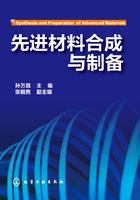
第1章 新型合金材料的制备
1.1 非晶态合金
1.1.1 非晶态合金发展概述
自然界中,物质存在着三种聚集状态,即气态、液态、固态。固态物质又有两种不同的存在形式,即晶体和非晶体。在晶体中原子、分子或离子在三维空间进行有规律的周期性排列。与此相反,有些物质的原子或离子并没有规律和周期性,是无序排列的,这种物质称为非晶态物质,非晶态物质又称“无定形”物质(amorphous),是相对晶态而言的。
非晶态材料包括非晶态合金、非晶态半导体、非晶态超导体及非晶态聚合物。本节内容仅限于讨论非晶态合金。
非晶态合金又称金属玻璃,即非晶态合金具有金属和玻璃的特征。首先,非晶态合金的主要成分是金属元素,因此属于金属合金;其次,非晶态合金又是无定形材料,与玻璃相类似,因此称为金属玻璃,是新型材料研究的热点之一。非晶态合金具有优异的力学性能(高的强度、硬度等),耐腐蚀性能,软、硬磁性能以及储氢性能等,在机械、通信、航空航天、汽车工业乃至国防军事领域都具有广泛的应用潜力。因此,开发块体非晶态合金成为这类材料实用化的重点。
世界上有关非晶态合金研究的最早报道,是1934年德国物理学家Kramer采用蒸发沉积的方法成功制备出了非晶态薄膜,自此,非晶的研究逐步开展。1951年,美国物理学家Turnbull通过水银的过冷实验,提出液态金属可以过冷到远离平衡熔点以下而不产生形核与长大,达到非晶态,Turnbull是非晶态合金的理论奠基人。
1960年Duwe等采用熔体快速冷却方法首先制备出Au-Si非晶态合金,虽然其在室温下呈不稳定状态,但由于其独特的无序结构,且兼有一般金属和玻璃的特性,引起了科研界人士的广泛关注和极大的兴趣,成为非晶态金属实验制备的先驱。20世纪70~80年代期间,非晶态合金的研究得到了极大的发展。不同体系和种类的非晶态合金先后问世,大量的关于非晶态合金的制备和应用的数据得以积累。但由于理论和相关工艺设备的限制,制备非晶态合金的冷却速率一般仍需106K/s以上,得到的非晶态制品外形大多仍为薄膜、细丝、条带及粉末状,很大程度上限制了非晶合金的应用。20世纪80年代后期,A.Inoue等在日本东北大学成功发现了La-Al-Ni和La-Al-Cu等三元合金。此后,又制备了厘米级的四元和五元块体非晶态合金。1997年,Inoue小组通过用Cu代替30%Ni,研制出了Pt-Cu-Ni-P合金系,该合金系被认为是具有最好玻璃形成能力的合金系。2000年Inoue课题组又成功研发了高强度Cu-Zr-Hf-Ti和Co-Fe-Ta-B块体非晶态合金。总之,到目前为止,已开发的非晶态合金体系有Mg—基、Zr—基、Pd—基、La—基、Cu—基、Fe—基、Ni—基、Nd—基、Ti—基、Co—基等,为块状非晶的发展提供了重要的研究基础。
1.1.2 非晶态合金的基本特征
①各向同性。非晶态材料各个方向的性质,如硬度、弹性模量、折射率、热膨胀系数、热导率等都是相同的。各向同性是材料内部质点无序排列而呈统计均质结构的外在表现。
②介稳性。玻璃是由熔体急剧冷却而得,由于在冷却过程中黏度急剧增大,质点来不及进行有规则的排列,系统的内能尚未处于最低值,因而处于介稳状态,在一定的外界条件下,仍具有自发放热转化为内能较低的晶体的倾向。
③无固定熔点。玻璃态物质由固体转变为液体是在一定温度区间(转化温度范围内)进行的,与结晶态物质不同,无固定的熔点。
④物理、化学性质随温度变化的连续性和可逆性。非晶态材料由熔融状态冷却转变为固体(玻璃体)是渐变的,需在一定温度范围内完成,其物理、化学性质的变化是连续的、可逆的。
⑤没有任何长程有序,只存在小区间内的短程有序。非晶态固体结构上的特征是原子排列缺乏周期性。虽然在某一原子周围原子排列有一定规律性,但整体来讲则是缺乏规律性的,即所谓短程有序、长程无序。
