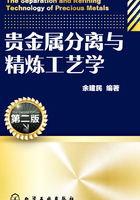
2.14 分子识别技术
2.14.1 分子识别技术(MRT)的基本原理
1967年Charles Pedersen合成了冠醚,1969年Jean-Marie Lehn合成了第1个穴醚,1973年Donald Cram合成出球醚并用它来检验预组织的重要性,1978年Jean-Marie Lehn提出“超分子化学”的概念,定义为“分子组装体的化学和分子间键的化学”,1987年3人共同获得Nobel化学奖,表彰他们在超分子化学方面的贡献[36]。
20世纪70~80年代后期Ronald L.Bruening、Izatt、R.M.等人合成了1,4-二硫代-19-冠-6(T219C6)、1,4,4,10-四硫代-18-冠-6(T418C6)等冠醚、大环芳烃[37],并将其键合到硅胶表面上[38],在研究了这些新化合物的物理性质、热力学性质,测定了这些环状配体与许多金属离子配合物相互作用的常数之后[39],才认识到可用于选择性回收有价金属,因为这些分子能够选择性键合一个或一组金属离子,例如,能够合成一个对金具有强亲和力而对常见贱金属无亲和力的分子,同时树脂对该金属的亲和力可以控制,以便树脂上的负载金属能用配合剂溶液如氨水、硫脲、氯化物、溴化物等淋洗回收[40]。
将所希望的环状配体键合到载体上去所必须遵循的原则[41]:
a.设计配体分子使配体亲和力(如电荷吸引力)、配位几何关系(如配位化学作用)、主-客体大小适合(例如,最佳空间作用或最小的立体障碍),使配体能够选择性地与一个或一组客体分子成键(例如,选择性地识别某一个或一组金属配合物),即建立锁与钥匙的关系。
b.分子识别配体与固体材料结合后仍保持未键合时配体的性质(例如,选择性和成键性),即保持原分子识别能力不变。
c.键合作用大小适中,负载金属能被适宜的洗脱剂淋洗下来。
d.分子识别配体在使用过程中损失小,这样才具有商业应用价值。
对于不同的金属配合物离子选择不同的配体键合到载体表面上去,制备了一系列材料,其结构如图2-22所示。

图2-22 SuperLig®材料结构
与传统火法冶金、湿法冶金、沉淀、离子交换、溶剂萃取等分离方法识别目标分子或离子通常仅依据单一因素,例如,熔融温度、溶解度、电荷及半径等,不同,MRT识别目标分子或离子依据离子半径、配位化学特征、几何结构等多种因素,其中冠醚环腔尺寸与目标分子或离子大小匹配在配体选择性识别过程中占主导地位,因而其选择性极高。沙啉修饰在硅胶上的结构如图2-23所示。[PdCl4]2-和的超配合物(Super Complex)的结构如图2-24所示。[Fe(CN)6]4-与大环多胺的次层配位结构如图2-25所示[36]。

图2-23 沙啉修饰在硅胶上

图2-24 [PdCl4]2-和的超配合物

图2-25 [Fe(CN)6]4-与大环多胺的次层配位
2.14.2 在贵金属矿产资源中的应用
自从1989年在美国Arizon召开的贵金属回收与精炼会议和1990年在美国California召开的第14届贵金属年会上Craig Wright博士和Ronald L.Bruening博士先后公开发表了有关利用分子识别技术分离精炼贵金属的论文以来[41,42],有关MRT分离纯化贵金属的新工艺引起了人们的普遍关注,经过二十几年来的开发研究,该技术已趋成熟,在最近几年的IPMI年会上不断有关于MRT分离贵金属的论文发表,如今MRT分离贵金属的工艺在贵金属工业中已众所周知,大量的MRT商业应用系统正在全球运行,其应用和装置正在持续扩大,先后在美国、南非、日本等国家和台湾地区得到了广泛的应用。
2.14.2.1 从氰化液中分离纯化金
127对氰化物介质中金的选择性比贱金属高,
127键合的是[Au(CN)2]-,洗脱产品是NaAu(CN)2或KAu(CN)2,一个很好的例子是:
127从氰化金钾电镀液中分离纯化金,MRT工艺既简单,又高效。氰化液中金的浓度为20~900mg/L,钾的浓度大约12g/L,经MRT工艺处理之后金的浓度降为0.05mg/L,应用0.5~1.0mol/L KCl洗涤,90℃的去离子水洗脱金。亦可以应用5mol/L KCl洗涤,56~75℃的去离子水洗脱,NaCl预洗脱与KCl预洗脱相比,其优点是用去离子水洗脱时温度低,洗脱液中金的浓度较高。在所有的实例中吸附尾液中金的浓度降为0.05mg/L,而贱金属在纯化后的金洗脱液中均在检测下限,金的纯度达到99.99%,图2-26给出了典型的工艺流程[43~45]。

