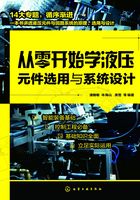
2.2 齿轮泵
齿轮泵是液压系统中广泛采用的一种液压泵,其主要特点是结构简单,制造方便,价格低廉,体积小,重量轻,自吸性能好,对油液污染不敏感,工作可靠。其主要缺点是流量和压力脉动大,噪声大,排量不可调,一般做成定量泵。齿轮泵广泛应用于各种机械设备,如水利电力施工机械平地机、起重机,闸门启闭机液压回路及施工机械的行走机械中。
2.2.1 齿轮泵的分类
按结构不同,齿轮泵分为外啮合齿轮泵和内啮合齿轮泵两种,其中外啮合齿轮泵应用最广。
(1)外啮合齿轮泵及其特点
外啮合齿轮泵的优点是:结构简单、重量轻、尺寸小、加工制造容易、成本低、工作可靠,维护方便,自吸能力强,对油液的污染不敏感,可广泛用于压力要求不高的场合,如磨床、珩磨机等中低压机床中。它的缺点是:内泄漏较大,轴承上承受不平衡力,磨损严重,流量脉动和噪声较大。泵的流量脉动对泵的正常使用有较大影响,它会引起液压系统的压力脉动,从而使管道、阀等元件产生振动和噪声。同时,也影响工作部件的运动平稳性,特别是对精密机床的液压传动系统更为不利。因此,在使用时要特别注意。
(2)内啮合齿轮泵及其特点
内啮合齿轮泵的优点是:结构紧凑、尺寸小、质量轻。由于内外齿轮转向相同,相对滑移速度小,因而磨损小,寿命长,其流量脉动和噪声与外啮合齿轮泵相比要小得多。内啮合齿轮泵的缺点是:齿形复杂,加工复杂、精度要求高,因而制造成本高。
(3)齿轮泵的应用
在现有各类液压泵中,齿轮泵的工作压力仅次于柱塞泵,加之它们体积小、价格低,因而广泛用于移动设备和车辆上作为液压工作系统和转向系统的压力油源。另一方面,由于齿轮泵的转速和排量范围均较大,吸油能力较强,成本又低,也常用作各种液压系统的辅助泵。例如,闭式回路中的补液泵、先导控制系统中的低压控制油源等。但在固定液压设备领域,由于外齿轮泵的流量脉动较大、噪声高且寿命有限,作为主泵已越来越不受欢迎,用途局限于作为运行在低压下的辅助泵及预压泵。与之相反,内齿轮泵却是噪声最低、综合性能最好的液压泵之一。除价格略高这一点以外,在其他方面几乎都优于外齿轮泵。现代制造技术的发展将大大缩小内、外齿轮泵的成本差距,而在工业领域中,调速电传动技术的日益普及,在很大程度上弥补内齿轮泵本身不能变量的缺点。可以预料,今后内齿轮泵在固定和移动设备中的应用面都将会迅速扩大。
在液压工程中,摆线齿轮泵以体积小、价格低和自吸能力较强的优点,被广泛地集成在闭式油路通轴柱塞泵的后盖中,作为低压补液泵(提供控制压力)使用,有时也用作某些机床液压系统的主泵。此种泵可实现单向供油,且与输入转向无关,这一性能对于某些车辆或行走机械上需要用车轮驱动的应急转向、制动系统具有特殊的使用意义。带固定针齿环的摆线齿轮副具有很大的单位体积排量,但因其许用转速较低,多用作低速液压马达,仅在车辆用液压转向系统中作为计量泵使用。当该系统中的动力油源发生故障时,可以用手动方式使此泵成为应急油源。
2.2.2 外啮合齿轮泵
(1)外啮合齿轮泵工作原理
外啮合齿轮泵工作原理如图2⁃4所示,它是分离三片式结构,主要包括上下两个泵端盖、泵体及侧板和一对互相啮合的齿轮。

