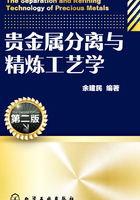
2.13 固相萃取技术
2.13.1 概述[29]
固相萃取(SPE)是一种基于色谱分离的样品的前处理方法。固相萃取包括固相(具有一定官能团的固体吸附剂)和液相(样品及溶剂)。液体样品在正压、负压或重力的作用下通过装有固体吸附剂的固相萃取装置(固相萃取柱、固相萃取膜、固相萃取吸嘴、固相萃取芯片等)。固体吸附剂具有不同的官能团,能将特定的化合物吸附并保留在SPE柱上。根据固相萃取的目的,我们可以将固相萃取划分为两种模式:一种是经典的固相萃取模式,SPE柱主要用于吸附目标化合物,称之为目标化合物吸附模式固相萃取(targets adsorption mode SPE);而另一种则是杂质吸附模式固相萃取(impurities adsorption mode SPE),即SPE柱主要用于吸附样品中的杂质。
在目标化合物吸附模式中,当样品通过SPE柱时,吸附剂的官能团与目标化合物发生作用,将目标化合物保留在柱子上,而通过SPE柱的样品基质则被排弃。为了降低分析中杂质对目标化合物的干扰,在对目标化合物洗脱之前,常常要用一定的溶剂对SPE柱进行洗涤。在尽可能不损失目标化合物的前提下,最大限度地除去这些干扰物。最后,用具有一定洗脱强度的溶剂将目标化合物从SPE柱洗脱出来,供下一步分析。这种模式通常包括五个步骤:①固相萃取柱的预处理(活化固相萃取柱);②样品过柱(添加样品并使其通过固相萃取柱);③洗涤(除去杂质);④干燥(除去水分);⑤洗脱(洗脱目标化合物)。
作为一项样品前处理方法,固相萃取已经在环境保护分析、食品分析、司法鉴定、药物分析、生命科学等领域得到了广泛的应用,特别是在农药残留物、兽药残留物、毒品、兴奋剂、药物以及环境中的有毒有害物质的分析中,已经成为许多国家及行业的标准分析方法,可以相信,随着人们对固相萃取技术的深入理解,以及对新型固相萃取材料的开发,其应用领域还会不断地扩大。
近几年来,有人试图将固相萃取技术应用于贵金属的分离,其实在20世纪80年代至20世纪末,科研人员对与固相萃取技术相似的萃淋树脂(浸渍树脂)或Levetrel树脂分离贵金属进行了大量的研究,发表了大量综述性及研究性论文。萃淋树脂(浸渍树脂)是将萃取剂浸渍在多孔性惰性骨架上制成的一种树脂。很多种萃取剂,如胺类(N235、TOA、Alamine 336)、膦类(TBP、P204、TOPO)等皆可浸渍在多孔性惰性骨架上。Levetrel树脂是将萃取剂与苯乙烯、二苯乙烯、致孔剂混合后通过高压聚合合成的树脂。萃淋树脂(浸渍树脂)或Levetrel树脂使用时兼有溶剂萃取和离子交换两种功能,具有提取能力强、选择性好、溶剂损失少、无需液-液两相分离、避免了乳化或产生第3相、设备简单、操作方便,特别是能像反萃一样,用类似的试剂能有效淋洗解吸,适用于从大体积、低浓度溶液中提取和富集贵金属。然而在实际使用时发现,萃淋树脂(浸渍树脂)上的萃取剂易脱落流失,经过几次循环使用之后,性能下降;Levetrel树脂吸附容量小、合成困难、价格高,难以推广。正因为如此,进入21世纪以后,有关应用萃淋树脂(浸渍树脂)或Levetrel树脂分离贵金属的文献报道日渐减少,由于这一研究领域已经超出本书的范畴,在此不再冗述,仅对近几年来文献报道的应用固相萃取技术分离贵金属进行简要的介绍。笔者认为,固相萃取技术难以克服萃淋树脂(浸渍树脂)或Levetrel树脂的缺点,它仅具有理论研究价值而不具有实际应用价值。