图2-26 MRT从废电镀液和浸渍液中分离纯化金
2.14.2.2 从银电解液中回收钯
测定了2与各种金属离子的稳定常数lgK,分别为:Pd(Ⅱ)32.0、Au(Ⅲ)45.0、Ag(Ⅰ)11.5、Hg(Ⅱ)16.8、Cu(Ⅱ)1.8。
胶片灰和铜电解阳极泥熔融物用硝酸溶解得到的银电解液组成(g/L)为:Ag 400、Pd 0.2、Pb 5、Cu 20~40、Fe<1、Ni<1。在直径10cm,高25cm的交换柱上以500~1100mL/min的流速用2从该溶液中吸附分离钯,吸附时柱由绿色变为蓝色,用0.5mol/L HCl洗涤,再用60℃ 0.1mol/L HNO3-1.5mol/L Tu淋洗得到亮橙色的钯硫脲配合物,柱恢复为淡绿色。亦可用氨水洗脱钯和银。两柱串联、氨水洗脱得到的产品组成(%)为:Pd 92.2、Pt 1.2、Rh 0.13、Au 0.6、Ag 5.2、Fe 0.32、Cu 0.13、Ni 0.20。用该法已回收了150oz(1oz=28.35g)的钯(1989年),2个月即收回投资,
2循环使用200次未发现异常。美国Cascade精炼厂贵金属精炼流程见图2-27[41,42]。

图2-27 美国 Cascade 精炼厂贵金属精炼流程
2.14.2.3 2从王水废液中回收钯
王水废液组成(g/L)为:Ag 0.15、Pd 0.18、Pb 0.02、Cu 10、Fe 15、Ni 5。用2从该溶液中吸附分离钯,0.5mol/L HCl溶液洗涤铁,然后用氨水洗脱钯。
2.14.2.4 南非Harmony贵金属精炼流程
南非Bateman公司的下属MRT公司与美国IBC公司合作,在Harmony矿利用分子识别技术分离精炼贵金属,替代了现有的规模庞大的生产系统,精炼流程如图2-28所示[46]。

图2-28 Harmony贵金属精炼流程
2.14.2.5 南非Impala Springs精炼厂贵金属精炼流程
(1)料液成分及其预处理
英帕拉铂业公司典型的原液组成(g/L)为:金<0.001、铂50~60、钯30~40、铑8~10、钌10~15、铱4~5、铁8~12、铜2~4、镍4~7。
调整料液的总酸度在15%~24%之间,在英帕拉铂业公司典型的酸度为20%,应用NaClO3氧化或用NH4HSO3还原调节溶液氧化还原电势为690~710mV,使钯以钯(Ⅱ)状态存在,相对较窄的氧化还原电势和高酸度有利于铂以铂(Ⅳ)状态存在,并能减少铱(Ⅳ)的形成,铱(Ⅳ)为氧化剂会对Su-2产生破坏作用。
(2)2的预处理
在钯的每套回收闭路中(包括2个柱)每柱装80L2,先将新的Su-
2装入调节槽中,通过泵循环使水流过
2,其作用是使
2润湿并除去粒子之间的空气,然后将
2泵入柱中并用水循环洗涤,用2个床体积(160L)的10%HCl溶液流过2个柱,
2即可使用了。
工艺流程如图2-29所示,分离柱如图2-30和图2-31所示[47,48]。

