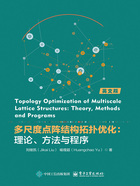
1.2.3 Homogenization
The intermediate material densities in minimum compliance problem have to be given physical meanings and one interpretation is to represent them with microstructures. The mechanical properties of microstructures can be computed through homogenization method. The effective mechanical properties of a microstructure can be expressed by the effective elasticity tensor EH, which satisfies,

where σ and ε are the second order stress and strain tensors. EH is the fourth order elasticity tensor. Applying Voigt notation, Eq.(1-13) can be written in matrix form,

Assuming the microstructures are periodically repeated in the macro-structure and the length scale of the microstructures is much smaller than the macro-structure, the equivalent effective elasticity tensor EH of the microstructure can be computed through,

where |Ω| denotes the unit cell volume, Epqrs is the stiffness tensor of base material, represents the prescribed macroscopic strain field (in 2D there are three; e.g., unit strain in the horizontal direction (11), unit strain in the vertical direction (22), and unit shear strain (12 or 21).
The periodical boundary condition is applied to the representative unit cell, i.e., the opposite boundaries are given a consistent displacement difference according to . Under such a periodic boundary condition, the locally varying strain field
is obtained by solving the elasticity equation:

where υ is a virtual displacement field belonging to the admissible displacement space Hper (Ω, R3).
For most practical problems the homogenization is performed numerically by discretizing and solving Eq.(1-16) using the finite element method. This is often referred to numerical homogenization. The homogenized effective elasticity tensor EH can be reformulated as the sum of the integration over finite elements, Eq.(1-15) is discretized by:

where is the sub-element displacements solved from Eq.(1-16), and ke is the sub-element stiffness matrix.
With energy-based homogenization method, Eq.(1-17) can be illustrated as the sum of elementary mutual energies by the induced displacement field, given by:

where stands for the elementary mutual energy, and
denotes the induced sub-element displacements.
As introduced above, the effective elasticity tensor EH can be calculated by homogenization method. The effective elasticity tensor of an anisotropic microstructure has 36 independent elements. This number can be decreased because there are different symmetries in the elastic properties of materials. Below give several common types of symmetries.
The elasticity tensor of an orthotropic material has 9 independent elements, which has the form of

The mechanical properties of an orthotropic material are unique and independent in three mutually perpendicular directions. As a simple case of orthotropy, the cubic material has the same mechanical properties in three mutually perpendicular directions. The elasticity tensor of a cubic material has 3 independent elements, which has the form of

The isotropic material has the same mechanical properties in all directions. The elasticity tensor of an isotropic material has the following expression,

There are only 2 independent elements in the elasticity tensor of an isotropic material. The mechanical properties satisfy,

where G is the shear modulus, E is Young's modulus, and v is the Poisson's ratio. Therefore, an isotropic measurement A named Zener ratio can be defined for cubic materials,

If the Zener ratio of a cubic material satisfies A=1, the material realizes elastic isotropy.
Finite element implementation of numerical homogenization written in MATLAB



