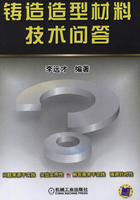
3.2 湿型砂的特点及配比
79.湿型砂的主要特点是什么?
湿型砂是以膨润土作粘结剂的一种不经烘干的型砂。湿型砂的基本特点在于砂型不需烘干、不经固化、具有一定的湿强度,虽然强度较低但是退让性较好,而且便于落砂。因为砂型不需烘干,所以造型效率高、生产周期短、材料成本低,便于组织流水生产。但是因为砂型不经烘干,所以在浇注时,砂型表面就出现了水分的汽化和迁移,使铸件容易产生气孔、夹砂以及砂眼、胀砂、粘砂等缺陷。
为了充分发挥湿型优点,提高铸件质量,在生产过程中必须保持型砂性能稳定、砂型紧实均匀及铸造工艺合理。因此,湿型工艺的发展一直是和造型机械及造型工艺的发展紧密相连的。目前湿型机械化造型已从普通的机器造型发展到高密度机器造型,造型的生产率、砂型的紧实度、铸件的尺寸精度不断提高,铸件表面粗糙度值则不断降低。各种造型方法的特点及所生产的铸件尺寸精度和表面粗糙度见表3-12。
表3-12 各种造型方法的特点、铸件的尺寸精度(GB/T 6414—1999)和表面粗糙度(GB/T 6060.1—1997)
① 砂型上下端面的硬度值,用B型型砂硬度计测出。
一般来说,压实比压大于0.7MPa的称为高压造型。高压造型的砂型密度可达1.5~1.6g/cm3,硬度在90以上(用B型硬度计测量),故也称高密度造型。高密度造型包括多触头高压造型、无箱挤压造型、气冲造型及静压造型等。这几种造型法所用湿型砂的性能和配比比较接近。
湿型砂主要应用于生产中小型铸件,特别是应用于大批量机械化造型生产汽车、拖拉机、柴油机、轻纺机械等铸件。采用湿型(不刷涂料时)也可生产重达几百千克的铸铁件。
80.湿型砂的主要原材料组分是什么?如何选用?
湿型砂的基本组分有原砂、膨润土和煤粉。为改善湿型砂的一些特殊性能,有时还添加重油、淀粉以及氧化铁粉等。
1)选用原砂时,首先要根据所浇注的合金种类确定原砂的二氧化硅含量;其次根据混合料种类确定原砂泥的含量及其他性能;还要根据铸件大小确定原砂粒度。湿型砂所用原砂一般较细,粒度主要有50/100、70/140和100/200筛号,如采用水洗砂,泥的质量分数最好在1%以下。高密度造型的湿型砂,为减小砂型受热时的膨胀,避免引起夹砂,原砂的SiO2含量不必过高,粒形不必很圆,可以采用多角形原砂,粒度不宜过于集中,一般采用三筛砂或四筛砂,必要时可将两种粒度的原砂混合使用,以达到合适的粒度要求。
2)选用膨润土时,首先应考虑的是膨润土的纯度,即其中的有效蒙脱石含量。为防止铸件夹砂,最好采用热湿拉强度较高的膨润土,如天然或人工活化的钠基膨润上。也可以采用部分活化的钠基膨润土,或是将钠基膨润土与钙基膨润土按一定比例混合后加入,以达到型砂对热湿拉强度的要求。
3)在选用煤粉时,首先检测煤粉的挥发分,有条件时还可增加检测煤粉的焦渣特征和光亮碳含量。为保持较好的造型性能,可将煤粉与重油或渣油配合使用,或者加入一种由膨润土、煤粉及其他高挥发分的炭质材料组成的复合添加剂。
4)为提高型砂韧性、减少型砂回弹现象并使型砂水分保持在一定范围,高密度造型的型砂中一般还加入少量α淀粉或糊精。淀粉类附加物对型砂性能的影响见表3-13。由表3-13可见,α淀粉与糊精的使用效果有明显差异。糊精能显著提高型砂的表面强度、热湿拉强度和韧性,但使湿压强度和流动性剧烈下降。α淀粉虽然对型砂的表面强度、热湿拉强度和韧性的提高程度不如糊精,但对湿压强度和流动性影响不大。
表3-13 淀粉类附加物对型砂性能的影响
注:水平箭头表示基本不变,箭头向上或向下表示提高或降低,双箭头表示显著提高或降低。
5)氧化铁粉能降低型砂的烧结点,在浇注时使型腔表面玻璃化,减轻铸件表面粘砂和球墨铸铁件的皮下气孔缺陷。氧化铁粉仅在正确使用时才有好的效果,加入的质量分数一般不超过3%。
81.在拟定湿型砂配比之前应考虑哪些事项?
