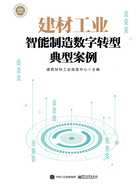
04 绿色新型墙体材料智能工厂——茌平信源环保建材有限公司

企业简介
茌平信源环保建材有限公司隶属于信发集团,成立于2017年7月,注册资本为1亿元,是一家综合利用工业副产废弃资源粉煤灰、脱硫石膏、炉渣、电石渣生产粉煤灰蒸压环保砖、环保型蒸压加气混凝土砌块、研发生产销售于一体的科技环保型生产企业。
该公司是国家发改委“双百工程”示范基地项目、国家大宗固废综合利用基地项目的承接单位,中国建筑材料联合会石膏建材分会副理事长单位,2019年被认定为国家级高新技术企业,2020年被认定为山东省“专精特新”中小企业,2020年度山东省重污染天气重点行业绩效评级引领企业,荣获2019年度山东省循环经济科学技术奖三等奖、山东省建筑节能科学技术奖三等奖,2020年被评为山东省建筑节能协会副会长单位。公司生产的蒸压加气混凝土砌块被评为“国家级绿色设计产品”。公司于2019年开始建立、实施ISO9001质量管理体系、ISO45001职业健康安全管理体系、ISO14001环境管理体系、ISO45001能源管理体系,并于2020年获得认证证书。
公司研发技术力量雄厚,在工业固体废弃物综合利用技术的研究、开发与应用方面均处于同行业领先水平,拥有聊城市工业固体废弃物资源综合利用重点实验室、山东省新型墙体材料科研实验基地等研发平台。目前已获得18项实用新型专利,是聊城市知识产权保护的重点联系单位。
案例实施情况
总体设计
本项目是茌平信源环保建材有限公司对热电厂产生的脱硫石膏、粉煤灰等工业固废全部吃干榨净,资源化的循环利用,采用工业互联网、工业大数据、人工智能、智能控制等先进技术手段,搭建绿色新型建筑材料信息化、数字化、智能化的系统平台,推进智能装备、自动化控制、制造执行系统(MES)、资源计划管理系统(ERP)、智能物流等技术在绿色新型建筑材料行业上的应用,将新一代信息技术贯穿于设计、生产、管理、运输等环节,构建以绿色新型建筑材料产品工艺和质量为基础,以生产智能化为核心,以提高产品质量为目的,年产1亿平方米脱硫石膏纸面石膏板、280万立方米粉煤灰加气砌块和2.4亿块粉煤灰蒸压砖的绿色新型墙体材料智能工厂。实现自动化生产线无固定操作人员,柔性化生产,产品全生命周期可追溯,核心装备安全可控,企业内部信息互联互通,生产效率和产品质量提升等目标。
项目总体技术架构分为物理层、采集层、网络层、平台层、应用层和展示层。

总体架构
物理层是构成智能工厂的物质技术基础,由核心智能制造装备、自动化生产线、车间智能化物流系统等智能设备组成。
采集层包括可编程逻辑控制器(PLC)、数据采集与监视控制系统(SCADA)、分布式控制系统(DCS)等。
网络层是工业互联网内网,建设统一的工业互联网架构,由有线和无线网络构成全厂万物互联的“高速公路”。
平台层构成企业的大数据中心,由数据仓库、数据算法引擎等构成。
应用层实现工厂的业务集成,实现面向工厂的生产管理和经营管理,包括制造执行系统(MES)、企业资源计划系统(ERP)、智能安全管控系统等。
展示层由手机端、PC端和智慧大屏组成,主要对工厂运营状态进行展示。
实施内容与路径
本项目研制面向绿色新型墙体材料生产线的核心智能装备、智能物流装备、数字化车间、智能工厂信息化管理平台等装备系统,建设无固定操作人员的绿色新型墙体材料智能工厂,全面提升产品设计、工艺、制造、检测、物流、信息化等产品全生命周期各环节的智能化水平,实现数字化转型的应用研究与突破。
项目分为三大任务:
