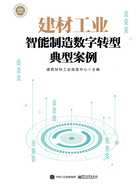
03 建设智能化粉体材料绿色工厂——贵州正和天筑科技有限公司

企业简介
贵州正和天筑科技有限公司(简称正和天筑)成立于2006年4月,坐落于清镇市站街镇经济技术开发区工业园区,是贵州省第一家利用固体工业废弃物、综合利用生产磷石膏基/水泥基等预拌粉体材料的民营企业,在职员工58人,其中技术人员15人,硕士研究生以上学历的有3人。
企业拥有25件专利(2件发明专利)和5件软件著作权,此外,还有8件专利(7件发明专利)处于实质审核阶段,6件专利处于受理阶段,现已建成一期年产120万吨磷石膏基、水泥基普通、特种砂浆、地铁盾构注浆料、3D打印砂浆等预拌产品的国内首家粉体绿色材料智能无人工厂。
案例实施情况
总体设计
项目以PLC、DCS、SCADA、SIS、IPC、MES等工业控制系统为基础,建设智能化生产线和动态生产管理监控平台,建成年产120万吨粉体材料智能化生产线,同步建立产品数据管理分析系统(PDM)、智能制造执行系统(MES)、设备联网控制系统(DNC)、生产数据管理分析系统(MDC)、仓储物流管理系统(WMS)、客户关系管理系统(CRM),与企业资源计划(ERP)构成完整体系,建成全数据融通管控平台,业务链从智能接单、排产、物料配送、质量监控、客户资源管理、产品追溯,到产业链协同、远程一键操作,依据数据自动分析,实现精准决策,围绕产业链的数据共享和互联互动,推动企业高质量发展。
实施内容与路径
该公司数字化控制平台是践行工业互联网智能制造模式的集中体现,深度融合数字技术、信息技术、智能技术与制造技术,以制造工艺流程和参数指令、智能装备和生产线、自动化物料配送系统、各级管理系统集成,实现面向产品规划、制造、销售和服务等产品全生命周期的先进的综合运行模式。
企业转型建设主要从两个方面着手:
1.建设智能化自动控制生产线
智能化自动控制生产线大数据架构体系分为五层,每层分工不同,形成上下交互的整体架构。
(1)生产现场(第一层):将各种设备、各节点传感器、各执行器等有效连接。
(2)产线控制(第二层):采用可编程控制器(PLC)、集散控制系统(DCS)、数据采集与监视控制系统(SCADA)、安全仪表系统(SIS)、远程终端单元(RTU)、IPC等工业控制系统,建立基于管理理念、生产模型、标准规范、优化的业务流程,结合行业相关应用,进行智能工厂整体规划,建立企业管理信息系统。
(3)数据采集与操作(第三层):SCADA系统是以计算机为基础的生产过程控制与调度自动化系统,能够实现对现场运行设备的监视和控制。
正和天筑SCADA系统分为两个层面,即客户/服务器体系结构。服务器与硬件设备通信,进行数据处理和运算。操作人员可进行人机交互,如用文字、动画显示现场的状态,并实现对现场开关、阀门的操作。另一种“超远程客户”的运用,实现了Web发布在Internet上的监控。硬件设备(如PLC)既可以通过点到点方式连接,也可以以总线方式连接到服务器。
正和天筑SCADA通信结构系统中的通信分为内部通信、与I/O设备通信和外界通信,主要由以下部分组成:监控计算机、远程终端单元(RTU)、可编程逻辑控制器(PLC)、通信基础设施、人机界面(HMI)。
(4)车间管理(第四层):正和天筑智能化生产系统及过程是涵盖智能工厂的核心,是对生产过程的智能管控,作为生产执行层,处于中间桥梁的位置,连接了上下层级,使整体架构互融互通,起到了支撑整个架构的枝干作用。
(5)企业管理(第五层):正和天筑整合了企业信息管理系统,与智能生产线数据相互融通、相互支持、相关依赖,形成一个完整的闭环来发挥整体效用,实现了产品全生命周期管理,贯穿产品的产能规划、产品设计、工艺设计、制造运行、检测及服务过程,实现价值链端到端的数字化流程优化和集成。

