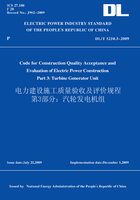
4.12 Turbine-driven Feedwater Pump Set Erection
Applicable scope:applicable to turbine-driven feedwater pump set erection,with the following inspection items:foundation preparation,sole plate grinding and in place,bearing(pedestal)and oil baffle inspection erection,cylinder assembly,inspection and in place,rotor in place,steam seal and adjustment of oil baffle groove center,cylinder fixing,diaphragm,steam seal erection,flow gap measurement and adjustment,thrust collar positioning,driving ST covering,bearing pedestal covering and gear type turning gear erection,driving ST regulation and protection system inspection and erection,driving ST lubricating oil system erection,driving ST trial run,turbine driven feedwater pump erection,feedwater set coupling centering,turbine driven feedwater pump trial run.Oil system flushing refers to Table 4.5.6-10;secondary grouting refers to general table 4.3.20.
4.12.1 Foundation preparation,iron cushion and foundation bolt machining and erection inspection and acceptance are given in Table 4.12.1.
Table 4.12.1 Foundation preparation,iron cushion and foundation bolt machining and erection

4.12.2 Sole plate grinding and in place inspection and acceptance are given in Table 4.12.2.
Table 4.12.2 Sole plate grinding and in place

4.12.3 Bearing(pedestal)and oil baffle inspection erection inspection and acceptance are given in Table 4.12.3.
Table 4.12.3 Bearing(Pedestal)and oil baffle inspection erection

4.12.4 Cylinder assembly,inspection,in place inspection and acceptance are given in Table 4.12.4.
Table 4.12.4 Cylinder assembly,inspection and in place

4.12.5 Rotor in place,steam seal and oil baffle groove center adjustment,cylinder fixing inspection and acceptance are given in Table 4.12.5.
Table 4.12.5 Rotor in place,steam seal and oil baffle groove center adjustment,cylinder fixing

Table 4.12.5(Continued)

4.12.6 Diaphragm,steam seal erection inspection and acceptance are given in Table 4.12.6.
Table 4.12.6 Diaphragm seal erection

Table 4.12.6(Continued)


Fig.4.12.6 diaphragm clearance
4.12.7 Flow gap measurement and adjustment,thrust collar positioning inspection and acceptance are given in Table 4.12.7.
Table 4.12.7 Flow gap measurement and adjustment,thrust collar positioning

4.12.8 Driving ST covering inspection and acceptance are given in Table 4.12.8.
Table 4.12.8 Driving ST covering

Table 4.12.8(Continued)

4.12.9 Bearing pedestal covering and turning gear erection inspection and acceptance are given in Table 4.12.9.
Table 4.12.9 Bearing pedestal covering and turning gear erection

Table 4.12.9(Continued)

4.12.10 Driving ST governing and protection system inspection and erection inspection and acceptance are given in Table 4.12.10.
Table 4.12.10 Driving ST governing and protection system inspection and erection

Table 4.12.10(Continued)

Table 4.12.10(Continued)

4.12.11 Driving ST lubricating oil system erection inspection and acceptance are given in Table 4.12.11.
Table 4.12.11 Driving ST lubricating oil system erection

Table 4.12.11(Continued)

4.12.12 Driving ST trial run inspection and acceptance are given in Table 4.12.12.
Table 4.12.12 Driving ST trial run

Table 4.12.12(Continued)

4.12.13 Turbine driven feedwater pump erection inspection and acceptance are given in Table 4.12.13.
Table 4.12.13 Turbine-driven feedwater pump erection

Table 4.12.13(Continued)

4.12.14 Feedwater pump set coupling centering inspection and acceptance are given in Table 4.12.14.
Table 4.12.14 Feedwater pump set coupling centering

Table 4.12.14(Continued)

4.12.15 Turbine driven feedwater pump trial run inspection and acceptance are given in Table 4.12.15.
Table 4.12.15 Turbine-driven feedwater pump trial run

4.12.16 Mandatory implementation inspection of turbine-driven feedwater pump set erection subsection project is given in Table 4.12.16.
Table 4.12.16 Mandatory implementation inspection table of turbine-driven feedwater pump set erection subsection project

Table 4.12.16(Continued)

Table 4.12.16(Continued)

Table 4.12.16(Continued)

Table 4.12.16(Continued)