⑥衍射花纹是由较宽的晕和弥散环组成的,在电子显微镜下看不到晶粒、晶界、晶格缺陷等。
1.1.3 非晶态合金的形成条件和玻璃形成能力评价标准
1.1.3.1 非晶态合金形成的热力学和动力学条件
熔融状态的液体合金在固化的过程中一般有两种途径。如果液态合金在凝固点附近被冻结,则会形成晶态合金。随着液体冷却速率的提高,过冷度急剧增大,因此发生结晶的温度范围大大缩小,原子来不及从容地排列成整齐的有序结构,由此就会产生各种不同的结构。先是显微组织细化,合金中溶质原子的固溶度增大。当冷却速率再次增加时,就会形成亚稳结晶相。最后,当冷却速率足够高时,晶核没有足够的时间生长,甚至来不及成核,由此会形成一种特殊的非平衡凝固现象,即凝固后的合金会保持液相中存在的短程有序和局部原子紧密堆垛的结构,即形成非晶态合金。
(1)非晶态合金形成的热力学条件
从热力学角度来看,过冷熔体由液态转变为晶体时其单位体积吉布斯自由能变化ΔGl-x可表示为:
(1-1)
式中,ΔH f为平衡温度(Tf)时的熔化焓;ΔCl-xp为过冷液体与晶体的比热容差。
ΔGl-x越小,结晶转变的热力学驱动力越小,合金的玻璃形成能力越强。
(2)非晶态合金形成的动力学条件
物质能否形成非晶固体,这与结晶动力学条件有关。已经发现,除一些纯金属、稀有气体和液体外,几乎所有的熔体都可以冷凝为非晶固体。只要冷却速率大于105℃/s或取适当值,就可以使熔体的质点来不及重排为晶体,从而得到非晶体。非晶形成的动力学条件是从运动的观点出发,考虑冷却速率和结晶动力学之间的关系,即考虑需要多高的冷却速率才能阻止成核及核的生长。根据动力学的处理方法,把非晶态的形成看成是由于成核率和生长速率很小,或者看成是在一定的过冷度下所形成的体结晶分数非常小(如10-6)的结果,这样就可以用经典的成核生长理论来讨论非晶态的形成,并定量地确定非晶态形成的动力学条件。
令均匀成核率为I(1/cm3·s),即在单位体积内单位时间所成核的数目,则根据吞布尔(Turnbull)的理论,有
(1-2)
式中,η是黏度;b为形状因子,对于球形核,b=16π/3 ;Tr为约化温度,Tr=T/Tm,Tm为熔点; ΔT=1-Tr;α为每一摩尔界面原子的自由能与结晶潜热之比;ΔS为结晶时的熵变;R为气体常数。
若最大成核率Imax<1,结晶过程就容易被抑制而形成非晶态。由式(1-2)可以看出,成核率和参数a3(ΔS/R)的关系很大,若取η=10-2,并忽略它的温度关系,则当a(ΔS/R)1/5=0.4~0.5时,Imax=1020~1025/cm3·s,有明显的结晶倾向。而当α(ΔS/R)1/5=0.9时,Imax=10-4/cm3·s,可以期望抑制成核而形成非晶态。从α和ΔS/R的定义可以看出,熔化焓大或者固-液相界面张力大都可大大增强形成非晶态的倾向。
1.1.3.2 非晶态合金玻璃形成能力的评价参数
一般来说,人们常用非晶态合金在加热过程中的玻璃转变温度Tg、晶化温度Tx、熔化开始温度Tm和液相线温度Tl之间的组合来表征合金玻璃形成能力(GFA),常用的表征参数如下。
(1)约化玻璃转变温度Trg
Turnbull提出了约化玻璃转变温度Trg(Trg=Tg/Tm)的概念,通常地,Trg越大,合金玻璃形成能力越强。Uhlmann指出Trg来源于对Tg~Tm温度区间内黏度的要求。只有在冷却过程中,黏度足够大,才能使金属原子没有足够时间重新排列,抑制结晶的发生,获得非晶态合金。一般认为,在Tg温度时,黏度等于常数(η=1013p),且Trg越大,在CCT或TTT曲线鼻尖处η值越高,则临界冷却速率Rc越低,合金的玻璃形成能力(GFA)就越高。如果合金Trg值大于2/3,则合金在过冷液相区的均匀形核速率将非常缓慢,从而易于形成非晶相。
(2)过冷液相区ΔT