智能化自动控制生产线大数据架构体系
2.动态数字化管理平台
(1)采用设备联网控制系统(DNC),自动化控制技术、检测监控技术和远程监控技术,实现生产过程的计算机控制,采用安全自动化设备代替人工操作,消除安全隐患,提高生产安全性,实现全生产工序环境下的无人操作;
(2)建立智能制造执行系统(EMS),深度融合数字技术、信息技术、智能技术与制造技术,以需求产品数据、优化工艺流程、协调生产装备为核心,实现自动化生产;
(3)建立产品数据管理系统(PDM),实现信息收集、分析、处理,以制造工艺流程和参数指令、智能装备和生产线、自动化物料配送系统集成,面向产品规划、制造、检测和服务等产品全生命周期各个环节,是动态整合与优化的一种先进的综合制造模式;
(4)建设综合管理信息和大数据分析系统,实现企业生产数据上传、汇总、存储、分析、预警、报警、查询等功能;
(5)建立仓储物流管理系统(WMS),实现无人过磅等物资管理、取数、数据集成汇聚系统;
(6)建立客户关系管理系统(CRM),通过数字化信息系统,旨在快速响应市场、满足客户个性化需求,高效、优质、柔性、安全经营;
(7)建立企业资源计划系统(ERP),实现供应链、物流、成本等企业管理功能,推动企业各系统的无缝集成,实现产业结构调整和优化。
公司以智能制造、大数据管理等技术为基础,以各环节采集的大量数据为核心,以产品、服务、流程优化重构为手段,利用智能制造技术,如工业物联网、工业大数据、云计算等,实现了企业绩效和竞争力的根本性提升。

数字化管理平台
案例特点
该公司为固废再造行业绿色转型升级树立了融合标杆,将生产经营全过程控制数据与ERP信息管理系统完美融合,突破接口技术壁垒,真正实现了与互联网的融合;
独创与众不同的控制系统“黑匣子”,可利用主控机屏幕录像记录+操作痕迹日志记录+操作痕迹数据库记录,多管齐下,严格把控生产安全和质量安全;
严格遵循高于国家标准的计量精度控制算法,通过严密而灵活的参数配置机制,在精确计量的前提下提高生产效率;
运用最新的网络通信技术,可将控制系统操作岗位、生产配比核发岗位、生产调度指令岗位和厂区视频监控中心集中,构建“智慧工厂”的核心,完美地实现远程集控;
自动记忆生产线关键机电元器件的工作次数或累计工作时间、主机运行记录,实时进行产能分析,记忆特殊情形下的手动消耗数据,为企业物资采购部门提供极有价值的决策支持;
独具匠心的“一机双控”控制模式,大幅提高了生产线自动化控制水平,助力混凝土企业真正实现减员增效。
实施效果
该公司通过打造集产、采、销、运、金融、数据为一体的产业服务体系,为产业链上下游企业提供一站式解决方案。项目建成投产后,真正实现了提质、降本、增效的目标。员工人数从近400人降为54人,一线员工人员配置比率大幅降低,研发人员、技术人员配置比率提高到26%,销售人员配置比率提高到13%,工作重心也相应地向技术创新和拓展市场规模转移,管理模式从金字塔式架构转变为扁平化式架构,在大大降低人力成本的前提下提高了管理效率;自动化生产线将员工与生产线完全分离,杜绝安全事故隐患;生产效率得到显著提高,生产能力提高3倍;产品实现了定制化生产,产品种类扩大3倍,合格率达到99.98%;现场环境彻底告别灰尘四溢的情况,降低了员工患上职业病的概率;材料配方可以实现0.1~2kg以下微添加物料自动计量,精度最高控制在±5g内,为新产品研发及技术创新提供了可靠的保障,彻底颠覆了传统材料“傻大粗”的印象。这一切为固废再造行业转型升级提供了一条新的发展路径。
该公司所产生的效益主要体现在以下几个方面:
(1)优化销售环节,销售成本降低3%,提升客户服务水平,加速货款回收效率;
(2)实现资金流、物流、信息流的统一管理,解决了内部信息不畅通及管理困难等问题;
(3)业务数据实时处理,决策命令准确下达;减少经营成本、降低经营风险、快速应对市场变化;
(4)库存下降15%~20%。具有自定义原辅料和砂浆成品预警功能,使企业库存投资减少,库存周转率提高15%,流动资金占用率降低10%;
(5)延期交货率降低16%。企业准时交货率平均提高18%,误期率平均降低15%,使企业效率大大提高,信誉增强;
(6)采购提前期缩短25%。采购人员有了及时准确的生产计划信息,就能集中精力进行货源选择,了解生产问题,缩短采购时间,节省采购费用;
(7)管理质量更科学,与生产、研发、销售相结合,对整个业务流程进行有效控制和规范化管理,并对生产质量进行有效溯源,制造成本降低12%。由于库存费用下降,劳动力节约,采购费用节省等一系列人、财、物的效应,生产成本得以降低。原辅料采购结构管理规范,确保采购部门与质检部门严格执行任务,提高产品质量;
(8)管理水平提高,协助员工快速完成任务,提高了工作效率,同时使生产能力提高20%;
(9)成本核算自动化,实时报表统计及月底结算能够瞬间完成,确保准确、快速地提供各种成本数据,提高财务人员的工作效率;同时实时监控财务信息,随时掌握资金动态。
目前,该公司具有年产120万吨粉体材料的生产能力,每年可消化磷石膏100万吨、赤泥3万吨、粉煤灰10万吨等,通过重塑产业链条,增强产业的生态化信息共享能力,推动产业链企业实现智慧增长,充分发挥数字赋能功效。