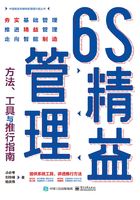
1.2.4 降低差错率,改善质量
6S与企业质量管理息息相关,这与其起源国日本不无关系。当时,日本制造在第二次世界大战后被公认为质量低劣的代名词。为了扭转这一局面,日本各大公司开始寻求质量改进的方法。这时它们选中了质量管理大师戴明博士,他开发了一套改进系统PDCA[P(Plan)—计划,D(Do)—执行,C(Check)—检查,A(Action)—行动(或处理)]。一个PDCA循环结束后,再进入下一个PDCA循环,周而复始。
在追求质量的道路上,从20世纪50年代到70年代,日本涌现了大批的质量管理方法,有石川馨的质量管理七种工具、田口玄一的田口法,还有丰田的JIT(准时化生产)、Kanben(看板生产)、Kaizen(持续改善)、QFD(质量功能展开)、新七种工具等。这一时期也是5S管理在日本不断发展和成熟的阶段,尤其是丰田,它将5S视为管理的起点,并将其作为精益化管理的基础。这种环境决定了5S成为推动质量管理的一种基础工具。PDCA模型如图1-13所示。

图1-13 PDCA模型
6S推行是一项需要长期坚持的基础性管理活动,一旦停滞又会回到原点,现场再次陷入混乱、看板缺失、不要的物品逐渐多了起来等,直接导致现场质量管理水平下降或原地踏步。
将6S或6S中的某一项纳入PDCA管理,可以有效避免这个问题。6S与PDCA循环改进关系如图1-14所示。

图1-14 6S与PDCA循环改进有关系
大家可以看到,随着6S推行水平的不断提升,企业的质量管理水平也在稳步提升。
企业通过6S活动可以营造一个精益求精、秩序井然的工作现场,对质量改善有积极的意义。6S与质量改善的关系如表1-3所示。
表1-3 6S与质量改善的关系

产品质量维持和管理依赖一个良好的生产运行环境。良好的人文素养和透明的现场环境可以有效降低差错率,改善质量。
以良好的工作态度和工作行为,取代漫不经心、凡事不以为然是增强质量意识、强化质量行为,降低作业失误、作业事故的根本。
丰田生产方式的创始人大野耐一,在做经理时十分重视员工的素养教育。那时工厂丢失看板的事情经常发生,不知该如何是好的企业顾问林南八先生决定以增加看板数量来解决此事。这样一来,有时就会出现多余的看板。知道这件事后,大野耐一勃然大怒,令林南八“去找回丢失的看板”。可是,林南八找了一个小时也没有找到。
林南八把情况如实地向大野先生做了报告。大野先生又一次大声斥责道:“只过了一个小时就说‘找不到’,这算什么事?”于是,林南八又去四处寻找,可还是没有找到。
大野先生问:“你知道为什么找不到吗?”林南八不知该如何回答才好。此时,大野先生又补充了一句:“这很简单!只是因为你没有一直找,直到找到为止!”
不肯服输的林南八又四处寻找了一番,终于找到了丢失的看板。原来是被油黏在了几个零件箱的底部。林南八对此加以改善后,看板就再也没有丢失过。
增加看板数量只不过是权宜之计,不管增加多少,还是会丢失的。解决人的“问题”才是解决现场问题根源的关键。
优良的品质来自优良的工作环境。通过经常性的清扫、点检,不断净化工作环境,避免污物损坏机器,维持设备的高效率,提高品质;通过各类看板,规范操作,预防质量事故等。这些6S管理方法,可以有效提高现场质量管理水平。
生产线状况看板如图1-15所示。

注:当3号工位发生异常时,按下黄色警报按钮,同时绿色按钮弹起,对应生产状况看板上的3号工位绿色显示灯熄灭,黄色显示灯亮起,表示异常。异常处理后,按下绿色按钮,对应看板绿灯亮起,恢复正常;否则工位看板维持异常状态。
图1-15 生产线状况看板
作业人员发现作业异常时,及时按下黄色按钮,生产线看板黄灯亮起,现场监督人员看到后,及时停止生产,并处理异常,阻止不良品进入下一工序。
6S注重从小处不断改善现场作业环境,持续消除质量事故,降低成本。装配车间无纺布带料收集改善前后对比如图1-16所示。

图1-16 装配车间无纺布带料收集改善前后对比
综上所述,6S管理是企业改善质量问题、提升质量管理水平的最简便的方法,它有着投入小、收益高的特点。