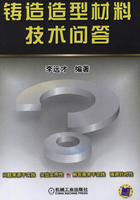
第3章 湿型砂
3.1 湿型砂用主要原材料
61.什么是粘土砂型?粘土砂型的类型和特点是什么?
粘土砂型根据在合型和浇注时的状态不同可分为湿型(湿砂型或潮型,green sand mold)、干型(dry sand mold)和表面烘干型(表干砂型,skin dried mold)。三者之间的主要差别在于:湿型是造好的砂型不经烘干,直接浇入高温金属液体;干型是在合型和浇注前将整个砂型送入窑中烘干;表面烘干砂型只在浇注前对型腔表层用适当方法烘干一定深度(一般5~10mm,大件20mm以上)。
湿型用的湿型砂按造型时情况不同,可分为面砂(facing sand)、背砂(backing sand)和单一砂(units and)等。面砂是指特殊配制的在造型时铺覆在模样表面上构成型腔表面层的型砂;背砂是在模样上覆盖在面砂背后,填充砂箱用的型砂。在砂型浇注时,面砂直接与高温金属液接触,它对铸件质量有重要影响。一般中、小件造型时,往往不分面砂与背砂,而只用一种型砂,称为单一砂。
湿型铸造法的基本特点是砂型(芯)无需烘干,不存在硬化过程。其主要优点是:生产灵活性大,生产率高,生产周期短,便于组织流水线生产,易于实现生产过程的机械化和自动化;材料成本低;节省了烘干设备、燃料、电力及车间生产面积;延长了砂箱使用寿命等。但是,采用湿型铸造,也容易使铸件产生一些铸造缺陷,如夹砂结疤、鼠尾、粘砂、气孔、砂眼、胀砂等。随着铸造技术的发展,以及先进的造型机械和砂处理设备的使用,使型砂紧实均匀,起模平稳,铸型质量得到了很大保证,促进了湿型铸造方法应用范围的扩大。例如汽车、拖拉机、柴油机等工业中,质量在300~500kg以下的薄壁铸铁件,目前均已成功地采用湿型铸造。目前,湿型砂造型也是使用最广泛、最方便的造型方法,大约占所有砂型使用量的60%~70%。
表面烘干型与干型相比,可节省烘炉,节约燃料和电力,缩短生产周期,所以曾在中型和较大型铸铁件的生产中推广过。
干型主要用于重型铸铁件和某些铸钢件。为了防止烘干时铸型开裂,一般以普通粘土为主,有需要时加入少量膨润土。干型主要靠涂料来保证铸件表面品质。其型砂和砂型的品质较易控制,但砂型生产周期长,需要专门的烘干设备,铸件尺寸精度差,因此近年来干型(包括表干型)的粘土砂型已大部分被化学粘结剂砂所取代。
62.什么是粘土?粘土的矿物成分及结晶特征是什么?
粘土是由各种含有铝硅酸盐矿物的岩石经过长期的风化、热液蚀变或沉积变质作用等生成的土状材料,它主要是由细小结晶质的粘土矿物所组成。
粘土是湿型砂和干模砂的主要粘结剂。粘土被水湿润后具有粘结性和可塑性;烘干后硬结,具有干强度,而硬结的粘土加水后又能恢复粘结性和可塑性,因而具有较好的复用性。但如果烘烤温度过高,粘土被烧死或烧枯,就不能再加水恢复塑性。粘土资源丰富,价格低廉,所以应用广泛。
(1)粘土的矿物成分 粘土矿物的种类很多,按晶体结构可分为高岭石组(包括高岭石、珍珠陶土、地开石、埃洛石等)、蒙脱石组(包括蒙脱石、贝得石、绿脱石、皂石等)和伊利石组(包括伊利石、海绿石等)。粘土是由各种含有铝硅酸盐矿物的岩石经过长期的风化、热液蚀变或沉积变质作用等生成的。粘土在沉积过程中,常混杂有一些非粘土矿物,如石英、长石、云母等,以及少量有机物质。只有其中的粘土矿物才是产生粘结能力的基本材料。非粘土矿物和有机杂质一般都不起粘结作用。
粘土与水混合后,其中所含的粘土矿物容易分散为细粒,直径大多数在1~2μm以下。其他矿物的颗粒直径大部分大于1~2μm。铸造上把直径小于20μm的细粒称为“泥分”,泥分中不一定含有粘土矿物。
在铸造行业所采用的粘土分为铸造用粘土和铸造用膨润土两类。膨润土主要是由蒙脱石组矿物组成的,主要用于湿型铸造的型砂粘结剂。铸造用粘土主要含有高岭石或伊利石类矿物,常用做干型砂和修炉、修包材料的粘结剂。
(2)粘土的结晶特征 各种粘土之所以具有不同的性能,其基本原因是粘土矿物的结晶结构不同。通过X射线衍射法的研究,可以得知按照粘土矿物的晶层排列,有两层型、三层型等不同形式。粘土矿物的晶格中都包含着两种基本结构单位:①硅氧四面体晶片:硅氧四面体是由一个Si+等距离地配上4个比它大得多的O2-(或氢氧离子)构成的。每个硅氧四面体中的三个氧位于同一平面,称为底氧。另一个氧带负电荷称为顶氧,是活性氧。在层状结构中,每个四面体的三个底氧分别和相邻的三个底氧四面体共用组成四面体群,在二维平面上排列成六角形的网格,连成无限延伸的整片。②铝氧八面体晶片:由一个铝(或铁、镁)离子居于中心,6个氧或氢氧等距离排列成八面体。八面体之间共棱相连形成八面体片。
63.什么是铸造用粘土?其主要矿物组成和理化性质是什么?
