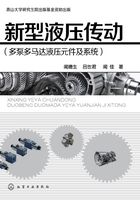
第五节 典型回路及液压传动概述
一、液压传动简介
液压传动系统按工作介质的循环方式不同可以分为开式系统和闭式系统。
开式系统是指液压泵从油箱吸油,油液流经各种控制阀后,驱动液压执行元件,最后再经过换向阀回油箱。这种系统结构较为简单,系统油箱大,油泵自吸性能好,还可以发挥油箱的散热、沉淀杂质作用,但因油液常与空气接触,使空气易于渗入系统,导致机构运动不平稳等后果。
闭式系统中,液压泵的进油管直接与执行元件的回油管相连,工作液体在系统的管路中进行封闭循环。其结构紧凑,与空气接触机会少,空气不易渗入系统,工作机构的变速和换向靠调节泵或马达的变量机构实现,避免了开式系统换向过程中所出现的液压冲击和能量损失,故传动较平稳。但闭式系统比开式系统复杂,因无油箱,油液的散热和过滤条件较差。为补偿系统中的泄漏,通常需要一个小流量的补油泵和油箱。由于单杆双作用油缸大小油腔流量不等,在工作过程中会使功率利用下降,所以闭式系统中的执行元件一般为液压马达。
二、典型回路简介
(一)快速运动回路
快速运动回路的功用在于使执行元件获得尽可能大的工作速度,以提高劳动生产率并使功率得到合理的利用。实现快速运动的回路主要有液压缸差动连接的快速运动回路和双泵供油的快速运动回路。
(二)调速回路
在液压系统中往往需要调节液压执行元件的运动速度,以适应主机的工作循环需要。目前常用的调速回路主要有以下几种:节流调速回路、容积调速回路、容积节流调速回路(联合调速)。下面主要讨论节流调速回路和容积调速回路。
1.采用节流阀的节流调速回路
节流调速回路根据流量控制元件在回路中安放的位置不同,分为进油路节流调速回路、回油路节流调速回路、旁油路节流调速回路三种基本形式。
(1)进油路节流调速回路
如图1-26(a)所示,将节流阀串联在液压泵和液压缸之间,用它来控制进入液压缸的流量,从而达到调速的目的,称为进油路节流调速回路。
在这种回路中,定量泵输出的多余流量通过溢流阀流回油箱。由于溢流阀有溢流,泵的出口压力为溢流阀的调定压力并保持定值,这是进油路节流调速回路能够正常工作的条件。
(2)回油路节流调速回路
如图1-26(b)所示,将节流阀串联在液压缸的回油路上,借助节流阀控制液压缸的排油量来调节其运动速度,称为回油路节流调速回路。
(3)旁油路节流调速回路
把节流阀装在与液压缸并联的支路上,利用节流阀把液压泵供油的一部分排回油箱实现速度调节的回路,称为旁油路节流调速回路。
如图1-26(c)所示,在这个回路中,液压泵的供油压力取决于负载,溢流的功能由节流阀来完成,而溢流阀作安全阀用,其调定压力为最大负载压力的1.1~1.2倍,正常工作时处于关闭状态。

图1-26 节流调速回路
2.容积调速回路
容积调速回路可用变量泵供油,根据需要调节泵的输出流量,或应用变量液压马达,调节其每转排量以进行调速,也可以采用变量泵和变量液压马达联合调速。容积调速回路的主要优点是没有节流调速时通过溢流阀和节流阀的溢流功率损失和节流功率损失。所以发热少,效率高,适用于功率较大,并需要有一定调速范围的液压系统中。
容积调速回路按所用执行元件的不同,分为泵-缸式回路(一般为开式回路)和泵-马达式回路(可做成闭式回路)。这里主要介绍泵-马达式容积调速回路。
(1)变量泵-定量马达式容积调速回路
图1-27(a)为变量泵-定量马达式容积调速回路。回路中压力管路上的安全阀4,用以防止回路过载,低压管路上连接一个小流量的辅助油泵1,以补偿泵3和马达5的泄漏,其供油压力由溢流阀6调定。辅助泵与溢流阀使低压管路始终保持一定压力,不仅改善了主泵的吸油条件,而且可置换部分发热油液,降低系统温升。
(2)定量泵-变量马达式容积调速回路
图1-27(b)为定量泵-变量马达式容积调速回路。马达的输出功率和回路的工作压力都由负载功率决定,不因调速而发生变化,所以这种回路常被称为恒功率调速回路。该回路的优点是能在各种转速下保持很大输出功率不变,其缺点是调速范围小,因此这种调速方法往往不能单独使用。