2.13.2 固相萃取技术分离金[30~32]
专利CN 101255499A报道了一种从碱性氰化液中固相萃取金的方法,其步骤为:①固相萃取金。固相萃取剂装柱,固相萃取剂为表面键合有疏水性烷基链的硅胶或聚合物,烷基可以是C2、C4、C8、C16及C18的烷基中的一种,使用粒度为20~80μm的粒状固相萃取剂装柱,柱高为柱直径的x倍,x>1;固相萃取剂活化,选用适量pH=10~11,浓度为0.01015mol/L的十六烷基三甲基溴化铵(CTMAB)溶液在室温下通过固相萃取剂柱活化处理;氰化金溶液的预处理,按CTMAB:Au的摩尔比为1.5:1的比例将两种溶液混合均匀后,放置5min,待萃液pH值为9.5~12;固相萃取,将预处理过的待萃氰化金溶液以<25mL/min流速通过固相萃取柱,使固相萃取剂萃取与CTMAB形成的缔合物。根据金浓度调整流速,金浓度愈低,允许过柱流速愈大,对于金浓度为2mg/L的氰化液,1g固相萃取剂可以萃取约35L溶液,固相萃取剂的饱和吸附量为70mg Au/g,Au的萃取率为98%~100%。②水洗涤分离杂质金属。由于Cu、Ni、Fe、Zn等金属离子会同时不同程度地被机械夹带吸萃,采用适量的pH=10~11的溶液洗涤固相萃取柱,使机械夹带的这些杂质金属离子与金分离。③有机溶剂洗脱金。用乙醇作洗脱剂以2mL/min的流速通过固相萃取柱,解吸柱上吸萃的金,18mL乙醇可以解吸1g固相萃取剂中吸萃的全部金,金富集倍数可达76~1916倍。④蒸馏回收有机溶剂。用蒸馏法或减压蒸馏法,在78.39℃下蒸馏回收乙醇。⑤蒸馏残余物回收金。用焚烧法、王水溶解赶硝后还原法、加适量水搅拌下电沉积法、加盐酸或硫酸破坏CN-后还原法等常规方法之一回收金。该方法提供了一种用固相萃取剂从金浓度很低的氰化液中富集和提取金的技术。该技术克服了从氰化金溶液液-液萃取金的问题,具有不需要使用大量有机溶剂、不会出现乳化、富集倍数高、操作简单易于自动化,环境污染小等特点。
【实例2-1】 C18键合硅胶0.5g,氰化液料液金浓度2mg/L,体积11.5L,pH值10.5。按十六烷基三甲基溴化铵(CTMAB):Au(摩尔比)=1.5:1加入CTMAB溶液到料液中,C18烷基键合硅胶固相萃取剂装柱,浓度为0.01015mol/L的CTMAB溶液室温下过柱活化处理固相萃取柱,预处理过的待萃溶液以15mL/min流速过柱萃取,金萃取率为100%;用pH值为10.5的溶液洗涤固相萃取柱分离铁;6mL乙醇过柱解吸金,金富集倍数为1916倍;蒸馏回收乙醇;灼烧法回收金,得金22.8mg。
【实例2-2】 C18键合硅胶10g,氰化液料液金浓度4μg/mL,银浓度4.6μg/mL,体积9.2L,pH值为10.5。按十六烷基三甲基溴化铵(CTMAB):Au(摩尔比)=1.5:1加入CTMAB溶液到料液中预处理料液,C18烷基键合硅胶固相萃取剂装柱,浓度为0.01015mol/L的CTMAB溶液室温下过柱活化处理固相萃取柱,预处理过的待萃溶液以15mL/min流速过柱萃取,金萃取率为98.7%;10mL乙醇过柱解吸金,金富集倍数为920倍;蒸馏回收乙醇;蒸残渣加硝酸破坏CN-并分离Ag后回收金,得金35.8mg。反相键合硅胶的空隙率较低,CTMAB阳离子与形成的离子缔合物很容易造成空隙的阻塞,使流速下降,同时,反相键合硅胶价格昂贵,提金成本高。
