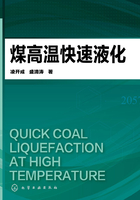
1.2 煤直接液化
1.2.1 煤直接液化综述
煤液化技术的发展所走过的历程大致可以分为以下三个阶段。第一阶段是从1913年到第二次世界大战结束,这一阶段主要以德国为代表,德国人F.Bergius获得了世界上第一个煤液化技术专利。在此阶段前期,煤直接液化由专利技术转化为工业生产成果;此阶段后期,德国为满足其战争的燃料需求,以其丰富的煤炭资源为基础,建立了12个煤直接液化工厂,工业化技术进一步成熟和完善。第二阶段是从第二次世界大战结束后到20世纪70年代,这一阶段前期即20世纪50年代,随着石油的大量开采,煤制液化油失去了市场竞争力,煤直接液化技术的发展陷入了低潮。而在70年代,由于战争原因引发的能源危机使得各国均意识到煤液化技术的重要性,使其又进入一个崭新的发展阶段。此阶段的代表工艺有溶剂精炼煤法Ⅰ和Ⅱ(SRCⅠ和Ⅱ)、氢-煤法(H-Coal)、供氢溶剂法(EDS)等。第三阶段是从20世纪70年代至今,在这期间开发了两段集成液化工艺、超临界溶剂抽提法以及煤和石油渣油联合加工等方法。总结20世纪70年代以来的煤直接液化工艺,其中最具代表的工艺有:德国IGOR工艺、美国碳氢公司(HRI)的氢-煤法(H-Coal)工艺、美国溶剂精炼煤工艺(SRC)、埃克森供氢溶剂法(EDS法)、日本NEDOL烟煤液化工艺等。
我国从20世纪80年代初开始煤直接液化的研究和开发。多年来,我国众多学者在煤直接液化的煤样选择、工艺优化、机理探讨和加氢催化剂的研发等方面均取得了丰硕的成果,为进一步开发具有中国特色的煤直接液化工艺奠定了坚实的基础。通过国际合作,煤炭科学研究院北京煤化工研究分院先后引进了3套不同工艺的煤直接液化连续试验装置,进行了上百个中国煤种的液化特性评价和煤液化工艺技术研究,筛选出了15种适合于液化的煤种,其液化油率达50%以上,取得了一批具有先进水平的研究成果,完成了国内液化煤种和铁系催化剂的筛选。目前我国人工合成铁系催化剂的研究、放大试验和催化剂催化性能评价已基本成熟。中国神华集团吸收了近几年煤炭液化研究成果,在美国HTI工艺基础上结合其他新工艺的优点,开发出了适合神华煤的一种先进煤直接液化工艺。
煤制油是满足未来不断增长液体燃料需求的重要途径之一,从1913年Bergius研究发现煤在高压下直接加氢液化获得成功开始,煤直接液化的研究己有百年历史。国内外的众多学者,无论在煤液化基础理论研究方面,还是在工程应用方面都做了大量工作,取得了丰硕的研究成果。
1.2.2 煤直接液化主要影响因素
煤在加氢液化过程中的化学反应极其复杂,涉及很多的化学反应,是一系列顺序和平行反应的综合,煤加氢液化过程受到很多因素的影响,主要有原料煤品种、气氛、溶剂、催化剂及反应条件等因素。
1.2.2.1 煤种的影响
煤直接液化对原料煤的品种有一定的要求,煤的反应性在很大程度上受到煤种的影响。一般用于煤炭直接液化的煤是年老的褐煤和年轻的烟煤。煤炭直接液化的难易程度与煤的变质程度有着密切的联系,反应的难易程度随煤的变质程度的增加而增加。表1-2列出了煤变质程度与加氢液化转化率间的关系。
表1-2 煤变质程度与加氢液化转化率的关系