图1-27 容积调速回路
(3)变量泵-变量马达式容积调速回路
图1-27(c)为双向变量泵2和双向变量马达3组成的容积式调速回路。回路中各元件对称布置,改变泵的供油方向,就可实现马达的正反向旋转,单向阀8和5用于辅助泵1双向补油,单向阀9和7使溢流阀4在两个方向上都能对回路起过载保护作用。一般机械要求低速时输出转矩大,高速时能输出较大的功率,这种回路恰好可以满足这一要求。
3.同步回路
同步运动包括速度同步和位置同步两类。速度同步是指各执行元件的运动速度相同;而位置同步是指各执行元件在运动中或停止时都保持相同的位移量。同步回路就是用来实现同步运动的回路。由于负载、摩擦、泄漏等因素的影响,很难做到精确同步。下面介绍的几种同步回路,只能做到基本上同步。
(1)液压缸机械联结的同步回路
这种同步回路是用刚性梁、齿轮、齿条等机械零件在两个液压缸的活塞杆间实现刚性联结以实现位移的同步。如图1-28(a)所示,这种同步方法比较简单经济,能基本上保证位置同步的要求,但由于机械零件在制造、安装上的误差,同步精度不高。同时,两个液压缸的负载差异不宜过大,否则会造成卡死现象。
(2)采用调速阀的同步回路
图1-28(b)所示是采用调速阀的单向同步回路。两个液压缸是并联的,在它们的进(回)油路上,分别串接一个调速阀,仔细调节两个调速阀的开口大小,便可控制或调节进入或自两个液压缸流出的流量,使两个液压缸在一个运动方向上实现同步,即单向同步。
这种同步回路结构简单,但是两个调速阀的调节比较麻烦,而且还受油温、泄漏等的影响,故同步精度不高,不宜用在偏载或负载变化频繁的场合。
(3)用串联液压缸的同步回路
图1-28(c)所示为带有补偿装置的两个液压缸串联的同步回路。当两缸同时下行时,若缸5活塞先到达行程端点,则挡块压下行程开关1S,电磁铁3YA得电,换向阀3左位投入工作,压力油经换向阀3和液控单向阀4进入缸6上腔进行补油,使其活塞继续下行到达行程端点;如果缸6活塞先到达端点,行程开关2S使电磁铁4YA得电,换向阀3右位投入工作,压力油进入液控单向阀控制腔,打开阀4,缸5下腔与油箱接通,使其活塞继续下行到达行程端点,从而消除累积误差。这种回路偏载所造成的压差不影响流量的改变,只会导致微小的压缩和泄漏,因此允许较大偏载,同步精度较高,回路效率也较高。
(4)采用同步马达的同步回路
图1-28(d)所示为采用相同结构、相同排量的两个液压马达作为等流量分流装置的同步回路。两个马达轴刚性联结,把等量的油分别输入两个尺寸相同的液压缸中,使两液压缸实现同步。图中的节流阀用于消除行程端点两缸的位置误差。