CN 101603123A报道了用大孔树脂从碱性氰化液中固相萃取金的方法,其步骤为:①待萃水相是含氰化亚金配合物的碱性溶液,溶液pH值为9.0~12.0,金浓度为1~50mg/L。②固相萃取前,向含氰化亚金配合物的碱性溶液中加入表面活性剂,表面活性剂与Au摩尔比为0.5:1~6:1,表面活性剂选十六烷基三甲基溴化铵(CTMAB)、苄基十四烷基甲基氯化铵(TDMBA)或溴化十六烷基吡啶(CPB)中的一种。③固相萃取剂的制备。将弱极性或非极性大孔吸附树脂与萃取剂共同振荡1~24h,经过滤和干燥后得到提金用的固相萃取剂,其中,浸渍用萃取剂选磷酸酯类、亚砜类或醇类中的一种或两种混合物,磷酸酯类的分子式为R1R2R3P=O,R为C4~C10的直链或支链烷基,亚砜类分子式为R1R2S=O,R为C4~C10的直链或支链烷基;弱极性或非极性大孔吸附树脂选聚苯乙烯基或丙烯酸酯基高分子微球,例如,南开牌D3520、南开牌D4020、南开牌AB-8或XAD-x(x范围为1~7)中的一种,粒径范围为0.3~1.25μm。④固相萃取条件。室温下将步骤②中加有表面活性剂的待萃溶液以1~30mL/min流速通过装有大孔树脂的固相萃取柱,使浸渍了萃取剂的大孔吸附树脂固相萃取
与表面活性剂形成的缔合物,固相萃取剂形成的饱和吸附容量为50.0~100.0mg Au/g树脂。
当水相中不加入表面活性剂苄基十四烷基甲基氯化铵(TDMBA)时,Am-XAD-7大孔吸附树脂对Au的萃取率很低,金氰化溶液过柱体积为800mL时,金的萃取率已经下降到2%。相反,随着水相中TDMBA量的增加,树脂对金的萃取率显著提高,当Au:TDMBA摩尔比值为1:1.5时,即使金氰化溶液过柱体积达到2000mL,金的萃取率仍然大于99.5%,可见表面活性剂起到了关键的作用。实验证明:2g浸渍有萃取剂的大孔吸附树脂可固相萃取金浓度为25mg/L的氰化液5000mL,Au的萃取率大于99%,再增大待萃取溶液的过柱体积,固相萃取效率有所下降。降低氰化液金浓度,在保证Au大于99%的高萃取率的前提下,允许过柱的氰化液体积增大,固相萃取剂的饱和吸附容量为50.0~100.0mg Au/g树脂。
【实例2-3】 将浸渍了二异辛基亚砜萃取剂的南开牌D4020大孔吸附树脂2g,装填于直径为1cm的玻璃柱中,柱高8cm。碱性氰化液中金浓度为25mg/L,pH值10.3,将十六烷基三甲基溴化铵(CTMAB)加入碱性氰化液中,CTMAB:Au(摩尔比)=1.5:1。将上述待萃取溶液以3mL/min流速过柱固相萃取,过柱溶液体积为4500mL,其萃取率大于99%,对载金树脂进行洗脱,用电解法从洗脱液中回收金,得金110.21mg。
【实例2-4】 将浸渍了三烷基氧膦(TRPO)的南开牌D3520大孔吸附树脂2g,装填于直径为1cm的玻璃柱中,柱高8cm。碱性氰化液中金浓度为25mg/L,pH值10.3,将苄基十四烷基甲基氯化铵(TDMBA)加入到碱性氰化液中,TDMBA:Au(摩尔比)=1.5:1。将上述待萃取溶液以3mL/min流速过柱固相萃取,过柱体积为5000mL,金的萃取率大于99.26%,对载金树脂进行洗脱,用电解法从洗脱液中回收金,得金123.04mg。
