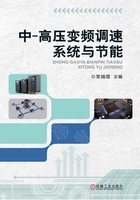
2.7 PLC与变频器的连接
在变频调速系统中,最为常见的是PLC与变频器的组合应用,即采用PLC控制变频器,进而变频器再控制电动机的运行,以适应生产自动化的要求。PLC和变频器的连接方式有很多,这里仅介绍变频器和PLC配合使用时的接线方式、电平转换及接线注意事项。
2.7.1 利用PLC的继电器输出模块与变频器连接
PLC的开关量输出一般可与变频器的开关量输入端直接相连。这种控制方式的接线简单、抗干扰能力强。利用PLC的开关量输出可以控制变频器的起动与停止、正转与反转、点动、转速和加减速时间等,能实现较为复杂的控制要求,但只能实现有级调速。
PLC通常利用继电器输出模块触点与变频器进行连接,如图2-25所示。使用这种连接方式时,为防止出现因接触不良而带来的误动作,要考虑触点容量及继电器的可靠性。目前,许多厂家生产的PLC和变频器,在继电器触点容量满足要求时,不会造成变频器的误动作。当变频器输入信号通过继电器等感性负载时,由于继电器开闭产生的浪涌电流带来的噪声有可能引起变频器的误动作,在设计变频器的输入信号电路时,可参考图2-26所示的正确连接方式,而不能采用图2-27所示的错误连接方式[7]。
图2-25 PLC的继电器输出模块触点与变频器的连接
图2-26 PLC的继电器输出模块与变频器的正确连接示意图
图2-27 PLC的继电器输出模块与变频器的一种错误连接示意图
2.7.2 利用PLC的晶体管输出模块与变频器连接
PLC除了利用2.7.1节介绍的继电器输出模块触点与变频器进行连接外,还可利用PLC的晶体管输出模块与变频器进行连接,如图2-28所示。
使用PLC的晶体管输出模块与变频器连接时,需要考虑晶体管自身的电压、电流容量等因素,以保证系统的可靠性。另外,当输入开关指令信号进入变频器时,有时会发生外部电源和变频器控制电源(DC 24V)之间的串扰,正确的连接方法见2.7.8节的相关内容。
图2-28 PLC的晶体管输出模块与变频器的连接
2.7.3 利用PLC的模拟输出模块与变频器连接
PLC的模拟输出模块输出0~5V、0~6V及0~10V电压信号或0~20mA、4~20mA电流信号,作为变频器的模拟量输入信号。其控制变频器的输出频率,从输出端子连接相应的指示器即可显示变频器的运转状态(如运行正常、故障、输出频率值等),如图2-29所示。由于接口电路因输入信号而异,所以必须根据变频器的输入阻抗选择PLC的输出模块。而连线阻抗的电压降以及温度变化、元器件老化等带来的温度漂移,可通过PLC内部的调节电阻和变频器内部参数进行调节。
图2-29 PLC的模拟输出模块与变频器的连接
当变频器和PLC的电压信号范围不同时,例如变频器的输入信号为0~10V而PLC的输出电压信号为0~5V,可通过变频器的内部参数进行调节。但由于在这种情况只能利用变频器A/D转换器的0~5V部分,所以和输出信号为0~10V的PLC相比,变频器进行频率设定时的分辨率将会更差。反之,当PLC的输出电压信号为0~10V而变频器的输入信号电压为0~5V时,虽然也可通过降低变频器内部增益的方法使系统工作,但由于变频器内部的A/D转换器被限制在0~5V,将无法使用高速区域。这时若要使用高速区域,可通过调节PLC参数或电阻的方式将输出电压降低,如图2-30所示。[7]
2.7.4 利用PLC的输出寄存器模块与变频器连接
变频器可以用PLC的输出寄存器模块作为频率指令信号。通用变频器通常都备有作为选件的数字信号输入接口卡,可直接利用BCD信号或二进制信号设定频率指令。使用数字信号接口卡进行频率设定,可避免模拟信号电路的电压降和温差变化带来的误差,以保证必要的频率精度,如图2-31所示。[7]
图2-30 模拟输出模块输入信号的电平转换