图1-28 同步回路
(5)采用同步阀的同步回路
泵输出的油液进入同步阀,经同步阀中的固定节流口分成两路,两路油经可变节流口后进入执行元件中。如图1-28(e)所示,两路油量因同步阀的自动调节作用,始终保持相等,不因外载变化而变化。采用同步阀的同步回路比较简单、同步精度高,但有节流损失。
4.顺序回路
当用一个液压泵向几个执行元件供油时,如果这些元件需要按一定顺序依次动作,就应该采用顺序回路。如转位机构的转位和定位,夹紧机构的定位和夹紧等。
顺序动作回路,根据其控制方式的不同,分为行程控制、压力控制和时间控制三类。其中以前两种用得最多,这里只对前两种进行介绍。
(1)行程控制顺序动作回路
图1-29(a)是一种采用行程开关和电磁换向阀配合的顺序动作回路。操作时首先按动启动按钮,使电磁铁1YA得电,压力油进入液压缸3的左腔,使活塞按箭头①所示方向向右运动。当活塞杆上的挡块压下行程开关6S后,通过电气上的联锁使1YA断电,3YA得电。液压缸3的活塞停止运动,压力油进入液压缸4的左腔,使其按箭头②所示的方向向右运动。当活塞杆上的挡块压下行程开关8S,使3YA断电,2YA得电,压力油进入缸3的右腔,使其活塞按箭头③所示的方向、向左运动;当活塞杆上的挡块压下行程开关5S,使2YA断电,4YA得电,压力油进入液压缸4右腔,使其活塞按箭头④的方向返回。当挡块压下行程开关7S时,4YA断电,活塞停止运动,至此完成一个工作循环。

图1-29 顺序回路
这种顺序动作回路的优点是:调整行程比较方便,改变电气控制线路就可以改变油缸的动作顺序,利用电气互锁,可以保证顺序动作的可靠性。
(2)压力控制顺序动作回路
图1-29(b)是利用压力继电器实现顺序动作的顺序回路。按启动按钮,使1YA得电,换向阀1左位工作,液压缸7的活塞向右移动,实现动作顺序①;到右端后,缸7左腔压力上升,达到压力继电器3的调定压力时发讯,使电磁铁1YA断电,3YA得电,换向阀2左位工作,压力油进入缸8的左腔,其活塞右移,实现动作顺序②;到行程端点后,缸8左腔压力上升,达到压力继电器5的调定压力时发讯,使电磁铁3YA断电,4YA得电,换向阀2右位工作,压力油进入缸8的右腔,其活塞左移,实现动作顺序③;到行程端点后,缸8右腔压力上升,达到压力继电器6的调定压力时发讯,使电磁铁4YA断电,2YA得电,换向阀1右位工作,缸7的活塞向左退回,实现动作顺序④。到左端后,缸7右端压力上升,达到压力继电器4的调定压力时发讯,使电磁铁2YA断电,1YA得电,换向阀1左位工作,压力油进入缸7左腔,自动重复上述动作循环,直到按下停止按钮为止。
在这种顺序动作回路中,为了防止压力继电器在前一行程液压缸到达行程端点以前发生误动作,压力继电器的调定值应比前一行程液压缸的最大工作压力高0.3~0.5MPa,同时,为了能使压力继电器可靠地发出信号,其压力调定值又应比溢流阀的调定压力低0.3~0.5MPa。
5.平衡回路
为了防止立式液压缸与垂直运动的工作部件由于自重而自行下落造成事故或冲击,可以在立式液压缸下行时的回路上设置适当的阻力,产生一定的背压,以阻止其下降或使其平稳地下降,这种回路即为平衡回路。
(1)采用单向顺序阀的平衡回路
图1-30(a)所示是采用单向顺序阀组成的平衡回路。调节单向顺序阀1的开启压力,使其稍大于立式液压缸下腔的背压。活塞下行时,由于回路上存在一定背压支承重力负载,活塞将平稳下落;换向阀处于中位时,活塞停止运动。此处的单向顺序阀又称为平衡阀。这种平衡回路由于回路上有背压,功率损失较大。另外,由于顺序阀和滑阀存在内泄,活塞不可能长时间停在任意位置,故这种回路适用于工作负载固定且活塞闭锁要求不高的场合。