Inoue等提出ΔTx能够表征玻璃形成能力的观点。所谓过冷液相区ΔTx(=Tx-Tg),是指晶化温度(Tx)和玻璃化转变温度(Tg)之间的温度区域,是表征过冷液体稳定性的一个重要参数。由于块体非晶态合金多组元之间较大的原子尺寸差及负的混合热的作用,使合金晶化相的形核与长大速率被抑制,从而导致合金在晶化前出现了明显的玻璃转变和稳定的过冷液相区。过冷液相区ΔT值与金属玻璃体系的玻璃形成能力有很大联系。一般来说,ΔTx越大,热稳定性越好,形成非晶所需的临界冷却速率Rc越小,合金的玻璃形成能力(GFA)越强。
然而,ΔTx的应用存在一定的局限性。实验表明,合金的玻璃形成能力与ΔTx之间并不存在必然的联系。研究合金的玻璃形成能力时仅仅考虑过冷液体的稳定性是不够的,如在Zr-Ti-Cu-Ni-Be块体非晶体系中,玻璃形成能力与Trg密切相关,而与ΔTx却没有太大的关系。此外,对于一些不具有过冷液相区的非晶态合金,其玻璃形成能力也无法用ΔTx来表征。然而,在超过冷液相区中,金属玻璃大多具有很好的塑性,所以数值较大的ΔT值对于非晶态合金的塑性加工和工业化应用具有非常重要的意义。
(3)γ判据
美国橡树岭国家实验室的Z.P.Lu和C.T.Liu系统研究了金属玻璃的形成及其晶化过程等热力学分析,提出了一个新的参数γ[=Tx/(Tg+Tl)]来评价金属玻璃体系的玻璃形成能力。与传统的判据相比,该参数综合考虑材料的热力学因素和动力学因素,较ΔTx和Trg,能够更好地反映各类非晶态合金的玻璃形成能力。应用回归分析法,他们得出了参数γ和过冷液体的临界冷却速率(Rc)或试样截面的临界厚度(tmax)之间的关系公式:
(1-3)
(1-4)
1.1.4 非晶态合金的制备方法
要获得非晶态,最根本的条件就是要有足够快的冷却速率,并冷却到材料的再结晶温度以下。基于这样的特点,无论哪一类制备方法都要解决以下两个关键技术问题:①必须形成原子或分子混乱排列的状态;②将这种热力学亚稳态在一定的温度范围内保存下来,并使之不向晶态发生转变。
要得到大块非晶态材料,即在较低的冷却速率下也可以制得非晶材料,就要设法降低熔体的临界冷却速率Rc,使之更容易获得非晶相。这就要求从热力学、动力学及结晶学的角度寻找提高材料非晶形成能力、降低冷却速率的方法。
目前,非晶态合金的制备方法大体上可以分为三类:①通过蒸发、溅射、电解等方法使金属原子或离子凝聚或沉积而成;②由熔融合金通过急冷快速固化而形成粉末、丝、条带等;③利用激光、离子注入、喷镀、爆炸等方法使表面层结构无序化。
1.1.4.1 非晶态合金粉末的制备方法
(1)雾化法
利用液氮等低温液体代替一般雾化法制造粉末所用氮气,再用冷却板使合金在雾化同时高速冷却而成为非晶态粉末,后者较难获得球状粉末。
在亚音速范围内,克服液流低的切阻,变成雾化粉末,对高性能易氧化材料往往用氩气雾化法,但气体含量仍高,一般高温合金的含氧量在100~200μg/g。冷却速率也不高,在(102~103)℃/s。粉末质量不高主要因为有较高的气孔率,密度较低,粉末颗粒有粘连现象,即大粉末颗粒粘了小颗粒,使组织不一致,筛分困难,增加了气体沾污。后来又发展了氦气下强制对流离心雾化法,使冷却速率提高至105 ℃/s。在氦气下可比在氩气下获得大一个数量级的冷却速率。目前又发展到了超声雾化法,它是采用速度为2~2.5马赫(1马赫≈340m/s)和频率为2×104~1×105Hz的脉冲超声氩气或氦气流直接冲击金属液流,从而获得超细的雾化粉末,其原理是利用一个带锥体喷嘴的Hartmann激波管,超声波在液体中的传播是以驻波形式进行的,在传播的同时,形成周期交替的压缩与稀疏,当稀疏时在液体中形成近乎真空的空腔,在压缩时空腔受压又急剧闭合,同时产生几百兆帕的冲击波,把熔液打碎。一般是频率愈大,液滴愈小,冷却速率可达105 ℃/s。
(2)旋转液中喷射法
一个高速旋转的冷却体,其内表面在离心力作用下附着一层冷却液,熔融合金喷射到其中而获得非晶态粉末。
(3)双辊法