【实例2-5】 将浸渍了三烷基氧膦(TRPO)大孔吸附树脂2g,装填于直径为1cm的玻璃柱中,柱高8cm。某矿山碱性氰化液组成为:Au 18.175mg/L、Cu 48.75mg/L、Zn 2.75mg/L、Fe 0.87mg/L、Ni 0.64mg/L,溶液pH值为10.5。将苄基十四烷基甲基氯化铵(TDMBA)加入碱性氰化液中,TDMBA:Au(摩尔比)=4:1。将上述待萃取溶液以3mL/min流速过柱固相萃取,过柱溶液体积为3000mL,金的萃取率大于99%,而对其他金属离子的萃取率均小于35%,尤其对Cu的萃取率小于10%,具有一定的选择性。对载金树脂进行洗脱,用电解法从洗脱液中回收金,并对金进行精炼,得金52.0mg。
为了找到性能更优良的新材料,CN 101538656A对常用反相材料进行了筛选,发现多孔石墨化炭黑比烷基键合相硅胶或多孔聚合物填料具有更强的保留能力,可在任何酸度和特殊温度下使用,材料使用范围和耐用性远远高于其他反向材料。而且进一步研究发现,表面活性剂(如双十六烷基二甲基氯化铵等)能在多孔石墨化炭黑上稳定附着,用水相介质(硝酸)洗脱不能被洗下。用附载有表面活性剂的多孔石墨化炭黑不仅能选择性地从碱性氰化液中富集金,并且萃取容量高、金回收率高、洗脱容易实现,具有工业应用价值。一种从碱性氰化液中萃取金的方法,包括以下步骤:①固相萃取柱。称取100g多孔石墨化炭黑(粒度为30~60μm。)置于500mL干燥的烧杯中,在不断搅拌下加入50mL 100g/L的表面活性剂(双十六烷基二甲基氯化铵、十八烷基三甲基氯化铵、十八烷基二甲基苄基氯化铵或十八烷基氯化吡啶)丙酮溶液,在搅拌下水浴蒸干,得到附载有表面活性剂的石墨化炭黑;在固相萃取柱中装入附载有表面活性剂的石墨化炭黑并压实;萃取柱用pH=9.4~13的稀氢氧化钠洗涤后备用。②固相萃取。将实际矿山料液或配制浓度为2~24mg/L的KAu(CN)2溶液,调节其pH值在9.4~13之间,以10~100mL/min的流速通过固相萃取柱,萃取富集,富集完后再以5~50mL/min的流速用10~500mL 2%~10%硝酸洗脱液反向洗脱,收集洗脱液。③回收金。用电沉积法回收洗脱液中的金。该方法的优点:可操作的pH值范围非常宽,金的一次萃取率超过96.5%,富集倍数超过250倍,材料对金的萃取容量大于29 mg/g;所制得的固相萃取材料(附载表面活性剂的石墨化炭黑)在使用超过100次后仍然能保持良好的柱效,洗脱时不拖尾,萃取容量和回收率与初使用时能保持一致;固相萃取过程更容易实现操作自动化,工业可行性大大强于溶剂萃取;克服了液-液萃取提金需使用大量有机溶剂、易乳化、相分离慢的缺点,有机溶剂消耗非常小,对环境的污染小。
【实例2-6】 从碱性氰化液中萃取金。称取100g粒度30μm的多孔石墨化炭黑置于500mL干燥的烧杯中,在不断搅拌下加入50mL100g/L的双十六烷基二甲基氯化铵丙酮溶液,在搅拌下65℃水浴蒸干,得到附载有双十六烷基二甲基的石墨化炭黑。固相萃取柱规格20mm×25mm,装填料8.2g。在装填管的一端装上筛板,装入附载有双十六烷基二甲基的石墨化炭黑并压实,然后在另一端装上筛板,拧紧柱帽。萃取柱用pH=9.4的稀氢氧化钠液洗涤。固相萃取:配制KAu(CN)2溶液,浓度为2mg/L,调节其pH=9.4,以10mL/min的流速通过固相萃取柱富集,富集完后再以5mL/min的流速用200mL的洗脱液反方向洗脱。100mL萃取洗脱液中加入20mL的0.5mol/L的硫酸钾溶液。