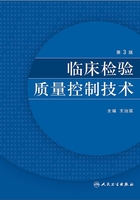
上QQ阅读APP看书,第一时间看更新
第四节 判异准则
判异准则有两类:
(1)点出界就判异;
(2)界内点排列不随机判异。
由于对点子的数目未加以限制,故后者的模式原则上有无穷多种,但现场能够保留下来继续使用的只有下列具有明显物理意义的几种,在控制图的判断中要注意对这些模式加以识别。
一、模式1:点子屡屡接近控制界限
在本模式中,“接近”这个词是很模糊的,应加以界定,一般规定:在距离控制界限的1σ范围内就称为“接近”。在图13-3中出现最左侧线圈的现象表明质量特性值分布的均值μ上移;出现中间线圈的现象表明质量特性值分布的均值μ下移;出现最右侧线圈的现象表明质量特性值分布的标准差σ增大。请读者在图13-3中画出各种对应的分布即可一目了然。
点子屡屡接近控制界限(指点子落在μ±3σ以内,μ±2σ以外的区域内)
设想:连续N个点子中,至少有n个点子接近控制界限,其概率计算公式为:
表13-2 点子屡屡接近控制界限概率计算

注:①只计算N= 1~7

②计算公式P=(0.0429) k·(0.9544) N-k
③P≤0.01为异常
表13-2中计算的内容是N= 1~7的概率计算结果。凡P≤0.01的事件都是异常事件,归纳之后总结以下判断准则:
a)连续3个点子中至少有2个点子接近控制界限(如图13-3所示);

图13-3 三点中有两点接近控制界限判异
b)连续7个点子中至少有3个点子接近控制界限;
c)连续10个点子中至少有4个点子接近控制界限。
通常只应用第一条,因为它点数少,容易判断。
二、模式2:链
出现图13-4的现象表明质量特性值分布的均值μ向出现链的这一侧偏移。现作如下说明:
(1)在控制图中心线一侧连续出现的点称为链,其中包含的点子数目称为链长。链长≥9,判异。
(2)现分析其α:
P(中心线一侧出现长为9的链)= 2(0.9973/2)9= 0.0038=α9
由于α 9= 0.0038与点出界就判异准则的α= 0.0027相近,故确定9点链判异。若链长≥7判异,则α 7= 0.0153比α= 0.0027约大6倍,偏大,不合适。
过去采用7点链判异,目前国外改为9点链判异,这主要是因为现在推行SPC一般都采用电脑进行,所有判异准则都用电脑来判断,从而整个系统的α 总增大了。不难证明:
式中,α i为第i条判异准则的显著性水平。为了减少α 总,就需要减少每条判异准则各自的α。

图13-4 7点链
三、模式3:间断链
间断链是指链中个别点子跳到另一侧,见图13-5。

图13-5 间断链
判异准则:
(1)连续11个点,至少有10个点在一侧;
(2)连续14个点,至少有12个点在一侧;
(3)连续16个点,至少有14个点在一侧;
(4)连续20个点,至少有16个点在一侧。
根据概率计算可知,上述4条判异准则的显著性水平分别为:
α1= 1.14%,α2= 1.25%,α3= 1.22%,α4= 1.12%
由于上述4条准则的α分别大于0.01,偏大,不适合现在应用电脑推行SPC的情况,应加以改造,增加判异准则中的点子数目,使其显著性水平变小。在未加以改造之前,暂不用为宜。
四、模式4:趋势
出现图13-6的下降趋势表明质量特性值分布的均值μ随时间而减少。点子递增或递减的状态称为趋势。注意,如图13-6所示的下降趋势,后面的点子一定要低于或等于前面的点子,否则趋势中断,需要重新算。对于上升趋势也有相应的要求。6点趋势判异。

图13-6 7点下降趋势判断异常
关于趋势的α的分析,由于
于是
从以上3个式子可见,α 6与点出界就判异准则的α= 0.0027最为相近,故确定6点趋势判异。
五、模式5:点子作周期性变化
点子呈周期性变化(指点子以一定的时间间隔作相同的上升或下降的重复排列)判异,如图13-7所示。

图13-7 点子呈现周期性变化判异
产生周期性变化的常见原因如下:
(1)操作人员疲劳;
(2)原材料的发送有问题。
消除上述周期性变化可使产品质量更加稳定。
六、模式6:点子集中在中心线附近
在模式6中“中心线附近”又是个模糊词语,我们规定在中心线±1σ的范围内称为“中心线附近”。出现图13-8的现象表明质量特性值分布的标准差σ减小。注意,碰到这种情况不要高兴过早,首先需要检查下列两种可能性:

图13-8 连续15点集中在中心线附近判异
(1)是否应用了假数据,弄虚作假;
(2)是否分层不够。
以老师傅车制机螺丝为例,设老师傅与青工早晚两班倒,操作同一台机床,作控制图时两人数据混在一起未分层,即未分类。于是从数理统计知
故
σ混>σ青
现在若用σ 混(6σ 混为控制图上下控制界限的间隔距离)作控制图,恰好又碰上用老师傅的数据打点,就会出现本模式。
在排除了上述两种可能性之后,这时才能总结现场减少标准差σ的先进经验,并加以推广。
模式6的α为α 15= 0.0033,也与点出界就判异准则的α= 0.0027相近。
注意事项:
(1)这种现象对初学者而言,往往认为是质量改进的结果,在实际工作还应注意分析,因为除此之外还有可能是控制图设计中的错误而导致控制界限过宽。
(2)控制图反映过程异常,应注意有坏的异常,还有可能出现好的异常。无论哪种异常,均应进行质量分析。
坏的异常出现时,应通过质量分析,找出确切的影响原因,采取措施将异常因素消除。
当确认是好的异常(如望目值质量特性的控制图中,点子过多地集中在中心线附近,说明质量数据分布的标准偏差已经减小;望大值质量特性的控制图中点子过多地接近上控制界限,甚至于超出上控制界限,说明质量数据分布的中心值向正向偏移;望小值质量特性的控制图中点子过多地接近下控制界限,甚至超出下控制界限,说明质量特性数据分布的中心值向负向偏移)时,也应通过质量分析,找出确切的影响原因,采取措施将良好的异常因素加以保持,并经生产验证后按新的典型分布重新设计控制图。