2-乙基己)酯的生产是用德国技术开发的目前唯一能替代邻苯二甲酸二异辛酯的大工业生产产品,德国的化学工业是举世闻名的。目前我国新上增塑剂的大生产装置极少。
国内邻苯二甲酸二异辛酯的生产企业可稍加改造,即能生产此环氢化系列产品,由此会产生巨大的经济与社会效益,并提高PVC的产品品级,增加PVC的出口创汇和扩大市场。环己烷二羧酸二(2-乙基己)酯新增塑剂的开发,可以打破传统的邻苯二甲酸二辛酯不可替代的观念,从而进一步产生双重的经济效益与社会效益。
在我国增塑剂向世界第一强国迈进的进程中,尤应首先加大环己烷-1,2-二羧酸二(2-乙基己)酯技术与系列产品的开发力度,大力研发专用化高性能的添加剂品种,提质降耗,才能使增塑剂产业向着绿色生态的大生产方向发展。