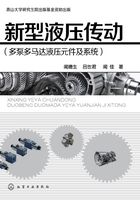
第二章 新型柱塞泵及马达
第一节 开路式轴向柱塞泵原理
随着工业的不断发展和液压传动的广泛应用,泵的类型也层出不穷,柱塞泵也在不断地改革和创新。到目前为止,在各种容积式泵中,柱塞泵是实现高压、高速化比较理想的结构之一,有必要认真研究一下。本章从分析闭式泵入手,提出了一系列新型的开式柱塞泵配流结构。
一、闭路式泵各种配流方式的比较
目前广泛应用的柱塞泵在配流方式上大体可分为轴配流、阀配流、端面配流三种。首先说明一下定义,我们把柱塞没有形成通路的柱塞泵叫闭路式柱塞泵,把柱塞形成通路的柱塞泵叫开路式柱塞泵。
下面分别对闭路式泵的三种配流方式进行讨论。
1.阀配流柱塞泵
图2-1是阀配流泵的几种形式。其配流原理为:由进、出油阀、缸体、柱塞组成周期性变化的控制腔室;由进、出油阀控制泵的吸压油过程。这种泵是最早的液压泵之一。优点是易获得高压,故一般超高压泵采用阀配流的较多。这种配流泵密封性好,结构简单,维修方便,抗污染性好,使用寿命长。缺点是:变量困难,不能双向和作为马达使用;自吸性能差,低压吸油阀只适用于较低转速(即低压阀只适应低频率)。

图2-1 阀配流泵的几种形式
2.轴配流柱塞泵
图2-2所示为轴配流柱塞泵简图,这种配流方式柱塞泵曾在液压传动中广泛采用。一般径向柱塞泵采用轴配流的较多。简单地说,这种泵的工作原理是:由配流轴、缸体、柱塞组成周期性变化的控制腔室,靠配流轴控制泵的吸压油过程。优点是:易于双向变量输出,可作马达用于闭式传动。

图2-2 轴配流柱塞泵简图
缺点是:结构复杂,体积大,重量大,对污染不太敏感,制造工艺复杂,成本高,压力低,效率低,磨损后间隙不易补偿,制造精度要求较高等。
3.端面配流柱塞泵
表2-1所示为端面配流柱塞泵结构类型。其原理为:由端面上直立配流盘、缸体、柱塞组成周期性变化的控制腔室;由配流盘控制泵的吸压油过程,达到输出高压液体之目的。
表2-1 端面配流柱塞泵结构类型

这种柱塞泵应用很广,优点是:结构简单,体积小,重量轻,易于达到高压、高速及实现变量,可作马达使用,制造简单,成本低,维修方便。缺点是不能自冷却、自润滑。
综上所述,这几种配流方式都是单一地应用于一种柱塞泵中,由此造成了多输出困难、多级串联困难等问题。
二、联合配流开路式泵原理及其组成
联合配流开路式轴向柱塞泵是综合了以前所述三种配流方式的优点而形成的一种新型轴向柱塞泵。它是高压侧采用阀配流,低压侧采用轴配流和端面配流的联合配流方式。这样既保持了阀配流方式密封性好、压力高、效率高、抗污染性能好等优点,又克服了完全采用阀配流方式低压配流阀适应频率低的不足,同时吸收了轴配流和端面配流的一部分优点。这几种配流方式在联合配流方案中是通过滑靴和柱塞使它们有机地结合起来的。
1.工作原理及组成
图2-3所示为联合配流开路式轴向柱塞泵结构简图。该泵为轴与配流盘一起转动的轴向柱塞泵,泵体2内轴向分布着柱塞缸体,缸体内装有配流阀1和柱塞4。这种泵的柱塞与闭路式柱塞泵中的柱塞的不同之处在于其中心有通孔,低压油从这里进入控制腔室,柱塞内装有回程弹簧3(这个回程弹簧可以不装,而用其他方式回程,这里主要是为了较简单地说明原理而引进的)。在吸油时靠这个回程弹簧的弹簧力使柱塞和滑靴紧压在倾斜的配流盘上。柱塞的球头部位装有中心开了吸油口的滑靴5,泵体内装有与转动轴固定在一起的配流盘6,这是一个不对称的配流盘,这块配流盘一侧开有吸油槽,一侧不开吸油槽。