除煤的变质程度外,煤的化学组成和岩相组成对煤液化也有很大影响。H含量高、O含量高、C含量低的煤转化为低分子产物的速度快,加氢液化生成的气体和水较多。原料煤中H/C原子比越大,在煤结构中存在的烷基侧链和亚甲基桥键也越多。这些基团的键能比较弱,在液化过程中易发生裂解反应而生成自由基碎片。从煤的岩相组分来看,煤中的壳质组和镜质组是煤加氢液化的有益组分,而惰性组分最难加氢。因此,含镜质组和稳定组高的煤,液化性能优于丝质组多的煤,表1-3列出了煤的岩相组分的元素组成和液化转化率的关系。
另外,煤中含有的官能团也对煤液化反应有一定程度的影响,其中含氧官能团对煤直接液化的影响最大[1]。煤中的矿物质对煤液化也有很大的影响,它既影响着催化剂的作用,本身又对煤直接液化反应有自催化作用。
表1-3 煤的岩相组分的元素组成和液化转化率的关系

1.2.2.2 气氛的影响
(1)氢气在煤液化中的作用
氢气是煤直接液化的反应物之一,高压氢气有利于煤的溶解和加氢液化转化率的提高。Guin等[2]用烷烃油分别在N2和H2气氛中将煤加热至400℃,溶解2h,然后冷却,用显微镜观察产物。结果发现,在H2中煤粒已有很大的变化,已经看不到原来的煤粒;在N2中煤粒基本上没有变化,这说明氢气能促进煤的溶解。Bruce等[3]的研究结果表明,在溶剂的供氢性能和数量不足时,氢气参与了短时液化反应。在氢气存在,尤其是在高压氢和催化剂条件下,煤转化率提高,前沥青烯向沥青烯或油的转化被促进,液化产品的质量有所提高。
一般而言,氢气参与煤液化反应的步骤为溶解、活化和反应。有研究者认为,在催化剂和高压氢气存在的条件下,供氢反应主要发生在煤和氢气之间,而不通过供氢溶剂,溶剂只是很好地溶解了煤以及液化过程中生成的小分子物质[4~6]。Ikenaga等[7]考察了以四氢萘为溶剂的煤直接液化反应。实验结果表明,不添加催化剂的煤直接液化反应,70%的活性氢来自于供氢溶剂;添加催化剂的煤直接液化反应,在过量的四氢萘中15%~40%的活性氢来自于供氢溶剂,而60%~80%的活性氢来自于气相氢。虽然前人为此做了大量的基础工作,但是由于煤液化机理的复杂性和影响因素的多样性,至今对煤直接液化过程中氢传递机理还没有形成统一的观点,因而氢气与煤之间能否直接发生热反应的问题至今年尚无满意的答案。由于氢的键合度较高(氢键裂解能427kJ/mol),氢分子似乎不可能直接与煤裂解的自由基碎片发生反应,如进行反应,需通过催化剂活化氢分子实现。
(2)其他气氛在液化中的作用
Fischer等在1921年指出,使用CO+H2O很容易使褐煤液化。许多研究表明,低煤化程度的煤与CO+H2O反应要比与H2反应更加容易,随着煤化程度增加,CO+H2O的优势减弱,而高含氧量的煤和有机物质(如泥炭、纤维素和木质素等)对CO+H2O同样有较高的反应性。Mukherjee等[8]在CO+H2O系统中对维多利亚褐煤进行了液化研究,比较了NaAlO2、NaOH、Na2CO3以及Ca(AlO2)2作为催化剂时的液化性能,并研究了反应时间、温度、搅拌速率等工艺条件对转化率的影响,发现在较低的煤水比及较低催化剂载入量的情况下,高效混合可以得到获得较高的转化率。Artanto等[9]在CO+H2O系统中对来自印度尼西亚烟煤和褐煤进行了液化试验,研究了碱金属催化剂及催化剂NaAlO2对液化性能的影响。结果表明在Ni/Mo催化剂中添加少量的S对液化反应具有较好的催化效果。