铸造用粘土,又称白泥、甘子土、陶土、瓷土、高岭土等,主要是由高岭石组粘土矿物所组成。杂质的含量对粘土的工艺性能有一定的影响。粘土中SiO2与R2O3的摩尔比对工艺性能也有一定的影响。高纯度的高岭土粘土可用于陶瓷、造纸等行业。铸造上所用的高岭石粘土一般是高岭石与其他粘土类矿物(例如伊利石)的混合物。
高岭石组粘土矿物的一般化学式为Al2O3·2SiO2·2H2 O,其结晶结构为两层型,由一层Si—O四面体和一层Al—(O·OH)八面体构成一个晶体单元。相邻单位晶层之间由氧面与氢氧面成氢键连接。
高岭石组矿物在研磨过程中,晶层边缘的氢氧基上容易出现断裂形成断键,断键处的氢易被其他阳离子所置换,因此高岭石组矿物研磨得越细,粘土颗粒的表面积就越大,断键也越多,粘结力也越好。
高岭石组粘土矿物遇水后,水分子难以侵入晶层之间,粘土颗粒不产生晶间膨胀,因此粘土的吸水率、膨胀率都比较小,湿强度较低,烘干时开裂倾向较小。
高岭石组粘土矿物加热到400~500℃便迅速失去结构水,再升温到750~800℃则完全失去结构水并转变为无水高岭石。粘土矿物中即使尚含有极少量的水也容易重新吸收水分,但若完全失去水分则要再吸收水分就比较困难。粘土矿物的脱水特性对粘土砂型的烘干和型砂的老化度都有直接的影响。
由于高岭石组的粘土矿物具有较小的膨胀率、收缩率和较高的耐火度,所以铸造用粘土主要用做需要烘干的粘土砂型和砂芯的粘结剂。对于较大的铸件所用的干型,选用的铸造用粘土应有较高的干强度和耐火度。
64.铸造用粘土的分级情况及技术指标如何?
根据JB/T 9227—1999《铸造用膨润土和粘土》的规定,铸造用粘土分级情况及技术指标如下:
1)铸造用粘土按耐火度的不同分为两级,见表3-1。
表3-1 铸造用粘土按耐火度分级
2)铸造用粘土按工艺试样湿压强度值分为三级,见表3-2。
表3-2 铸造用粘土按湿压强度值分级
注:混合料配制:标准砂2kg,粘土200g,加水量按紧实率45%控制,干混2min,湿混8min。
3)铸造用粘土按工艺试样干压强度值分为三级,见表3-3。
表3-3 铸造用粘土按干压强度分级
注:混合料配制同表3-2,试样在(180±5)℃保温1h,在干燥器中冷却至室温后进行测定。
4)铸造用粘土的牌号以耐火度等级和强度等级表示。在强度等级中,前者为湿压强度等级,后者为干压强度等级。例如:耐火度高、湿压强度值为30~50kPa、干压强度值大于500kPa的铸造用粘土,其牌号为NG-3-50。
5)技术指标:各种牌号的铸造用粘土,其水分含量(质量分数)应不大于10%,95%以上应通过140筛号铸造用试验筛。
65.什么是膨润土?铸造用膨润土的矿物成分及结晶特征是什么?
膨润土是6000万~1.2亿年前火山灰沉积的产物。铸造用膨润土主要由蒙脱石矿物所组成。蒙脱石是一种SiO2与Al2O3的摩尔比在4左右,并含有少量碱金属和碱土金属的水化硅酸铝,其化学式为Al2O3·4 SiO2·H2O·nH2O。
蒙脱石的结晶结构为三层型,它是由两层Si-O四面体中间夹一层Al-O(OH)八面体构成的晶体单元。所有四面体的尖端都朝向中央的八面体,四面体中的氧与八面体中的氧结合成公共原子层。因为这个原子层均为氧面,仅靠较弱的范德华引力连接,容易破碎成极细的颗粒,遇水后,水分子及其他离子容易进入相邻单位晶层之间,引起蒙脱石晶格沿c轴方向膨胀,由0.96nm膨胀到2.140nm。因此,蒙脱石具有较大的吸水膨胀性、胶体分散性、吸附性、离子交换性和湿态粘结性能等。
晶体结构以及晶格膨胀的特点使蒙脱石比高岭石具有更高的湿强度,其强度受颗粒大小的影响较小。蒙脱石加热至100~200℃,即失去大部分结晶层间所吸附的水分;500~700℃失去结晶水,基本结束脱水作用;加热到800℃以上,晶格破坏,矿物转变为无定形物质;再加热到1100~1200℃,即开始出现高温新相。根据以上几方面的特点,所以膨润土一般主要用做粘土湿砂型的粘结剂。
66.铸造用膨润土的技术指标及分级情况如何?