从图1-1可以看到,熔融的合金通过双辊接触表面快速固化而形成非晶态,当辊速足够大时,在带与相分离区形成较大负压,使已固化的非晶态合金带粉碎成非晶态粉末。此法工艺要求严格,射流应是有一定长度的稳流;射流方向要控制准确;流量与辊子转数要匹配恰当,否则不是因凝固太早而产生冷轧,就是因凝固太晚而部分液体被甩出。关于辊子的选材,既要求导热性能良好,又要求表面硬度高,而且还要适当考虑有一定的耐热蚀性。实际上双辊法获得的是片状非晶粉末。

图1-1 双辊法
1.1.4.2 非晶态薄膜的制备方法
(1)溅射法
溅射法是在位于低压气氛中的2个电极上加上电压,将气体电离,离子冲击原材料表面,使其释放出原子。加在电极上的电压很高,到达衬底的原子动能可达10eV左右,因此,即使对于组元蒸气压相差较大的合金,薄膜也比较致密,且与衬底的黏附性较好。此法的优点是有较高的沉积速率,约1~10nm/s,可得较厚膜,也可以制作合金膜;缺点是由于真空度较低(1.33~0.13Pa),因此容易混入气体杂质,而且基板温度上升快,适于制备晶化温度较高的非晶态材料。
(2)真空蒸发法
在高真空(1.33×10-4Pa)中将预先配制好的材料用电阻、高频感应或电子束等方法加热,使得从表面蒸发出来的金属原子附着到用玻璃等材料做成的基板上,从而制得非晶态薄膜。在蒸发生长非晶态半导体Si、Ge时,基板一般保持室温或高于室温的温度;但在蒸发晶化温度很低的过渡金属Fe、Co、Ni时,一般要将基板降温,例如保持在液氮温度,才能实现非晶化。蒸发制备合金膜时,大多用各组元同时蒸发的方法。此法的优点是设备与工艺比较简单,冷却速率较快,可以制取纯金属非晶态薄膜;缺点是合金品种受到限制,成分难以控制,且蒸发过程中不可避免地夹带杂质,使薄膜的质量受到影响,此外,蒸发沉积速率太慢,约0.5~1nm/s,一般只可以获得厚度小于10nm的极薄膜,且膜的致密度低。
(3)化学气相反应法
化学气相反应法是将反应气体通过加热的基板,使之在基板表面上发生异质反应,或者在基板上的气流中发生均匀反应,生成物在基板上产生沉积。化学气相沉积法适于制备非晶态Si、Ge、Si2N4、SiC、SiB等薄膜。这种方法工艺简便、成本低廉,适用于制备大面积非晶态薄层。
(4)离子注入法
很多种类的原子可以用离子注入法注入多种材料的表面而获得非晶态表层。离子注入法不受组成成分相图的限制而具有很大的成分自由度,相近的成分规律对离子注入法和一般急冷法的合金都有效。把单个原子注入的过程作为热脉冲来考虑,可以得到约1014K/s的有效冷却速率。把离子注入看成是一种表面改善技术,仅仅是因为与靶材料的表层原子连续相碰撞时穿透的离子经受能量的损失。离子注入适于制备非晶薄膜材料。
(5)喷枪法
当降温速率足够快而避免结晶时,熔体的无序状态在固体中得以保持。为了达到更高的冷却速率,需要将熔体与一种具有高导热率的固体接触,一般使用铜等金属。Duwez给出了对这种方法最好的描述,其基本思想是将液体颗粒高速喷射到高热传导的基体上,基体表面呈凹球面,离心力使得液体表面与基体表面良好接触,以便有强的热传导能力。
该方法是将少量的原料(如金属)装入一个底部有一直径为1mm的小孔的石墨坩埚中,通过感应或电阻加热,并在惰性气体中使之熔化,由于金属的表面张力大,所以不至于从小孔中溢出。随后使用冲击波使熔体由小孔中很快地喷出,在铜板上形成数微米级的不定形非晶薄膜,它具有109℃/s的冷却速率,是液体急冷法中冷却速率最快的一种,是早期研究非晶态合金的制备方法之一。
(6)锤砧法
如果用两个导热表面迅速地相对运动而挤压落入它们之间的液珠,则此液珠将被压成薄膜,并急冷成金属玻璃。锤砧法就是按此原则提出来的。用此法制得的薄膜要比用喷枪法制得的均匀,且两面光滑。但冷却速率不及喷枪法的高,一般为105~106℃/s。后来又发展出一种锤砧法与喷枪法相结合的装置。它综合了上述两种方法的优点,所制得的薄膜厚度均匀,且冷却速率快,这样获得的薄膜宽约为5mm,长约为50mm,厚度约为70μm。