图2-29 Impala Springs贵金属精炼厂的贵金属分离工艺流程

图2-30 Impala铂业公司Springs贵金属精炼厂MRT分离柱

图2-31 Impala铂业公司Springs贵金属精炼厂MRT分离钯的工艺
(3)MRT分离钯
将通过实验室实验所测定的2对钯的负载容量输入PLC控制系统,该系统即可计算出需要循环的料液量,要有足够的料液分别通过2个柱子,使第1个柱子饱和,第2个柱子达到负载量的30%。足够量的负载钯可以使第1个柱子中的其他元素被钯所替代,料液从第1个柱子顶部泵入,从其底部流出后再泵入第2个柱子的顶部,料液的流速为10L/min。然后用3个床体积(240L)的10%HCl溶液流过2个柱挤压出其中残留的料液和其他金属,较低的酸度有利于降低总的酸耗。也可以使用20%HCl溶液,但效果并不见得好。
2对钯的高的动力学和选择性使得在第2个柱子的顶部出现暗色色带而其底部仍为透明色。钯的吸附率大于99.5%,钯铂比达到200:1。10%HCl洗液与料液合并,送入下一个回收闭路中。
第1个柱子上的钯应用一种铵盐溶液洗脱,但在洗脱前为了防止柱子上的盐酸与铵盐溶液反应,用200L的去离子水洗涤。部分负载的第2个柱子中的盐酸不用洗涤。水的流速为14L/min,洗涤水送到酸再生工厂。
应用250L NH4HSO3溶液以12L/min的流速洗脱第1个柱子上的钯。曾经使用氨缓冲液洗脱钯,但发现若提高2对钯的负载容量会生成钯盐沉淀,这是由于当洗脱液流过柱子时,氨的浓度下降生成了Pd(NH3)2Cl2,而NH4HSO3与钯生成稳定的配合物不易生成沉淀。
洗脱钯之后用200L的去离子水以16L/min的流速洗涤除去柱子上残留的铵盐溶液,用150L 10%HCl溶液以相同的流速洗脱后柱子即可循环使用。
在第2次循环中,未负载饱和的第2个柱子作为第1个柱子,泵入足够的料液使新的第1个柱子吸附饱和,使新的第2个柱子负载量接近30%。
1个柱子完成1次吸附、洗脱就完成了MRT分离钯的1个循环,完成1个循环后2对钯的负载容量会稍有降低,该降低值会输入PLC以便计算出每次所需要料液的准确体积,结果发现
2对钯的负载容量每一次的降低值均为一恒定值。
(4)钯洗脱液的处理
钯NH4HSO3洗脱液不能沉淀为铵盐或金属,含有15kg钯的洗脱液加入150L浓盐酸酸化,在搅拌下鼓入空气氧化8h,反应为放热反应,需用冷却水冷却至30℃以下,氧化后过滤除去沉淀的杂质,调节总酸度小于1%,然后加入氨水调整至pH=9~10,在搅拌下加入50L H2O2氧化,加热溶液至80℃并维持30min使加入氨水时所生成的钯盐溶解。将溶液冷却至低于30℃,加入30L H2O2使铂等杂质氧化,3h后,加入浓盐酸调整pH=0.5~1,钯生成Pd(NH3)2Cl2而铂(Ⅳ)留在溶液中,过滤、洗涤、煅烧、还原得到海绵钯。
1992年英帕拉与IBC高技术公司合作研究MRT、离子交换、溶剂萃取分离贵金属,进行了不同工艺的实验室规模实验,1994年确定进行MRT、离子交换工艺的工业实验,所建立的工业实验工厂运行了3年,提出了一个工艺并为设计新的精炼厂提供了依据。工业实验结束后,实验工厂的生产量已达到英帕拉贵金属产量的25%,在进行工业实验工厂的同时,平行进行了MRT产品的优化和扩大生产规模。1997年英帕拉决定建设规模较大的铂族金属精炼厂,1998年旧的精炼厂停产。由于新工艺简单,能显著降低金属在流程、管道、设备中的存量,新工艺的优点在运行的第1年内就显现了,钯的定量回收使产量增加、金属循环降低。由于没有钯进入下一个工序,在水解步骤中能够获得较纯的铂,使铂的产量增加,铂在流程、管道、设备中的存量显著降低。
经过多年运行之后为了适应产量的扩大,英帕拉铂业公司已扩大了钯的生产规模,运行参数仍然是稳定,如今英帕拉铂业公司已运行11套MRT分离钯的装置,每一套含有2的装置均完成了不同数量的循环,体现了两个优点:第一,每个柱子中的
2在不同时间内更换以免引起工艺的波动;第二,钯的总交换容量维持在20g/L左右。最近英帕拉铂业公司用160L的交换柱代替了80L的交换柱,交换柱的容量扩大了1倍,在大柱中高径比接近1:1。已经观察到使用大体积的柱子及与之相配套的大流量不影响分离效率,这样英帕拉铂业公司就可以继续扩大钯的产量以便与其未来的生产计划相匹配。由于定量分离钯对后续工序及其重要,MRT分离钯工艺是精炼厂成功的关键。
2.14.3 在贵金属二次资源中的应用
2.14.3.1 从铜阳极泥中回收精炼铂族金属
物料的大致成分为Pd 20g/L、Pt 1g/L和Rh<0.1g/L,氧化还原电位(ORP)维持在550~720mV。系统的设计能力为年产钯80000oz、铂5000oz及铑500oz。分离工艺条件如表2-23所示[49,50]。
表2-23 从铜阳极泥中分离铂族金属

2.14.3.2 从Pt/Cr/Co合金废料中选择性分离纯化铂
基于在IBC完成的成功实验工作,1个包含3个柱系统的商业规模的分离、精炼铂的体系已在台湾某精炼厂建成,该体系由35kg133安装在3个柱子中组成,设计生产能力为年生产铂1000kg。
料液是以HCl-H2O2或HCl溶解Pt/Cr/Co合金废料得到的,在Cl-介质中铂通常生成[PtCl6]2-,133对[PtCl6]2-配阴离子的选择性比其他铂族金属配阴离子高,溶液中其他阴离子和阳离子浓度也较高。在室温下用水洗脱,应用5mol/L NaCl+0.1mol/L HCl和或1mol/L NaCl+0.1mol/L HCl洗涤。
合金废料中的铂溶解率达到100%,133对铂的单级回收率为99.9%(不包括留在尾柱上的铂),总回收率为99.99%。已经证明,
133对铂的选择性比溶液中其他离子高得多,用NH4Cl从洗脱液中沉淀铂为(NH4)2PtCl6,沉铂母液中含有极少的铂,铂盐应用传统的还原工艺转化为海绵铂,铂的纯度达到99.99%,铂用于制造薄膜,工艺流程如图2-32所示[51]。