天然蒙脱石按主要的交换性阳离子种类和相对含量进行分类,主要有钠蒙脱石、钙蒙脱石、镁蒙脱石、锂蒙脱石、氢蒙脱石等。铸造生产中常用的有钙基膨润土、钠基膨润土以及一些混合基膨润土。
根据JB/T 9227—1999《铸造用膨润土和粘土》的规定,铸造用膨润土分类、分级情况及技术指标如下:
1)铸造用膨润土按其主要交换性阳离子分类。以膨润土代号“P”及主要交换性阳离子的化学元素符号来表示。
如某一交换性阳离子量占阳离子交换容量的50%或50%以上时,称其为主要交换性阳离子;如任一交换性阳离子量均占阳离子交换容量的50%以下时,以其中含量相对较多的两种交换性阳离子表示(含量较多的阳离子的符号在前)。
例如:以钠离子为主要交换性阳离子的膨润土以PNa表示,称为钠膨润土;以钙离子与钠离子为主要交换性阳离子的膨润土以PCaNa表示,称为钙钠膨润土。
2)铸造用膨润土按pH值的不同又可分为酸性、碱性两类,分别用S和J表示。
3)铸造用膨润土按工艺试样湿压强度值分为4级,见表3-4。
表3-4 铸造用膨润土按湿压强度值分级
注:混合料配制:标准砂2000g,膨润土100g,干混2 min然后加水40mL再混8min后测定紧实率。当紧实率小于43%时,可加少量水(外加水量可按每毫升水提高紧实率1.5%估算)湿碾2min,再检查紧实率,若紧实率大于47%,将试料过筛1~2次再检查紧实率,紧实率在43%~47%的范围内即可。
4)铸造用膨润土按工艺试样热湿拉强度值分为4级,见表3-5。
表3-5 铸造用膨润土按热湿拉强度值分级
5)铸造用膨润土的牌号按分类、分级代号顺序排列表示。例如湿压强度值30~50kPa、热湿拉强度值为0.5~1.5kPa的酸性钙膨润土,其牌号为PCaS-3-5。
6)技术指标:各种牌号的铸造用膨润土,其吸附亚甲基蓝量每100g土至少应在20g以上;水的质量分数应不大于12.0%,冬季允许不大于15%;其质量的95%以上应通过200号铸造用试验筛。
67.铸造用膨润土有哪些主要性能?其质量如何评定?
铸造膨润土的性能包括物理性能、铸造性能和复用性能等,各自相应的性能指标见表3-6。
表3-6 铸造用膨润土的性能指标
膨润土的质量主要由湿态粘结力、热湿态粘结力以及复用性等性质来评定。
(1)膨润土的湿态粘结力 在湿型砂中,膨润土的主要作用是将松散的砂粒粘结在一起,使砂型具有适当的强度、硬度、韧性。如果铸造厂所使用的膨润土粘结力差,为了使湿型砂具有所要求的性能,就必须加入较多的膨润土。这不仅使生产成本提高,而且增加了型砂的含水量,还会引起铸件产生气孔缺陷。影响膨润土湿态粘结力的因素有多种,其中主要是膨润土的纯度。此外,膨润土磨粉的粗细、分散程度高低、蒙脱石晶体的晶粒大小等因素也有很大影响。
(2)膨润土的热湿态粘结力 在金属液浇入湿型中之后,型砂由于受高温烘烤,石英在573℃发生相变而急剧膨胀;同时砂型表面水分向内迁移产生水分凝聚区,使膨润土的粘结力下降。由于经受不住石英膨胀所产生的横向剪切力和向外凸出的拉力,砂型表面开裂而造成铸件表面夹砂、结疤、鼠尾等缺陷。这时膨润土应当具有的粘结力是一种热态(100℃左右)和过湿态(含水量大约为通常型砂含水量的2~3倍)下的热湿态粘结力。
(3)膨润土的复用性 又称为膨润土的热稳定性或耐用性,是指在砂型中经高温金属液加热的膨润土再次加入水分后,仍然具有粘结力,能够反复配制型砂的性能。不同膨润土的晶体结构破坏的温度和速度有很大差别。如果铸造厂所选用的膨润土复用性差,旧砂回用时必须补充加入较多的新膨润土,这样一方面提高了铸件生产成本,同时又使被烧损的死粘土积累速度加快,型砂含水量增加。
68.如何测定膨润土的湿态粘结力、热湿态粘结力以及复用性?