图2-3 联合配流开路式柱塞泵结构简图
1—配流阀;2—泵体;3—回程弹簧;4—柱塞;5—滑靴;6—斜盘
当主转动轴带动与轴固定在一起的配流盘转动时,由于配流盘是倾斜放置的,且泵体又固定,所以柱塞就必然在缸体内做往复的直线运动。柱塞向外伸长时正好是处在开有吸油窗口的斜盘这一侧,这样低压油将从斜盘上开的配流窗口通过滑靴进入柱塞腔内。
当柱塞向内被压缩时,正好处于无配流窗口一侧,由于斜盘上没有开配流口,故由斜盘表面将滑靴的底孔堵死,从而形成一个由阀、柱塞、滑靴、配流盘组成的密封腔室。随着轴的转动,这个密封的腔室中体积将逐渐减小,压力随之升高。当压力升高到阀的开启压力时,高压配流阀打开,将高压油输出。轴不断地转动,高压油就源源不断地输出,这就是联合配流开路式轴向柱塞泵的工作原理。图2-4所示为联合配流开路式径向柱塞泵原理简图。该泵为缸体固定、偏心轴转动的径向柱塞泵,在泵壳上沿径向均布着几个如图所示的固定缸体,缸体内装有柱塞组和单向阀。吸油时,液压油将通过转轴中心进入配流槽,再从柱塞孔中心孔进入缸体内。压油时,由偏心轴配油槽处将滑靴底孔堵死,液压油被密封在由缸体、柱塞组、偏心轴、单向阀组成的空间中,随着偏心轴的转动,液压油压力升高,当压力高于单向阀的压力时,泵输出液压油,这是径向开路式泵的工作原理。

图2-4 联合配流开路式径向柱塞泵结构
1—偏心转轴;2—滑靴;3—柱塞;4—缸体;5—回程弹簧;6—单向阀
这种原理还可用于制成如图2-5所示的变量型泵。当图中F处克服外力时,弹簧7的力变心(即改变),达到变量的目的。

图2-5 变量型径向联合配油开路式柱塞泵原理
1,7—回程弹簧;2,10—滑块;3—泵壳;4—外环;5—转子;6—单向阀;8—柱塞;9—滑靴
简而言之,其原理为由阀、柱塞、滑靴、配流盘(偏心轴)组成周期性变化的控制腔室,由阀和配流盘(偏心轴)同时控制泵的吸、压油过程,达到输出高压液体的目的。
2.多输出的办法
若在以轴心为圆心的某个半径的圆上布置这样的柱塞(x=1,2,3,…),而对不同半径,又可以安排不同分布圆(z=1,2,3,…),则组成一个由x乘以z个柱塞组成的泵,以xz表示。如将其中任意几个组合起来,就可以组成不同定量的多输出泵。由于其组合的形式多种多样,这里就不再详述,但要掌握一条原则,即组合后的流量波动性应最小(因为同样几个柱塞的组合,由于柱塞的位置不同,所以组合起来的波动性就不同,这一点千万注意,关于其波动性问题将会在下一章讨论)。由于每一个柱塞的排量是一定的,所以称为联合配流开路式多输出定排量轴向柱塞泵。
为了克服轴向不平衡力,我们可以采用如图2-6所示的对顶开式泵,即在配流盘的另一侧再加上一个同样的由xz个柱塞组成的泵,让两个泵的柱塞位置相对应,这样就可克服轴向力的不平衡,于是就组成了一个由2xz个柱塞组成的泵了。它也可以由若干个柱塞组成多个输出,由于单向阀的作用,这若干个输出(即2m个输出)是互不相干、互不影响的。