图2-32 MRT精炼铂原则工艺流程
完整的MRT分离纯化铂的商业体系由下列各步组成:
负载——133吸附料液中的[PtCl6]2-配阴离子。
预洗脱(洗涤)——用5mol/L NaCl+0.1mol/L HCl和/或1mol/L NaCl+0.1mol/L HCl洗涤,部分洗液循环使用。
洗脱——133吸附柱上的铂在室温下用水洗脱得到纯度较高的铂氯化物溶液,部分洗脱液循环使用。
后洗脱(再生)——柱子用5mol/L NaCl+0.1mol/L HCl和/或1mol/L NaCl+0.1mol/L HCl洗涤,部分再生液循环使用。
2006年我国台湾某精炼厂安装了较大规模商业MRT铂系统,该系统自安装后已成功运行并达到了预期目标,图2-33给出了我国台湾某精炼厂的较大规模商业MRT铂系统照片,该系统由3个柱组成。

图2-33 我国台湾某精炼厂的较大规模商业MRT铂系统
2.14.3.3 从失效催化剂中分离纯化铑
已经证明应用MRT分离铑的工艺系统要庞大一些,例如,日本TKK正在应用MRT回收铑,TKK精炼厂的铑回收系统位于东京附近,已运行10多年[52,53],用于回收含铂、铑、贱金属失效催化剂中的铂、铑。MRT分离铑的190工艺系统由5个柱子组成,前4个柱子用于铑的分离,第5个用于洗脱(见图2-34)。

图2-34 日本TKK精炼厂铑的MRT系统
铑在盐酸中以3价状态存在,190能够键合[RhCl6]3-或[RhCl(H2O)5]2-,为了使至少98%的铑以[RhCl6]3-或[RhCl(H2O)5]2-形式存在,溶液中的Cl-浓度至少超过5mol/L,溶液的电势小于等于720mV(Ag/AgCl电极),相当于溶液中无游离的Cl2,以免对SiO2载体造成破坏,在此条件下
190可以循环使用1000次以上。
190对铑的选择性远远高于溶液中的其他配阴离子,这是由于
190是通过氯配阴离子配位的,
190对其他配阴离子的选择性也很高,单级分离铑能够获得足够高的纯度。
TKK精炼厂的典型料液成分为含约17g/L Rh、6mol/L HCl,含有其他贵金属和贱金属,在该浓度下铑的单级回收率为98%,有时铑的回收率更高。吸附铑之后应用6mol/L HCl溶液洗去柱子上残留的料液,保证料液中的钯、铂从柱子中洗去,然后用蒸馏水洗涤,用5mol/L NaCl洗脱铑,该洗脱液的优点是可以避免铂沉淀、降低费用、还原铑之后可以循环使用。如果需要也可以使用钾盐或铵盐作为洗脱液。循环使用5mol/L NaCl洗脱液可以增加铑的浓度,洗脱后应用蒸馏水和6mol/L HCl溶液洗涤柱子,再生后的柱子即可重复使用。洗脱液中的铑还原为铑黑,铑的纯度高于99.95%。TKK从应用MRT分离铑中获得了与Impala相似的好处,其主要优点是从料液进入MRT分离系统到获得高纯度的铑盐及纯铑所需要的处理时间大大缩短。
我国台湾另外一个公司主要从事从半导体和电子废料中回收贵金属,目前已经成功运用MRT回收纯化钯和铑。
2.14.3.4 从废料中分离纯化钌
我国台湾某精炼厂已经建成187分离纯化钌的中间工厂系统,并成功运行了几个月,该系统由4个柱子组成,从含有铝、铁、钠及其他贱金属的6mol/L HCl溶液中分离钌,每个柱子中装1.5~2.0kg
187,钌以[RuCl5(H2O)]2-或[RuCl6]2-配阴离子形式键合到
187上,低的电势(300~400mV,Ag/AgCl电极)及氯离子浓度超过6mol/L保证钌以钌(Ⅲ)状态存在,并使存在较少的钌-氯离子,洗脱液为室温下的5mol/L NH4Cl,也可以应用其他洗脱液,如盐酸。洗脱液经氧化、沉淀钌为(NH4)2RuCl6,钌的纯度达到99.98%~99.99%,应用火法工艺将钌盐还原为海绵钌,图2-35为工艺流程[51]。