(1)湿态粘结力 铸造厂型砂实验室最常用的检测膨润土湿态粘结力方法有两种:型砂工艺试样湿强度法和吸蓝量法。
1)型砂工艺试样湿强度法:膨润土能使砂型具有一定的强度,因此,检测湿型砂试样湿态抗压强度成为判断膨润土湿态粘结力最直接的方法。具体试验步骤见相关资料。
2)膨润土的吸蓝量法:膨润土的纯度(即蒙脱石含量)与其粘结能力有极为密切的关系。一般情况下,膨润土的纯度越高,其粘结力也越大。在专门的研究单位中可以用X射线衍射等方法比较准确地测定出膨润土中蒙脱石含量。然而这不但需要特殊的仪器设备,而且也要专门的检测技术。在铸造厂的型砂实验室中可以采用测定膨润土的吸蓝量的办法大体推算出其纯度。
膨润土中的蒙脱石比其他粘土矿物和膨润土中的石英等杂质吸附亚甲基蓝(C16H18N3 SCl·3H2O,相对分子质量为373.88)或其他色素的能力要强烈得多,因此用吸蓝量可以检验膨润土的纯净程度,也可以用来检验型砂中有效膨润土含量。其测定方法分为比色法和滴定法两种。比色法的原理是称取一定质量的试样与过量的亚甲基蓝溶液混合,使之充分吸附;然后用比色计测出残余液中剩余亚甲基蓝量,即可计算出试样的吸蓝量。此法由于操作较复杂,还需要使用比色计等仪器,目前使用不多。滴定法不需要任何特殊仪器设备,操作又较简单,更适合铸造厂的型砂实验室使用。
用吸蓝量仅仅能够大致推算膨润土的湿态粘结力大小。为了更准确地检测出膨润土的湿态粘结力,最好直接采用测定工艺试样湿态强度的方法。
(2)热湿态粘结力 铸造厂评价膨润土热湿态粘结力的方法有热湿拉强度法和膨润土的膨润性能法两种。
1)热湿拉强度法:不论是天然的还是人工活化的膨润土,其所含交换性钠、钾离子越多,型砂的热湿拉强度就越高,抗夹砂能力就越强。此外,膨润土的纯度也影响其热湿拉强度。热湿拉强度的具体试验方法见相关资料。
在实际铸造生产中并不是都要求使用钠基膨润土或者达到极限程度的活化膨润土配制型砂,因为使用这样的膨润土在混砂时会产生团块,而且型砂的流动性、落砂性较差。国外的汽车铸件通常选用钠基和钙基两种膨润土混合的膨润土或不完全活化膨润土,这样不但可以避免上述缺点,还可以降低生产成本,而且对于防止夹砂类缺陷已经足够。
如铸造厂的型砂实验室没有热湿拉强度测试仪,可以采用三倍于通常型砂水分含量下的常温抗拉强度试验来大致估算出膨润土的热湿拉强度。
2)膨润土的膨润性能法:膨润土在水中的膨胀性能与膨润土吸附阳离子的种类和数量密切相关。各种交换性阳离子的含量可采用原子吸收光谱分析技术来精确测定。在铸造厂的型砂实验室中,可以利用测量膨润土在水中的膨胀量估算出膨润土中钠、钾离子含量及这两种离子在总阳离子交换量中所占比例。试验时将膨润土在水中均匀分散成悬浮液,静置一定时间后,观察在容器的底部形成沉淀物的多少,通常以膨润值、胶质价或膨胀倍数表示,具体试验方法见相关资料。
(3)膨润土复用性 铸造厂检验膨润土复用性的方法也可分为工艺试样法和吸蓝量法两种。
1)工艺试样法:将烘干后的膨润土在200℃、300℃、400℃、500℃、600℃几种温度下焙烧后,各称取100g,与2000g标准砂按紧实率45%±2%加水混砂,测定工艺试样的湿压强度,绘出湿压强度和膨润土焙烧温度的关系曲线,由粘结力的下降趋势判断膨润土的复用性能好坏。
2)吸蓝量法:将烘干后的膨润土约0.5g盛在磁舟内,置入管式炉中先缓慢加热,然后分别在200℃、300℃、400℃保温焙烧1h。冷却后称取0.2g,测定其吸蓝量,并绘出焙烧温度与吸蓝量变化曲线。由吸蓝量的下降趋势即可判断膨润土的复用性。
69.膨润土的人工钠化的实质是什么?其钠化工艺有哪些?
有些湿型铸造生产要求型砂具有较高的抗夹砂能力和较高的复用性能。这就希望使用钠基膨润土或含有一定数量钠离子的钠钙基膨润土。我国天然钙基膨润土资源丰富,而且开采供应方便。相比之下,天然钠基膨润土的资源较少。为了适合铸造厂对钠基膨润土的需要,可用碳酸钠等钠化剂对钙基膨润土进行处理,使原来所含的钙离子部分或绝大部分被钠离子置换,称为膨润土的“钠化处理”或“活化处理”。这一过程的化学反应机理简单示意如下:
Ca2+蒙脱石+Na2CO3→Na+蒙脱石+CaCO3
活化膨润土时的碳酸钠加入量通常为膨润土质量的3%~5%。膨润土的钠化反应能否充分进行的关键在于钠化的工艺。我国有些铸造厂在混砂时向砂和膨润土中加入粉状或碳酸钠的水溶液。这种工艺处理后的钠离子不能充分地被蒙脱石晶体吸收和与钙离子相互置换,不但需要多加碳酸钠,而且还可能引起铸件表面粘砂缺陷。较好的活化工艺有湿法和干法两种。
1)湿法工艺是将膨润土和水配成泥浆后加入碳酸钠,经强力搅拌而成。这种方法适用于配制铸型涂料。如果用于湿型砂,需经过脱水、干燥、破碎、磨粉等复杂工序,所以难以在铸造厂应用,只能在膨润土加工厂进行。
2)干法工艺是由膨润土加工厂将开采出的膨润土破碎成小颗粒,与碳酸钠混合成具有一定湿度的混合料。有时还要添加少量增效助剂,加入挤压机(如轮碾机、双螺旋挤压机、对辊挤压机等)中反复挤压,然后存放数日老化,从而完成钠化反应过程,再经低温烘干、破碎制粉,即可得钠化膨润土产品。挤压是膨润土钠化工艺的关键,因为强力挤压作用可使钙基膨润土的团块产生相对运动而分离,增加与钠离子的接触,而使交换速度加快。挤压摩擦可产生大量的热,加快了离子运动速度和运动范围。在较大的机械力作用下,蒙脱石彼此连接的化学键遭到破坏,也有利于吸附带有相反电荷的钠离子。这些方法都有助于钠化反应的充分进行。
70.如何选用铸造用膨润土?