在拟定湿型砂配比之前,必须首先根据浇注的合金种类、铸件特征和要求、造型方法和工艺及清理方法等因素确定型砂应具有的性能范围;然后再根据各种原材料的品种和规格、砂处理方法、设备、砂铁比及各项材料烧损比例等因素拟定型砂的配比。一个新的型砂系统通常在开始使用前,先参考类似工厂中比较成功的型砂系统的经验,再结合本厂的具体情况,初步拟定出型砂的技术指标和配比,进行实验室配砂,并调整配比,使性能符合指标要求;然后进行小批混制,造型浇注,对型砂的技术指标及配比进行反复修改,直到试验合格才可投入正式生产。一个车间的型砂技术指标和配比要经过长期生产验证才能确定。
82.如何根据合金种类来拟定湿型砂的配比?
由于铸铁件、铸钢件和铸造非铁合金件的合金特性和浇注温度不同,因此它们用的湿型砂配方也不相同。
铸铁件的合金熔点较高(略低于铸钢),浇注温度一般为1200~1400℃,因此对湿型砂耐火度的要求可比铸钢件低。
铸铁件湿型砂的显著特点是其中普遍加入了煤粉,因而亦称“煤粉砂”。煤粉的作用主要在于防止粘砂,如煤粉与渣油液混合使用可使铸铁件表面更加光洁,同时减小了夹砂缺陷的倾向,还有利于保持型砂中水分和消除型砂中的团块,使型砂比较松软,从而使流动性得到改善。
铸铁件用的湿型砂配比,工厂习惯将旧砂和新砂之和作为100(质量份),膨润土、煤粉和其他附加物在100之外。之所以这样,是因为在实际生产中旧砂与新砂的加入量基本保持不变,而粘土、煤粉等附加物的加入量需要根据型砂性能的要求和变化随时调整,如果将旧砂、新砂、各种附加物、水一起算做100,则一旦调整其中的某一种材料的加入量,那么各种材料的质量份就必须重新计算,而且新、旧砂的质量份会出现小数点以后的数字,计算和控制都十分麻烦。在型砂配比中,旧砂加入量一般为80~95,新砂加入量为5~20(生产砂芯多的铸件时,因大量芯砂进入旧砂系统,新砂加入量减为0~5),活性膨润土加入量为6~10,有效煤粉加入量为2~7,如有需要还可以加入0.5~1.0的α淀粉,以改善型砂性能。
铸钢件的合金熔点很高,浇注温度高达1500~1650℃,因此要求混型砂有较高的耐火度和透气性。
在铸钢件用的湿型砂中,新砂所占比例较大,膨润土加入量也相应增多。为提高型砂性能,常加入少量有机水溶性粘结剂(例如糊精、α淀粉)等附加物。
铸造非铁合金件的合金(铜合金、铝合金、镁合金)熔点一般不高,铜合金浇注温度约1200℃,铝合金浇注温度一般不超过700~800℃,镁合金浇注温度更低,因此时湿型砂的耐火度和化学热稳定性要求不高。但非铁合金液一般极易氧化,主要要求是防止合金液渗入铸型,要求铸件有较清晰的轮廓、美观及尺寸比较精确,因此,原砂粒度一般较细,含水量较低,以减少型砂的发气量和提高流动性。铸造铜合金的湿型砂中常加入重油以提高铸件的表面质量。在铸造镁合金的湿型砂中,还需加入保护剂,如硫磺粉、硼酸等,以防止镁液氧化。
膨润土和煤粉的加入量必须根据所生产的铸件不同和铸件品质情况具体确定。如果在一个型砂系统的造型线上生产几种铸件的砂铁比不同、芯砂流入量不同和工艺参数不同,则回用旧砂中的活性膨润土含量、有效煤粉含量都不相同。若始终按照固定批料配方所规定的膨润土和煤粉补加量进行加料和混砂,即使型砂紧实率符合要求,也会造成型砂性能波动和铸件废品率增高。为此,生产多种铸件的型砂系统应当根据每天的生产计划来改变膨润土和煤粉的加入量。
相关铸造造型材料手册列出了一些铸铁件、铸钢件、非铁合金件湿型砂所用或曾经使用的配比和性能实例。需要说明的是,这些配方分别是根据各厂的具体条件制定的,包括原材料来源及性能、造型方法、铸件材质及大小、壁厚、生产习惯、检测仪器等许多因素,型砂性能的取样大多是从混砂机旁,而不是从造型处,而且数值也并非全部合理,因此仅供相关工厂参考,而不是作为推荐,其他工厂不可照搬。
83.什么是高密度造型型砂?其有何特点?