图2⁃4 外啮合齿轮泵工作原理
1—泵体;2—主动齿轮;3—从动齿轮
泵体内相互啮合的主、从动齿轮2和3,齿轮两端端盖和泵体一起构成密封容积,同时齿轮的啮合又将左、右两腔隔开,形成吸、压油腔。当齿轮按图示方向旋转时,右侧吸油腔内的轮齿脱离啮合,密封工作腔容积不断增大,形成部分真空,油液在大气压力的作用下从油箱经吸油管进入吸油腔,并被旋转的轮齿带入左侧的压油腔。左侧压油腔内的轮齿不断进入啮合,使密封工作腔容积减小,油液受到挤压被排出系统,完成齿轮泵的吸油和排油过程。在齿轮泵的啮合过程中,啮合点沿啮合线把吸油腔和压油腔隔开。
(2)齿轮泵的流量和脉动率
外啮合齿轮泵的排量V可以近似相当于一对啮合齿轮所有齿谷容积之和。假如齿谷容积大致等于轮齿的体积,那么齿轮泵的排量等于一个齿轮的齿谷容积和轮齿容积体积的总和,即相当于以有效齿高h和齿宽构成的平面所扫过的环形体积,排量V可近似为

(2⁃7)
式中 z——齿轮的齿数;
m——齿轮的模数;
b——齿轮的齿宽;
d——齿轮的节圆直径,d=mz;
h——齿轮的有效齿高,h=2m。
实际上齿谷的容积要比轮齿的体积稍大,并且齿数越少误差就越大。因此,上式中的π常以3.33代替,则式(2⁃7)可写为

(2⁃8)
齿轮泵的实际流量为

(2⁃9)
齿轮泵在工作过程中,排量是转角的周期函数,存在排量脉动,瞬时流量也是脉动的。实际上齿轮泵的输出流量是有脉动的,故式(3⁃9)所表示的是泵的平均流量。流量脉动会直接影响到系统工作的平稳性,引起压力脉动,使管路系统产生振动和噪声。如果脉动频率与系统的固有频率一致,还将引起共振,加剧振动和噪声。一般用流量脉动率σ度量流量脉动的大小,即

(2⁃10)
式中 σ ——液压泵的流量脉动率;
qmax——液压泵最大瞬时流量;
qmin——液压泵最小瞬时流量;
q0——液压泵实际平均流量。
综上所述,可得出如下结论:
① 齿轮泵的输出流量与齿轮模数m的二次方成正比;
② 在泵的体积一定时,齿轮齿数少,模数就大,故排量增加,但流量脉动大;反之,流量脉动小;
③ 齿轮泵的输出流量和齿宽b、转速n成正比。
(3)困油现象
为保证齿轮传动平稳,供油连续,齿轮的重叠系数ε必须大于1,即一对轮齿即将脱开前,下一对轮齿已开始啮合,因此在某一短时间内同时有两对轮齿啮合,如图2⁃5(a)所示,留在齿间中的油液被困在两对轮齿间的封闭容腔内,既不与压油口连通,也不与吸油口连通。随着齿轮的旋转[由图2⁃5(a)转到图2⁃5(b)所示位置],该封闭容积由大变小。由于油液的可压缩性很小,因而压力急剧增高,油液只能从各缝隙里硬挤出去,使齿轮轴和轴承等受到很大的冲击载荷。当齿轮继续旋转[由图2⁃5(b)转到图2⁃5(c)所示位置],该封闭容积将由小变大,造成局部真空,使油液中的空气分离出来,油液本身也会汽化,产生气泡,这就是困油现象。困油现象会使流量不均匀,形成压力脉动,产生很大的噪声,使泵的寿命降低。为了消除困油现象,可在齿轮两侧的端盖上铣两个凹下去的卸荷槽,如图2⁃5(d)所示。当封闭容腔缩小时,通过右边的卸荷槽与压油口连通,当封闭容腔增大时,通过左边的卸荷槽与吸油口连通,吸荷槽之间的距离a应保证在任何时候吸、压油口都不会窜通。

