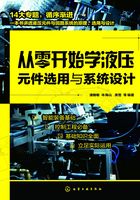
2.3 叶片泵
2.3.1 分类及特点
(1)叶片泵的分类
叶片泵按其输出流量是否可调节分为定量叶片泵和变量叶片泵;按泵轴每转中每个叶片封闭室的吸排油次数分为单作用叶片泵、双作用叶片泵和多作用叶片泵,其中单作用叶片泵一般为变量泵,双作用叶片泵一般是定量泵。按叶片设置的部位又可分为普通叶片泵(叶片在转子上)和凸轮转子叶片泵(叶片在定子上)。某些叶片泵还有单级和多级之分。
(2)叶片泵的特点
叶片泵具有悠久的应用历史,在机床液压系统中应用广泛。现代叶片泵的构造复杂程度和制造成本都介于齿轮泵和柱塞泵之间。其主要优缺点如下。
① 优点
a.可制成变量泵,特别是结构简单的压力补偿型变量泵。
b.单位体积的排量较大。
c.定量叶片泵可制成双作用或多作用的,轴承受力平衡,寿命长。
d.多作用叶片泵的流量脉动较小,噪声较低。
② 缺点
a.吸油能力较差。
b.受叶片与滑道间接触应力和许用摩擦力的限制,变量叶片泵的压力和转速均难以提高,而根据叶片外伸所需离心力的要求,其转速又不能太低,故实用工况范围较窄。
c.对污染物比较敏感。
(3)叶片泵的应用场合
传统上,叶片泵特别是变量叶片泵多用于固定安装的工矿设备和船舶上,但近年来,不少行走机械也装用了高压定量叶片泵。
各种金属加工机床广泛应用叶片泵作为液压油源,它们的液压系统一般功率不大(20kW以下),工作压力中等(常用2.5~8MPa),而要求所使用的液压泵输出流量平稳、噪声低和寿命长,这正符合了叶片泵的特点。利用排量不等的两个单元构成的双联叶片泵可经叠加切换得到三种不同的流量,适用于进给及退回速度相差悬殊的加工设备。
各种中小型锻压、冲剪、铸造、橡胶和塑料成形等设备在一个作业周期中负荷变化大,还常需对加工对象或模具“保压”,使用有压力补偿功能的变量叶片泵可以用节能的运转方式满足这些要求,且成本较低。不过由于新一代设备中液压系统工作压力的提高,以及其他元件在降低噪声及制造成本方面的长足进步,变量叶片泵在这一领域中的应用略有减少。由于种种原因,变量叶片泵属于近20年间技术进步最不明显的液压泵类元件。与现代变量柱塞泵相比,变量叶片泵在压力、转速、功率、效率和可选用的变量方式等方面均有明显差距,品种也少,除了价格较低和自吸能力稍好以外,几乎没有其他优势可言。其应用范围正日益萎缩。照此趋势发展,相当一部分变量叶片泵将不可避免地被综合性能更好、调节方式更多样的变量柱塞泵或变速电动机驱动的定量叶片泵和内齿轮泵所取代。
与变量叶片泵相反,新型高性能的定量叶片泵不仅保持并发展了自己在工业液压领域中的地位,而且以其体积小、重量轻、噪声低和寿命长的优点在行走机械中占据了许多原来属于外齿轮泵的市场。特别是在轿车液压转向助力系统领域中已形成了很大的优势。此外,在工程机械、重型车辆、船用甲板机械、航空航天设备上的应用也日益增多。它们和内齿轮泵一起将成为今后高性能定量液压泵的主流产品。
2.3.2 工作原理
叶片泵(液压马达)的核心部件是一组能在滑槽中沿径向伸缩的矩形叶片,它们把前后端盖和转子、定子间形成的环状空间沿圆周分隔成与叶片数量相同的封闭室。由于转子、定子间的径向距离沿圆周变化,在转子旋转的过程中,这些封闭室的容积会发生周期性的扩大和缩小。在泵的端盖或定子上(偶尔也有在壳体上或在固定的中心销轴上),有分隔开的腰形配流窗口,其中与正在扩大容积区域的封闭室相通的为吸油腔,与正在减小容积区域的封闭室相通的则为排油腔,从而完成吸、排油过程。叶片的作用是在各封闭室间形成密封的“隔墙”,其伸缩运动用以补偿转、定子间距离的变化。
(1)双作用式叶片泵
图2⁃12所示为双作用式叶片泵的工作原理。定子的两端装有配流盘,定子3的内表面曲线由两段大半径圆弧、两段小半径圆弧及四段过渡曲线组成。定子3和转子2的中心重合。在转子2上沿圆周均布开有若干条(一般为12或16条)与径向成一定角度(一般为13°)的叶片槽,槽内装有可自由滑动的叶片。在配流盘上,对应于定子3四段过渡曲线的位置开有四个腰形配流窗口,其中两个与泵吸油口4连通的是吸油窗口;另外两个与泵压油口1连通的是压油窗口。当转子2在传动轴带动下转动时,叶片在离心力和底部液压力(叶片槽底部始终与压油腔相通)的作用下压向定子3的内表面,在叶片、转子、定子与配流盘之间构成若干密封空间。当叶片从小半径曲线段向大半径曲线滑动时,叶片外伸,这时所构成的密封容积由小变大,形成部分真空,油液经吸油窗口吸入;而处于从大半径曲线段向小半径曲线滑动的叶片缩回,所构成的密封容积由大变小,其中的油液受到挤压,经过压油窗口压出。这种叶片泵每转一周,每个密封容腔完成两次吸、压油过程,故这种泵称为双作用叶片泵。同时,泵中两吸油区和两压油区各自对称,使作用在转子上的径向液压力互相平衡,所以这种泵又称为平衡式叶片泵或双作用卸荷式叶片泵。这种泵的排量不可调,因此它是定量泵。