任务一:工业互联网内网建设和大数据中心建设;
任务二:采用人工智能、机器视觉和工业机器人,完成智能装备研发和智能化生产线的建设;
任务三:业务系统集成,建设基于MES的管控一体化智慧管理平台。
实施路径:
以核心智能制造装备、智能化生产线、车间智能物流装备为重点建设方向,采用工业互联网、人工智能、大数据、自动控制技术,并充分利用研发设计、生产经营管理、制造执行管理等信息化系统,建立绿色新型建筑材料智能工厂。
采用机器人、机器视觉、AGV、智能配料系统等技术装备实现自动化生产的闭环,实现从原料精准制备、成型、干燥、质量在线控制、自动化包装和自动装车发运全流程的智能化生产。
建设工业互联网内网和大数据中心,实现企业内外部的硬件设备数据采集和连接,满足工厂内部智能化、网络化及与外部信息交换的需求,实现网络联通、数据打通、业务打通。
通过基于MES系统的智慧管理平台,完成对ERP、MES、DCS等多系统的融合应用,实现透明化、可视化、智能化的生产管理和运营决策。
案例特点
采用机器人、自动装车系统和全自动包装机等智能装备,实现了无固定操作人员的大规模自动化生产。
采用在线质量控制系统,在线监测产品的宽度、厚度及湿度,通过机器视觉,对产品进行在线检测和分析,形成了全流程的质量管控体系。
通过分布式控制系统DCS及PLC实现生产线的一键启停。专家优化控制完善了生产参数的自动跟踪和在线修改配方的功能,减少了原辅材料的浪费,保障了产品质量的稳定性。
采用电厂余热作为烘干系统的热源,采用三组十二层烘箱结构,做到了能源利用最大化、温度控制自动化、产量平衡智能化。
智慧管理平台、工业互联网内网和数据中心的建设,在数据融合、业务打通等方面进行了集成应用,实现了工厂透明化、智慧化管理和决策。
实施效果
本项目利用电厂排出的灰、渣和脱硫石膏,建设新型制砖、砌块、脱硫石膏板项目,上游产品的废料成为下游产品的原料,减少固废储存和运输,达到“出灰不见灰、出渣不见渣、污染变资源”的目的。粉煤灰和脱硫石膏粉等原料通过管道直接输送到工厂,减少物料运输中间环节的环境污染。脱硫石膏生产纸面石膏板项目,采用先进的脱硫石膏二部煅烧法工艺,100%脱硫石膏为原料生产纸面石膏板。
项目实施后,实现了自动化的闭环生产,数据采集率达到了90%,车间内数控设备占80%以上,主要设备联网率达到100%,实现了工厂的互联互通。生产设备运行状态实现了实时监控和故障自动报警,生产任务指挥调度实现了可视化,关键设备能够自动调试修复;车间作业基于主生产作业计划自动生成,生产制造过程中物料投放、产品产出数据实现自动采集、实时传送。根据车间生产制造特点和需求,配备相应的车间环境(热感、烟感、温度、湿度、有害气体、粉尘等)智能监测、调节、处理系统,实现对车间工业卫生、安全生产、环境自动监控、自动检测、自动报警等智能化控制,安全生产防护符合行业规范要求。生产过程采用二维码、条形码、移动扫描终端等自动识别技术,实现对物品流动的定位、跟踪、控制等,车间物流根据生产需要实现实时配送和自动输送。通过智能化建设,工厂生产效率提高25%,用工成本降低50%以上,产品不良品率下降80%,节约能源15%,实现了较好的经济效益。
项目实施后,CCTV-10《走近科学》栏目于2019年5月22日播放的“石膏新生”节目以此为例,重点介绍了热电厂固废脱硫石膏的资源化利用做法。中国建筑材料联合会组织的第十四届全国石膏技术交流大会于2019年11月3日在聊城举行,由信发集团承办。会议期间,与会专家重点观摩,该公司的项目得到了专家学者的一致好评。