图2-6 轴向力平衡式多输出轴向柱塞泵
如图2-6所示,为了使轴向柱塞泵的轴向力平衡而放置xz个柱塞组成的右半部分泵,是与传动轴无关的,若将现有闭路式柱塞泵的变量方式应用到此泵上,就可以很方便地得到一个变量的多输出泵,这是xz个柱塞的同步变量,若组成m个输出,则也是同步变量的;若将这xz个柱塞组成一个输出,则就成为联合配流开路式变量单输出泵。若再将左半部分加上,就是多输出定量泵与单输出变量泵的组合,这样可以有多种组合,这里就不再详述。同样道理径向联合配油开路式柱塞泵不但可在同一个平面径向均布n个同样缸体,而且可布置m个平面,也是n×m个柱塞组合的柱塞泵,也可以有多种组合。
3.联合配流开路式泵自冷却方法
联合配流开路式轴向柱塞泵不但可以组合成各种不同形式的多输出泵,而且还可以实现自冷却和自润滑。图2-7所示为联合配流开路式轴向柱塞泵的自冷却简图(液流流动如箭头所示)。液压油不但可以由斜盘的一侧进入柱塞腔内,而且可以由斜盘的另一侧经过滑靴之间的间隙进入滑靴的底孔处,从而也就进入柱塞腔内。这部分油将对滑靴和斜盘这对摩擦副起自冷却和自润滑作用,也就是说,由于这部分液压油的流动而将热量带走,使摩擦副的温度下降,润滑性加强。这部分液压油流量的大小将直接影响泵的自冷却和自润滑性能的好坏。若将进油口改放到具有滑靴的一侧,则可以使整个泵的流量全部参加对泵中摩擦冷却。另外,柱塞位于高压侧时将有一定的泄漏(占总流量的2%~3%),这部分油液可以直接通过泵内流道进入低压侧的柱塞腔内。所以,这种原理的柱塞泵不必再装泄漏回油管路,这也是这种泵的一个优点,并且是柱塞泵提高寿命的关键所在,同时径向联合配流开路式柱塞泵也可以实现自冷却。

图2-7 联合配流开路式轴向柱塞泵自冷却原理
4.联合配流开路式泵的优缺点
这种泵的优点是:无泄漏回油管路,可自冷却,可串、并联,结构简单,压力高,效率高,工艺性好,寿命长。它不但可以同时供给多个系统不同的定流量,而且可以供给一个系统不同的分级定流量,这些流量间是互不相干的。
缺点是这种泵不可逆,因此不能作油压马达使用。
由于这种开路式泵的产生,使得很多以前要求系统解决的问题,有的甚至连系统也难以解决的问题得到了解决。从而使它成为液压行业不可缺少的且广泛应用的泵类之一。
三、端面配流半开路式泵工作原理及组成
端面配流半开路式轴向柱塞泵是在闭路式轴向柱塞泵原理的基础上发展起来的新型轴向柱塞泵。它具有无泄漏回油管路,可以自冷却、自润滑、发热量小、温升低、可逆(可作单向马达使用)、结构简单、体积小、重量轻、效率高、寿命长等优点。
按其原理可制造出各种型号的新泵,并可以对目前广泛应用的闭路式轴向斜盘泵进行改造,改造后同样具备开路式泵的优点。
1.基本组成
图2-8所示为端面配流半开路式斜盘型轴向柱塞泵工作原理简图。配流盘固定不动,传动轴带动缸体转动,它相当于两个配流盘配流的柱塞泵,即前配流盘7和后配流盘2。这两个配流盘都是不对称结构,一半开配流窗口,一半不开配流窗口,并且开的位置不同,放的方向也不同,有的是直立着,有的是倾斜着,在壳体8内有转动缸体3,缸体内均匀分布着多个轴向放置的柱塞5。这个柱塞与联合配流开路式轴向柱塞泵中的柱塞完全相同,柱塞内装有回程弹簧4,靠这个回程弹簧的弹簧力使柱塞和滑靴紧压在倾斜的配流盘上(这个弹簧是为了说明原理而画的,实际结构工作原理简图不是在这个位置上)。在柱塞的球头上装有与柱塞头配合的滑靴6。滑靴中心开有进油孔,低压油从这个孔进入柱塞腔内。这个柱塞、滑靴和弹簧完全与联合配流开路式泵相同。

