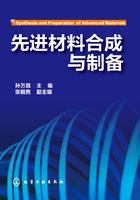
1.2 智能材料与形状记忆合金
1.2.1 智能材料的发展
智能材料是近年来在世界上兴起并迅速发展的材料技术的一个新领域。设想一下,如果大坝能自己发现混凝土结构里的裂缝;玻璃能根据环境光强的变化而自行改变透光率,使进入室内的阳光变暗或变亮;墙纸可以变化颜色以适应不同环境;空中飞行的飞机能自行诊断其损伤状态并自行修复,等等。这就是给这些材料、结构赋予了仿生的功能,使它们具有了“智能”,这种类型的材料就称为智能材料。这种智能材料是能对环境有感觉并产生反应的流体、合金、玻璃、陶瓷、高分子有机物等。它们可使大坝感知混凝土构件的裂缝并能在破裂前发出警报,在飞机机身上覆盖探测疲劳的智能光纤材料,能预知飞机及其构件的损伤,它们能自己诊断损伤甚至自己修复,以延长构件寿命,保证构件的安全。
智能材料是高技术新材料领域中正在形成的一门新的分支学科,是21世纪的先进材料。智能材料是当前工程学科发展的国际前沿,材料的“智能化”是一项具有挑战性的课题,要求材料本身具有生物所具有的高级功能,如对环境和各种信息的感知功能、自诊断和预警能力,自适应和自修复功能等。智能材料是一门交叉学科,它的发展不仅是材料学科本身的需要,而且可以带动许多相关学科的发展,也是国民经济建设发展的需要。目前各国有一大批各学科的专家和学者正积极致力于发展这一学科,其中包括化学家、物理学家、材料学家、计算机专家、土木工程和航空领域的专家等。
智能材料概念是美国和日本科学家首先提出的,1989年日本高木俊宜教授将信息科学融于材料的特性和功能,提出智能材料( intelligent materials)概念,它是指对环境具有可感知可响应等功能的新材料。美国的R.E.Newnhain教授提出了灵巧(smart)材料的概念,这种材料具有传感和执行功能,他将灵巧材料分为被动灵巧材料、主动灵巧材料和很灵巧材料三类。此后,每年国际上都有大量文章和专利发表。智能材料应用范围越来越广,现已发展成为当代高新技术领域里的一项重要研究内容。
1.2.2 智能材料的基本概念
所谓智能材料是指同时能够感知外部环境条件的变化(传感器功能),作出自己的判断(信息处理器功能)以及发出指令或自行采取行动(执行器功能)的材料。这种材料一般具有四种主要功能:
①对环境参数的敏感;
②对敏感信息的传输;
③对敏感信息的分析、判断;
④智能反应。
早期的智能材料往往是一种材料集上述四种功能于一身,因此种类极少,而且适应面很狭窄,功能单一,例如形状记忆合金(SMA)智能材料,就集上述四种功能于一体。随着科学技术的不断发展,尤其是20世纪80年代光纤传感技术和微电子技术的高速发展,给智能材料注入了新的活力和概念,科技工作者开始对智能材料的四种功能分别进行处理,分别按需要进行设计,制造多种性能优越的智能材料。因此,智能材料往往不是研制一种材料使之具备多种智能特性,而是根据需要在所使用的基体材料中融入某种新的材料和器件,这种融入的材料或器件一般具有某种或多种智能特性,这样使智能材料的性能和应用得到了很大扩展,它可以根据人们的需要来设计和制作具有多种智能属性的智能材料,它的智能特性不是在单一材料中予以表现,而往往是在最终结构体中才得以表征。
与智能材料有关的特性很多,下面对一些主要特性加以介绍。
(1)敏感特性
融入材料使新的复合材料能感知环境的各种参数及其变化。可供融入的材料很多,但必须具备对环境不同参数的敏感特性。例如常用的光导纤维传感器,就具备对多种参数的敏感特性。因为它不仅与各种复合材料有较好的相容性,而且光纤传感技术的发展使得光导纤维本身就可以制成能检测力、热、声、光、电等物理参数的几百种传感器;它体积小,种类多,能测量多种物理参数及其分布状况,是一种较理想的基础智能材料。目前常用的具有敏感特性的智能材料还有形状记忆合金、压电陶瓷等。
(2)智能特性