由于甲烷要在高温下才能热解,所以,长期以来的研究一直认为甲烷在煤的热解过程中是一种惰性气体,为了减少煤液化过程中耗氢量,也有研究者对甲烷气氛下煤加氢液化进行了研究。结果发现煤热解释放出的活性自由基促使甲烷在较低温度下(400℃左右)裂解,释放出活性甲基和活性氢,从而提供了稳定自由基碎片的活性氢,提高煤转化率。
1.2.2.3 溶剂的影响
在一定条件下,许多有机溶剂都能溶解一定量的煤,除了起溶解煤的作用外,更重要的是供氢溶剂在煤液化中能提供和传递活性氢。一般认为,分子量较大且部分饱和的稠环化合物适合用作供氢体,溶剂在煤液化中除了充当溶解和传热介质外,更重要的是可以提供和传递氢,使煤大分子中键裂解生成的自由基通过结合活性氢及时稳定下来。煤加氢液化中的溶剂有以下几种作用:
a.热溶解作用;
b.对煤粒的溶胀和分散作用;
c.对煤粒热裂解生成的自由基起稳定保护作用;
d.提供和传递活性氢作用;
e.对液化产物起稀释作用。
一般来说,可提供活性氢的溶剂都可用作供氢溶剂,而性能好的供氢溶剂要具有以下的特点:
a.具有芳香结构;
b.具有氢化芳香结构;
c.具有极性基团,如氨基或酚羟基;
d.高沸点的有机化合物;
e.分子体积不要太大。
工业上常用杂酚油或加氢蒽油作为溶剂。
1.2.2.4 催化剂的影响
煤高压加氢液化工艺初始时不用催化剂,循环油中沥青烯含量很高,黏度很大,操作发生困难,把反应压力提高到70.0MPa还是不行,后来用钼酸铵和氧化铁作催化剂才使这一工艺得以实施。有些工艺虽然不外加催化剂,但所用煤的矿物质中含黄铁矿,而黄铁矿也是一种活性较好的加氢催化剂。
在煤直接液化反应过程中催化剂起着举足轻重的作用,也是影响煤液化成本的关键因素之一。研究认为,催化剂的作用有以下两个方面:
a.促进煤的热解;
b.促进氢气转化为活性氢。
煤直接液化催化剂在工业上可以分为以下三类:第一类是金属卤化物催化剂,如氯化锌和氯化锡等化合物;第二类是金属催化剂,如Mo、Ni、Co、W等硫化物,这类催化剂一般用于重油加氢,活性高,用量少,但价格高,再生反复使用困难;第三类催化剂是铁基催化剂,现在工业上用得最多的是铁系催化剂,主要包括含铁的氧化物、硫化物和氢氧化物,及其他一些工业废弃的残渣和天然的含铁的矿石。因为铁系催化剂活性比较高、来源广且价格比较便宜,可不用再生,被称为“廉价可弃性催化剂”。因此,铁基材料作为煤直接液化的催化剂备受研究者的青睐。
虽然研究者对铁基催化剂的研究做了大量努力,但是对于煤直接液化过程中催化剂的机理还没有达到一致的认同。同时,研究者们对催化剂在煤直接液化过程中所起到的催化作用也持不同观点。Sharma等[10]的研究表明,催化剂主要用于煤转化为沥青烯和前沥青烯方面;而Pradhan等[11]则认为催化剂主要用于煤液化产物的轻质化方面,也就是催化剂主要影响到液化产物由前沥青烯和沥青烯向油和气的转化。
一般认为钼和钨等贵重金属化合物的催化活性在煤液化反应中的催化效果最好。为了提高贵重金属催化剂的活性,通常将钼、钨等贵重金属化合物负载在氧化铝或硅-铝载体上使用。随着时间的延长,活性不断下降,需要不断排出失活后的催化剂,同时补充新的催化剂。失活的催化剂经过再生(除去表面的积炭和重新活化)或者重新制备,再加入反应器内,许多现代煤液化工艺也采用钼的化合物作催化剂。