图2-8 端面配流半开路式斜盘型轴向柱塞泵工作原理简图
1—传动轴;2—后配流盘;3—缸体;4—回程弹簧;5—柱塞;6—滑靴;7—前配流盘;8—壳体
2.工作原理
该泵的工作原理简图如2-8所示。由于有一个倾斜的配流盘,所以随着缸体的转动,柱塞将在缸体内做往复直线运动。柱塞伸长(即吸油)时,由直立的配流盘将缸体的底孔堵死,此时滑靴刚好位于倾斜配流盘上所开的配流窗口处,液压油通过倾斜配流盘上开的配流窗口经过滑靴中心孔进入由柱塞、滑靴、直立的配流盘、倾斜的配流盘、转动缸体所组成的控制腔室。压油时,由倾斜的配流盘无配流口侧将滑靴的底部堵死,此时,直立的配流盘上开的配流窗口正好对着转动缸体的输出口,随着缸体的转动,柱塞向内压缩,使得腔内的油液压力升高,当压力高于输出口压力时,油液被压出,这就是端面配流半开路式斜盘型轴向柱塞泵的工作原理。
若改变倾斜配流盘的倾斜角度,就可以改变泵的输出流量,这样就成为变量的端面配流半开路式轴向柱塞泵了。其变量形式可参照已成型的各种变量闭路式轴向柱塞泵。
图2-9所示为端面配流半开路式径向柱塞泵的工作原理简图。图中外环4是配油环,它上面开有进油槽,6为传动轴,2是配油轴,它上面开有配流槽(是压油槽),柱塞滑靴仍是中心开通孔的,当转子转动时,柱塞在转子内做往复运动,伸出时吸油,压缩时压油,由轴、转子、柱塞、滑靴、外环组成控腔室,由轴与外环控制吸压油过程,以达到泵的作用。

图2-9 端面配流半开路式径向柱塞泵工作原理
1—回程弹簧;2—配油轴;3—泵壳;4—外环;5—转子;6—轴;7—柱塞的回程弹簧;8—柱塞;9—滑靴;10—滑块
简而言之,其原理为:由直立的和倾斜的外环、两块配流盘、转动的缸体、柱塞、滑靴组成周期性变化的密封容积,由两块配流盘同时控制泵的吸、压油过程,达到输出高压液体的目的。轴向力不平衡问题可参照联合配流开路式轴向柱塞泵轴向力平衡方法解决。
3.端面配流半开路式泵自冷却方法
图2-10(a)所示为端面配流半开路式泵的自冷却原理简图(图中箭头表示液压油流动情况和方向)。液压油不但可以由倾斜配流盘一侧进入腔室内,而且还可以由斜盘的另一侧经过滑靴之间的间隙进入腔室内。这部分液压油的流动可以将滑靴和斜盘这对摩擦副所产生的热量带走,起到自冷却的作用,同时加强了该摩擦副的润滑性能。为了使得其冷却性能更好,可将进油口开在如图2-10(b)所示的箭头处。因为在图2-10(a)中,液压油只能对滑靴和斜盘这对摩擦副起作用。而图2-10(b)所示情况,不但可以起到以上作用,又可以对直立的配流盘和转动缸体这对摩擦副起冷却作用。这样一来,泵所吸进的全部流量都参加了泵的自冷却。所以这种泵温升低,发热量少,润滑性好。