智能特性是智能材料的核心,也是智能材料与普通功能材料的主要区别,智能材料与结构除了能敏感传输环境参数外,还应能分析判断其参数的性质与变化,具有自学习、自适应等功能。经过学习和“训练”的智能材料能模仿生物体的各种智能,由于计算机技术的高度发展,智能材料与结构的智能特性已经或正在逐步实现,问题的关键是如何将材料敏感的各种信息通过神经网络传输到计算机系统。现在一般有两种方法:一种是在大型智能结构系统中,将智能材料敏感到的各种参数传感到结构体系的普通计算机内;另一种是在智能材料中埋入超小型电脑芯片,国外已研制成的这类芯片比人体血管还细。总之材料的“智能化”是一项十分有意义的工作,许多研究目前才刚刚开始,前景是十分诱人的,有待广大科技工作者努力工作,相信不久以后,具有更高智能特性的智能材料和结构将会产生。
(3)传输特性
智能材料不仅需要敏感环境的各种参数,而且需要在材料与结构中传递各种信息,其信息传递类似人的神经网络,不仅体积微小,而且传递信息量特大。目前用于智能材料中信息传递的方法很多,最常用的是用光导纤维来传递信息。据医学专家介绍,光导纤维的构造和人的神经构造相近,国外很多报道也把融入智能材料中的光纤比作为玻璃神经网络。
(4)自适应特性
这个特性主要是由智能材料中的各种微型驱动系统来实现的。该系统由超小型芯片控制并可做出各种动作,使智能材料自动适应环境中应力、振动、温度等变化或自行修复各种构件的损伤。目前常用的微型驱动系统有形状记忆合金、磁致伸缩材料、电流变体等。尤其是电流变体材料在自适应材料中的应用特别引人注目。
(5)相容性
相容性的内容很多,原则上是以埋置的材料性质与原构件的材料基质的性质越相近越好。下述几种相容性是最需要考虑的。
①强度相容 埋置材料不能影响原材料的强度或者说影响很小。例如,在混凝土中埋入少量碳纤维,它不仅不会影响原混凝土的强度,还有增强作用。而埋入碳纤维的混凝土可能具有多种敏感特性。
②界面相容 埋入材料的表面和原材料有相容性。例如,在智能复合材料中常需埋入光导纤维,由于普通复合材料中有玻璃纤维,因此它们有良好的相容性,但在碳纤维复合材料中必须将埋入的光导纤维表面碳化处理,它们才有较好的界面相容性。
③尺寸相容 埋入材料或器件和原材料构件相比,体积应很小,不影响原构件特性。光导纤维体积很小(直径仅几十微米),是目前机敏复合材料中最常采用的埋入材料。
④场分布相容 埋入材料与器件不影响原材料构件各种场分布特性,如应力场、振动模态等。
1.2.3 智能材料的分类
依据智能材料的内涵,按照组成智能材料的基材来划分,智能材料可分为以下几种。
(1)无机非金属系智能材料
无机非金属系智能材料主要包括压电陶瓷、电致伸缩陶瓷、电(磁)流变体等。
(2)高分子系智能材料
由于人工合成高分子材料的品种多,范围广,所形成的智能材料因此也极其广泛,其中智能凝胶、药物控制释放体系、压电聚合物、智能膜等是高分子智能材料的重要体现。
(3)金属系智能材料
金属智能材料,主要指形状记忆合金材料(SMA)。形状记忆合金是一类重要的执行器材料,可用其控制振动和结构变形。形状记忆是热弹性马氏体相变合金所呈现的效应,金属受冷却、剪切由体心立方晶格位移转变成马氏体相。形状记忆就是加热时马氏体低温相转变至母相而回复到原来形状。
从智能材料的自感知、自判断和自执行的角度出发,智能材料又可分为自感知智能材料(传感器)、自判断智能材料(信息处理器)以及自执行智能材料(驱动器)。
1.2.4 形状记忆合金智能材料
1.2.4.1 形状记忆合金发展概述