箱式电积槽:100mm×60mm×60mm,总容积360mL,有效容积330mL。一块阴极板的有效几何面积60mm×60mm。阴极材料为碳纤维,阳极材料均为镀铂的钛网,直流电源JH-2D恒电位仪。阴极极板数为1,异极中心距为10mm。电积液温度为室温。总电积时间为8h。在电积过程中不断摇动电积槽使电积液回流以消除浓度差,电沉积完后残液回收乙醇。待电积液中金的浓度为1.2mg/mL,电积残液中金的浓度为0.05μg/mL,金的回收率超过99%,所得金的纯度≥95%。按0.7元/(kW·h)的电价计,电解每克金的电耗费用为0.17元。
【实例2-7】 从实际矿山料液中萃取金,表面活性剂为十八烷基氯化吡啶。实际矿山料液采自大理弥渡金矿,料液中的金含量为12.8mg/L,银含量为7.2mg/L,镍含量为2.8mg/L,铜含量为1.6mg/L,锌含量为28.4mg/L,铁含量为2.4mg/L,钴含量为0.84mg/L。矿山料液分别采用(ϕ8mm×10mm,装填料0.6g),(ϕ12mm×15mm,装填料1.9g),(ϕ16mm×20mm,装填料4.5g),(ϕ20mm×25mm,装填料8.6g),(ϕ40mm×50mm,装填料65g)的萃取柱进行萃取。分别测定萃取容量,结果见表2-21。从表2-21可看出,对实际矿山料液,萃取柱对金的萃取量随萃取柱的扩大而扩大;但和单一KAu(CN)2溶液萃取相比,实际矿山料液萃取中金的萃取容量显著降低,每个规格萃取柱的萃取容量都下降了2倍以上,说明实际矿山料液中共存离子对金的萃取产生了影响。对萃取柱上的富集物进行了洗脱,合并洗脱液并测定了金泥的组成。金泥中各元素的含量分别为:金14.8%、银4.27%、锌5.22%、镍0.52%、铜0.68%、铁0.14%、钴0.28%,说明几种共存元素均随金一起被萃取,但萃取柱对金仍然保持较高的萃取容量。
表2-21 不同规格萃取柱对实际料液中金的萃取

(1)介质的pH值
介质的pH值是影响固相萃取的重要参数,它可能会影响金氰配阴离子和双十六烷基二甲基铵阳离子的有效浓度,进而影响生成离子缔合物的稳定性和缔合物在萃取柱上的吸附。由于金氰配阴离子在pH>9.4的条件下才能稳定存在,生成的离子缔合物也在pH>9.4的条件下才稳定。因此实验的pH值范围设定在9.4~13之间,结果表明在pH值为9.4~13范围内,金的萃取率均在95%以上,而且pH值改变对金的萃取率无明显影响,说明可操作pH范围非常宽。
(2)萃取容量的测定
萃取容量是衡量方法实际应用价值的重要参数,萃取容量越高,每次操作富集的金越多,工作效率越高。为了测定萃取柱的萃取容量,取Au(Ⅰ)浓度为10mg/L的氰化亚金钾溶液,以50mL/min的流速过柱,收集萃残液浓缩后测定金的量,当过柱溶液体积超过30L时金的回收率开始明显下降,说明萃取柱对金的吸附已达到饱和。由此可推断萃取柱对金的最大萃取容量约为28mg/g。
(3)洗脱剂的选择和用量
在固相萃取中,由于被萃取成分优先在柱的顶部富集,造成顶部的浓度大于下部的浓度,富集完后颠倒萃取柱反方向洗脱可有效缩短洗脱路径,减少需要洗脱液的体积,因此本实验中选择富集完后颠倒萃取柱反方向洗脱。试验测定了用硫脲、硝酸、EDTA、硫代硫酸钠对金的洗脱效果,结果表明以2%~10%的硝酸为洗脱剂效果最好,所需洗脱剂的体积和萃取柱上富集的金成正比,每10mL的洗脱液可洗脱72.6mg萃取柱上富集的金。