图2-10 端面配流半开路式泵自冷却原理简图
4.端面配流半开路式泵的特点
该泵具有无泄漏回油管路、压力高、效率高,寿命长,可自冷却、自润滑,可逆(作单向马达使用)、结构简单、加工方便、重量轻、体积小、单位输出功率大、变量方便、节能等特点。但是由于柱塞的一端进油,所以自吸性能受到限制,高速时(1500r/min以上)要有一定的供油压力方能正常工作。
5.端面配流半开路式泵与其他轴向柱塞泵的区别
该泵与闭路式端面配流轴向柱塞泵的区别是:以轴向泵为例,由一块配流盘控制泵的吸压油过程变为由两块配流盘同时控制泵的吸压油过程,变直立的配流盘进油为斜盘进油;变缸体进油为柱塞球头进油,使柱塞成为通路,这就是我们称之为开路式泵的原因。
该泵与联合配流开路式轴向柱塞泵的区别在于:去掉了不可逆元件——高压配流阀;改转动斜盘结构为转动缸体结构,使得变量更为方便。
四、端面配流全开路式泵工作原理及组成
1.工作原理及组成
图2-11所示为端面配流全开路式轴向柱塞泵结构简图。该泵的基本组成除件2与图2-8中件2不同外,其余完全相同。它的工作原理是:当柱塞做往复直线运动时,液压油可以像端面配流半开路式轴向柱塞泵那样,从倾斜配流盘上开的配流窗口处进入由直立的配流盘、倾斜配流盘、柱塞、滑靴、转动缸体所组成的腔室内。这样一来,液压油实际上在被吸入时,是由柱塞的两端同时进入腔室内的,因此减少了吸油阻力,增加了吸油时的油面积,降低了吸油流速,从而为提高泵自吸情况下的转速打下了良好的基础。压油时的情况与端面配流半开路式轴向柱塞泵完全相同。径向全开路式柱塞泵与图2-9相同,只是轴向再开一个吸油口,其原理略。

图2-11 端面配流全开路式轴向柱塞泵工作原理简图
1—传动轴;2,7—配流盘;3—缸体;4—回程弹簧;5—柱塞;6—滑靴;8—壳体
其工作原理可概括为:由两块配流盘、缸体、柱塞、滑靴组成周期性变化的腔室,由两块配流盘控制泵的吸、压油过程,达到输出高压液体的目的。
2.端面配流全开路式泵的自冷却方法
以轴向泵为例,如图2-11所示,箭头表示液流流动方向。液压油可以由倾斜配流盘上的窗口进入柱塞腔内。此外,还有一部分油液绕经倾斜盘上的窗口进入柱塞腔内,另有一部分油液经过缸体与壳体之间的间隙绕到直立的配流盘处(这要看进口的阻力如何,这部分油液还有倒流的可能)。
同时,在直立的配流盘侧,还有另一部分油液进入柱塞腔内,若此处进油阻力小,可能有一部分液压油将绕过缸体与壳体之间的间隙,流到倾斜的配流盘处,再经过该配流盘进入柱塞腔内。我们可以通过改变两个入口的进口阻力来改变各进口的进入油量。由于各进口的油流分别对摩擦副起冷却作用,所以我们可以通过控制进口阻力的办法来控制自冷却流量,即哪部分发热大,就让其自冷却流量大些。可以按发热量控制自冷却流量的大小,这一点是其他柱塞泵所不可比拟的。
从以上分析可知,端面配流全开路式轴向柱塞泵所吸入的全部流量都参加了自冷却,同时又可以按着各摩擦副的发热量的大小随意分配自冷却流量,从而为提高柱塞泵的寿命打下了坚实的基础。
为了与标准情况相同,可将进油口改到直立的配流盘侧,图2-12所示为标准的端面配流全开路式轴向柱塞泵自冷却简图。