图2-35 MRT精炼钌工艺
完整的MRT分离纯化钌的商业体系由下列各步组成:
负载——187吸附6mol/L HCl料液中的[RuCl5(H2O)]2-或[RuCl6]2-配阴离子。
预洗脱(洗涤)——用6mol/L NaCl+0.1mol/L HCl洗涤,部分洗液循环使用。
洗脱——187吸附柱上的钌在室温下用NH4Cl溶液洗脱得到纯度较高的(NH4)2RuCl6溶液,部分洗脱液循环使用。
后洗脱(再生)——柱子用0.1mol/L HCl+6mol/L NaCl洗涤,部分再生液循环使用。
分离纯化钌的商业MRT系统:基于钌的中间工厂实验的成功,台湾某精炼厂正在建设两套商业规模的MRT分离纯化钌系统,每套由3个柱子组成,这些系统预计今年晚些时候投入运行。
表2-24对MRT与传统蒸馏工艺的优缺点做了对比。
表2-24 MRT与传统蒸馏工艺优缺点对比

应用MRT工艺分离纯化贵金属已趋于成熟,具有一定工业规模的生产线已分别在南非、日本等国家和我国台湾地区建成投产。
2.14.4 在电解液净化等领域中的应用
2.14.4.1 从铜电解液中除铋
LS日光铜业公司基本的工艺循环步骤为[54~56]:将电解液加入MRT柱中吸附;用水或2mol/L H2SO4溶液洗涤,用9mol/L H2SO4溶液洗脱铋(60℃),以水或2mol/L H2SO4溶液再生。根据加入物料中的铋含量,可以调节实际的周期。料液中铋含量越高,柱装填得越快,周期越短。铋加入含量大约为300×10-6时,总的周期为8~9h。每天的操作周期也取决于电解液中的铋含量。铋加入的含量为300×10-6时,工厂每天大约操作1.8个周期。
柱体大约装填了1400kg MRT83树脂,料液为来自电解车间的电解排放液。在铋柱进出口定期测量铋的含量。根据电解液中铋含量的不同,加入MRT工艺的电解液量也不同。
83树脂具有比较高的选择性及较高的脱铋能力。每个周期的脱铋量大约为42kg,脱铋量不受物料流量(20~40m3/h)影响。
铋的吸附曲线、洗脱曲线如图2-36、图2-37所示,锑的吸附曲线、洗脱曲线如图2-38、图2-39所示。

图2-36 83铋的吸附曲线

图2-37 83铋的洗脱曲线

图2-38 92锑的吸附曲线

图2-39 92锑的洗脱曲线
主要设备包括装填有83的柱体;几个缓冲槽、收集槽和产品槽;电解液的微过滤器及收集硫酸铋滤饼产品的压滤机。
硫酸氢铋在热硫酸(60℃)中具有较高的溶解度是产品高效回收的关键。在铋洗脱过程中,硫酸氢铋溶液过度饱和。随着洗脱液产品溶液的冷却,铋很容易作为高纯硫酸氢铋沉淀。用压滤机从冷却洗脱液产品溶液中回收沉淀铋产出硫酸氢铋饼,无铋洗脱液用于下个洗脱周期。高纯铋产品目前在行业内进行销售。
该工艺的主要优点包括:83树脂对铋有非常高的选择性及较高的吸附能力;负载阶段没有铜的吸收或损失;由于快速反应动力学,铋的负载可以获得非常高的电解液流量;洗脱液中铋产品的浓度非常高,且易于沉淀,形成可以通过过滤方法收集的高纯硫酸氢铋;硫酸氢铋有显著的市场价值,对降低操作成本有相当大的作用。
2.14.4.2 从铜电解液中除锑
无铋电解液送至92脱锑柱脱锑,然后电解液返回电解液回路。完成柱体装填和洗脱步骤后用水洗涤柱体。洗脱使用3mol/L NaCl+0.5mol/L HCl溶液[55,56],洗脱液排往锑沉淀槽。洗涤液作为补充水返回电解车间,由于后洗涤液可能含有氯化物,在处理前用NaOH溶液中和,NaOH溶液在较低pH值时加入含锑洗提液中,以中和溶液并形成锑的氢氧化物沉淀。固体沉淀在压滤机中回收。一部分澄清的滤液返回沉淀槽,剩余的溶液则循环至洗脱液槽,加入HC1后重新酸化。
2.14.4.3 从钴电解液中除镉、铁
177分离柱、D2EHPA萃取剂和S950吸附剂从含60g/L钴电解液中去除6mg/L杂质Cd2+。结果表明[57],
177分离柱对Cd2+有较高的选择性,其洗脱液中Cd2+被富集了480倍,不但有利于后续回收,而且克服了后两种方法需预处理、选择性较差以及易引起Co损失等缺陷。
48分离柱可去除Co电解液中的杂质Fe3+。该工艺先将经氧化并酸化的Co电解液通过
48分离柱,再以37%HCl溶液洗脱并回收吸附在分离柱上的Fe3+,但使用该方法后的洗涤液不可以循环利用,需进一步改进。
2.14.4.4 从锌电解液中除镍、钴
167分离柱可有效去除Zn电解液中的杂质Ni2+,经2000次以上循环使用,去除效率仅下降25%,平衡吸附量达到15~20g/kg。
138分离柱从含120~170g/L的Zn电解液中去除杂质Co。结果表明[57],
138分离柱对Co3+的亲和力远超过其他2价金属离子,因此在应用该工艺的过程中,需向Zn电解液中加入一定量的Fe3+,并不断通入O2,确保杂质Co以Co3+的状态存在,经过处理后的Zn电解液中杂质Co的质量浓度可低于0.1mg/L。该工艺的优势在于克服了传统沉淀法使用对环境有潜在危害的As2O3催化剂的缺陷,但在洗脱阶段需用到对环境有害的SO2。因此,如何最小化使用SO2仍是今后的研究重点。
2.14.4.5 从铜精炼电解液中脱除氯化物
智利国家铜公司的楚基卡马塔厂铜电解液中Cl平均浓度为22.1×10-6,装填循环4h之后,尾柱出口处溶液中Cl的平均浓度低于2.0×10-6。可以得出这样的结论:对于所示的料液浓度,3h是装填循环的最佳时间。物料平衡表明,超过3h的装填周期时,Cl的脱除效率大约为95%。的平均负载能力大约为0.060mol/L,表明了
将电解液中Cl控制在低含量时的效率。氯化物浓度非常高的电解液第142次循环的结果也非常好,工艺流程如图2-40所示[58]。