目前,世界上煤直接液化催化剂正向着高反应活性、高分散、低加入量与复合型的方向发展,如美国HTI公司的胶体铁催化剂。他们在30kg/d的两段液化工艺试验中,催化剂加入量为0.1%~0.5%的Fe和0.005%~0.01%的Mo,仅为传统催化剂的常规加入量的1/10~1/5。我国煤炭科学研究院研制的高分散铁系催化剂已用于神华煤制油项目,催化效果良好。
1.2.2.5 反应条件的影响
反应温度、时间和压力是煤加氢液化的主要工艺参数,也是影响煤转化率和油收率的主要因素。
(1)反应温度
温度是影响煤直接液化最基本的外部因素,不达到一定的温度,无论多长时间,煤也不能液化。在其他条件配合下,煤加热到最合适的反应温度,就可获得较高的转化率和油收率。
一般煤直接液化的温度在450℃左右。煤液化反应的基础是煤的热解,液化温度决定着热解反应,煤加氢液化的反应温度大致与煤热解的活泼区一致。反应温度升高,不仅可以增加煤的转化率,还能促进前沥青烯向油的转化,并可提高催化剂的活性。但并非反应温度越高越好,温度过高,煤的缩聚反应加强,可使部分反应生成物缩合或裂解生成气体产物,造成气体产率增加,油收率降低。不同的煤种,不同的催化剂、溶剂和氢压应选择适宜的反应温度,使煤的转化率达到最大。
(2)反应时间的影响
在适合的反应温度和足够活性氢供应下,煤加氢液化反应随着反应时间的延长,煤的转化率增大,有利于前沥青烯向苯可溶物和油转化,并且转化率出现最高点,但同时耗氢量也随之增加。目前工业加氢一般采用的反应时间为40~50min,实验室中反应时间一般为30min或60min。
(3)反应压力的影响
煤直接液化的反应温度较高,采用较高的压力才能有足够的氢分压,才能加快反应速率。煤在催化剂存在下的液相加氢速率与催化剂表面直接接触的液体层中的氢气浓度有关。提高氢压有利于氢气在液相中的溶解,催化剂表面吸附并活化的氢分子就越多,使催化剂活性表面得到充分利用。压力提高,煤液化反应中的加氢反应速率加快,抑制了煤热解产生的低分子组分缩合成半焦的反应,低分子物质得到稳定,从而使煤转化率和油收率增大。但压力提高,对高压设备的投资、能量消耗和氢耗量都要增加,产品成本相应提高,所以应根据煤性质、催化剂活性和操作温度选择合适的氢压。
1.2.3 煤直接液化反应机理
由于煤结构的复杂性和多样性,煤直接液化反应过程中化学反应也极其复杂,煤液化机理至今还没有一个统一的认识,一般认为煤在溶剂、催化剂和高压氢下,发生煤的热解,是煤液化的基础。煤在隔绝空气的条件下,加热到一定温度,煤中较弱的化学键开始断裂,形成煤热解自由基碎片,温度再升高,煤中键能较大的化学键也发生断裂。煤中容易受热裂解的主要有下列桥键。
次甲基键:—CH2—,—CH2—CH2—,—CH2—CH2—CH2—等。
含氧桥键:—O—,—CH2—O—等。
含硫桥键:—S—,—S—S—,—S—CH2—等。
裂解的难易程度与键本身有关,也与键所连接的芳香基团大小及芳香基团上的官能团有关。煤热解产生的自由基碎片由活性氢来稳定,生成低分子化合物,体系中活性氢不足时就会发生缩聚反应,生成分子量更大的产物。反应机理如图1-1所示。

