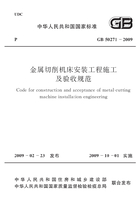
5.1 重型深孔钻镗床
5.1.1 检验预调精度时,应符合下列要求:
1 检验机床安装水平时,应在沿床身导轨的两端,纵、横向放置水平仪进行检测,水平仪读数不应大于0.06/1000;
2 检验床身导轨在垂直平面内的直线度时(图5.1.1-1),应在床身上平行于床身导轨方向放一桥板,桥板上放置水平仪,移动桥板在导轨的全长上进行检测,并应每隔500mm测取一次水平仪读数。直线度偏差值应按本规范附录B的规定计算,并应符合表5.1.1-1的规定;

图5.1.1-1 检验床身导轨在垂直平面内直线度
1—水平仪;2—桥板
Ⅰ—主轴箱固定型;Ⅱ—主轴箱移动型
A—工件床身;B—钻杆床身
表5.1.1-1 床身导轨在垂直平面内直线度的允许偏差(mm)

注:在任意500mm检测长度上的局部允许偏差为0.020mm,只许凸。
3 检验床身导轨在垂直平面内的平行度时(图5.1.1-2),应在床身上垂直于床身导轨方向放一专用检具,检具上放置水平仪,移动检具在导轨的全长上进行检测,并应每隔500mm测取一次水平仪读数。平行度偏差值应以水平仪读数的最大代数差值计,并应符合表5.1.1-2的规定;

图5.1.1-2 检验床身导轨在垂直平面内平行度
1—水平仪;2—专用检具
Ⅰ—主轴箱固定型;Ⅱ—主轴箱移动型
A—工件床身;B—钻杆床身
表5.1.1-2 床身导轨在垂直平面内平行度的允许偏差

4 检验床身导轨在水平面内的直线度时(图5.1.1-3),应在床身的两端沿床身纵向绷紧一根直径不大于0.2mm的钢丝,床身上放一专用检具,显微镜固定在检具上,调整钢丝并使显微镜读数在钢丝两端相等后,移动检具在导轨的全长上进行检测,并应每隔500mm测取一次显微镜读数。直线度偏差值应以显微镜读数的最大代数差值计,并应符合表5.1.1-3的规定;

图5.1.1-3 检验床身导轨在水平面内的直线度
1—钢丝;2—钢丝与显微镜零位间的偏差;3—显微镜;4—专用检具
Ⅰ—主轴箱固定型;Ⅱ—主轴箱移动型
A—工件床身;B—钻杆床身
表5.1.1-3 床身导轨在水平面内直线度的允许偏差(mm)

注:在任意500mm检测长度上的局部允许偏差为0.020mm。
5 检验工件床身对钻杆床身在水平面内的平行度时(图5.1.1-4),应在工件床身和钻杆床身的两端沿床身纵向绷紧一根直径不大于0.2mm的钢丝,床身上放一专用检具,显微镜固定在检具上,调整钢丝使显微镜在钻杆床身导轨上两端点的读数为零,应以钢丝为基准,移动工件床身导轨上的检具并应每隔500mm测取一次显微镜读数。平行度偏差值应以显微镜读数的最大代数差值计,在3000mm检测长度上不应大于0.030mm。

图5.1.1-4 检验工件床身对钻杆床身在水平面内的平行度
1—显微镜;2—专用检具
A—工件床身;B—钻杆床身;
a1、b1—钻杆床身两端的测点;a2、b2—工件床身两端的测点
本条为检验预调精度的规定,其目的是使机床处于静态稳定性,为检验几何精度打下基础。但交工验收时,只检验几何精度。床身导轨在垂直平面内直线度每条导轨均应检验。
5.1.2 检验钻杆箱移动在垂直平面内的直线度和平行度时,应符
合下列要求:
1 检验钻杆箱移动在垂直平面内的直线度时(图5.1.2-1),应将各中心架置于工件主轴箱一端,在钻杆箱滑板上平行于导轨方向放一水平仪,移动箱体在全行程上进行检测,并应每隔500mm测取一次水平仪读数。直线度偏差值应按本规范附录B的规定计算,并应符合表5.1.2-1的规定;

图5.1.2-1 检验钻杆箱移动在垂直平面内的直线度
1—钻杆箱滑板;2—水平仪
Ⅰ—主轴箱固定型;Ⅱ—主轴箱移动型
表5.1.2-1 钻杆箱移动在垂直平面内直线度的允许偏差(mm)

注:在任意500mm检测长度上的局部允许偏差为0.020mm。
2 检验钻杆箱移动在垂直平面内的平行度时(图5.1.2-2),应将各中心架置于工件主轴箱一端,钻杆箱滑板上垂直于导轨方向放一水平仪,移动箱体在全行程上进行检测,并应每隔500mm测取一次水平仪读数。平行度偏差值应以水平仪读数的最大代数差值计,并应符合表5.1.2-2的规定。

图5.1.2-2 检验钻杆箱移动在垂直平面内的平行度
1—滑板;2—水平仪
Ⅰ—主轴箱固定型;Ⅱ—主轴箱移动型
表5.1.2-2 钻杆箱移动在垂直平面内平行度的允许偏差

本条是参照《重型深孔钻镗床 精度》JB/T 8332.1中的G1、G2制定的,是安装组装床身的必检项目。
5.1.3 检验钻杆箱移动在水平面内的直线度时(图5.1.3),应将各中心架置于工件主轴箱一端,机床中心高的位置上沿床身导轨方向绷紧一根直径不大于0.2mm的钢丝,显微镜固定在钻杆箱的滑板上,调整钢丝使显微镜读数在钢丝两端相等后,移动箱体在全行程上进行检测,并应每隔500mm测取一次显微镜读数。直线度偏差值应以显微镜读数的最大代数差值计,并应符合表5.1.3的规定。