图1-30 平衡回路
(2)采用液控单向阀的平衡回路
图1-30(b)所示是用液控单向阀的平衡回路。由于液控单向阀是锥面密封,泄漏小,故其闭锁性能好。回油路上的单向节流阀2用于保证活塞向下运动的平稳性。假如没有节流阀,活塞下行时,液控单向阀1将被控制油路打开,回油腔无背压导致活塞加速下降,使液压缸上腔供油不足,液控单向阀又会因此而关闭,但关闭后控制油路又建立起压力,将阀2打开,致使液控单向阀时开时闭,活塞下行时很不平稳,产生振动或冲击。
6.卸荷回路
当系统中执行元件短时间工作时,常使液压泵在很小的功率下做空运转,而不是频繁启动驱动液压泵的原动机。这样可以减少液压泵磨损,降低功率消耗,减小温升。因为泵的输出功率为其输出压力与输出流量之积,当其中的一项数值等于或接近于零时,即为液压泵卸荷。
卸荷的方式有两类:一类是液压泵卸荷,执行元件不需要保持压力;另一类是液压泵卸荷,但执行元件仍需保持压力。
(1)执行元件不需保压的卸荷回路
图1-31(a)所示为采用M型(或K型、H型)中位机能换向阀实现液压泵卸荷的回路。当换向阀处于中位时,液压泵出口直通油箱,泵卸荷。因回路需保持一定的控制压力以操纵执行元件,故在泵出口安装单向阀。

图1-31 卸荷回路
(2)执行元件需要保压的卸荷回路
图1-31(b)所示为限压式变量泵的卸荷回路。当系统压力升高达到变量泵压力调节螺钉调定压力时,压力补偿装置动作,液压泵3输出流量随供油压力升高而减小,直到维持系统压力所必需的流量,回路实现保压卸荷,系统中的溢流阀1作安全阀用,以防止泵的压力补偿装置的失效而导致压力异常。
三、辅助元件简介
液压辅助元件有滤油器、蓄能器、管件、密封件、油箱和热交换器等,除油箱通常需要自行设计外,其余皆为标准件。液压辅助元件和液压元件一样,都是液压系统中不可缺少的组成部分,它们对系统的性能、效率、温升、噪声和寿命的影响不亚于液压元件本身。辅助装置处理不好,可导致系统工作性能不好,甚至使系统遭到破坏而无法工作。
1.滤油器
液压系统的故障大多数是由于油液中含有杂质而造成的,油液中的杂质会使液压元件运动副的结合面磨损,堵塞阀口,卡死阀芯,使系统工作可靠性大为降低。在系统中安装滤油器,是保证液压系统正常工作的必要手段。
按滤芯的材料和结构形式,滤油器可分为网式、线隙式、纸质滤芯式、烧结式滤油器及磁性滤油器等。按滤油器安装的位置不同,还可以分为吸滤器、压滤器和回油过滤器。考虑到泵的自吸性能,吸油滤油器多为粗滤器。
(1)网式滤芯
如图1-32(a)所示,网式滤芯是在周围开有很多孔的金属筒形骨架1上,包着一层或两层铜丝网2,过滤精度由网孔大小和层数决定。网式滤芯结构简单,清洗方便,通油能力大,过滤精度低,常作吸滤器。

