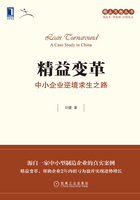
安镁深圳的窘境
随着经济全球化,中国加入WTO,安镁跟着客户产业转移的脚步开始进入中国市场。2005年,安镁开始在中国投资工厂,收购了一家位于广东深圳的民营小企业,也就是后来的安镁金属制品(深圳)有限公司,简称安镁深圳。
好了伤疤忘了痛,何况还是别人的伤疤。收购的工厂是一家非常典型的民营小企业:是批量生产模式,现场存在大量的库存和返工。但是在美国转移订单和技术的支持下,纵使这样的工厂也利润良好,销售额每年稳步增长,员工待遇高于平均水平。客户、老板和员工都很高兴。虽然安镁对外宣称也是在做精益,但实际上没有员工真的在乎精益。精益不精益都没关系,企业能赚钱,员工待遇福利好才是真的。
那个时候中国工业增加值在飞速增长,尤其是在改革开放前沿的深圳。只要有增长的订单,就迅速接下订单,生产出来才是第一优先级要考虑的事情。那时候流行的是,时间就是金钱。确实,安镁深圳在那个环境里过了好些年好日子。
2008年的全球经济危机,让安镁管理层脊背一凉,以为会重蹈2001年美国工厂的覆辙。但是中国政府却在危急之时力挽狂澜,4万亿元的刺激成了全球市场的一剂强心针。
经济危机期间,国家层面的基建投资是刺激经济的重要手段。在当时的环境下,其中一项基建投资就是3G网络建设。突如其来的巨大需求让电信设备供应商为了迅速量产抢占市场使出了浑身解数。安镁作为二级供应商,又地处深圳,自然是拿出了深圳速度。安镁的工程师和客户的工程师一起打拼,吃住在工厂,一起设计、出图,然后模具设计和制造几乎同时开始。设备投资也基本上一路绿灯,迅速安装投产。在这个特定的历史时段,良好的品质和速度自然赢得了广泛的市场和丰厚的利润。
2008年,很多制造企业都在经济危机的冲击下苦苦支撑。而安镁深圳却度过了几年非常美好的日子。车间里一切都是为了赶货,几乎从未停下来过。车间地面的油泥足有1厘米厚,用员工的话来说:“都下不去脚。”但是每月的利润和超额奖金让大家都忘记了脚下的油泥,自然也没人会提到精益。那时中国的管理团队去美国总部都会受到英雄一般的欢迎。因为他们没有经历过美国的那段危机,所以也就不会想起如何把美国工厂的经验复制到中国工厂来。因为利润高于美国工厂,所以他们更有一种心态觉得美国还不如深圳。
历史总是惊人的相似,这次不是经济危机,而是行业本身。3G的投资建设需求是有峰值的,一旦基站的布设大体完成,后续需求会呈几何级数下降。2011年开始,安镁深圳的销售额开始大幅降低。雪上加霜的是,国内基础工业的蓬勃发展,使安镁原来依靠昂贵的整机进口设备和多年积累的工程技术经验所建立的壁垒消失殆尽。美国转移来的订单也由于市场下滑,逐渐流失。
2011年开始,安镁深圳进入亏损,后来亏损竟持续数年。总部因此提供一切可能的支持,希望帮助深圳工厂通过精益来实现扭亏为盈。
国内许多企业开始实施精益的时候,都会有以下类似的怀疑和挑战:
·老板不理解精益,不支持或者只是口头上支持精益,把执行任务交给精益经理,期待精益是一剂速效药。
·自身行业和汽车行业相差甚远,丰田的工具和方法无法落地。
·在中国没有同行的经验可以借鉴,不知道是不是可行。
·没有合适的精益专家。
中国精益圈的许多朋友这个时候看安镁深圳,应该非常羡慕:
·安镁深圳和美国芝加哥工厂的运作基本相同,甚至部分产品全部运作都一样。
·安镁深圳有美国工厂的成功变革经验可以拿来用。
·安镁董事长是个精益的信徒,曾带领美国安镁通过精益变革扭亏为盈,建立了一个精益标杆工厂。
·安镁深圳这些年也在内部培养了一批精益专家。
安镁此时是天时地利人和。如果按照正常故事发展,下一集的情节就应该是安镁深圳复制美国工厂的变革历史,通过精益变革扭亏为盈,在深圳复制一个精益标杆工厂。
在安镁董事长的决策支持下,中国管理层按照美国的步骤开始了大刀阔斧的精益变革:
·改革组织架构,打破部门建制,建立两个横向的价值流组。
·建立后加工和CNC[1]连接的生产单元。
·取消计划部门,建立均衡化看板,用看板来管理生产计划。
·董事长定期前往深圳,选定题目,亲自下线,带领并辅导为期一周的改善活动(改善周)。
3年过去,事与愿违。如此相似的亲兄弟工厂,深圳的进展却和芝加哥工厂相去甚远。
·价值流组织架构遇到强烈的“反弹”。十几个部门突然变为两个价值流组,很多原来的部门经理只能回到工程师或者职员的职位。在“官本位”的思想影响下,流失了一半以上的中层,而且首先辞职而去的都是“恃才傲物”的优秀员工。
·价值流组织架构更大的困难是选拔和培养合格的价值流经理。在这个组织架构下,价值流经理不再是传统的生产经理或者品质经理。价值流经理要有能力掌握全流程的生产工艺及关键点、工程、品质的相关知识,还要懂得订单接收、审核、排产、发货甚至收款的相关业务知识。在财务报表分开核算之后,价值流经理还要懂财务。相对年轻的深圳工厂没有合适的人能担此重任。
·建立了生产单元却卡在换模时间上。CNC的换线时间没有迅速缩短到一定水平就建立生产单元,导致后加工经常停线。在客户催货和员工抱怨下,生产状态几乎回到从前,生产单元形同虚设,成为象征式的摆设,实质上等于回到了原来的大批量生产模式。如果不是董事长坚决反对,估计生产单元真的会被拆掉,会回到原来的工艺专业化的布局。
·生产单元的形同虚设直接导致了均衡看板的有名无实,可视化看板只有在董事长来的时候才会更新。而且在服务器上,只有一个共享的Excel文件用于做生产计划。大家把这个表格打印出来作为生产指令单,经常会出现打印的版本不一样导致订单没有及时生产或者生产过多。
·在董事长亲自带队的改善周,声势浩荡,但是这种集中的“脱产”改善让大家疲于奔命,每次大家都将其当作一个负担。董事长走了之后大家心照不宣地舒一口气,一切又回到了平时。因此再好的改善成果也无法维持。
如此,3年过去,亏损依旧,士气低落,品质抱怨频发,好几个重要的客户都因此离开。库存居高不下,但是客户需要的却没有,准时交货率不到80%。
[1] CNC, Computer Numerical Control, 计算机数控。CNC机床或CNC加工中心也简称CNC。