图5.1.3 检验钻杆箱移动在水平面内的直线度
1—钢丝;2—钢丝与显微镜零位间的偏差;3—显微镜
表5.1.3 钻杆箱移动在水平面内直线度的允许偏差(mm)

注:在任意500mm检测长度上的局部允许偏差为 0.020mm。
5.1.4 检验工件主轴箱主轴锥孔轴线的径向跳动时(图5.1.4),应在主轴锥孔内插入一根检验棒,并将指示器固定在床头上,使指示器测头触及检验棒表面,旋转主轴并应分别在靠近主轴端部和距主轴端部500mm处进行检测,拔出检验棒并旋转主轴90°后重新插入,依次应重复检测三次。检测两处的径向跳动偏差值应分别以四次检测结果代数和的平均值计,并应符合表5.1.4的规定。

图5.1.4 检验工件主轴箱主轴锥孔轴线的径向跳动
1—指示器;2—检验棒
a—靠近主轴端部测点;b—距主轴端部500mm处测点
表5.1.4 工件主轴箱主轴锥孔轴线的径向跳动的允许偏差(mm)

注:a为靠近主轴端部测点,b为距主轴端部500mm处测点。
考虑到重型深孔钻镗床的工件主轴箱多为分件出厂,在现场组装后,应检验此项。
5.1.5 检验工件主轴箱主轴的轴向窜动时(图5.1.5),应在主轴锥孔内插入一根检验棒,指示器固定在床身上,使指示器测头触及检验棒中心孔内的钢球表面,旋转主轴检测。轴向窜动的允许偏差值应以指示器读数的最大差值计,并应符合表5.1.5的规定。

图5.1.5 检验工件主轴箱主轴的轴向窜动
1—检验棒;2—指示器
表5.1.5 工件主轴箱主轴轴向窜动的允许偏差(mm)

参照《重型深孔钻镗床 精度》JB/T 8332.1进行修订。
5.1.6 检验工件主轴箱主轴轴线对床身导轨的平行度时(图5.1.6),应将工件主轴箱置于床身左端位置并锁紧,主轴锥孔内插入一根检验棒,床身上放置专用检具,指示器固定在检具上,使指示器测头触及检验棒的垂直平面和水平平面的母线上,移动专用检具进行检测,旋转主轴180°后重复检测一次。垂直平面和水平平面的平行度偏差值应分别以两次检测结果代数和的1/2计,在500mm检测长度上平行度允许偏差应符合表5.1.6的规定。

图5.1.6 检验工件主轴箱主轴轴线对床身导轨平行度
1—检验棒;2—指示器;3—专用检具
a—检验棒垂直平面的母线;b—检验棒水平平面的母线
表5.1.6 工件主轴箱主轴轴线对床身导轨的平行度允许偏差(mm)

参照《重型深孔钻镗床 精度》JB/T 8332.1进行修订。
5.1.7 检验钻杆箱主轴锥孔轴线的径向跳动时(图5.1.7),应在主轴锥孔内插入一根检验棒,指示器固定在床头上,使指示器测头触及检验棒表面,旋转主轴应分别在主轴端部和距主轴端部500mm处进行检测;拔出检验棒旋转90°后,重新插入再依次重复检测三次;两检测处径向跳动偏差值应分别以四次检测结果代数和的平均值计,并应符合表5.1.7的规定。

图5.1.7 检验钻杆箱主轴锥孔轴线的径向跳动
1—指示器;2—检验棒
a—主轴端部检测点;b—距主轴端部500mm处检测点
表5.1.7 钻杆箱主轴锥孔轴线径向跳动的允许偏差(mm)

注:a为主轴端部检测点,b为距主轴端部500mm处检测点。
参照《重型深孔钻镗床 精度》JB/T 8332.1进行修订。
5.1.8 检验钻杆箱主轴的轴向窜动时(图5.1.8),应在主轴锥孔内插入一根检验棒,指示器应固定在床身上,并应使指示器测头触及检验棒中心孔内的钢球表面,应旋转主轴检测。轴向窜动偏差值应以指示器读数的最大差值计,并应符合表5.1.8的规定。

图5.1.8 检验钻杆箱主轴的轴向窜动
1—检验棒;2—指示器
表5.1.8 钻杆箱主轴轴向窜动的允许偏差(mm)

参照《重型深孔钻镗床 精度》JB/T 8332.1进行修订。
5.1.9 检验钻杆箱主轴轴线对床身导轨的平行度时(图5.1.9),应将钻杆箱置于床身右端位置,在主轴锥孔内插入一根检验棒,床身上放置专用检具,指示器固定在检具上,并应使指示器测头触及检验棒的垂直平面和水平平面的母线上,移动专用检具进行检测,并应旋转主轴180°后再重复检测一次;垂直平面和水平平面的平行度偏差值应分别以两次检测结果的代数和的1/2计,在500mm检测长度上平行度允许偏差应符合表5.1.9的规定。

图5.1.9 检验钻杆箱主轴轴线对床身导轨的平行度
1—专用检具;2—指示器;3—检验棒
a—检验棒垂直平面的母线;b—检验棒水平平面的母线
表5.1.9 钻杆箱主轴轴线对床身导轨的平行度允许偏差(mm)

参照《重型深孔钻镗床 精度》JB/T 8332.1进行修订。