高密度造型是指提高造型紧实力以制得较高紧实程度或较高密度砂型的造型方法。过去高密度造型仅指各种高压造型。近年来,高速的冲击造型,包括动力(机械)冲击和气流冲击造型得到了越来越广泛的开发和应用,也属高密度造型。
与用通常方法造型相比较,高密度造型的型砂性能具有以下特点:
(1)湿强度 为提高砂型的硬度,避免浇注时型壁移动,型砂应当具有高的湿强度,因为高湿强度是保证砂型高硬度的必要条件。
(2)紧实率和含水量 型砂比通常造型型砂稍干一些,因为在高密度造型条件下,型砂较湿易引起铸件产生气孔缺陷或水爆炸现象。
(3)透气性 高密度造型的砂粒排列比较密实,所以要求透气性稍微高些。
(4)抗夹砂结疤能力 高密度造型的紧实程度高,所以希望型砂具有较好的抗夹砂结疤能力。
(5)抗机械粘砂能力 由于高密度造型的砂型比较紧实,生产铸铁件时可以降低型砂中的有效煤粉含量。这对于防止呛火和爆炸粘砂也有好处。
(6)流动性 气流冲击造型的紧实过程是在一瞬间使砂粒高速运动。因此要求型砂在紧实前为疏松的低密度状态,有利于砂粒在高加速度下产生高的工作压力,使模板处砂型得到更好的紧实。高压造型用的型砂中加入质量分数为0.5%~1.0%的α淀粉,可提高型砂的热湿拉强度,减少热压应力,延长型砂表面激热开裂时间,提高抗夹砂能力;可提高砂型表面强度和风干后表面强度,加强抗冲蚀能力,减少冲砂等缺陷。特别是在应用钙基膨润土的型砂中加α淀粉,能使型砂热湿拉强度剧增,韧性明显提高。
84.如何控制手工造型和震实机器造型方法生产中小灰铸铁件时的型砂性能?其混砂的合理配比应是什么?
表3-14中的数值综合了一些国内外生产中小灰铸铁件比较稳定的铸造工厂的型砂性能。含泥量是指型砂而言,不是旧砂含泥量。性能的波动范围根据铸件大小、厚薄和结构,以及清理方法不同而异,一般情况可取中间值。表中有效膨润土量是指5.00g型砂的0.20%浓度试剂纯亚甲基蓝溶液滴定量;有效煤粉量是指1.00g型砂900℃的发气量。
表3-14 国内外铸造工厂生产中小灰铸铁件的型砂性能
注:其型砂取样来自造型处。
至于混砂的配比是很难做出合理推荐的,因为各厂所用的原材料品质不同,各种原材料在浇注时的烧损程度不同,旧砂回用的处理方法不同。表3-15所推荐的混砂配比的条件是原材料为内蒙古砂、优质膨润土、优质煤粉;砂铁比5~7;树脂芯砂混入旧砂中约占旧砂质量的0.5%~2%;无旧砂除尘冷却装置;铸件经抛丸清理。一般情况可取中间值。
表3-15 国内某厂两种造型条件下的型砂配比
85.在生产设备和检测设备均比较简陋的工厂,如何控制混砂配比才能浇注出高质量的铸件?
在生产设备和检测设备均比较简陋的工厂,其旧砂中残余的有效膨润土和煤粉都是难以准确估计的,要得出适宜的混砂配比只能靠生产经验来确定。混砂时膨润土加入量靠边混砂边手捏,发现强度不足就适量补加一些膨润土,如果感到强度过高就向碾中补加旧砂或新砂。但是砂中需要补加多少煤粉就只能看浇注后的铸件表面光洁程度,确定下一批铸件的煤粉加入量。如果铸件表面出现蓝色,对于无抛丸清理设备的工厂可能已经合适,但需注意煤粉不可过多,以防气孔缺陷。如果单一砂混砂时,膨润土和煤粉已经加入相当多,例如膨润土加入2.0%以上,煤粉加入量1.0%以上,而型砂强度仍然不高,铸件表面仍然毛糙,则表明所用膨润土和煤粉为等外品,必要时需更换材料来源。
86.采用静压和挤压两种高密度造型方法,典型的型砂性能和混砂配比应当如何确定?