形状记忆合金(shape memory alloy,简称SMA)是一种具有感知和驱动功能的新型功能材料。形状记忆效应(shape memory effect,简称SME)最早是美国学者A.Olander于1932年在研究Au-Cd合金时发现的。1938年,美国哈佛大学的A.B.Greninger和V.G.Moonradian在Cu-Zn合金中同样发现了马氏体的热弹性转变。1949年,前苏联的V.G.Kurdjumov等对Cu-Al-Ni和Cu-Sn合金的热弹性马氏体转变进行了研究,从热力学角度讨论了可逆转变的热弹性马氏体。1963年,美国海军武器实验室(Naval Ordinate Laboratory)的W.J.Buchler博士研究小组系统地研究了Ti与Ni原子比接近1∶1的合金的形状记忆现象,并揭示出记忆效应的巨大应用价值,奠定了记忆合金的重要地位。首例应用:20世纪70年代初,美国工程技术人员利用TiNi合金研制了具有记忆特性的管路接头,成功解决了F14战斗机同种和异种金属液压管路的快速连接问题。正是记忆合金材料的成功应用引起了人们的关注和兴趣,1975年以后,形状记忆合金作为一种新型的功能材料被人们发展成为一个独立的学科分支,世界各国学者和工程技术人员进行了广泛的基础研究和应用开发研究,并取得了巨大进展。到目前为止,形状记忆合金在应用开发中申请的专利己逾万件,在市场上付诸实际应用的例子已超过数百种。
1.2.4.2 形状记忆合金的特性
形状记忆效应和超弹性是形状记忆合金的两个基本特性。形状记忆合金的这两个基本特性都是和一种可逆的马氏体相变分不开的,这种可逆的马氏体相变和温度有着密切的关系,被称为热弹性马氏体相变。
(1)形状记忆效应
形状记忆效应是指一定形状的合金材料在一定条件下经一定塑性变形后,当加热至一定温度时又完全恢复到原来形状的现象,即它能记忆母相的形状。
如果对材料进行特殊的时效处理和热-机械训练,则在随后的加热和冷却循环中,能够重复记住高温状态和低温状态的两种形状,称为双程形状记忆效应。大多数记忆合金经过适当的工艺处理,都会呈现出双程形状记忆效应。
某些材料在实现双程形状记忆的同时,继续冷却到更低温度,可以出现与高温时完全相反的形状,称为全程形状记忆效应。
以某种TiNi合金为例来比较三种形状记忆效应的异同见表1-1。
表1-1 三种不同的形状记忆效应

(2)超弹性(相变伪弹性)
产生热弹性马氏体相变的形状记忆合金,在Af温度以上诱发产生的马氏体只有在应力作用的条件下才能稳定地存在,应力一旦解除,立即产生逆相变,回到母相状态,在应力作用下产生的宏观变形也随着逆相变而完全消失。其中应力与应变的关系表现出明显的非线性,这种非线性弹性和相变密切相关,所以叫做相变伪弹性(transformation pseudoelasticity),也叫超弹性。
通常材料在弹性极限之内,应力和应变呈线性关系。但对于某些形状记忆合金,应力-应变曲线完全不呈线性关系,其产生的原因是由于应力诱发马氏体相变(stress induced martensitic transformation,简称SIM)及其逆相变。马氏体的产生,除了热诱发之外,还可以通过应力来诱发。在As温度以上,母相在应力的作用下,可以发生应力诱发马氏体相变,从而能产生较大的变形,在应力去除之后,由于母相是热力学稳定的状态,在应力作用下存在的马氏体发生逆相变,回到母相的状态,所产生的宏观变形也随之消失。
(3)形状记忆效应和超弹性的关系
图1-6给出了形状记忆效应和超弹性效应之间的关系。

图1-6 形状记忆效应和超弹性区示意图
图1-6中,正斜率直线表示诱发马氏体的临界应力,负斜率直线表示临界滑移应力。一般来说,只要临界滑移应力足够高,则在同一试样中,依据试验温度不同形状记忆效应和超弹性均可观察到。在温度低于Mf点的范围,表现出形状记忆效应。如果变形温度在Mf~As之间,施加外力则导致应力诱发马氏体形成。卸除外力后,由于温度低于As,马氏体不能逆转变回母相,则需要加热升温至Af以上,马氏体才能完全逆转变回母相。因此,在Ms~As之间合金仍呈现形状记忆效应。温度在As~Af之间时,施加外力导致应力诱发马氏体形成,卸除外力后,由于温度介于As~Af之间,只能有一部分马氏体逆转变回母相。因此,在As~Af之间合金既不呈现完全的形状记忆效应,也不呈现完全的超弹性效应。当温度高于Af时,表现出超弹性效应。需要指出的是,无论在哪种情况下,施加的应力都不能超出滑移临界切应力(A),若超出,合金会发生塑性变形,形状记忆效应和超弹性效应就会同时被破坏。另一方面,若合金的滑移临界切应力很低,如图1-6中的虚线(B)所示,则在未达到诱发马氏体所需的应力之前,先发生塑性变形,这种情况下,合金没有超弹性效应或只能呈现部分超弹性效应。