图2-12 端面配流全开路式轴向柱塞泵自冷却原理
3.端面配流全开路式泵的特点
该泵不但具备端面配流半开路式泵的一切优点,而且还有其独特的优点。它可以改善自吸性能,从而可以提高自吸转速;也可以任意分配自冷却流量的比例,从而大大提高柱塞泵的实际使用寿命。
4.端面配流全开路式泵与其他轴向柱塞泵的区别
以轴向泵为例,端面配流全开路式轴向柱塞泵与闭路式端面配流轴向柱塞泵的区别是:由一块配流盘配流控制泵的吸压油过程,变为由两块配流盘同时配流控制泵的吸压油过程。变直立配流盘进油为两块配流盘同时进油,变不通路柱塞为通路柱塞,即开路式柱塞。
端面配流全开路式轴向柱塞泵与联合配流开路式轴向柱塞泵的区别为:变缸体不动为转动,变转动斜盘为固定斜盘,变出油阀为配流盘,变由滑靴进油为柱塞两端同时进油的双端面进油。
端面配流全开路式轴向柱塞泵与端面配流半开路式的区别在于:改直立配流盘不对称结构为对称结构,改柱塞的一端进油为从柱塞的两端同时进油。
另外,对于开路式轴向柱塞泵来讲,当柱塞位于高压侧时,由于柱塞内是高压液体,所以使得柱塞腔内的液体从各个不同间隙泄漏出来。在开路式泵中,这部分油直接参与自冷却流量,不需像闭路式轴向柱塞泵那样安装一个泄漏回油管将其引走。因此开路式泵不仅简化了结构,而且提高了性能。
开路式泵不但可以按以上所述的原理设计新型结构的轴向柱塞泵,而且可用该原理对如今广泛应用在液压行业中的闭路式柱塞泵进行改造,改造后的闭路式泵完全可以具备开路式泵的性能。
五、开路式斜盘型串联多级泵原理及组成
在液压技术领域中,一般将压力大于32MPa的称为超高压。随着锻压、轧钢、工程、矿山机械的飞速发展,越来越要求液压传动的高压化,于是对液压泵的流量和压力提出了越来越高的要求。目前,超高压范围内,国内外应用的泵的压力是63MPa、70MPa、80MPa。在英、美、日、德等国家都有这一压力等级的泵、缸、阀系列产品,泵流量大都在4~10L/min的范围内。近几年来,国内也陆续有超高压小流量泵问世,且已形成系列。由于超高压在技术上有一定难度,故到目前为止还没有超高压、大流量的液压泵问世。
众所周知,到目前为止,在各种容积式液压泵中,唯有柱塞泵是实现高压、高速化较为理想的泵结构之一。但超高压、大流量的要求给柱塞泵的设计带来了一系列的问题。
①滑靴的承载能力。随着工作压力的增加,柱塞泵中柱塞副对滑靴的作用力随之增大;另一方面,随着流量的增加,柱塞直径随之增大(在转速和柱塞行程一定的情况下),因此柱塞副对滑靴的作用力随时之增大。所以滑靴的承载能力是发展超高压大流量液压泵的关键环节之一。同样道理,配流盘与缸体这对摩擦副,随着高压大流量化的发展,本来就易烧盘的地方,就更难于解决了。因此,这也是液压泵实现高压、高速、大流量化的一个关键。
②随着压力的增加,对各零件的强度要求增加,因此尺寸将逐渐加大,即体积、重量增大,有时即使增大了强度,也不一定能达到越高压的目的。
③泄漏问题。超高压泵压力可达到70~100MPa,根据泄漏公式Q=kh3Δp可知,泄漏量与压力成正比,随着压力的增大,泄漏量将大大增加。
目前,国内生产的高压大流量泵最高压力达40MPa,流量为250L/min左右。泵在实际工作时,一般压力为20~25MPa。为了得到超高压油液,液压机大都采用多台柱塞泵供应增压器,由增夺压器传动液压缸工作。增压器工作,可产生80MPa以上的压力,这样虽然解决了液压机上超高压油源的压力供应问题,但不能解决大流量超高压问题。同时还会使液压机上液压缸的工作行程、速度受到限制,并导致液压机能源复杂,液压泵遍地,使占地面积增大、泄漏严重、故障点增多、整个设备价格上升等。
近十几年来超高压小流量液压泵在我国才逐步发展起来,但其产品规格少,基本上没有形成自己的系列产品,大多只是参照国外样机研制成功的产品。目前国内生产的超高压小流量泵均属于阀配流定量柱塞泵,规格范围是压力63MPa、70MPa、80MPa,流量为4~10L/min。如机电部自动化所配合德州液压机具厂从德国引进的RK系列超高压径向柱塞泵,上海华光工具厂生产的CZB6302及英国托靴尔公司生产的FCM系列阀式轴向柱塞泵等。这些超高压小流量液压泵均采用阀配流。径向柱塞采用套有滚针轴承的偏心轴驱动柱塞;轴向柱塞泵采用有推力轴承的斜盘驱动柱塞,柱塞头部直接作用于滚针轴承外套或斜盘上,为线接触或面接触,呈挤压状态,承载能力有限。这些超高压泵结构仅能适应超高压小流量,不能满足超高压大流量的要求。
到目前为止,容积中为使泵的压力成倍提高,已有串联的齿轮泵、叶片泵,就是没有串联的柱塞泵,如能实现串联柱塞泵,超高压大流量的供应问题就能迎刃而解了。
为了解决液压机上多台泵供液的问题,满足轧钢、锻压、工程、矿山机械对液压泵的超高压大流量的要求,国外一直有人想搞柱塞泵直传,即取消增压器,实现轴向柱塞泵串联。但到目前为止,还未见串联柱塞泵问世。
为了说明问题,请看图2-13所示的串联叶片泵原理简图,第一级的高压输出口与低压输出口相通,第二级泵的工作原理与第一级泵完全相同。第二级泵的容腔形成与第一级泵输出压力相等的压力容腔,一部分高压油经泄漏通道流入第二级泵的低压口(实际是第一级泵的出口),形成内泄漏。