表3-16归纳了一些国内外高密度造型线的造型机处型砂性能要求。有效膨润土量是指5.00g型砂的0.20%浓度试剂纯亚甲基蓝溶液滴定量;有效煤粉量是指1.00g型砂900℃的发气量。静压造型的湿压强度、有效膨润土和有效煤粉取中间值及以上,挤压造型取中间值及以下。根据气候条件不同及运送距离不同,混砂机取样含水量可能需比造型机处提高0.2%~0.4%,紧实率提高2%~4%。
表3-16 国内外高密度造型线的造型机处型砂性能要求
注:型砂取样来自造型机处。
型砂的混砂原材料品质不同,铸件厚薄不同,砂型砂铁比不同,配比也就不同。表3-17列出了国内某铸造厂的较成功的型砂配比。其砂型用原砂为内蒙古砂或平潭砂,粒度为70/140目,合脂芯砂和冷芯盒芯砂用原砂为50/100目。膨润土为辽宁优质活化土,煤粉为高效煤粉。静压线生产较厚大铸铁件,假定砂铁比为5~7。难起模的砂型局部必要时覆盖加有α淀粉的面砂。挤压线生产较薄小铸铁件,假定砂铁比为6~8。新砂加入是为了补充落砂时砂粒部分的损失,并冲淡逐渐积累的灰分。混入旧砂中的溃散芯砂作用与新砂类似,只是会使型砂粒度变粗,砂粒上附着的残留树脂膜也可代替一部分煤粉起防粘砂作用。
表3-17 静压和挤压造型的型砂配比
87.溃散后的树脂芯砂混入量约占旧砂总量的10%左右时,其是否正常?
表3-18列出了国内某厂148造型线用型砂配比。从表中可以看出:①旧砂中树脂砂混入量约10%,即使不计旧砂中树脂芯砂的长时间累积量,加上新砂3%后,砂子更新量已经高达13%,必然会迫使该厂经常丢弃一些旧砂,以免砂系统过满。应设法降低芯砂混入量。②由紧实率/水分=11.8~13.2的比值来看,型砂的含泥量不高,是溃散芯砂混入过多引起的。③透气性过高是较粗颗粒树脂芯砂(通常粒度50/100)大量混入造成的,铸件表面会有粘砂。如果煤粉品质不够好,粘砂就更加严重,估计砂型表面喷涂料是不可避免的。④单一砂中膨润土加入量1.2%~1.3%,而型砂湿压强度只有0.12~0.15 MPa。可以确定或者膨润土品质不良,或者混砂程度严重不足(例如混砂时间短、刮板磨损未能经常调整和更换、混砂机中粘附大量砂子、没有每日清理干净),型砂中会出现大量砂豆。
表3-18 国内某厂148造型线用型砂配比
88.如何解决机械化造型机流水线上的旧砂中混入过量芯砂所导致的问题?
如国内某厂用造型机流水线生产汽车发动机缸体,在落砂时有大量溃散的冷芯盒芯砂掺入旧砂中,使旧砂量增多,砂系统容纳不下,只好定期扔掉一些旧砂。实际上扔掉的都是好的砂子,浪费了资源。更严重的是芯砂掺入后混出的型砂性能不好,发脆且缺乏韧性,而且型砂粒度明显变粗,透气率达到180~200,砂型表面如果不喷刷涂料就会产生铸件表面粗糙和粘砂缺陷。
事实上,冷芯盒芯砂大量混入型砂中,优点是残余芯砂也是光亮碳析出物,能够代替部分煤粉防止铸件表面粘砂缺陷。缺点是必然会使型砂性能变脆和发散。壳芯和合脂芯砂也有类似倾向。这只能靠少许增加膨润土量、延长混砂时间,必要时再加入少许α淀粉才能有所好转。国内很多铸造工厂混砂时间与国外相比严重不足。例如国内某拖拉机制造企业,经过实践发现,只要适量延长混砂时间就可使冷芯盒芯砂混入旧砂而使型砂变脆和起模性变差的问题大为好转。
由于溃散芯砂混入旧砂中,而且越来越多,透气性必然逐渐增高。如果型砂透气性超过150~160,只好在砂型表面喷刷醇基或水基涂料,只喷下型或上下型都喷。在国内外的发动机铸件生产工厂类似情况也普遍存在。美国有一家铸造工厂的经验是混砂时改为加入粒度100/140的两筛分布原砂,加入量为5%,使型砂粒度保持在50/140的四筛分布,据称效果良好。
89.湿压强度过高或过低对铸件有何不良影响?
