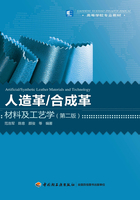
1.2 人工革
随着人类社会的发展,天然革的供应量与日益增长的需求量之间的不平衡现象越来越突出,已不能满足人们对皮革服饰面料广泛使用的需要。与此同时,天然皮革产业还面临着原料皮紧缺、生产效率低、利用率低、环保以及消费者动物保护意识增强等多重因素导致的下行压力,未来发展空间受限。自20世纪30年代起,人们开始使用各种不同的化学原料和方法来制造天然皮革的代替品,即人工革。时至今日,人工革的发展日新月异,已完成了从早期简单仿形到后期高度仿真的历史转型,日益得到市场的肯定,其应用范围之广、产量之大、品种之多,传统的天然皮革难以望其项背。
人工革是将合成树脂以某种方式(如涂覆、贴合等)与基材结合在一起得到的天然皮革的代用品,有人造革、合成革及超细纤维合成革之分。在历史上,人工革的命名方案较为混乱,没有形成较为统一的称谓体系。按《中国大百科全书》轻工卷的定义,人造革与合成革的区别在于人造革主要以织物为基材,而合成革则以无纺布为基材,同时具有微孔结构的面层,但这种区分仅适用于天然革代用品发展的早期。目前,人们习惯按造面树脂的种类对人工革加以区分:将以聚氯乙烯(PVC)树脂作为涂层生产的人工革称为PVC人造革(简称人造革),将以聚氨酯(PU)树脂为涂层的人工革称作PU合成革(简称合成革),将以PVC树脂为底层、PU树脂为面层的人工革称作半PU,而超细纤维合成革则是在后期独立于前三种革种发展起来的一种天然皮革高仿品,具有较为复杂的生产方法和独特的物化结构。
1.2.1 第一代人工革——聚氯乙烯人造革(PVC人造革)
PVC人造革是将聚氯乙烯树脂(PVC)、增塑剂、稳定剂等组成的混合物,涂覆或贴合在基材上而得到的一种仿皮革塑料制品,史称第一代人工革。PVC人造革的外观近似天然皮革,具有色泽鲜艳、质地较轻和强度高、耐磨、耐折、耐酸碱性等优良特性,并且成本低廉、加工方便。PVC人造革可用于制造箱包、家具、手套、汽车/游艇/房车内饰、地板、壁纸、篷布等,广泛应用于工业、农业、交通运输业、国防工业及日常生活等方面。它的缺点是与基布黏结牢度差,易剥离;耐寒性差,易脆裂,手感僵硬,柔软性差;所添加的增塑剂会散发出令人不悦的气味以及透气性、吸湿性差等。PVC人造革按是否发泡可分为PVC普通人造革(不发泡)和PVC泡沫人造革。
PVC人造革的制造方法有直接涂刮法(现已基本淘汰)、离型纸法(转移涂层法)和压延法等,其工艺流程如图1-1、图1-2和图1-3所示。

图1-1 直接涂刮法PVC泡沫人造革工艺流程图
以上获得的复合物习惯上称为PVC贝斯(Base)。贝斯表面经整饰后,即得PVC人造革成品。
1.2.2 第二代人工革——聚氨酯合成革(PU革)
第二代人工革——聚氨酯合成革是将聚氨酯树脂形成的涂层与基布结合获得的一种外观、性能与天然皮革更为接近的塑料制品。PU合成革具有许多聚氯乙烯人造革所不能比拟的优点(表1-1),包括手感柔软、光泽自然、颜色柔和、耐寒、耐老化、屈挠性能好、透气透湿性能优异、剥离强度高、真皮感强等,目前主要应用于各种鞋类、衣料、家具、箱包等领域。

图1-2 转移涂层法(离型纸法)PVC泡沫人造革工艺流程图

图1-3 压延法PVC泡沫人造革工艺流程图
表1-1 聚氯乙烯人造革与聚氨酯合成革的主要性能对比

续表

PU合成革的制造方法有干法和湿法两种,其生产工艺相应可分为干法生产工艺和湿法生产工艺。
(1)干法
干法PU合成革是把溶剂型聚氨酯树脂(PU)溶液烘干后得到的多层薄膜与基布结合而构成的一种多层复合体。它于20世纪60年代初在意大利、西班牙、日本等国开始投产,从70年代开始以每年约20%的速度增长,目前已成为人工革市场上的主流产品。
早期的干法合成革主要采用直接涂刮法进行生产,其工艺流程如图1-4所示。然而,由于直接涂刮法对基布的强度/紧密性以及刮刀系统的精密度等提出了较高要求,同时由于聚氨酯浆料与基布直接接触,涂层的剥离强度与成革手感间矛盾无法调和,因此这种方法现已鲜有制革厂采用。