图2-13 双级叶片泵原理及符号简图
1,2—液压管道
也就是说,齿轮泵和叶片泵都是一个进油管、一个出油管,没有其他管路,现有的闭路式轴向柱塞泵不但有进油管路和出油管路,而且还多了一条泄漏回油管路,成为三条管路的泵。所以不易形成柱塞泵的串联。而开路式轴向柱塞泵正好和齿轮、叶片泵一样,只有进、出油口,所以也完全可以实现柱塞泵的串联,并可以增压。
1.联合配流开路式串联多级泵原理
图2-14所示为联合配流开路式串联双级轴向柱塞泵原理简图。它是由两个联合配流开路式轴向柱塞泵串联而成的。可以是用一个通轴使串联泵成为一体,也可以是分体的,即分两个泵,分别由管路连接起来,只要二级泵轴处可以密封(这里假定可以密封),就可以实现柱塞泵的串联了。

图2-14 联合配流开路式串联双级轴向柱塞泵原理简图
联合配流开路式轴向柱塞泵和齿轮泵、叶片泵一样,只有进油和出油管路,没有闭路式轴向柱塞泵的泄漏回油管路,故与齿轮泵和叶片泵一样具有可串联性。
如图2-14所示,液压油由p入进入第一级泵,然后第一级泵将压力提高后进入第二级泵的吸油腔,第二级泵吸入后,将压力再提高,则使泵成为高压输出,即成倍地提高压力,这是双级联合配流开路式轴向柱塞泵原理,依此类推,可得到多级联合配流开路式轴向柱塞泵,从而使压力提高。
2.端面配流半开路式串联多级泵原理
图2-15所示为端面配流半开路式串联双级轴向柱塞泵原理简图。这种开路式轴向柱塞泵原理与联合配流开路式轴向柱塞泵原理一样具有可串性。这里的关键在于第二级泵壳内为吸入压力(即第一级输出压力),所以可以实现双级泵的串联,当然可以是通轴的,也可以是分体轴的,并且可以实现多级串联。

图2-15 端面配流半开路式串联双级轴向柱塞泵原理图
3.端面配流全开路式串联多级泵原理
图2-16所示为端面配流全开路式轴向双级串联柱塞泵原理简图,同样道理也可以实现多级串联。串联中的每一级泵也可以实现分别变量。

图2-16 端面配流全开路式轴向双级串联柱塞泵简图
4.混合型多级开路式轴向柱塞泵
如前所述,所有开路式柱塞泵均具有可串性,也就是说,可以将三种泵任意组合串联起来组成混合型串联多级开路式柱塞泵。任意一种泵均可作为任意一级泵,但需要指出的是,第一级泵(即初级泵)可以是开路式泵,也可以是现有的闭路式泵。
5.轴向柱塞泵的新分类
由于开路式泵的出现,应对轴向柱塞泵进行新的分类。
轴向柱塞泵可分为闭路式轴向柱塞泵、开路式轴向柱塞泵及两种混合型的泵。
①闭路式轴向柱塞泵。可分为阀配流式、轴配流式、端面配流式泵。
②开路式轴向柱塞泵。可分为联合配流开路式(单级、多级、多输出、变量)、端面配流半开路式(单级、多级、变量)、端面配流全开路式(单级、多级、变量)、开路式混合型多级泵。
③轴向开、闭路混合式多级泵。
同理,径向泵也可重新分类。