1.2.4.3 形状记忆效应的机理
(1)热弹性马氏体相变
在金属的马氏体相变中,根据马氏体相变和逆相变的温度滞后大小(即As~Ms)和马氏体的长大方式大致分为热弹性马氏体相变(thermoelastic martensitic transformation)和非热弹性马氏体相变。
普通铁碳合金的马氏体相变为非热弹性马氏体相变。其相变温度滞后非常大,约为几百摄氏度。各个马氏体片几乎是在瞬间就长到最终大小,且不会因温度降低而再长大,相变过程是以在未相变的母相领域内生成新的马氏体的形式进行的。
形状记忆合金的马氏体相变属于热弹性马氏体相变(但具有热弹性马氏体相变的材料并不都具有形状记忆效应)。其相变温度滞后比非热弹性马氏体相变小一个数量级以上,有的形状记忆合金只有几摄氏度的温度滞后。冷却过程中形成的马氏体会随着温度的变化而继续长大或收缩,母相和马氏体相的相界面表现出弹性式的相界面推移,在相变的全过程中一直保持着良好的协调性。
(2)微观机理
热弹性马氏体相变过程中,当具有较高对称性的母相(奥氏体相)降低温度转变为低对称性的马氏体相时,在母相内会生成许多惯习面指数不同,但在晶体学上等价的马氏体,称为马氏体变体,马氏体变体一般有24种。两种或几种马氏体变体形成马氏体片群,马氏体片群中的各个变体的位向不同,有不同的应变方向。每个马氏体变体形成时,会在周围的基体中造成一定方向的应力场,使沿该方向的变体长大越来越困难。新的马氏体变体形成时会沿阻力小、能量低的方向生长,这样变体之间的应力场互相抵消,使片群整体的应变量几乎为零。由于马氏体相变具有这种自适应性,所以在宏观上没有变形。
在低温时施加应力,相对于外应力有利的变体择优长大,不利的变体缩小,这样通过重新取向造成了试样宏观形状的改变。当外力去除后,试样除了回复微小的弹性变形外,其形状基本保持不变。只有将其加热到As温度以上,由于热弹性马氏体在晶体学上的可逆性,逆相变可以完全回复原来的母相晶体,宏观变形完全消失,因此试样也就回复到原来的形状,这就是形状记忆的基本原理(见图1-7)。

图1-7 形状记忆效应原理示意图
L—初始形状;ε—塑性变形
图1-8所示为马氏体形变与加热后的形状记忆回复。图1-8(a)所示为母相状态下材料的宏观形状;图1-8(b)所示为冷却到Mf以下,生成了一组晶体结构相同而取向不同的马氏体变体(这里只表示了两种取相的变体),根据自适应现象,宏观形状大体不变;对这种马氏体施加外部应力时,相对于外应力有利的变体将择优长大,不利的变体缩小,变体重新取向,相互吞食,变体界面移动,形成马氏体单晶,从而发生宏观变形[见图1-8(c)和图1-8(d)],经过这样变形的合金被加热到Af以上将发生逆相变,并返回到原来母相的形状[见图1-8(e)]。

图1-8 形状记忆效应的变形过程
呈现形状记忆效应的合金应具备以下条件:马氏体相变是热弹性的;马氏体点阵的不变点阵切变为孪变,亚结构为孪晶或层错;母相和马氏体均为有序点阵结构。
1.2.5 形状记忆合金的种类
目前材料科学工作者投入大量精力研究的、在工业上具有实用(或潜在实用)价值的形状记忆合金(SMA)主要有三类,即Ti-Ni基合金、Cu基合金和Fe基合金。另外,近年发现一些聚合物和陶瓷材料也具有形状记忆效应,其形状记忆原理与合金不同,还有待进一步研究。
1.2.5.1 Ti-Ni基形状记忆合金