膨润土的性能指标及其稳定性取决于其矿源及原矿储备量、供应商的研发能力、质量保证系统、生产设备和检验设备,以及制造商的技术服务能力等方面的因素。
研究结果表明,蒙脱石颗粒表面所吸附的水,最里层呈有规则的排列,其密度及粘滞性普通液态水大,称为非液态水。非液态水的性质和层数对膨润土的工艺性能有重要的影响。蒙脱石颗粒表面所吸附的水的特性,与晶层间和八面体中阳离子的种类及交换容量有很大关系。钠蒙脱石颗粒表面非液态水有3个分子层,比钙蒙脱石略小,但从非液态水到液态水之间有一个逐渐转变的过渡层,比钙蒙脱石大6~7倍,因此钠基膨润土具有较好的水分适应性,型砂中水的加入量可降低,而且在水分较高时仍能保持较好的强度,反映在工艺性能上即具有较高的热湿拉强度和抗夹砂能力,更适于在夹砂倾向较大的砂型上使用。钠基膨润土与钙基膨润土工艺性能见表3-7。
表3-7 钠基(天然钠基及活化)膨润土与钙基膨润土工艺性能比较
然而,钙基膨润土型砂具有易混碾、流动性好、落砂容易、旧砂中团块少等优点,而且在我国钙土产地分布较广,售价低廉。因此,不应理解为只有钠基膨润土才是高质量膨润土。对于生产中小铸件的工厂而言,可能铸件本来就不易产生夹砂结疤缺陷,尤其是湿型铸铁型砂中含有煤粉等附加物和使用SiO2较低的原砂,在能防止砂结疤的情况下,使用钙基膨润土通常可以取得良好效果。
铸造厂应当根据本厂生产铸件的特点确定使用膨润土的质量级别。如果所生产的湿型铸件比较重要,要应用湿态粘结力较高或蒙脱石含量较高的优质膨润土。这样可以减少膨润土的加入量,降低型砂的含泥量,减少型砂的吸水物质。其结果是型砂的含水量低,铸件不易生成气孔类缺陷。
如果所生产的铸件具有较大的平面,或者砂型的表面在浇注时受金属液的高温烘烤而又不能立即被金属液覆盖,就要求型砂具有足够高的热湿态粘结强度,否则铸件会产生夹砂类缺陷。为了防止铸件产生夹砂类缺陷和提高膨润土的复用性,应当使用活化膨润土,或者用钠基与钙基混合膨润土。膨润土的活化程度或钠、钙基膨润土的混合比例应根据铸件的结构特点以及生产中造型和浇注的具体条件而定。
71.国内外主要铸造用膨润土的资源及产地情况如何?
全世界现已探明的膨润土总储量约25亿t,其中美国、中国和俄罗斯的储量最多,约占3/4,其次是西班牙、希腊和德国。全世界膨润土的矿藏中,钙基膨润土约占70%~80%,钠基膨润土的储量不多,主要在美国西部的怀俄明州及其周边地区。目前,全世界膨润土年产量约1000万t,其中美国约500万~600万t,中国250万~300万t,日本约60万t,西班牙、希腊和德国都在50万t左右。
我国膨润土矿藏分布很广,但主要是钙基膨润土,钠基膨润土目前尚未发现有开采价值的矿点,品位也不是很好。
我国膨润土的主要产区是辽宁建平、凌源、黑山一带,不仅储量丰富,而且出产的钙基膨润土品质很好,已成为世界各国关注的重点。许多国际知名企业,如世界最大的膨润土生产、供应厂商美国胶体公司(American Colloid Company),以生产人工活化钠基膨润土著称的德国南化公司,希腊的Silver&Baryte公司等,都已在这一带建立独资或合资生产企业。
浙江的临安、余杭一带,安徽的黄山、铜陵、六安一带,河南信阳一带也有比较丰富的矿藏。
此外,吉林、河北、山东、江苏、湖北、福建、广西、四川及新疆等省(区)也都有膨润土产出。
由于国产膨润土中钙基膨润上占90%以上,为了提高粘土湿型砂的质量,目前铸造行业中所用的膨润土,除少数外资企业、合资企业自美国进口少量天然钠基膨润土外,大都是经活化处理的人工钠基膨润土。
在铸造行业快速发展的推动下,我国很重视膨润土资源的开发,目前这一产业已具有可观的规模,除产量大幅度增长外,加工、处理的工艺也不断改善,产品质量已达国际水平。
72.铸造用煤粉的主要原料煤是什么?其在湿型砂中起什么作用?