如果型砂试样测得湿压强度过低,同时砂型的紧实程度也过低,则制得的砂型强度和砂型硬度必然显得过低。砂型强度和硬度不足就会造成冲砂、掉砂及砂孔缺陷,还会发生胀砂、缩松而影响铸件尺寸精度和致密性。这就是如今先进的湿型铸造工厂采用高强度型砂和高密度造型方法的原因。但是型砂湿压度也不可过高,否则会使溃散性变差,落砂时大砂块难以破碎,也会使铸件产生裂纹的倾向增大。
型砂试样强度过高的原因主要是所含有效膨润土量过多,给混砂造成很多困难,只有靠有力和足够长时间的混合才能均匀,否则极易出现未混匀的膨润土所形成的砂豆。此外,追求过高型砂度还会增加生产成本。同时应加强对型砂有效膨润土量的控制。
90.泥分含量对型砂性能有什么影响?不同生产线对型砂含泥量的要求是多少?
型砂中泥分包括:①有效膨润土和有效煤粉。使用高品质膨润土和煤粉时,型砂中这两者总共含量大约10%左右。②加入新砂、煤粉、膨润土时带入的粉尘杂质和已被烧损的死粘土和死煤粉。这些无用的材料称为“灰分”。泥分是吸水物质,在同样紧实率的条件下,泥分高的型砂含水量增多。高密度造型的型砂紧实率除以含水量应当为10%~12%。如果低于此数值,表明型砂含泥量(尤其是灰分)过多。型砂的灰分过多还会使透气性下降,铸件容易产生气孔类缺陷,而且在同样的湿压强度情况下,灰分使型砂韧性、起模性和热湿拉强度明显降低,铸件容易产生砂孔类和夹砂类缺陷。
有的铸造厂只测旧砂的含泥量,实际上最重要的是型砂含泥量。型砂含有泥分多少决定型砂的各种重要性能,然而从旧砂含泥量无法推算出型砂含泥量。在不同铸造工厂中两者相差大约0.5%~3.5%。虽然测定旧砂含泥量所需时间稍微短一些,不过不论测定旧砂或型砂含泥量,几乎均需一天时间才能获得相关数据。
DISA公司推荐一般挤压造型机用型砂含泥量为11%~13%,而较大的2070型造型机用型砂的含泥量为12%~14%,原因是后者砂型较大,要求型砂的强度较高,加入了更多的膨润土。BMD公司要求国内某公司气冲线型砂含泥量10%~13%。B&P公司对另一铸造厂的射压造型线要求型砂含泥量10.5%~13.5%。我国有的工厂使用同样造型线的型砂含泥量在15%以上,可能是由于所使用的原砂、膨润土和煤粉品质不良,旧砂缺乏有效除尘处理造成的。
91.如何改善砂型的起模性能?
为了容易起模和避免砂型棱角破碎和吊砂(砂台)断裂,型砂应当具有一定的韧性,即砂型受到起模所施加的外力后,能否产生适量的变形和不易破碎的性能。选用优质膨润土,延长混砂时间,型砂的相对湿度(紧实率)高,型砂中加入糊精和α淀粉都能提高型砂韧性。型砂中灰分不可过多,因为灰分能够使型砂变脆。但是型砂韧性与流动性是相互矛盾的,通常韧性较高的型砂,流动性明显降低,因此,二者必须兼顾。例如,高密度造型时,希望保证型砂具有良好的流动性,只要起模没有困难,就尽量降低型砂的紧实率。为了测定型砂的韧性,可以在测定型砂试样强度(抗剪、抗压)时,检测试样开始破裂的变形量。也可由型砂的破碎指数表示其韧性。
另一个改善起模性的措施是提高砂型与模样之间的润滑性,降低型砂对模样的粘附力和摩擦阻力。喷涂分型剂是最常用的办法。测定将型砂试样从试样筒顶出的力可以用来衡量是否容易起模。型砂的湿压强度越高,顶出阻力也高。型砂中加有煤粉、α淀粉,试样筒表面涂油,都能降低顶出阻力。研究表明,加有1%α淀粉或糊精的型砂顶出力只有原来的三分之一左右。但是从生产成本考虑,除了个别面砂适量加入一些淀粉材料以外,主要靠控制好型砂干湿程度来保证起模容易。
92.在实际生产中如何通过手捏感来判断型砂的强度和柔韧性?