(4)不同金浓度时的萃取回收率
参照实际矿山料液中金的浓度,实验测定了不同浓度金的萃取回收率,用pH=10.5的稀氢氧化钠溶液配制金浓度(mg/L)为:2、8、16、24的氰化亚金钾溶液,以50mL/min的流速通过萃取柱,直至萃取柱接近饱和(金的总量为230mg),测定其萃取回收率,结果见表2-22。从表2-22可看出,浓度为2~24mg/L范围内,金的浓度对萃取回收率无明显影响,而且金的回收率均在95%以上,回收率很高;金的浓度越低,达到萃取柱饱和所需通过溶液的体积越大,富集倍数越高(由于洗脱液的体积均固定在30mL);所以固相萃取对低浓度的金的萃取富集优势更明显。
表2-22 不同金浓度时的萃取回收率

(5)材料使用寿命
固相萃取柱富集金后用硝酸洗脱,固相萃取柱上负载的表面活性剂不流失,柱洗脱干净后用稀氢氧化钠溶液平衡,可再次用于金的萃取,固相萃取材料可重复使用。实验表明,该固相萃取材料在所述实验条件下使用超过100次后仍然能保持良好的柱效(洗脱时不拖尾,萃取容量和回收率与初使用时能保持一致)。
2.13.3 固相萃取技术分离钯[33]
专利CN 101020964A报道了一种固相萃取钯的方法,其步骤为:①料液过柱固相萃取钯。用一种键合了钯萃取剂的高分子微球聚合物为固相萃取固定相,从含Pt、Pd、Rh、Ir铂族金属及Cu、Fe、Ni、Zn贱金属的盐酸中萃取钯,钯萃取剂可以从分子式为R—S—R’的二烃基硫醚、分子式为RR'S=O的二烃基亚砜中任选一种,其中R是C4~C16的直链、支链的烷基、苯基或苄基,R’是与R相同的C4~C16的直链、支链的烷基、苯基、苄基或含氮硫元素的杂环;高分子复合微球聚合物支持体可以是下述聚合物之一,例如:N,N-亚甲基二丙烯酰胺与乙烯基咪唑、2,6-丙烯酰胺吡啶与二丙烯酰胺-2-甲基-1-丙磺酸或三甲基丙烯酸季戊四醇酯与4-苯乙烯基-亚氮二乙酸、二甲基丙烯酸乙二醇酯与丙烯酸等等。通过聚合反应将萃取剂键合于高分子聚合物内部而形成固相萃取固定相。其微球粒径为150~830μm,盐酸介质含铂族金属及贱金属的料液,其HCl浓度范围为0.01~2.0mol/L,最佳范围为0.1~0.5mol/L。Pd的浓度范围为0.00x~xxg/L,最佳范围为x~20g/L。Pt的浓度可等于Pd的浓度或高于最佳Pd浓度xg/L的数倍。所含的Rh、Ir应为3价的氯配阴离子。贱金属Cu、Fe、Ni、Zn等的浓度不受限制,可等于铂族金属总浓度或大于铂族金属浓度数倍。钯吸萃率≥99.5%,每1000mg固相萃取固定相的萃取容量可这80~130mg钯。②淋洗除去杂质元素,用浓度范围为0.05~0.5mol/L稀盐酸溶液淋洗载钯固定相,除去机械吸留的少量铂、铑、铱及贱金属铜、铁、镍、锌,达到钯与其他铂族金属及贱金属的比较彻底地分离,淋洗液视情况可以与流出液合并。③洗脱回收钯。用一种能与钯配合的试剂,如从浓度为每升几克到几十克的硫脲溶液或浓度为1~5的NH3·H2O溶液中任意选择一种通过固相萃取柱洗脱钯,钯洗脱率为99%,洗脱钯后的固相萃取柱用浓度为0.1mol/L稀盐酸过柱使固相萃取剂再生待下一次使用。④从洗脱液精制钯。硫脲洗脱液中加盐酸与氧化剂,加热浓缩使钯的硫脲配合物转化为氯配合物;对于氨水洗脱液,可直接浓缩后用盐酸酸化沉出Pd(NH3)Cl2,金属钯的进一步提纯精炼可使用传统的经典方法。该方法分离效果好,所需时间短,操作简便,成本低;固相萃取柱可反复使用40次以上;适用范围广,可用于多种资源中贵金属的分离提取。