Ti-Ni基合金是最早发展的记忆合金,它不仅具有独特的形状记忆效应和超弹性,还具有良好的机械性能和优异的生物相容性、耐腐蚀性,在实际中得到大量应用,从而成为形状记忆合金家族中的佼佼者,是当今最具实用性的、性能最好的形状记忆合金系列,但制造过程较复杂、价格昂贵。
在Ti-Ni二元合金系中有TiNi、Ti2Ni和Ni3Ti三个金属间化合物。Ti-Ni基记忆合金就是基于TiNi金属间化合物的合金。此类合金的记忆性能与其成分配比、加工工艺和热处理条件等有密切的关系。如加入不同的合金元素可以显著影响Ti-Ni合金的相变乃至记忆效应。Cu在Ti-Ni合金中固溶度可高达30%,在Ti-Ni合金中加入一定量的Cu置换Ni后,合金的形状记忆效应、力学性能仍然很好,而合金的价格可降低很多。与Cu的作用相反,在Ni-Ti合金中加入一定量的Nb,可以得到很宽滞后的记忆合金。与Ni-Ti-Cu合金不同的是,Nb不是以置换原子的方式溶入NiTi相的点阵中,也没有与Ni或Ti原子形成第二相,而主要是以纯Nb相弥散分布在NiTi基体中。由于Nb相很软,在施加应力使马氏体变形时,Nb相也相应地发生塑性变形,逆转变时,马氏体的变形是可回复的,而Nb相的变形是不可回复的,且Nb相的变形对马氏体的逆转变有阻碍作用,从而导致逆转变温度显著升高,得到宽滞后的记忆合金。添加Fe可使合金显现出明显的R相变,此时合金的相变过程明显分为两个阶段,即冷却时母相(B2结构)首先转变为R相,进一步冷却又使R相转变为马氏体,加热时的相变过程则相反。此外,通过不同的处理工艺可分别获得单程、双程或全程记忆效应。
1.2.5.2 Cu基形状记忆合金
Cu基形状记忆合金是继Ti-Ni合金之后又一种实用性较强的形状记忆合金,主要由Cu-Zn与Cu-Al两个二元系发展而来,其中Cu-Al-Ni基和Cu-Zn-Al基形状记忆合金是最主要的两种记忆合金,它们最大的特点是形状记忆效应好,价格便宜,易于加工制造。但也存在一些问题,主要是疲劳寿命短、热稳定性差以及记忆恢复性能易衰退等。与Ti-Ni记忆合金相比,Cu基形状记忆合金的强度较低,稳定性、疲劳强度差,疲劳寿命短,且不具有生物相容性,主要原因是:①Cu基合金的各向异性因子(A≈13)比Ti-Ni合金(A≈2)大得多,这样在弹性区域内造成大的应力集中;②Cu基合金晶粒尺寸(毫米量级)比Ti-Ni合金(数十微米)大几个量级,使得变形时很容易产生应力集中而导致晶界开裂。因此,阻止Cu基记忆合金的晶间断裂,提高其塑性和疲劳寿命,最主要的方法就是细化晶粒。例如:Cu-Zn-Al合金经β相区固溶处理后平均晶粒尺寸约为1mm,加入质量分数为0.01%的硼后晶粒尺寸降至约0.1mm,加入质量分数为0.025%的硼后晶粒尺寸降至约50μm。晶粒细化后,Cu基记忆合金的力学性能有显著的改善,例如:晶粒尺寸由160μm细化至60μm时,断裂伸长率提高40%,疲劳寿命延长10~100倍,同时合金的记忆效应保持良好。
1.2.5.3 Fe基形状记忆合金
Fe基形状记忆合金分为两类:一类是基于热弹性马氏体相变;另一类是基于非热弹性可逆马氏体相变。Fe基记忆合金具有强度高、易于加工成形等优点。具有热弹性可逆马氏体相变的铁基形状记忆合金主要有Fe-Pd、Fe-Pt和Fe-Ni-Co-Ti。前两个由于含有贵金属Pd(原子数比例约30%)和Pt(原子数比例约25%),工业应用的价值不大。Fe-Ni-Co-Ti合金进行793K时效30min的预处理,即可获得热弹性马氏体相变。但是该合金由于含有较多的Co,价格依然偏高,更为不利的是其马氏体相变温度太低(Ms约为200K),使其应用受到限制。