图2⁃12 双作用式叶片泵的工作原理
1—压油口;2—转子;3—定子;4—吸油口
(2)双作用叶片泵的结构特点
双作用叶片泵如不考虑叶片厚度,泵的输出流量是均匀的,但实际叶片是有厚度的,长半径圆弧和短半径圆弧也不可能完全同心,尤其是叶片底部槽与压油腔相通,因此泵的输出流量将出现微小的脉动,但其脉动率较其他形式的泵(螺杆泵除外)小得多,且在叶片数为4的整数倍时最小。因此,双作用叶片泵的叶片数一般为12片或16片。
① 提高双作用叶片泵压力的措施 由于一般双作用叶片泵的叶片底部通压力油,就使得处于吸油区的叶片顶部和底部的液压作用力不平衡,叶片顶部以很大的压紧力抵在定子吸油区的内表面上,使磨损加剧,影响叶片泵的使用寿命,尤其是工作压力较高时,磨损更严重,吸油区叶片两端压力不平衡,限制了双作用叶片泵工作压力的提高。所以在高压叶片泵的结构上必须采取措施,使叶片压向定子的作用力减小。常用的措施如下。
a.减小作用在叶片底部的油液压力。将泵压油腔的油通过阻尼槽或内装式小减压阀通到吸油区的叶片底部,使叶片经过吸油腔时,叶片压向定子内表面的作用力不致过大。
b.减小叶片底部承受压力油作用的面积。叶片底部受压面积为叶片的宽度和叶片厚度的乘积,因此减小叶片的实际受力宽度和厚度,就可减小叶片受压面积。
减小叶片实际受力宽度结构如图2⁃13(a)所示,这种结构中采用了复合式叶片(亦称子母叶片),叶片分成母叶片1与子叶片2两部分。通过配油盘使K腔总是接通压力油,引入母子叶片间的小腔c内,而母叶片底部L腔,则借助于虚线所示的油孔,始终与顶部油液压力相同。这样,无论叶片处在吸油区还是压油区,母叶片顶部和底部的压力油总是相等的。当叶片处在吸油腔时,只有c腔的高压油作用而压向定子内表面,减小了叶片和定子内表面间的作用力。图2⁃13(b)所示的为阶梯片结构,在这里,阶梯叶片和阶梯叶片槽之间的油室d始终和压力油相通,而叶片的底部和所在腔相通。这样,叶片在d室内油液用力作用下压向定子表面,由于作用面积减小,使其作用力不致太大,但这种结构的工艺性较差。