图1-4 直接涂刮法干法PU革工艺流程图
目前合成革工业主要采用转移涂层法生产干法聚氨酯合成革。这种方法以离型纸为载体,将溶剂型聚氨酯树脂浆料涂刮在离型纸上(一般涂刮一至两次),放入烘箱加热除去树脂中的溶剂,以形成连续均匀的聚氨酯薄膜;然后将上述复合物与基布贴合,经烘干固化后,利用剥离装置将离型纸剥离,并将成革与离型纸分别成卷,其典型生产流程如图1-5所示。当然,以上获得的复合物只能被称为干法贝斯,贝斯还需改色、增光/消光等后整理处理才能获得成革。
采用这种方式生成的聚氨酯合成革膜层致密、产品强度优异、黏结牢固,过程所生产的废水较少,但由于涂层完全致密,这种产品的卫生性能依然较差,且生产过程产生的有机溶剂废气污染严重。
鉴于干法聚氨酯合成革的上述缺陷,自21世纪初,研究人员开始尝试以水性聚氨酯代替溶剂型聚氨酯用于合成革造面,同时已开发出与水性聚氨酯干法造面相配套的离型纸、干燥装置及发泡技术等。

图1-5 离型纸干法PU革工艺流程图
(2)湿法
湿法PU是将含有各种助剂的聚氨酯二甲基甲酰胺(DMF)溶液浸渍或涂覆于基布上,然后放入与溶剂(DMF)具有亲和性,而与聚氨酯树脂不亲和的液体(如水)中,DMF被水置换,聚氨酯树脂逐渐凝固,从而形成连续的多孔型皮膜,即微孔聚氨酯粒面层,习惯上称为湿法贝斯。贝斯表面经整饰后,成为聚氨酯合成革成品。
湿法PU合成革最早于1963年在国外市场上出现。与干法致密涂层相比,湿法PU涂层具有大量微孔,因此具有良好的透湿、透气性能,手感柔软、丰满、轻盈,更富于天然皮革的风格和外观,曾经一度被认为是天然皮革的最佳替代产品。20世纪70年代末期和80年代初期,国外市场出现了以普通织物为基布的湿法PU合成革,解决了无纺布湿法合成革工艺复杂、成本高、价格贵、品种单一等问题。这种生产方法工艺成熟、产品品种多、用途广泛、价格便宜,是目前合成革市场上极具生命力的产品。然而,湿法工艺一般须投资精馏塔以解决湿法废水的回用问题,精馏塔建设费用及其日常运行费用不可小觑;与此同时,湿法合成革配方中大量使用木质纤维素作为填料,因此合成革存在易霉变、寿命短等缺陷。
湿法聚氨酯合成革的生产工艺可分为单涂覆法、浸渍法和含浸涂覆法3种(图1-6至图1-8),所用基布有纺织布和无纺布两类。

图1-6 单涂覆法聚氨酯贝斯生产工艺流程

图1-7 浸渍聚氨酯贝斯生产工艺流程

图1-8 含浸涂覆聚氨酯贝斯生产工艺流程
1.2.3 第三代人工革——超细纤维合成革
超细纤维合成革简称超纤革,是超细纤维通过梳理、针刺或水刺制成具有三维网络结构的无纺布,再经聚氨酯湿法含浸、减量、磨皮、染整等工艺最终形成的仿革产品。超细纤维采用与天然皮革中束状胶原纤维结构和性能相似的超细纤维制革高密度无纺布,结合具有开式微孔结构的高性能聚氨酯为填充材料,在结构和外观质感上真正模拟天然皮革的特殊形态(图1-9)。超细纤维合成革是一种跨行业的产品,其研发及应用技术涉及纺织、塑料、化工等诸多领域。
20世纪70年代,日本可乐丽公司、东丽公司等先后成功开发出超细纤维合成革。此后,随着生产技术、应用技术的进步和完善,生产成本的逐渐下降以及人们消费观念的转变和环保意识的增强,超细纤维合成革的生产和消费快速增长,现已被广泛应用在高档鞋、服装、家具、球类和汽车内饰等领域中。据统计,目前有90%以上的高档运动鞋(包括NIKE等国际著名品牌)是用超细纤维合成革制成;高档汽车座椅中也已大量采用超细纤维合成革代替天然皮革。