图2⁃5 齿轮泵的困油现象
(4)径向液压作用力的不平衡
由图2⁃6可知,齿轮啮合点的左侧是压油腔,其中压力为工作压力;右侧是吸油腔,其中压力一般部低于大气压力;同时部分压力油沿齿顶圆周缝隙由压油腔漏至吸油口,压力沿周向逐渐由高降低,致使沿齿轮径向的液压作用力不平衡,如图2⁃6所示。再加上齿轮啮合力的联合作用,因此在齿轮轴的轴承上受到一个很大的径向力。泵的工作压力愈高,该径向力愈大,使泵的工作所示。再加上齿轮啮合力的联合作用,因此在齿轮轴的轴承上受到一个很大的径向力。泵的工作压力愈高,该径向力愈大,使泵的工作条件变坏,不仅加速轴承的磨损,减低泵的寿命,而且会使轴变形,造成齿顶与壳体内表面之间的摩擦,使泵的总效率降低。为了解决齿轮泵径向受力不平衡的问题,有的泵在侧盖或座圈上开有平衡槽,如图2⁃7(a)所示。这种方法会增多泄漏的途径,使容积效率降低,压力上不去,此外加工较复杂。另一种方法是缩小压油口[见图2⁃7(b)],通过减小压力油作用在齿轮上的面积来减小径向力,虽然采用这种方法后径向力未得到完全平衡,轴仍受径向力的作用而产生弯曲变形,但可稍加大齿顶的径向间隙以减小摩擦,由于圆周密封带较长,漏油的增加并不显著。

图2⁃6 径向液压作用力的不平衡

图2⁃7 径向力平衡的方法
(5)齿轮泵的泄漏问题和高压化措施
对任何容积式液压泵来讲,为了提高其工作压力,必须使液压泵具有较好的密封性能,但为了实现密封容积的变化,相对运动的零件间又不得不具有一定的间隙,这就构成了一对矛盾。因此,提高容积式液压泵工作压力的途径就是要合理地解决这一矛盾。对齿轮泵来讲,漏油的途径有齿顶圆和壳体内孔之间的径向间隙;齿轮端面和侧盖之间的轴向间隙以及由于在齿宽方向上不能保证完全啮合而造成的齿面缝隙。而其中尤以齿轮端面的轴向间隙对泄漏的影响为最大,油压愈高,泄漏愈多。如果制造时减小此间隙,这不仅会给制造带来困难,而且将引起齿轮端面的很快磨损,容积效率仍不能提高。所以高压外啮合齿轮泵一般都采取利用液压力来补偿轴向间隙的方法。目前国内生产的外啮合齿轮泵,主要是采用浮动轴套或采用浮动侧板来自动补偿轴向间隙,对任何容积式液压泵来讲,为了提高其工作压力,必须使液压泵具有较好的密封性能,但为了实现密封容积的变化,相对运动的零件间又不得不具有一定的间隙,这就构成了一对矛盾。因此,提高容积式液压泵工作压力的途径就是要合理地解决这一矛盾。对齿轮泵来讲,漏油的途径有齿顶圆和壳体内孔之间的径向间隙;齿轮端面和侧盖之间的轴向间隙以及由于在齿宽方向上不能保证完全啮合而造成的齿面缝隙。而其中尤以齿轮端面的轴向间隙对泄漏的影响为最大,油压愈高,泄漏愈多。如果制造时减小此间隙,这不仅会给制造带来困难,而且将引起齿轮端面的很快磨损,容积效率仍不能提高。所以高压外啮合齿轮泵一般都采取利用液压力来补偿轴向间隙的方法。目前国内生产的外啮合齿轮泵,主要是采用浮动轴套或采用浮动侧板来自动补偿轴向间隙,这两种方法部是引入压力油使轴套或侧板贴紧齿轮端面,压力越高贴得越紧,便可自动补偿轴向磨损和间隙,这种泵结构紧凑,容积效率高,但是流量脉动较大。
(6)齿轮泵的泄漏途径及端面间隙的自动补偿
在液压泵中,运动件之间是靠微小间隙密封的,这些微小间隙形成了运动学中所谓的摩擦副,而高压腔的油液通过间隙向低压腔泄漏是不可避免的。齿轮泵压油腔的压力油可通过以下三条途径泄漏到吸油腔:①齿侧间隙,通过齿轮啮合线处的间隙;②齿顶间隙,通过泵体内孔和齿顶间隙的径向间隙;③端面间隙,通过齿轮两端面和侧板间的间隙。
在这三类间隙中,端面间隙的泄漏量最大,占泄漏总量的70%~80%。外啮合齿轮泵压力越高,吸压油腔两端的压差越大,由间隙泄漏的液压油液就越多。因此,为了实现齿轮泵的高压化,提高齿轮泵的压力和容积效率,减少泄漏,需要从结构上来考虑,对端面间隙进行自动补偿。通常采用如下自动补偿端面间隙的措施。
① 浮动轴套 图2⁃8(a)所示为浮动轴套式间隙补偿装置。它将泵的出口压力油引入齿轮轴上的浮动轴套1的外侧A腔,在液体压力作用下,使轴套紧贴齿轮2的侧面,因而可以消除间隙并可补偿齿轮侧面和轴套间的磨损量。在泵启动时,靠弹簧4来产生预紧力,保证了轴向间隙的密封。
② 浮动侧板 如图2⁃8(b)所示,浮动侧板式补偿装置的工作原理与浮动轴套式的基本相似,它也是将泵的出口压力油引到浮动侧板1的背面,使之紧贴于齿轮2的端面来补偿间隙。启动时,浮动侧板靠密封来产生预紧力。
③ 挠性侧板 图2⁃8(c)所示为挠性侧板式间隙补偿装置,它是将泵的出口压力油引到侧板的背面后,靠侧板自身的变形来补偿端面间隙的,侧板较薄,内侧面须耐磨,如烧结0.5~0.7mm的磷青铜,对这种结构采取一定措施后,易使侧板外侧面的压力分布大体上和齿轮侧面的压力分布相适应。

