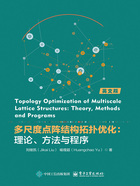
1.2.4 Inverse homogenization
With the help of homogenization, using microstructures to represent intermediate densities is feasible. However, the microstructures required are not always known. Homogenization can approximate the effective properties of microstructures, and inversely, it can also be exploited to design microstructures with target properties, named the inverse homogenization approach first proposed in 1994 by Sigmund[12].
Aiming at achieving specific properties of a microstructure, the optimization problem is formulated as,

where K is the global stiffness matrix, U and F are the global displacement vector and the external force vector of the test case, respectively.αis the vector for element volumes, and is the upper bound on the volume fraction. The objective c (EH) is an objective function established based on the homogenized elasticity tensor components.
The optimization problem (1-24) can be solved using the modified SIMP approach. According to the calculation formula of the effective elasticity tensor EH [Eq.(1-18)] and the density-property interpolation model [Eq.1-4], the sensitivity of the objective function is computed using the adjoint method,

where k0 is the sub-element stiffness matrix with unit Young's modulus. When a uniform mesh is used, the element volume αe is set to 1 and therefore .
The optimization problem (1-24) can be solved by gradient-based methods such as the optimality criteria method introduced above, or the method of moving asymptotes (MMA)[13], which can integrate more constraints like isotropy and manufacturability.
A MATLAB implementation of inverse homogenization by SIMP is given as follows. And Fig.1-2 displays three microstructures generated by inverse homogenization.

Fig.1-2 Several microstructures generated by inverse homogenization[14]
The MATLAB implementation of inverse homogenization by SIMP


