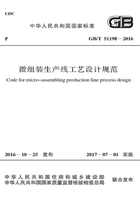
3.12 清 洗
3.12.1 采用清洗工艺应符合下列规定:
1 微组装工艺宜采用气相清洗、超声清洗、等离子清洗方式;
2 对微组装中基板、金属腔体、组件、电路片上需要清除的颗粒、油污、助焊剂、氧化物、多余物去除时,应采用清洗工艺;
3 电路上、焊料上等残留氧化物、引线键合焊盘上氧化物、多余的环氧粘接剂的清除宜采用等离子清洗;
4 焊接后残余的助焊剂、毛发、油污、油脂等污染物的清除,在超声振动不影响待清洗件可靠性及使用性的情况下宜采用超声清洗;否则宜采用溶剂清洗或气相清洗;
5 含有晶体器件、陶瓷器件的组件的清洗,有裸芯片的、键合金丝后的清洗不宜采用超声清洗;
6 微组装清洗工艺的工作媒介宜为化学溶剂、等离子体气体、紫外臭氧气氛、水。
3.12.2 清洗主要工序应符合下列规定:
1 清洗过程宜包括初洗、漂洗、烘干,按清洗介质不同可采用水洗、半水洗和溶剂洗,清洗应在焊后及时进行;
2 应根据助焊剂的成分选择清洗剂;
3 清洗电路片时,应加热清洗或在异丙醇中超声清洗脱水,然后烘干或用氮气吹干;
4 金属腔体、盖板及绝缘子的清洗可采用超声气相清洗,在加热的清洗剂中超声清洗,接着冷却漂洗,然后蒸汽清洗,最后氮气吹干;表面污染严重或去除氧化物时,应加入抛光剂;
5 等离子清洗工艺应根据应用范围合理选用等离子气体,设置等离子清洗的气体的激发功率、清洗时间、真空度、温度;
6 清洗完成后,应按要求晾干或烘干洗后元器件及在制品,并应在10倍~30倍放大的体视显微镜下目检产品质量。
3.12.3 清洗工艺运行条件应符合下列规定:
1 清洗工艺应在7级净化区中进行;
2 清洗工艺中的水洗宜配置纯水系统;
3 清洗工位应建立强制排风环境;
4 清洗后的废液处理应符合现行国家标准《电子工程环境保护设计规范》GB 50814的有关规定。
5 进行清洗工艺时应严格遵守化学品、危险品的安全使用操作规范。