图2⁃8 端面间隙补偿装置示意图
1—浮动轴套(侧板);2—齿轮;3—泵体;4—弹簧
④ 二次密封机构 二次密封机构是指在主动齿轮轴颈两端各放置一个密封环,由于密封环与轴颈间的间隙节流作用,相当于继浮动侧板之后的第二道密封,从而使轴向泄漏进一步减少。
(7)外啮合齿轮泵典型结构
CB⁃B齿轮泵的结构如图2⁃9所示,当泵的主动齿轮按图示箭头方向旋转时,齿轮泵右侧(吸油腔)齿轮脱开啮合,齿轮的轮齿退出齿间,使密封容积增大,形成局部真空,油箱中的油液在外界大气压的作用下,经吸油管路、吸油腔进入齿间。随着齿轮的旋转,吸入齿间的油液被带到另一侧,进入压油腔。这时轮齿进入啮合,使密封容积逐渐减小,齿轮间的油液被挤出,形成了齿轮泵的压油过程。齿轮啮合时齿向接触线把吸油腔和压油腔分开,起配油作用。当齿轮泵的主动齿轮由电动机带动不断旋转时,轮齿脱开啮合的一侧,由于密封容积变大则不断从油箱中吸油,轮齿进入啮合的一侧,由于密封容积减小则不断地排油,这就是齿轮泵的工作原理。泵的前后盖和泵体由两个定位销17定位,用6只螺钉把紧,如图2⁃9所示。为了保证齿轮能灵活地转动,同时又要保证泄漏最小,在齿轮端面和泵盖之间应有适当间隙(轴向间隙),小流量泵轴向间隙为0.025~0.04mm,大流量泵为0.04~0.06mm。对于齿顶和泵体内表面间的间隙(径向间隙),由于密封带长,同时齿顶线速度形成的剪切流动又和油液泄漏方向相反,故对泄漏的影响较小。这里要考虑的问题是:当齿轮受到不平衡的径向力后,应避免齿顶和泵体内壁相碰,所以径向间隙就可稍大,一般取0.13~0.16mm。