煤按煤化程度的不同可分为褐煤、烟煤、无烟煤。铸造用煤粉首先应属烟煤类。烟煤按煤化程度又可细分为长焰煤、气煤、肥煤、焦煤、瘦煤和贫煤。根据煤的特性,有较高挥发分和适宜的焦渣特征的烟煤是焦煤和肥煤。铸造用煤粉应以肥煤和焦煤为原料,经过精洗、磨制而成。
湿型用煤粉是以烟煤为原料经粉碎制成的产品,外观为黑色或黑褐色细粉。煤粉的作用是利用煤在高温的分解及分解后包覆在砂粒表面的碳膜以防止铸铁件产生粘砂和夹砂,同时也起到提高型砂溃散性的作用,因此煤粉中挥发物的含量是质量分级的主要依据。煤的挥发物包括气体和液体两部分,因此在控制湿型用煤粉的质量方面,除了挥发物的含量外,对煤粉的胶质层厚度及焦渣特性也应加以控制。
目前普遍认为适合湿型砂应用的优质煤粉在浇注过程中的作用如下:
1)在铁液的高温作用下,煤粉产生大量还原性气体,防止铁液被氧化,并可使铁液表面的氧化铁还原,减小金属氧化物和型砂进行化学反应的可能性。型腔中还原性气体主要来自煤粉热解生成的挥发分,也包括碳与型砂中水分在高温下反应生成的氢气。
2)煤粉受热后开始软化,具有可塑性。如果由开始软化至固化之间温度范围比较宽和时间比较长,则可缓冲石英颗粒在该温度区间受热而形成的膨胀应力,从而可以减少因砂型受热膨胀而产生的铸件夹砂缺陷。
3)煤粉受热后产生气、液、固三相的胶质体,胶质体的体积膨胀可部分地堵塞砂型表面砂粒间的孔隙,使铁液不易渗入。国家标准GB/T 212—2008将煤的“焦渣特征”分为8级,能够区分煤粉受热时是否生成起粘结作用的液相,以及是否发生膨胀。
4)煤粉在受热时产生的碳氢化物(主要为芳烃类)的挥发分在650~1000℃高温下,于还原性气氛中发生气相热解,而在金属液和铸型的界面上析出一层带有光泽的微细结晶炭,称为“光亮炭”或“光泽炭”。这层光亮炭使砂型不受铁液润湿和难以向砂粒孔隙中渗透,从而得到表面光洁的铸件。
73.湿型用煤粉的主要理化指标有哪些?其对防粘砂性能有何影响?
煤粉的主要理化指标如下:
(1)光亮碳 煤在干馏过程中产生的气相产物在高温深度分解过程中,产生热解碳的显微结晶,沉积在灼热的物体上,称为光亮碳。光亮碳含量高的煤粉受热析出的光亮碳层使砂型不被铁液润湿并难以向砂粒孔隙中渗透,从而得到表面光洁的铸件。光亮碳理论目前已被国内外铸造工作者普遍接受。
(2)挥发分JB/T 9222—2008规定煤粉中除水以外的挥发物所占的质量分数即为煤粉的挥发分。煤粉应具有足够多的挥发分,这是在铸型内形成还原性气氛,以及产生光亮碳所必需的。通常认为挥发分不应少于28%,但是也并非越高越好,更重要的是应当具有良好的形成胶质体和分解出光亮碳的能力。长焰煤和气煤的挥发分产率较高,在36%以上,甚至能达到40%。受热分解后形成很多对热不稳定的低沸点液体产物,很快又受热分解成气态产物逸出,胶质体的温度间隔小,滞留时间短,不能有效堵塞砂粒间的孔隙,而且低沸点挥发分不利于产生光亮碳层,所以不适合用做湿型砂的抗粘砂附加物。
(3)焦渣特征 焦渣特征反映煤在干馏过程中软化、熔融形成胶质体,并固化粘结成焦的特性。焦渣特征按GB/T 212—2008划分为8级:
1级:粉状,全部是粉末,没有相互粘着的颗粒。
2级:粘着,用手指轻碰即成粉末或基本上是粉末,其中较大的团块轻轻一碰即成粉末。
3级:弱粘结,用手指轻压即成小块。
4级:不熔融粘结,以手指用力压才裂成小块,焦渣上表面无光泽,下表面稍有银白色光泽。
5级:不膨胀熔融粘结,焦渣形成扁平的块,煤粒的界线不易分清,焦渣上表面有明显银白色金属光泽,下表面银白色光泽更明显。
6级:微膨胀熔融粘结,用手指压不碎,焦渣的上、下表面均有银白色金属光泽,但焦渣表面具有较小的膨胀泡(或小气泡)。
7级:膨胀熔融粘结,焦渣上、下表面有银白色金属光泽,明显膨胀,但高度不超过15mm。
8级:强膨胀熔融粘结,焦渣上、下表面有银白色金属光泽,焦渣高度大于15mm。
根据煤粉的防止铸件粘砂的焦炭膜理论和氢气还原理论可知,铸造用煤粉在铁液高温作用下应有较多的胶质体,特别是高沸点液相产物,且胶质体应具膨胀性,以堵塞砂粒间的孔隙,使铁液不易渗入。上述焦渣特征中,6、7、8三级具有膨胀性,其中6、7两级适于铸造。应避免使用强膨胀熔融粘结的8级,以避免将砂粒粘结成大的复合颗粒而影响型砂的复用性。焦渣特征为1~4级的煤粉,即使挥发分较多,由于胶质体量过低,其抗粘砂效果不良。
测定煤粉发气性后,不锈钢舟中残留物的状态与测定煤粉挥发分后瓷舟中的残留物焦渣特征非常相似。因为两者的试验条件都是煤粉在干馏条件下熔融、析气、固化的结果,因此,用发气性测定仪也能够完成焦渣特征的测定。
(4)粒度JB/T 9222—2008《湿型铸造用煤粉》规定煤粉的粒度应95%以上通过0.106mm(140目筛)的筛孔。许多企业按此标准制订企业标准。但欧美各国所用煤粉的粒度比我国粗,而且认为根据铸件的大小和厚薄不同,对粒度应有不同要求。煤粉粒度粗些的优点是对环境污染小,较大铸件的凝固时间长,粗粒煤粉可以保持较长时间发气,而且有助于改善型砂的透气性。浇注时细粒煤粉会立即燃烧掉而不能持久发挥作用。但是煤粉的粒度也不可太粗,否则型砂变脆,修型困难,靠近浇口处易被冲刷,铸件表面粗糙。重要的是不可有大于1mm的颗粒,不然铸件局部表面会出现痘疤缺陷或气孔缺陷。要求铸件表面光洁的小铸件则选用较细的煤粉,原则是煤粉的粒度应比原砂稍细些。高紧实度造型(如挤压造型、多触头高压造型、气冲造型)不可用极细煤粉,以免因透气性下降过多而使铸件产生气孔缺陷。
此外,煤粉中的灰分、水分、硫分,要求其含量越低越好。
根据JB/T 9222—2008《湿型铸造用煤粉》的规定,湿型用煤粉质量分为3级(见表3-8)。
表3-8 湿型用煤粉的技术指标(质量分数,%)
74.在湿型中添加煤粉的主要问题是什么?