图2-40 从铜精炼电解液中脱除氯化物工艺流程
2.14.4.6 从矿山酸性排水(AMD)中回收铜
酸性排水液的pH值范围为3~5.5,设计的料量大约为19000L/min。系统包括并联的MRT多柱操作。工厂的总设计能力为年产100万吨阴极铜,料液中铜的浓度为(100~400)×10-6,排放液中铜的平均浓度低于5×10-6。大约为28BV(床体积,bed volume)时或者达到180000L的处理量完成全部负载。用稀硫酸(0.5mol/L H2SO4)进行每个柱体的洗脱,可以产生铜含量为3~5g/L的负载电解液。然后采用电积方法从电解液中产出高纯阴极铜,电积过程中产生的硫酸返回至贫电解液洗脱槽,洗脱在不到2BV时完成。使用氢氧化钙中和污水脱铜,然后排放。工艺流程如图2-41所示[58]。

图2-41 从矿山酸性排水中脱铜工艺流程
2.14.4.7 从硒还原液中除铋
肯尼科特铜业公司应用83含有对Bi3+阳离子选择性非常高的专有螯合分子,铋螯合分子与直径为0.25~0.5mm的硅珠共价结合,
83的初始总配位体有效容量最低为0.2mol/kg。
83捕获Bi3+后,在62~68℃时用9mol/L硫酸洗脱。铋在热酸中有非常高的溶解度。饱和溶液直接导入产品槽中,然后冷却至室温,进行铋的沉淀。铋饼的化学成分为Bi(HSO4)3。
240含有对[BiClx]n-阴离子特别是[BiCl6]3-阴离子选择性非常高的专有螯合分子。在这种情况下,螯合分子与直径大约为0.5mm的多丙烯酸酯珠粒结合。
240捕获铋氯阴离子后,用1mol/L硫酸洗脱,最终的产品溶液为含铋8~9g/L的盐酸。该溶液用氢氧化钠溶液中和,随后进行铋的沉淀,沉淀的铋产品以BiOCl/Bi(OH)3混合饼的形式收集。
83能够在酸性硫酸盐和一些含氯化物的溶液中起作用,而Super-
240只能在酸性氯化物溶液中起作用。工艺流程如图2-42、图2-43所示[54~56]。