图2⁃9 CB⁃B齿轮泵的结构
1—轴承外环;2—堵头;3—滚子;4—后泵盖;5—键;6—齿轮;7—泵体;8—前泵盖;9—螺钉;10—压环;11—密封环;12—主动轴;13—泄油孔;14—从动轴;15—泄油槽;16—定位销
为了防止压力油从泵体和泵盖间泄漏到泵外,并减小压紧螺钉的拉力,在泵体两侧的端面上开有油封泄油槽16,使渗入泵体和泵盖间的压力油引入吸油腔。在泵盖和从动轴上开有小孔,其作用是将泄漏到轴承端部的压力油也引到泵的吸油腔,以防止油液外溢,同时也润滑了滚针轴承。
2.2.3 内啮合齿轮泵
(1)工作原理
内啮合齿轮泵也是利用齿间密封容积的变化来实现吸油、压油的。图2⁃10为内啮合齿轮泵的工作原理。

图2⁃10 内啮合齿轮泵的工作原理
内啮合齿轮泵是由配流盘(前、后盖)、外转子(从动轮)和偏心安置在泵体内的内转子(主动轮)等组成。内、外转子相差一齿,图中内转子为6齿,外转子为7齿,由于内外转子是多齿啮合,因此形成了若干密封容积。
当内转子围绕中心O1旋转时,带动外转子绕外转子中心O2做同向旋转。这时,由内转子齿顶A1和外转子齿谷A2间形成的密封容积c(图中虚线部分),随着转子的转动密封容积就逐渐扩大,于是就形成局部真空,油液从配油窗口b被吸入密封腔,至、
位置时封闭容积最大,这时吸油完毕。
当转子继续旋转时,充满油液的密封容积便逐渐减小,油液受挤压,于是通过另一配油窗口a将油排出,转至内转子的另一齿和外转子的齿在A2位置全部啮合时,压油完毕。
内转子每转一周,由内转子齿顶和外转子齿谷所构成的每个密封容积,完成吸油、压油各一次,当内转子连续转动时,即完成了液压泵的吸油、排油工作。
内啮合齿轮泵的最大优点是:无困油现象,流量脉动较外啮合齿轮泵小,噪声低。当采用轴向和径向间隙补偿措施后,泵的额定压力可达30MPa,容积效率和总效率比较高。缺点是齿形复杂,加工精度要求高,价格较贵。
(2)渐开线内啮合齿轮泵的典型结构
图2⁃11所示为带有溢流阀的内啮合齿轮泵,当泵的出口压力达到或超过出弹簧10所调定的压力时,高压腔的压力油克服弹簧力,顶开锥阀芯,溢流到吸油腔。