图1-32 不同材料和结构形式滤油器
(2)线隙式滤芯
线隙式滤芯如图1-32(b)所示,用铜线或铝线密绕在筒形骨架的外部来组成滤芯,油液经线间间隙和筒形骨架槽孔流入滤芯内,再从上部孔道流出。这种滤油器结构简单,通油能力大,过滤效果好,多为回油过滤器。
(3)纸质滤芯
图1-32(c)所示为纸质滤油器的结构,其类同于线隙式,只是滤芯为纸制,由三层组成。外层2为粗眼钢板网,中层3为折叠成星状的滤纸,里层4由金属丝网与滤纸折叠而成。纸制滤芯结构紧凑,通油能力大,过滤精度可达5~30m,可在32MPa下工作,在配备壳体后用作压力油的过滤;其缺点是无法清洗,需经常更换滤芯。
为了保证滤油器能正常工作,不致因杂质逐渐聚积在滤芯上引起压差增大而损坏纸芯,滤油器顶部装有堵塞状态发讯装置1,当滤芯逐渐堵塞时,压差增大,感应活塞推动电气开关并接通电路,发出堵塞报警信号,提醒操作人员更换滤芯。
(4)烧结式滤芯
图1-32(d)所示为金属烧结式滤芯。滤芯可按需要制成不同的形状,选择不同粒度的粉末烧结成不同厚度的滤芯,可以获得不同的过滤精度,其范围在10~100μm之间。烧结式滤油器的过滤精度较高,滤芯的强度高,抗冲击性能好,能在较高温度下工作,有良好的抗腐蚀性,且制造简单,它可安装在不同的位置。
(5)磁性滤油器
磁性滤油器的工作原理就是利用磁铁吸附油液中的铁质微粒。但一般的磁性滤油器对其他非铁质污染物不起作用,通常用作回油过滤或其他形式滤油器的一部分。
2.蓄能器
蓄能器是一种能量储蓄装置。它在适当的时机将系统中的能量转变为压缩能或位能储存起来,当系统需要时,又将压缩能或位能转变为液压或气压等能量释放出来,重新补给系统。
(1)蓄能器的功能
辅助动力源——工作周期较短的间歇工作系统或一个循环内速度差别很大的系统,在系统不需要大流量时,可以把液压泵输出的多余压力油储存在蓄能器内,到需要时再由蓄能器快速向系统释放,这样就可以减小液压泵的容量以及电动机的功率消耗,从而降低系统温升。
系统保压——在液压泵停止向系统提供油液的情况下,蓄能器所存储的压力油液向系统补充,补偿系统泄漏或充当应急能源,使系统在一段时间内维持系统压力。避免系统在油源突然中断时所造成的机件损坏。
吸收系统脉动,缓和背压冲击——蓄能器能吸收系统压力突变时的冲击,如液压泵突然启动或停止,液压阀突然关闭或开启,液压缸突然运动或停止。也能吸收液压泵工作时的流量脉动所引起的压力脉动,相当于油路中的平滑滤波。
(2)蓄能器的结构形式
如图1-33所示,蓄能器通常有重力式、弹簧式和充气式(气体加载式)等几种。目前常用的是利用气体压缩和膨胀来储存、释放液压能的充气式蓄能器。

图1-33 蓄能器的结构形式
3.油箱
油箱的基本功能是:储存工作介质;散发系统工作中产生的热量;分离油液中混入的空气,沉淀污染物及杂质。
按油面是否与大气相通,可分为开式油箱与闭式油箱(充压式油箱)。开式油箱与大气相通,散热条件较好,广泛用于一般的液压系统;闭式油箱体积小,散热性差,需设置专门的冷却装置,一般由于行走机械、水下和高空无稳定气压的场合。
为了在相同的容量下得到最大的散热面积,油箱外形以立方体或长六面体为宜,最高油面只允许达到油箱高度的80%,油箱一般由钢板焊接而成,顶盖可以是整体的,也可以分为几块,泵和电机、阀的集成装置有时也安装在箱盖上,油箱底脚高度应在150mm以上,以便散热、搬移和放油;油箱四周要有吊耳,以便起吊装运。
4.管件
管件包括管道、管接头和法兰等,其作用是保证油路的连通,并便于拆卸、安装;根据工作压力、安装位置确定管件的连接结构;与泵、阀等连接的管件应由其接口尺寸决定管径。
(1)管道
管道种类、特点和适用场合见表1-1。
表1-1 管道的种类、特点和适用场合

(2)管接头
管接头是管道与管道、管道与其他元件的可拆卸连接件,如泵、阀、集成块等的连接。接口一般采用普通细牙螺纹或锥螺纹。
5.热交换器
液压系统的工作温度一般希望保持在30~50℃的范围之内,最高不超过65℃,最低不低于15℃,如果液压系统靠自然冷却仍不能使油温控制在上述范围内,就需要安装冷却器;反之,如环境温度太低,无法使液压泵启动或正常运转,就需安装加热器。
(1)冷却器
液压系统中用得较多的冷却器是强制对流式多管头冷却器,也有使用蛇形管冷却器。
当液压系统散热量较大时,可使用化工行业中的水冷式板式换热器,它可及时将油液中的热量散发出去。
(2)加热器
液压系统的加热一般采用结构简单、能按需要自动调节最高和最低温度的电加热器,由于油液是热的不良导体,单个加热器的功率容量不能太大,以免其周围油液的温度过高而发生变质。