图1-9 超细纤维合成革的剖面电镜图
超细纤维的细度已经超过纺织上最细的天然纤维——蚕丝,而目前国际上对超细纤维的界定尚无统一的规格和标准。日本将0.55~1.1 dtex的纤维称为细旦丝,0.55 dtex以下的纤维称为超细丝;而欧洲的划分是:1.0~2.4dtex的纤维称为细旦丝,0.3~1.0dtex的纤维称为微细丝,0.3dtex以下的纤维称为超细丝。我国目前还没有统一的国标,但更倾向日本的划分界限,将纤维单丝线密度小于0.55 dtex的纤维称为超细纤维。
超细纤维在结构上的最大特点就是纤维的纤度极小,比表面积急剧增大,这种结构上的变化使纤维的诸多性能均发生了变化。如纤维直径的细化降低了纤维的刚度,大大提高了人工革的柔顺性和触感;纤维的细化还可以增加丝的层状结构,增大毛细效应,强化人工革的吸湿性和穿着舒适性;与此同时,纤维细化还可使纤维内部反射光泽,使成革具有细腻、柔和的视觉效果。由此可见,超细纤维合成革不论是内部微观结构、外观质感、穿着舒适性等均已达到天然皮革的标准,在耐化学性、质量均一性、大生产加工适应性以及防水、防霉变性等方面更超过了天然皮革,完全可以作为高档天然皮革的替代产品。因此,超细纤维合成革对于人工革行业具有革命性意义,它把人工革行业推向了更高的发展层次。
目前,超细纤维合成革的主流生产方法为海岛法。海岛纤维采用共混纺丝或复合纺丝的方式将一种聚合物分散于另一种聚合物中,在纤维截面中分散相呈 “岛”状态,而母体则相当于 “海”,从纤维的横截面看是一种成分以微细而分散的状态被另一种成分包围着,好像海中有许多岛屿(图1-10)。一旦用溶剂(甲苯或碱)将海组分溶解掉,则可得到集束状的超细纤维束。海岛纤维的岛组分通常是聚酯(PET)、聚酰胺(PA6)以及聚丙烯腈(PAN)等;海组分可以是聚乙烯(PE)、聚丙烯(PP)、聚苯乙烯(PS)或改性聚酯(COPET)等。

图1-10 海岛纤维减量前截面形貌图
目前,国内外生产海岛纤维主要是通过不定岛法和定岛法。
(1)不定岛法
采用双组分混溶纺丝技术,在纤维的横截面上能观察到岛组分(通常为PA6)以细微而零散的形态包含于海组分(通常为PE或PP)中,岛的数目、粗细、长短均不可控,其在纤维伸展方向上是非连续密集分布的,但总体比定岛纤维更纤细。通过后续加工加溶剂(一般为甲苯)操作使海组分溶解后(图1-11),才可以获得真正意义上的超细纤维束。

图1-11 不定岛超纤甲苯减量示意图
不定岛超细纤维中岛数量、分布及其纤度都存在随机性,经溶剂抽取开纤后,超细纤维的线密度在0.0011~0.11dtex,该技术由日本可乐丽公司最早发明。在国内,烟台万华公司首先拥有该技术并实现了产业化。到目前为止,国内大部分超纤革企业均是采用不定岛纺丝技术。但是,不定岛超纤的缺陷非常明显,这主要是由于不定岛超细纤维海岛结构及其岛形貌的不稳定性,增加了合成革后道工序中的不可预测因素。与此同时,由于岛形貌的不匀性,造成不定岛超细纤维纤度不匀,在染整过程中,这很容易影响成革的染色效果。另外,采用甲苯减量会产生成分复杂的有机溶剂废水,存在较为严重的环境污染问题和溶剂回收压力。当前这种方法还无法运用于生产长纤,只能用来生产短纤。
(2)定岛法
定岛超细纤维生产技术是在非定岛超细纤维生产技术及复合纺丝组件制造技术发展的基础上形成的,是超细纤维未来发展趋势。这种方法采用双组分复合纺丝技术,在纺丝分配板前各组分以独立形式存在,各自有各自的通道。观察纤维的横截面会发现,其中一种组分(通常为PET或PA6)以细微而分散的方式(犹如海水中的岛屿一般)包含于另一种组分(通常为COPET)中,两种组分在纤维伸展方向上是连续密集均匀分布的,岛的数目是确定、均匀而且富有规律的。纺丝后通常该复合纤维以常规纤度存在,通过后续加工的加溶剂(一般为碱)操作使海组分溶解(图1-12),才能得到真正意义上的束状超细纤维束。
这种方法目前主要用于生产高质量长纤。虽然纤维的纤度稍逊于非定岛纤维,但是由于克服了不定岛超细在纤维形貌不可控方面的缺陷,由定岛超细纤维制作的合成革产品在手感、仿天然皮革风格、机械性能和染色性能等各方面有了更大的改善,对开发高端的合成革产品具有相当的吸引力。在合成革领域,定岛超纤技术的研发与应用主要集中在日本、韩国及中国的台湾地区,尤其是日本可乐丽公司、旭化成公司、东丽公司、三菱造丝等掌握着定岛纺丝的核心技术。在中国大陆,经过多年研发探索,也有少数几家公司拥有了定岛长纤的生产设备及相关技术。

图1-12 定岛超纤碱减量示意图
无论是定岛还是不定岛超纤,碱减量开纤后均需进行染色、磨皮及三防、抗菌、阻燃、防紫外线等多种后整理加工,才能获得外观、性能逼真的防革产品。