图1-1 煤直接液化反应机理
根据图1-1,可以得出如下几点结论。
①煤的组成是不均一的,其中的低分子化合物容易被液化,可不经沥青质而直接转化为液体产物,而另一些惰性组分如丝质组则基本上不能液化。
②反应基本上以顺序反应为主,液化的主反应是煤先转变为沥青质,再由沥青质转变为小分子的液化油和其他产物。
③煤在液化过程中,首先共价键热解生成自由基,自由基在获得活泼氢后生成稳定的小分子液体产物。当温度过高或者供氢不足时,缩聚等副反应相继发生,自由基碎片之间发生缩聚,而且沥青质也会缩聚形成焦。所以,在煤液化过程中氢的供给对煤液化油的产率有很大关系。
1.2.4 液化产物的分离及计算
煤液化产物是一种包括气、液、固三相的混合物系。从低沸点到高沸点,分子量分布很广。
1.2.4.1 煤液化产物分离
煤液化产物分离装置一般有两种:一种是真空蒸馏装置;另一种是溶剂抽提分离装置。溶剂抽提分离是利用物质在不同溶剂中的溶解度不同来进行分离的。
实验中所采用的抽提装置即索氏抽提器,其分离原理是利用抽提溶剂的回流与虹吸,对所需分离的物质进行连续不断的溶剂萃取。煤液化产物分级萃取一般采用的是250mL索氏抽提器。抽提溶剂依次为正己烷、苯和四氢呋喃(THF)。具体操作方法是:将液化得到的液化产物和用于清理反应釜的脱脂棉放入事先折好的与索氏提取器的大小相匹配的滤纸套中,然后依次以正己烷、苯和四氢呋喃为抽提溶剂对其进行抽提。加热开始后,经蒸发变为气态的溶剂从烧瓶进入到冷凝管中,经冷凝后回流到滤纸套中,与液化产物混合,对其进行溶解萃取,当抽提器中的溶剂高度高于虹吸管时,溶剂就会和所抽提的物质一同从侧面的虹吸管流入底部的烧瓶中。如此反复循环,依次实现对液化产物中不同组分的萃取分离。每一步溶剂抽提分离后,都要把实验后的滤纸套放入烘箱干燥,并放入干燥器中冷却,然后称重。记录每次的称量结果,以计算相应组分的转化率。
根据产物在不同抽提溶剂中的溶解性,将其划分为残渣、前沥青烯、沥青烯和油。液化产物中仅溶于正己烷的部分定义为油组分;不溶于正己烷却溶解于苯的部分定义为沥青烯组分;不溶于苯而溶于四氢呋喃的部分定义为前沥青烯;四氢呋喃不溶物定义为液化残渣。煤液化产物的分离流程如图1-2所示。

图1-2 煤液化产物分离流程
1.2.4.2 煤液化转化率的计算
气产率定义为反应前后釜加物料总重减少的百分比;油产率定义为正己烷可溶物占干燥无灰基煤的百分比;沥青烯产率定义为苯可溶物占干燥无灰基煤的百分比;前沥青烯产率定义为四氢呋喃可溶物占干燥无灰基煤的百分比;残渣产率定义为最后的四氢呋喃不溶物占干燥无灰基煤的百分比。
煤液化转化率的计算公式如下:
(1-1)
其中,反应前原料未包括H2,反应后产物指反应后釜中的物质。
(1-2)
(1-3)
(1-4)
(1-5)
1.2.4.3 煤液化产物的分析
目前用于分析煤直接液化原料及产物的分析手段:对于原料及液体产品的分析一般有元素分析、黏结性、分子量、分子量分布分析,采用1H核磁共振波分析芳香氢分布及氢分布,用13C核磁共振分析芳香碳含量及碳分布,组分鉴定采用气相、液相色谱-质谱联用,官能团鉴定采用薄层色谱与红外吸收光谱,同系物碳原子数测定采用高分辨质谱,轻组分化合物鉴定采用气相色谱分析手段等。