用手抓一把型砂,并将它捏紧的感觉是多种型砂性能的综合表现:①首先可以从沾手的感觉判断型砂干湿程度,也可与以前型砂检测结果对比估计出含水量多少。②然后,手的五指攥紧使型砂受到压缩,可以感觉出手掌中砂样的紧实变形量。国内某日资铸造厂要求测定型砂的“抗缩值”,即制备标准试样时测出冲击两下与冲击三下之间的试样高度变化,要求控制在(1.30±0.15)mm。抗缩值过低表明试样紧实的前两下冲击过程中试样已接近最终高度,但是手感不够柔和。抗缩值过高表明前两下冲击试样高度与最终高度相差较多,手感柔和,但紧实流动性低,而且浇注时容易“胀砂”。③继续将几只手指向手掌进行少许相对搓揉运动,感觉已经紧实的型砂团是否容易改变形状而不破碎,这代表型砂的可塑性或韧性,也继续感觉出型砂的柔软或扎手。可以用测定型砂试样强度(抗剪、抗压)时试样开始破裂的变形量或用测定破碎指数来表示韧性。④用中指与拇指掐断已经形成长条的型砂试样的中间部位,感觉型砂的强度,大致相当于型砂的劈裂强度。⑤由长条试样上的手指纹路是否清晰来判断型砂的流动性。
93.在一个型砂系统的造型线上同时生产砂铁比悬殊(砂铁比从3到15)的铸件,应如何调控型砂配制,以确保其性能稳定?
首先,两种砂铁比相差悬殊的铸件分别代表两种厚薄和大小不同的铸件,所需要的型砂差别主要在于有效膨润土和煤粉含量不同,以及膨润土与煤粉的补充量不同。砂铁比大的铸件属于薄壁小件,型砂的有效煤粉量即使较低,也能生产出光洁铸件。膨润土和煤粉的烧损较少,因而补充量较低。而砂铁比较小的厚大铸件,就需要更高的有效煤粉量才使铸件表面光洁。膨润土和煤粉的烧损量较大,因而补充量较高。如果同时生产厚薄相差非常大的铸件,对型砂中有效煤粉和有效膨润土含量控制只能迁就厚大件,但是需要密切注意薄铸件表面是否显示出过度光洁和有呛火趋势。在造型浇注计划的安排上,应当有规律交错搭配,即周期性地交替生产,使型砂的组分及性能在允许的范围内轻微波动,而避免长时间单向趋势造成巨大起伏。除了要保持型砂的强度稳定,还应当严密检测和控制型砂的有效煤粉及有效膨润土量,使这两个指标能分别适合厚薄铸件的要求。
94.型砂中煤粉的有效含量在生产球铁件和灰铁件时有何区别?
灰铁件型砂中的有效煤粉量是用来保证铸件不产生表面粘砂缺陷,使铸件表面光洁。具体的有效煤粉量不但取决于煤粉本身的品质好坏,也取决于铸件的厚薄和大小,还要看铸件的清理方法。例如,有的手工造型工厂只用钢丝刷清理铸件表面,要求刷后即露出光滑蓝色表面,则型砂中必须含有较多的有效煤粉。有的工厂具有强力抛丸设备,铸出后局部表面粘附一薄层砂,也会在随后抛丸清理时完全露出铸件的金属表面。这种情况下,有效煤粉量稍低一些也无妨,甚至不希望铸出表面过分光洁,以免产生侵入气孔缺陷。按照一般经验数据,高密度造型型砂的有效煤粉量和机器造型煤粉量,折合优质煤粉或高效煤粉的有效含量(质量分数)分别大约为3.5%~5.5%和4.5%~6.5%。生产球墨铸铁件还要求在浇注时型腔中充满大量还原性气体,可以防止浇入铁液中的镁和硫化镁与型砂水分产生反应性气孔缺陷,要求有效煤粉量取上限。