图2⁃13 减小叶片作用面积的高压叶片泵叶片结构
1—母叶片;2—子叶片;3—转子;4—定子;5—叶片
c.使叶片顶端和底部的液压作用力平衡。图2⁃14(a)所示的泵采用双叶片结构,叶片槽中有两个可以作相对滑动的叶片1和2,每个叶片都有一棱边与定子内表面接触,在叶片的顶部形成一个油腔a,叶片底部油腔b始终与压油腔相通,并通过两叶片间的小孔c与油腔a相连通,因而使叶片顶端和底部的液压作用力得到平衡。适当选择叶片顶部棱边的宽度,可以使叶片对定子表面既有一定的压紧力,又不致使该力过大。为了使叶片运动灵活,对零件的制造精度将提出较高的要求。
图2⁃14(b)所示为叶片装弹簧的结构,这种结构叶片1较厚,顶部与底部有孔相通,叶片底部的油液是由叶片顶部经叶片的孔引入的,因此叶片上、下油腔油液的作用力基本平衡,为使叶片紧贴定子内表面,保证密封,在叶片根部装有弹簧。
② 配流盘 配流盘结构如图2⁃15所示,在配流盘上有两个吸油窗口2、4和两个压油窗口1、3,窗口之间为密封区,密封区的中心角α略大于或大于两个叶片间的夹角β,保证密封。当两个叶片间的密封油液从吸油区过渡到密封区时,压力基本上是吸油压力。当转子在转过一个微小的角度时,该密封腔和压油腔相通,油压突然升高,油液的体积收缩,压油腔的油液倒流到该腔,泵的瞬时流量突然减小,引起液压泵的流量脉动、压力脉动、振动和噪声。为了消除这一现象,在配流盘的压油窗口靠叶片从吸油区进入密封区的一边开三角槽。在配流盘接近中心位置处开有槽c,槽c和压油腔相通,并和转子叶片槽底部相通,使叶片底部作用有压力油。
③ 定子曲线 定子曲线由四段圆弧和四段过渡曲线组成。过渡曲线主要为修正的阿基米德螺线、正弦加速曲线、等加速⁃等减速曲线、同次曲线。现在的双作用叶片泵多采用等加速⁃等减速曲线。

图2⁃14 叶片液压力平衡的高压叶片泵叶片结构
1,2—叶片;3—定子;4—转子

图2⁃15 配流盘
1,3—压油窗口;2,4—吸油窗口
④ 叶片的倾角 叶片在工作过程中,受到离心力和叶片底部的液压力作用,使叶片和定子紧密接触。当叶片转到压油区时,定子内壁迫使缩向转子中心。在双作用叶片泵中,将叶片顺着转子回转方向前倾一个角度,可减小定子内壁对叶片作用的侧向力,使叶片在槽中移动灵活,并减少磨损。
(3)单作用叶片泵的工作原理
图2⁃16所示为单作用叶片泵的工作原理。与双作用叶片泵明显不同的是,单作用叶片泵的定子内表面是一个圆形,转子与定子间有一偏心量e,两端的配流盘上只开有一个吸油窗口和一个压油窗口。当转子旋转一周时,每一叶片在转子槽内往复滑动一次,每相邻两叶片间的密封容腔容积发生一次增大和缩小的变化,容积增大时,通过吸油窗口吸油;容积减小时,通过压油窗口将油挤出。由于这种泵在转子每转一周过程中,每个密封容腔容积吸油、压油各一次,故称为单作用叶片泵。又因这种泵的转子受有不平衡的液压作用力,故又称不平衡式叶片泵。由于轴和轴承上的不平衡负荷较大,因而使这种泵工作压力的提高受到了限制。改变定子和转子间的偏心距e值,可以改变泵的排量,因此单作用叶片泵是变量泵。