图2-42 83除铋工艺流程

图2-43 240除铋工艺流程
240和
83试验规模的柱体系统表明:铋回收率较高(低铋吸附余液中Bi的浓度小于1g/L);铋固体产品中铋纯度较高(
240,铋金属纯度为97%~99%;
83,铋金属纯度为99.9%~99.99%)。在试验期间,没有检测出
铋结合能力的损失。
83的优点为:即使当物料氧化还原电势值较低时,物料也不需要进行氧化还原电位调节;减少化学药品的消耗,不需要HCl和NaOH或者其他碱和氧化剂,只需要少量的硫酸;铋固体产品过滤产生的吸附余液大部分循环,减少了废液量;铋洗提液中较高的铋浓度,使洗提液量更少,进一步减少了该过程消耗的化学药品量;由于销售回收的硫酸氢铋获得的潜在经济收益可以减少操作成本,因此提供了有吸引力的投资回报。
240的优点为:物料无需稀释,尽管对于低氧化还原电势的情况来说,可能必须进行氧化还原电位的调节,如同试验中用漂白剂物料进行的调节;与输入的新鲜料液相比,由于无需进行物料稀释以及容量高出6倍(与Su-
83相比),使得输出的低铋吸附余液的稀释度小得多(
240总的稀释系数为1.7,
83总的稀释系数为6);与
83相比,
240的铋容量更高,对初始的
需求更低;操作的温度更低,温度要求的灵活性更大,这就导致了工艺操作的灵活性更大;因为操作温度要求及在树脂柱上沉淀吸附余液中铋的机会减小;工艺的洗涤、洗脱阶段最大的酸强度更低;实际上,产品流中的铋完全进入铋固体产品中;由于销售回收的铋盐,获得的潜在经济收益可以减少操作成本。
2.14.4.8 从浓硫酸中除汞
浓硫酸在室温和600~900mV(vs Ag/AgCl)的氧化还原电势下(用SO2和H2O2调节),以每小时30倍固定床体积的流量依次流过一组除汞塔,硫酸中的汞被捕获于塔内装填的SuperLig材料上。在上述氧化还原电势下,汞离子呈+2价氧化态,从而可最有效地予以去除,而SuperLig材料也不会因配位体的氧化而失效。通常除汞塔以滑道的形式安装,各塔首尾相连,串联运行。酸从首塔流入,依次流经各塔,由尾塔流出。首塔达到汞饱和后即退出运行,第2个塔接替成为首塔。装有新鲜SuperLig材料的塔总是作为最后一个精脱塔。这种操作方式可使SuperLig材料的除汞能力发挥到极致。SuperLig材料可一次性使用,也可多次重复使用。一次性使用往往用于汞的精脱。在这种情况下,饱和SuperLig材料的处置只需满足环保要求即可。如多次重复使用,可采用酸性硫脲对SuperLig材料进行洗提再生,汞则以HgS的形式加以回收。多塔串联的工业试验已在欧洲的几个主要的金属冶炼厂进行,无论是一次性流程还是多次循环流程均已获得成功。
2.14.5 在核燃料后处理中的应用
644分离柱对137Cs离子的吸附选择性。结果表明[59],
644能够有效地去除并回收核燃料废水中的137Cs离子,经其处理的废水中137Cs离子的质量浓度可低于0.001μg/mL,回收纯度达到99%以上。应用
620分离柱分离核燃料废水中的Sr与Ra离子。研究表明,
620对Sr离子有较高的选择性,可去除废水中85%以上的Sr。
639分离柱能够有效地去除核燃料废水中的
,去除率高达95%以上,但是对于处在低氧化态的Tc,
639分离柱的选择性较差,而
644分离柱的去除效果更佳。
171分离柱可用于治理核燃料废水中的[
],经MRT系统处理的废水中残留的铀可低于0.005μg/mL。
2.14.6 国内相关研究概况
2.14.6.1 分子识别材料的合成
冠醚、大环芳烃的合成,早已引起了国内众多高等院校、科研单位科研工作者的重视,人们先后对离子识别型杯芳烃、带支链的氮、硫代杯-4-芳烃、硫代杯-6-芳烃、硫代杯-8-芳烃、含硫杂杯芳的大环冠醚和非环多醚等均进行了大量的研究,并研究了它们对各种金属离子的识别性能[60~67],特别是近年来浙江大学对大孔硅基-杯[4]-冠-6、异丙氧基杯[4]-冠-6等超分子识别材料吸附Cs+等核燃料后处理技术方面进行了大量的研究工作,取得了一系列科研成果[68~75],缩小了与国际研究水平的差距。
2.14.6.2 分子识别材料的结构表征
人们对用于PGMS的分子识别材料2、
95及
190进行了初步分析,得到了许多有价值的信息。下面我们还将继续进行固体质谱、固体核磁、共振光谱等诸多表征分析。
①用于识别分离钯的2 白色颗粒,粒度分布为d10316.530μm、d50446.966μm、d90629.222μm;比表面积(BET)232.180m2/g,孔容(TPV)0.7895mL/g,孔径(APS)68.0086Å;元素分析含量(%):C 11.22;H 1.622、N 1.073、O 27.51;XRF分析含量(%):SiO293.14、S 2.456、Na2O 0.48、Fe2O30.116、Al2O30.11、CuO 0.018。IR主要吸收峰(cm-1):3426(s)、1629(w)、1482(w)、1102(s)、803(s)、692(w)、471(s)。其SEM分析图谱如图2-44所示。

