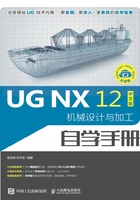
1.3.3 数控加工编程的内容与步骤
正确的加工程序不仅应保证加工出符合图样要求的合格工件,同时应能使数控机床的功能得到合理的应用与充分的发挥,以使数控机床能安全、可靠、高效地工作。数控加工程序的编制过程是一个比较复杂的工艺决策过程。一般来说,数控编程过程主要包括分析零件图样、工艺处理、数学处理、编写程序单、输入数控程序及程序检验,计算机辅助数控编程的一般步骤如图1-18所示。

图1-18 计算机辅助数控编程的一般步骤
数控加工编程主要包含以下几个步骤:
1. 加工工艺决策
在数控编程之前,编程人员应了解所用数控机床的规格、性能、数控系统所具备的功能及编程指令格式等。根据零件形状尺寸及技术要求,分析零件的加工工艺,选定合适的机床、刀具与夹具,确定合理的零件加工工艺路线、工步顺序以及切削用量等工艺参数,这些工作与普通机床加工零件时的编制工艺规程基本是相同的。
(1)确定加工方案:此时应考虑数控机床使用的合理性及经济性,并充分发挥数控机床的功能。
(2)工夹具的设计和选择:应特别注意要迅速完成工件的定位和夹紧过程,以减少辅助时间。使用组合夹具,生产准备周期短,夹具零件可以反复使用,经济效果好。此外,所用夹具应便于安装,便于协调工件和机床坐标系之间的尺寸关系。
(3)选择合理的走刀路线:合理地选择走刀路线对于数控加工是很重要的,应考虑以下几个方面。
- 尽量缩短走刀路线,减少空走刀行程,提高生产效率。
- 合理选择起刀点、切入点和切入方式,保证切入过程平稳没有冲击。
- 保证加工零件的精度和表面粗糙度的要求。
- 保证加工过程的安全性,避免刀具与非加工面的干涉。
- 有利于简化数值计算,减少程序段数目和编制程序的工作量。
(4)选择合理的刀具:根据工件材料的性能、机床的加工能力、加工工序的类型、切削用量以及其他与加工有关的因素来选择刀具,包括刀具的结构类型、材料牌号、几何参数。
(5)确定合理的切削用量:在工艺处理中必须正确确定切削用量。
2. 刀位轨迹计算
在编写NC程序时,根据零件形状尺寸、加工工艺路线的要求和定义的走刀路径,在适当的工件坐标系上计算零件与刀具相对运动的轨迹的坐标值,以获得刀位数据,诸如几何元素的起点、终点和圆弧的圆心、几何元素的交点或切点等坐标值,有时还需要根据这些数据计算刀具中心轨迹的坐标值,并按数控系统最小设定单位(如0.001mm)将上述坐标值转换成相应的数字量,作为编程的参数。
在计算刀具加工轨迹前,正确选择编程原点和工件坐标系是极其重要的。工件坐标系是指在数控编程时,在工件上确定的基准坐标系,其原点也是数控加工的对刀点。工件坐标系的选择原则如下。
- 所选的工件坐标系应使程序编制简单。
- 工件坐标系原点应选在容易找正,并在加工过程中便于检查的位置。
- 引起的加工误差小。
3. 编制或生成加工程序清单
根据制定的加工路线、刀具运动轨迹、切削用量、刀具号码、刀具补偿要求及辅助动作,按照机床数控系统使用的指令代码及程序格式的要求,编写或生成零件加工程序清单,并需要进行初步的人工检查,以及进行反复修改。
4. 程序输入
在早期的数控机床上都配备光电读带机,作为加工程序输入设备,因此,对于大型的加工程序,可以制作加工程序纸带,作为控制信息介质。近年来,许多数控机床都采用磁盘、计算机通信技术等各种与计算机通用的程序输入方式,实现加工程序的输入,因此,只需要在普通计算机上输入编辑好的加工程序,就可以直接传送到数控机床的数控系统中。当程序较简单时,也可以通过键盘人工直接输入数控系统中。
5. 数控加工程序正确性校验
通常所编制的加工程序必须经过进一步的校验和试切削才能用于正式加工。当发现错误时,应分析错误的性质及其产生的原因,或修改程序单,或调整刀具补偿尺寸,直到符合图样规定的精度要求为止。