煤粉虽然是一种很好的型砂附加物,但随着人们对煤粉作用机理认识的深化和环境意识的增强,煤粉的各种缺陷逐渐显现出来。
1)由于煤粉的原料——工业用煤在我国是一种很重要的能源材料,而且用于加工铸造用煤粉的原料煤必须是优质煤。随着能源危机的日益严重,如果在湿型砂中继续使用煤粉,将面临着被截流的危险。
2)由于煤粉的光亮碳生成率较低,对于厚壁铸件,当煤粉加入量不足时,起不到防粘砂作用,而当煤粉的加入量较大时,会大大降低型砂的透气性,而且煤粉的焦化是吸热反应,会使铁水冷却得更快,不易控制灰铁的冷却工艺。
3)煤粉在燃烧后将残留下一些低熔点的灰分残渣,这些灰分与死粘土一起包覆在砂粒表面,造成“鱼卵石化”,使型砂的耐火度降低,增加了型砂次生机械粘砂的倾向,而且型砂中灰分的大量积累会导致型砂透气性的下降,含水量增加。煤粉砂在循环使用时,灰分含量增加很快,需要补加大量的新砂才能保证型砂的其他性能不降低,这又使得铸件的成本增加。
4)由于煤粉是黑色粉状物,所以从加工、运输、贮存直到整个生产过程都是尘埃飞扬,严重恶化了环境卫生,使周围的人们深受其害。另外,煤粉在浇注时发出难闻的气味,冒出大量浓烟,这种烟气中含有有毒物一氧化碳和致癌物3,4-苯并花,而且煤粉烟雾的累积物以及煤粉在缺氧状态下燃烧生成的煤焦油也属于致癌物。
75.什么是煤粉的代用品?主要有哪些?
煤粉代用品是指在湿型砂中可以完全替代或部分替代煤粉的材料,在混砂时与煤粉共同加入,相互配合使用。作为湿型铸造的煤粉代用品种类繁多,分类介绍如下:
(1)油类 主要是石油炼制过程中的油状产品或副产品,这些产品的光亮碳形成能力约为40%。如果油类的粘度不高,可以在混砂时直接加入。例如用废机油代替部分煤粉,面砂中加入煤粉的质量分数为2%~3%,废机油的质量分数为0.6%~1%,使铸件的表面粘砂有所改善,提高起模性,气孔类缺陷下降。但是废机油的来源有限,不适合大量生产中应用,常用渣油代替。
(2)合成树脂及聚合物 可以是粉状的聚苯乙烯、聚丙烯酸胺、聚乙烯、聚丙烯、聚酯等。其中常以聚苯乙烯作为煤粉代用品。聚苯乙烯的光亮碳形成能力高达80%~85%,挥发分接近100%,平均粒度0.15mm,型砂中加入量仅为煤粉质量的1/9~1/6。由煤粉更换成聚苯乙烯粉以后,型砂的需水量可降低20%,透气性提高,气孔缺陷减少;型砂紧实流动性提高,砂型紧实度增加,铸件尺寸更精确;车间空气中CO含量降低,浇注时产生的苯乙烯单体含量未超过允许含量。用煤粉时,车间粉尘中煤粉残留物约为50%,而聚苯乙烯不存在这种残留物,对环境和工作场地的污染最小。但是在各种煤粉代用品中聚苯乙烯的价格最贵。
(3)植物类产品 有粉状淀粉(普通淀粉、淀粉和面粉)、植物树脂、植物纤维粉等材料。虽然淀粉并不形成光亮碳,但能有效地防止铸件粘砂。例如在手工造型的湿型砂中加入质量分数为1%的面粉可以大大改善铸铁件表面质量。我国有两家静压造型的铸造工厂,按照日本汽车铸造工厂的技术,在灰铸铁型砂中不加煤粉,改为加入α淀粉。其中一家工厂的型砂中泥的质量分数降为8%~9%、紧实率为35%~40%时,型砂中水的质量分数只有2.4%~2.7%,透气性高达200~240。另一家工厂型砂中泥的质量分数降为7%~11%,型砂中水的质量分数为2.7%~3.2%,透气性为160~200。由于型砂中不加煤粉就可以减少型砂的有效膨润土含量,并使含水量降低。不加煤粉还可以使型砂的流动性好、起模容易、对环境污染小。但在较大规模铸造生产中,使用淀粉完全替代煤粉会使铸件生产成本提高,因此只在混制面砂时加入淀粉,也可以按一定比例同时加入淀粉和煤粉,以降低淀粉的消耗。
市场上还有多种“抗粘砂添加剂”、“光亮剂”、“湿型覆膜剂”等商品销售。但出于商业目的,都不曾明确说明产品的有效成分,也给不出与铸件质量有关的检验指标(如光亮碳形成能力、焦渣特征、灰分、挥发分等)。建议铸造厂在选用任何煤粉代用品之前,应该持慎重态度,一定先进行试验,例如用同样铁液一次浇出四块阶梯试块进行比较,或是先用该产品小规模使用一段时间(如1年),再根据铸件质量和型砂性能的变化决定是否继续长期扩大应用该种产品。
76.在湿型中,所谓复合添加剂是指哪些材料?其有何作用?