图2-44 2 SEM图谱
②用于识别分离铂的95 白色略带黄色颗粒,粒度分布为d10316.353μm、d50433.171μm、d90591.104μm、比表面积(BET)137.428m2/g,孔容(TPV)0.4859mL/g,孔径(APS)70.7176Å;元素分析含量(%):C 14.61、H 3.245、N 1.709、O 22.28;XRF分析含量(%):SiO268.8.14、S 14.118、Cl 5.41、Al2O32.6、I 0.63、MgO 0.38、PbO 0.325、NiO 0.26、TiO20.17、Fe2O30.15、CuO 0.049、ZrO20.032。IR主要吸收峰(cm-1):3426(s)、1631(w)、1101(s)、799(s)、471(s)。其SEM分析图谱如图2-45所示。

图2-45 95 SEM图谱
③用于识别分离铑的190 白色略带黄色颗粒,粒度分布为d10175.689μm、d50249.563μm、d90353.752μm、比表面积(BET)213.868m2/g,孔容(TPV)0.8825mL/g,孔径(APS)82.5287Å;元素分析含量(%);C 7.529、H 1.708、N 2.518、O 41.08;XRF分析含量(%),SiO299.38、Al2O30.26、S 0.04、CaO 0.087、Na2O 0.084、TiO20.04、MgO 0.022、Fe2O30.0116、ZrO20.011、CuO 0.0058。IR主要吸收峰(cm-1):3425(s)、2949(w)、1634(w)、1456(w)、1102(s)、803(s)、471(s)。其SEM分析图谱如图2-46所示。

图2-46 190 SEM图谱
2.14.6.3 从汽车失效催化剂中分离铂族金属
近几年来,在笔者的建议下,昆明贵研催化剂有限责任公司(SPMC)和美国IBC公司在应用MRT技术从失效汽车催化剂浸出液中分离铂族金属方面进行了实质性的合作,IBC公司已经完成了实验室实验、工业生产规模的设计。原则工艺流程如图2-47所示,所用分子识别材料的性能如表2-25所示。实验结果证明,应用MRT技术从失效汽车催化剂浸出液中分离铂族金属具有流程短、分离效率高、可以直接获得纯度很高的铂族金属淋洗液、产品纯度高、铂族金属收率高等优点。美国IBC公司已经向昆明贵研催化剂有限责任公司提供了分离钯、铂、铑的材料,目前昆明贵研催化剂有限责任公司正在验证美国IBC公司的实验结果。

图2-47 MRT从汽车失效催化剂中分离铂族金属工艺流程
表2-25 SPMC应用MRT从汽车失效催化剂中回收铂族金属(PG-Ms)

原始料液:Pd 0.1427g/L、Pt 0.094g/L、Rh 0.03g/L,每年250d,每天15h。钯原液日处理量6.25m3,铂原液日处理量6.50m3,铑原液日处理量7.115m3;钯每天处理2.3批,铂每天处理1.86批,铑每天处理3.51批。
洗脱剂:Pd-氨水;Pt-硫脲(65℃,由于原液中铁的缘故);Rh-氯化钾。
对于含铁低的物料,用133吸附铂,水即可在常温下洗脱。
目前,贵研(易门)资源公司引进了铑的分子识别系统、金川集团股份公司即将引进建立年产500kg铂族金属的分子识别系统。
总之,经过近20年的持续发展,MRT分离稀贵金属的技术日趋成熟[76~78],我国由于铂族金属资源及其匮乏,应用MRT实现其高效分离就引起了人们极大的兴趣[59,79],MRT分离贵金属的次序:①Au-Pd-Rh-Pt;②Au-Pd-Pt-Rh;③Au-Rh-Pd-Pt;④Au-Pd-Pt-Ir-Rh;⑤Ir-Rh。MRT分离贵金属的优点:贵金属单级分离效率为99%;产品纯度为99.95%~99.99%;贵金属循环快-总的处理时间缩短;贵金属回收率增加-过程损失减少;贵金属生产费用降低-过程中所应用的化学试剂减少;步骤减少;维持费用降低;生产周期缩短-降低了金属投资费用,使金属易销售;有利于过程控制;可以处理稀或高浓度的料液;生产的金属盐可以直接销售或还原为市场所需要的金属;快速及半连续工艺;可以处理任意大小体积的溶液;负载及洗脱的流速均很高;部分溶液可以循环使用;简单、紧凑的设备需要的空间很小;贵金属安全风险降低-分离体系较小;产品可以多次循环使用、寿命长。目前,应用于分离稀贵金属的分子识别材料总结于表2-26中。
表2-26 应用于稀贵金属分离提纯的分子识别材料

应该指出的是,分子印迹技术(molecular lmprinting technique,MIT)、固相萃取技术(solid phase extraction,SPE)在分离机理、分离性能、选择性等诸多方面均不同于分子识别技术(molecular recognition technology,MRT),不能将其混为一谈。