【实例2-8】 模拟从铂族金属精矿获得的料液成分,以含钯3.752g/L、铂5.0199g/mL、铑0.562g/L、铱0.125g/L、铜1.254g/L、铁1.221g/mL、锌1.192g/mL、镍0.832g/L的合成样进行试验。用键合了正十六烷基硫醚的三甲基丙烯酸季戊四醇酯与4-苯乙烯基-亚氮二乙酸聚合物作固定相,粒径为550μm;固相萃取柱规格为ϕ15mm×400mm,进样体积为32.00mL;介质盐酸浓度为0.1mol/L,料液流速3mL/min;淋洗液为0.1mol/L盐酸20mL,流速3.0mL/min;洗脱液为2%的硫脲溶液50mL,流速3mL/min;固相萃取柱用0.1mol/L盐酸40mL再生。钯的回收率为99.81%。
【实例2-9】 贵金属催化剂Ⅰ中钯的分离。从处理失效汽车催化剂获得铂族金属富集物,用王水溶解并赶硝后获得盐酸介质的贵金属富液,用成分为钯1.336g/L、铂6.467g/L、铑1.618g/L、铜2.908g/L、铁15.58mg/L、锌45.98mg/L、镍11.86mg/L的样品进行试验。用键合了甲基苯基硫醚的二甲基丙烯酸乙二醇酯与丙烯酸聚合物作固定相,粒径为250μm,固相萃取柱为ϕ10mm×350mm,料液体积为20.00mL;盐酸浓度为0.1mol/L,过柱流速2mL/min;淋洗液为0.1mol/L盐酸20mL,流速2.5mL/min;洗脱液为2%的硫脲溶液40mL,流速2mL/min,固相萃取柱用0.1mol/L盐酸20mL再生。整个分离过程在1h内完成,钯的回收率为99.69%。
【实例2-10】 贵金属催化剂Ⅱ中钯的分离。由贵金属催化剂Ⅱ获得的料液组分浓度为:钯0.8908g/L、铂4.3g/L、铑1.078g/L、铜1.871g/L、铁10.389mg/L、锌30.65mg/L、镍7.90mg/L。用键合了异戊基苯并噻唑硫醚的二甲基丙烯酸乙二醇酯与三氟甲基丙烯酸的聚合物作固定相,粒径为270μm,固相萃取柱为ϕ10mm×350mm,料液体积为15.00mL;介质盐酸浓度为0.1mol/L,料液流速2mL/min;淋洗液为0.1mol/L盐酸30mL,流速2.5mL/min;洗脱液为2%的硫脲溶液30mL,流速2mL/min,固相萃取柱用0.1mol/L盐酸20mL再生。整个分离过程在1h内完成,钯的回收率为99.61%。
【实例2-11】 贵金属催化剂Ⅲ中钯的分离。由贵金属催化剂Ⅲ获得的料液组分浓度为:钯1.824g/L、铂12.57g/L、铑3.235g/L、铜5.658g/L、铁31.8mg/L、锌93mg/L、镍23.8mg/L。用键合了二苯基硫醚的三甲基丙烯酸季戊四醇酯与4-乙烯基吡啶聚合物作固定相,粒径为212μm,固相萃取柱为ϕ10mm×350mm;进样体积为10.00mL,介质盐酸总浓度为0.1mol/L,进样流速2mL/min;淋洗液为0.1mol/L盐酸20mL,流速2.5mL/min;洗脱液为2%的硫脲溶液40mL,流速2mL/min。固相萃取柱用0.1mol/L盐酸20mL再生。结果表明,贵金属与贱金属分离效果好,整个分离流程在1h内完成,钯的回收率为99.73%。
2-乙基己基辛基硫醚树脂及二苄基硫醚树脂固相萃取钯[34,35]实际上是含硫醚的萃淋树脂对钯的吸附,在此不再冗述。