图2⁃16 单作用叶片泵的工作原理
1—压油口;2—转子;3—定子;4—叶片;5—吸油口

图2⁃17 单作用叶片泵排量计算原理图
(4)单作用叶片泵排量和流量计算
单作用叶片泵的排量和流量可以用图解法近似求出,图2⁃17为其计算原理图。如果相邻两叶片的在吸油腔形成的最大容积为V1,当转子旋转π弧度后,达到最小容积V2,两叶片间排出容积为ΔV的油液,当两叶片再由容积最小位置转到容积最大位置时,两叶片间吸入容积为ΔV的油液。由此可见,转子旋转一周,两叶片间排出油液体积为ΔV。当泵有z个叶片时,就排出z个与ΔV相等的油液体积。若将各部分体积加起来,就可近似为环形体积。因此,单作用叶片泵的理论排量为

(2⁃11)
式中 R——定子的半径;
b——转子的齿宽;
e——定子相对转子的偏距。
单作用叶片泵的流量为

(2⁃12)
式中 n ——叶片泵的转速;
ηv——叶片泵的容积效率。
单作用叶片泵的叶片底部与工作油腔相通。当叶片处于吸油腔时.它与吸油腔相通,也参与吸油;当叶片处于压油腔时,它与压油腔相通,向外压油。叶片底部的吸油和排油正好补偿了工作油腔中叶片占的体积。因此,叶片对容积的影响可以忽略。
(5)单作用叶片泵的结构特点
① 困油现象 由于配流盘吸、排油窗口间的密封角大于相邻两叶片的夹角,而单作用叶片泵的定子不存在与转子同心的圆弧段。因此,在吸、排油过渡区,当两叶片间的密封容腔发生变化时,会产生与齿轮泵相类似的困油现象。为解决困油现象,通常在配流盘排油窗口边缘开三角卸荷槽。
② 叶片根部通油 在转子旋转时,如果只依靠离心力使叶片向外伸出,并不能保证叶片和泵体充分接触,在这种情况下,根本不能形成吸压油腔,造成泵的失效。为了解决这个问题,就在叶片根部通压力油,使叶片和泵体充分接触。
③ 叶片倾角 单作用叶片泵的叶片在吸油区是靠离心力紧贴在定子表面,与定子、转子、配流盘形成容积可变的密封空间的,叶片在运动的过程中,受到科里奥利力和摩擦力的复合作用,为了使叶片所受的合力与叶片的滑动方向一致,保证叶片更容易地从叶片槽滑出,常将叶片槽加工成沿旋转方向向后倾斜一定的角度。
④ 径向力不平衡 单作用叶片泵转子的一侧为高压油的排油腔,一侧为低压油的吸油腔,泵的转子和轴承将承受较大的液压力,这使得泵的工作压力和排量的提高受到一定的限制。
⑤ 流量脉动 单作用叶片泵的流量也是有脉动的,泵内叶片数越多,流量脉动率越小。奇数叶片的泵的脉动率比偶数叶片的泵的脉动率小,所以单作用叶片泵的叶片数均为奇数,一般为13或15片。
2.3.3 典型结构
如图2⁃18所示为YB1型双作用叶片泵的结构,它为分离式结构,由前泵体7、后泵体6和端盖10组成泵的外壳。泵体内安装有左配流盘1、右配流盘5、定子4、转子3、叶片11。为了拆装方便,泵体内的元件通过紧固螺钉13连接成一个整体部件。通过后泵体上的定位孔使13的头部定位,保证吸、压油窗口与定子内表面过渡曲线相对位置准确。吸油口开在后泵体上,压油口开在前泵体上,转子3和传动轴9通过花键连接,并通过两个球轴承8、2支承在前泵体和后泵体上。转子上开有12或16条叶片槽,叶片在槽内可自由滑动。端盖和传动轴间的密封圈14防止油液外泄漏以及空气和灰尘的侵入。