在湿型中,通常所说的复合添加剂是指增效煤粉、膨润土/有机物复合添加剂等。
(1)增效煤粉(合成煤粉、高光亮碳煤粉、高效煤粉)从20世纪70年代起,欧洲煤粉供应厂商考虑到天然煤粉的不足,研制成“增效煤粉”供应铸造厂使用。采用的商品名称为“合成煤粉”,实际上是煤粉与一定比例沥青的混合物。典型的配比(质量比)是煤粉80~60,沥青20~40。配比中的沥青过去曾用煤焦油沥青,现已改用特制的石油沥青。增效煤粉的两种成分可以取长补短,与天然煤粉相比,增效煤粉的挥发分和光亮碳形成能力较强,软化区间加宽,灰分和硫分降低,加入量下降,浇注时烟气减少。增效煤粉的光亮碳形成能力为12%~20%,在型砂中的加入量大约为天然煤粉的一半。国产增效煤粉有两种牌号,见表3-9。
表3-9 国产增效煤粉牌号
(2)膨润土/有机物复合添加剂 在机械化大批量生产的铸造厂中,各造型线的铸件种类单一,而且都有独自的砂处理工步,混砂时各种原材料的配比也是固定的。因此,供应厂商可以将各种附加物(包括煤粉、膨润土、淀粉和其他材料)按比例预先混合后向铸造厂销售。这样可以简化材料的贮存,又可防止煤粉自燃。用户在混砂加料时,只加入一种物料,使生产控制更加方便。
将膨润土与有机物进行混配制成砂型的复合添加剂在美国和欧洲的铸造企业已广泛应用。美国每年的这种添加剂的用量多达80万t,占膨润土市场的较大份额,混配的有机物多达十来种,一般由两种膨润土和2~3种有机物混配而成。表3-10是美国某公司常用的有机物添加剂的配方。
表3-10 美国某公司常用的有机物添加剂的配方
77.如何选购煤粉及复合添加剂?
煤粉是我国铸铁厂湿型应用最为普遍的附加物。应用的关键是煤粉的质量及用量。长期使用劣质煤粉不但不能防止粘砂和改善铸件光洁程度,而且还会给铸造生产带来灾难性后果。劣质煤粉使型砂的性能变脆,湿压强度虽高但湿剪切强度和湿拉强度降低,起模性能变差,型砂含泥量提高,含水量居高不下,透气性下降。由于煤粉的质量低劣,不得不增大加入量,又导致不得不多加膨润土,使型砂的含水量增加,从而使铸件气孔、砂孔缺陷猛增。因此,对于生产要求表面光洁、无气孔和砂孔缺陷的重要铸件,一定要选用质量好的煤粉或增效煤粉。
煤粉的适宜加入量取决于多种因素,如铸件壁厚、浇注温度、浇注速度、铁液压头、造型方法、型砂透气性、砂型硬度、铸件清理方法等,必须根据实际使用效果调整煤粉的加入量。
78.在湿型砂中添加重油有何作用?其主要性质是什么?
重油也称燃料油,有石油工业产物和煤焦油工业产物两种。铸造中常用的是石油工业在提取汽油、煤油和柴油后的塔底油。重油仍可进一步减压分馏,所得塔底油为渣油。重油和适当稀释的渣油可用做铸造型砂的添加材料,对防止铸件粘砂有良好作用。
重油的光亮碳析出量可达(质量分数)20%左右,为煤粉的1~6倍。湿型砂中加入适量的重油不但可以减少煤粉的加入量,还可减少型砂中水的加入量,使型砂具有更好的造型性能。
重油或渣油的粘度过大时可用柴油适当稀释,渣油除稀释后作抗粘砂材料外还可作砂芯粘结剂。重油(渣油)乳状液配方及性能见表3-11。
表3-11 重油(渣油)乳状液的配方及性能
① 钙基膨润土,若用钠基膨润土可以不加碳酸钠。