图2⁃11 带有溢流阀的内啮合齿轮泵
1—泵轴;2—泵体;3—内齿环;4—小齿轮;5—调节螺钉;6—锁紧螺母;7—螺塞;8—弹簧座;9,13—O形密封圈;10—弹簧;11—泵盖(阀体);12—锥阀;14—锥阀座;15—组合密封圈
2.2.4 齿轮泵的选用原则和使用
(1)齿轮泵的选用原则
① 齿轮泵工作压力 液压系统正常工作压力应小于或等于齿轮泵的额定压力,瞬时压力峰值不得超过最大压力。齿轮泵的工作压力是决定齿轮泵寿命至关重要的因素之一。由于齿轮泵的寿命取决于轴承的寿命,负载大轴承寿命就短,尤其是采用滑动轴承结构的齿轮泵,如果超出规定的压力很多,瞬间就会使泵的轴承与齿轮轴颈咬死。合理选择齿轮泵的工作压力至关重要,可按照齿轮泵的不同压力等级(低压为小于等于2.5MPa、中压为8~14MPa、中高压为16~20MPa、高压为21~31.5MPa)选用合适的泵。
② 齿轮泵的转速 根据原动机的转速来选用齿轮泵的转速,其正常工作转速必须低于或等于齿轮泵的额定转速,短瞬的转速峰值不得超过样本规定的最高转速。对于滑动轴承来说,会因为过高的转速而发热烧死。泵的转速应与原动机的转速范围相匹配。
③ 齿轮泵的排量 根据系统需要的流量和原动机的转速来选择齿轮泵的排量。由于齿轮泵是定量泵,流量过大不仅造成不必要的功率损失,还会使系统发热而出故障。因此在确定流量时,除考虑系统的工作流量外,还应充分考虑其他液压元件的泄漏损失,以及齿轮泵磨损后容积效率少量下降时不致影响系统的正常工作,这种矛盾在选择小排量齿轮泵时尤为突出。
④ 齿轮泵的抗污染能力 不同结构的齿轮泵抗污染能力不同。若是固定侧向间隙和滚动轴承的齿轮泵,可选用过滤精度较低的过滤器;而带轴向或径向间隙补偿及滑动轴承结构的齿轮泵,对污染的敏感性高,应选用过滤精度较高的过滤器,按样本的要求执行。通常低压齿轮泵的污染敏感度较低,允许系统选取过滤精度较低的过滤器。相反,高压齿轮泵的污染敏感度较高,故系统需选用过滤精度较高的过滤器。
⑤ 其他因素 为了节省功率和合理使用,可采用多联齿轮泵来解决多个液压源的问题,或采用串级齿轮泵来达到所需要的压力。需要提高压力等级时,可选用多级齿轮泵。要考虑对齿轮泵的噪声和流量脉动的要求,外啮合齿轮泵的噪声较大,内啮合齿轮泵的流量脉动较小。带安全阀的复合型齿轮泵可用于小型行走或移动的设备上,系统可不设安全阀,结构更紧凑简单。转向系统可选用组装单路稳定分流阀的复合型齿轮泵,该阀把齿轮泵的排油分成两部分,其中一部分稳定不变的流量供给转向系统,另一部分供其他系统使用。在要求齿轮泵能够正反两个方向旋转,进出油口又保持不变的场合,可选用与正反向阀组合的复合型齿轮泵,或选用带偏心套的摆线齿轮泵。
综合考虑齿轮泵的可靠性、经济性、使用维护方便与否、供货及时与否等条件,要优先采用经国家有关部门及行业中经过鉴定的产品。
(2)齿轮泵的使用
使用齿轮泵时,应注意以下几点。
① 泵传动轴与原动机输出轴之间的安排采用弹性联轴器,其同轴度误差不得大于ϕ0.01mm,采用轴套式联轴器的同轴度误差不得大于ϕ0.05mm。
② 输出轴不能承受径向力的泵,传动装置应保证泵的主动轴不承受径向力和轴向力,可以允许承受的力应严格遵守许用范围。
③ 泵的吸油高度不得大于0.5mm。
④ 泵的过滤精度应≤40μm,在吸油口常用网式过滤器,滤网可采用150目。设置在系统回油路上的过滤器的精度最好≤40μm。
⑤ 工作油液应严格按规定选用,一般常用运动黏度为25~33mm2/s,工作温度范围为-20~80℃。
⑥ 泵的旋转方向即进、出油口位置不得搞错。
⑦ 在必要的情况下,进行泵的拆卸和装配时,必须严格按厂方的使用说明书进行。
⑧ 要拧紧泵进、出口管接头连接螺钉,密封装置要可靠,以免引起吸空、漏油,影响泵的工作性能。
⑨ 应避免带负载启动及在有负载情况下停车。
⑩ 启动前必须检查系统中的溢流阀(安全阀)是否在调定的许可压力上。
泵在工作前应进行不少于10min的空负载运转和短时间的负载运转。然后检查泵的工作情况,不应有渗漏、冲击声、过度发热和噪声现象。
泵如长时间不用,应将它和原动机分离。再次使用时,不得立即使用最大负载,应有不小于10min的空负载运转。
为了节省功率和合理使用,可采用多联泵来解决多个液压源的问题,或采用串级泵来达到所需要的压力。
CB⁃B系列齿轮泵使用时应注意,此系列齿轮泵属于低压齿轮泵,适用于机床、工程机械等低压液压系统和润滑系统作液压能源,使用32号机械油,工作油温为10~50℃。