图2-31 PLC的输出寄存器模块与变频器的连接
2.7.5 利用PLC的输出定位模块与变频器连接
变频器也可以将脉冲序列作为频率指令信号,以脉冲序列作为频率指令时,需要使用f/U变换器将脉冲序列转换为模拟信号。当利用这种方式进行精密转换器电路和变频器内部的转速控制时,必须考虑f/U变换电路的零漂、由温度变化带来的漂移以及分辨率等问题,如图2-32所示。[7]
图2-32 脉冲序列作为频率指令时的连接
2.7.6 PLC输入变频器触点信号的连接
在变频器的工作过程中,常需要通过继电器触点或晶体管集电极开路输出的形式将变频器的内部状态(运行状态)通知外部的PLC。而在PLC输入这些信号时,必须考虑继电器和晶体管的允许电压、允许电流等因素,以及噪声的影响,如图2-33所示。在主电路的开闭是以控制AC 220V继电器的线圈或AC 220V的辅助触点,而有的控制信号(DC 12~24V)的开闭是以晶体管进行控制的场合。应注意将布线分开,以保证AC 220V侧的噪声不传至DC 12~24V侧。
图2-33 PLC输入变频器触点信号的连接
对带有线圈的继电器等感性负载进行控制时,感性负载需并联浪涌吸收器或续流二极管;对容性负载进行控制时,容性负载需串联浪涌吸收器或续流二极管,以保证通断时的浪涌电流值不超过继电器和晶体管的允许电流值。[7]
2.7.7 利用PLC的现场总线接口与变频器通信连接
中、高压变频调速系统一般采用中型或大型PLC,这些PLC基本上都具有标准的现场总线接口,其中RS-485(有的提供RS-232接口)通信方式控制变频器的方案得到了广泛的应用,因为它抗干扰能力强、传输速率高、传输距离远且造价低廉。PLC通过其配套的通信模块,或其CPU内置的PROFIBUS-DP接口,或其CPU内置的MPI接口,或通过PLC的通信模块进行点对点的数据通信,通过这些接口的现场总线或光纤网络与变频器连接,进行数据交换和联锁控制,具体的通信连接可参考第3章有关内容。
2.7.8 PLC与变频器配合使用时应注意的问题
PLC与变频器配合使用时应注意以下问题。
1.变频器运行中产生的电磁干扰对PLC的影响
变频器在运行中会产生较强的电磁干扰,而PLC以数字电路为主,工作灵敏度高,很容易受到各种外界电磁干扰的影响。为保证PLC不因变频器主电路断路器及开关器件等电磁干扰源产生的噪声而出现故障,PLC与变频器连接时应注意以下几点:
1)PLC系统接地抗干扰措施见2.6.2节使用要点4)。
2)电源部分的抗干扰措施见2.5.2节。
3)当PLC和变频器安装在同一操作柜中时,应尽可能使PLC和变频器的电线分开走线。
4)使用屏蔽线和双绞线以达到提高抗噪声的目的。
2.PLC扫描时间的影响[7]
在使用PLC进行顺序控制时,如对多条胶带输送机进行顺序控制,由于CPU进行处理需要时间,故总是存在一定时间(扫描时间)的延迟。在设计控制系统时,必须考虑上述扫描时间的影响,尤其在某些场合下,当变频器运行信号投入的时刻不确定时,变频器将不能正常运行。在以自寻速功能构成系统时必须加以注意,图2-34以图形化的方式给出了运用自寻速功能时的参数设定及其含义,图中“∗”表示寻速信号应此运行(正转/反转)信号先接通或同时接通。
图2-34 运用自寻速功能时的参数设定及其含义
3.通过数据传输进行的控制
在某些情况下,变频器的控制(包括各种内部参数的设定)是通过PLC或上位机完成的。在这种情况下,必须注意信号线的连接以及所传数据顺序格式等是否正确,若有异常,将不能得到预期的结果。此外,在需要对数据进行高速处理时,往往需要利用专用总线构成系统。
4.外部电源和变频器控制电源间的串扰[7]
当输入开关信号进入变频器时,有时会发生外部电源和变频器控制电源(DC 24V)之间的串扰。正确的接法如图2-35所示。
图2-35 输入信号防干扰的连接方法[7]