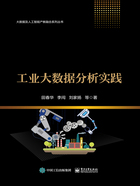
1.1.2 支撑技术的演化
随着传感器和物联网技术的发展,对物理过程的感知变得更加实时和密集,系统可以得到实时反馈。将这些数据有效应用到实际控制过程中,从而进一步提高设计水平、控制水平、系统可靠性和运行效率,是近期物理信息系统(Cyber-Physical System,CPS)、数字孪生(Digital Twin)等提法的基本出发点。基于这些海量数据的数据分析是工业企业数字化转型的关键技术。
MES(Manufacturing Execution System)、ERP(Enterprise Resource Planning)、SCM(Supply Chain Management)等信息系统在企业中的深度应用以流程为中心,解决了信息及时流转和有序管理等问题,但业务决策和创新层面缺乏全局信息,需要依赖领域专家经验。这种全局信息体现为以物理实体为中心的全生命周期模型和全要素信息模型。大数据技术可以在一定程度上将局部化的信息有机组织起来,数据分析技术可以从组织好的数据中挖掘有用信息。
一些关键应用领域在技术上不断深化,实现了跨领域的融合。在制造环节,以CAE(Computer Aided Engineering)、MBE(Model Based Engineering)[4]等技术为支撑的“数字化工厂”倡导实现设计数字化、管理数字化、生产过程数字化、产品数字化和制造装备数字化。以设备全生命周期的相关数据为基础,对整个生产过程进行仿真、优化和重组,实现了工厂中重要过程和资源的整体规划、评估和持续改善。在规划中,生产中的所有元素通过计算机辅助方法建模。这种方式使产品的物理制造过程达到所有质量、时间和成本目标。在设备运行和运维环节,以DCS(Distributed Control System)、SCADA(Supervisory Control and Data Acquisition)为核心的运行监控系统实现了整体系统环节过程参数的监控与采集,TSI(Turbine Supervisory Instruments)、TDM(Turbine Diagnosis Management)[5]等系统实现了关键设备状态监控与诊断,为“设备数字化与智能化”奠定了技术基础。这些技术的发展,为工业大数据在更大时空范围上的应用提供了契机。