图2⁃18 YB1型双作用叶片泵
1—左配流盘;2—轴承;3,12—转子;4—定子;5—右配流盘;6—后泵体;7—前泵体;8—轴承;9—传动轴;10—端盖;11—叶片;13—紧固螺钉;14—密封圈
2.3.4 叶片泵的选用原则和使用
(1)叶片泵的选择原则
① 根据液压系统使用压力来选择叶片泵 若系统常用工作压力在10MPa以下,可选用YB1系列或YB⁃D型叶片泵;若常用工作压力在10MPa以上,应选用高压叶片泵。
② 根据系统对噪声的要求选择 一般来说,叶片泵的噪声较低,双作用叶片泵的噪声又比单作用泵(即变量叶片泵)的噪声低。若主机要求泵噪声低,则应选低噪声的叶片泵。
③ 从工作可靠性和寿命来考虑 双作用叶片泵的寿命较长,如YB1系列叶片泵的寿命在10000h以上,而单作用叶片泵、柱塞泵和齿轮泵的寿命就较短。
④ 考虑污染因素 叶片泵抗污染能力较差,不如齿轮泵。若系统过滤条件较好,油箱又是密封的,则可以选用叶片泵,否则应选用齿轮泵或其他抗污染能力强的泵。
⑤ 从节能角度考虑 为了节省能量,减少功率消耗,应选用变量泵,最好选用比例压力、流量控制变量叶片泵。采用双联泵甚至三联泵也是节能的一种方案。
⑥ 考虑价格因素 价格是一个重要的因素。在保证系统可靠工作的条件下,为降低成本,应选用价格较低的泵。在选择变量泵或双联泵时,除了从节能方面进行比较外,还应从成本等多方面进行分析比较。
(2)叶片泵的使用注意事项
① 使用叶片泵时要注意泵轴的旋转方向:顺时针方向(从轴端看)为标准品,逆时针方向为特殊式样。回转方向的确认可用瞬间启动液压马达来检查。
② 要注意液压油的黏度和油品:工作压力7MPa以下时,使用40℃时黏度为20~50cSt❶(ISO VG32)的液压油;工作压力7MPa以上时,使用40℃时黏度为30~68cSt(ISO VG46,VG68)的液压油。
③ 泄油管压力:泄油管一定要直接插到油箱的油面下,配管所产生的背压应维持在0.03MPa以下。
④ 注意泵吸油口距液面高度不应大于500mm,吸油管不得漏气。
⑤ 工作油温:连续运转的温度为15~60℃。
⑥ 安装泵时,泵的轴线与电动机或原动机轴线应保持一定的同轴度,一般要求同轴度误差不大于ϕ0.1mm,且泵与电动机之间应采用挠性连接。泵轴不得承受径向力。
⑦ 吸油压力:吸油口的压力为-0.03~0.03MPa。
⑧ 新机运转:新机开始运转时,应在无压力的状态下反复启动电动机,以排除泵内和吸油管中的空气。为确保系统内的空气排除,可在无负载的状态下,连续运转10min左右。
⑨ 注意保持油液清洁。油箱应保持清洁,液压系统应装有过滤器,油液清洁度应达到国家标准等级19/16级。
⑩ YB1系列单级叶片泵是在YB型的基础上改进发展的,是一种新的中低压定量泵,具有结构简单、压力脉动小、工作可靠、使用寿命长等优点,广泛应用于机床设备和其他液压系统中。对于YB1系列单级叶片泵,推荐使用L⁃AN32全损耗系统用油,工作油温为10~50℃。
双联叶片泵是由两个单级叶片泵组合而成,采用同轴传动。泵有一个共同的(或各泵有单独的)进油口,有两个出油口。按两种泵的系列组合,可获得多种流量。双联叶片泵一般用于机床、油压机或其他机械上。
YBN型变量叶片泵依靠移动定子偏心位置来改变泵的排量。泵附有压力补偿装置及最大
流量调节机构,在系统达到调定压力后,自动减少泵的输出流量,以保持系统压力恒定。这种变量叶片泵适用于组合机床及其他机械设备,可以减少油液发热及电动机的功率消耗。