在Fe-Mn-Si合金中,由于冷却形成的马氏体是非热弹性的,马氏体变体不能在外力作用下发生再取向,因此不能像热弹性马氏体那样在马氏体状态下通过再取向变形,然后在加热过程中通过逆转变使变形消失来实现形状记忆效应。一般情况下,Fe-Mn-Si合金的最大回复应变量不超过2%,超过后将会产生较大的不可回复的应变。显然,较低的可回复应变量是制约Fe基记忆合金工程应用的难点之一。为提高材料的可回复应变量,热机械处理或训练(使材料经历一定变形,在高于奥氏体转变结束温度加热后再冷却到马氏体转变结束温度以下,如此反复多次)工艺的研究目前受到关注。研究表明:Fe-28%~33%Mn-5%~6%Si成分范围内的合金具有较好的记忆效应,同时其Ms点在室温附近,对于在常温下使用十分有利。与Fe-Mn-Si类似,Fe-Cr-Ni-Mn-Si-Co合金也具有较好的记忆效应,其可回复变形高达4%,合金的Ms点在173~323K之间,而且耐蚀性优良。
1.2.6 形状记忆合金的制备方法
制备TINi形状记忆合金的传统方法是真空熔铸法,这种真空熔炼的温度一般要超过基体金属熔点150~300℃,用于熔炼TiNi合金的设备有自耗电极电弧炉、非自耗电极电弧炉、电子束炉、等离子弧和等离子束炉及感应熔炼炉等。该方法简单,工艺成熟,但合金元素极易挥发,因而其相变点很难控制(马氏体相变温度强烈依靠合金成分);此外,该工艺对晶粒大小也难以控制,制备的多晶记忆合金晶粒容易长大,导致合金脆性增大。
粉末冶金方法克服了传统熔铸法易产生成分严重偏析的现象,使合金成分均匀,并可制备形状复杂、加工困难的元件,减少加工工序,获得近终形产品。因此,粉末冶金方法可被应用于合成TINi形状记忆合金,包括致密的和多孔的TINi形状记忆合金。粉末冶金方法的工艺是,金属粉末的制备、粉末压制成压坯、压坯在不超过基体组分熔点的温度下烧结、烧结试样的后处理。用粉末冶金法制取TiNi合金的主要目的是降低合金的成本。
自蔓延高温合成技术(SHS)也称燃烧合成技术,已被用来制备出高孔隙度的多孔TiNi合金。该技术是基于放热化学反应的基本原理,利用物质反应热的自传导作用,使反应持续进行,蔓延至整个体系,最终合成所需要的材料。SHS技术的优点是节能、省时,投资少,产品纯度高;缺点是反应过程难以控制,产品性能不稳定。
目前用溅射法、脉冲激光沉淀法制备出了记忆合金薄膜。日本采用球磨纯TiNi金属,然后按比例混合均匀,在压力下拉拔出合金丝。TiNi合金在微执行元件中的大量应用要求制备出合格的超薄板、细丝、细管。
Cu基形状记忆合金由于易发生沿晶界的脆性断裂,所以一般使用寿命不长,要改变这一缺点主要有以下两个途径:①细化晶粒;②强化织构。细化晶粒的方法有变质处理、快速凝固、粉末冶金、控制再结晶等。目前主要采用添加稀土元素及B、Ti、V等方法来细化晶粒,已获得了显著的效果,晶粒尺寸可有效地控制在60μm左右,同时明显改善了合金的加工性能。利用快速凝固法可获得非晶态或微晶铜基形状记忆合金,但是合金在800℃以上加热时,其晶粒很快长大。采用粉末冶金法制备的Cu-A1-Ni合金的晶粒尺寸熔铸法的1%,同时它的塑性、记忆性能均明显改善,相变点也相应提高。强化织构可以通过冷塑性变形和二次再结晶等方法来实现。金属冷塑性变形时,晶体要发生转动,使金属晶体中原为任意取向的各晶粒逐渐调整到取向彼此趋于一致,这就形成了晶体的择优取向,即变形织构。变形量越大,择优取向程度越大。因为各晶粒沿织构的取向基本一致,所以在这一方向上进行塑性变形时,不易在晶界上产生应力集中,继而产生裂纹的机会也少,故金属沿这一方向的塑性就比较好。因此,具有强化织构组织的金属,在某一特定取向,会有很好的疲劳性能和机械性能。例如,通过控制材料的凝固过程,可以直接得到所需要晶粒取向的柱状晶甚至单晶,这就是一种特殊的、更为直接有效的强化织构的方法。Cu基记忆合金柱状晶和单晶的制备及性能研究已经证实,单晶化可以大幅度提高形状记忆性能、疲劳性能和机械加工性能。
利用机械合金化制备的铜基形状记忆合金主要是Cu-A1-Ni、Cu-Zn-A1和Cu-Al-Nb系合金。如在制备Cu-Zn-Al合金时可以避免Zn在熔炼时的挥发,获得性能稳定的Cu-Zn-Al形状记忆合金。