(7)辉光放电分解法
这是目前用于制备非晶半导体锗和硅的最常见的方法。将锗烷或硅烷放进真空室内,用直流或交流电场加以分解。分解出的锗原子或硅原子沉积在加热的基板上,快速冷凝在基板上而形成非晶态薄膜。这种方法与一般方法相比,其突出特点是:在所制成的非晶态锗或硅样品中,其电性活泼的结构缺陷低得多。1975年英国敦提大学的Spear及其合作者又将其掺入少量磷烷和硼烷,成功地实现了非晶硅的掺杂效应,使电导率增大了10个数量级,从而引起了全世界的广泛注意。
(8)其他方法
利用激光扫描、等离子喷镀、爆炸等方法可以获得大面积非晶薄膜,但这些方法大多处在初期研究阶段。
1.1.4.3 非晶态合金带材的制备方法
图1-2给出了几种连续制备非晶态合金条带的方法示意图。其基本特征是液体金属的射流喷射到高速运动着的羁绊表面,熔层被拉薄而凝成条带。

图1-2 液体急冷连续制备方法示意图
(1)离心法
如图1-2(a)所示,将0.5g左右的合金材料装入石英管,并用管式炉或高频感应炉熔化。随即将石英管降至旋转的圆筒中,并通入高压气体迫使熔体流经石英管底部的小孔(直径0.02~0.05cm)喷射到高速旋转的圆筒内壁,同时缓慢提升石英管从而可得螺旋状条带。离心法的特点是,由旋转筒产生的离心力给予熔体一个径向加速度,使之与圆筒接触良好。因此,此法最易形成金属玻璃,而且可获得表面精度很高的条带,但条带的取出较困难。本法冷却速率可达到106℃/s。
(2)单辊法
从图1-2(b)可以看到,单辊法是用各种加热方法熔化的母合金,通过一定形状的喷嘴喷射到高速旋转的急冷圆辊面上,主要依靠接触导热,使熔融合金以105~109℃/s的冷却速率高速固化而形成连续的条带。此法工艺较易控制,熔体喷射温度可控制在熔点以上的10~200℃/s ;喷射压力为0.5~2kg/cm2 (表压);喷管与辊面的法线约成14°角;辊面线速度一般为10~35m/s。当喷射时,喷嘴与辊面的距离应尽量小,最好小到与条带的厚度相近。辊子材料最好采用铍青铜,也可用不锈钢或滚珠钢。通常用石英管做喷嘴,如熔化高熔点金属,则可用氧化铝或碳、氮化硼管等。由于离心力的作用,熔体与辊面的热接触不理想,因此,条带的厚度和表面状态不及离心法。此法的冷却速率约为106℃/s,若需制备活性元素(如Ti、Re等)的合金条带,则整个过程应在真空或惰性气氛中进行。对工业性连续生产,辊子应通水冷却。
条带的宽度可通过喷嘴的形状和尺寸来控制。若制备宽度小于2mm的条带,则喷嘴可用圆孔,若制备大于2mm的条带,则应采用椭圆孔、长方孔或成排孔(见图1-3)。条带的厚度与液体金属的性质及工艺参数有关。

图1-3 喷嘴形状示意图
(3)熔体沾出法
当冷却辊紧贴熔体表面高速旋转时,熔体被冷却辊沾出一薄层,随之急冷而成条带,如图1-2(c)所示。此法不涉及上述几种方法中的喷嘴的孔形问题,可以制备不同断面的条带。其冷却速率不及上述方法的高,所以很少用于制备金属玻璃,而常用于制备急冷微晶合金。
(4)熔滴法
如图1-2(d)所示,合金棒下端由电子束加热熔化,液滴接触到转动的辊面,随即被拉长,并凝固成丝或条带。这种方法的优点是:不需要坩埚,从而避免了坩埚的沾污;不存在喷嘴的孔形问题,适合于制备高熔点的合金条带。
1.1.4.4 非晶态合金的其他制备方法
(1)磁悬浮熔炼法
将试样置于悬浮线圈中,如图1-4所示,线圈中的电磁场将使试样产生与外部电磁场相反方向的感生电动势,该感生电动势与外部磁场间的斥力与重力相抵消,从而使样品悬浮在线圈中。同时,试样中的涡流使样品加热熔化,随后让样品在惰性气体保护气氛下冷却凝固。由于磁悬浮熔炼时样品周围没有容器壁,避免了引起的非均匀形核,所以材料的临界冷却速率更低。但是与此同时,由于试样在冷却过程中处于悬浮状态,因而冷速不是很快,增加了材料制备的难度。该方法目前不仅用来研究大块非晶合金的形成,而且广泛用来研究金属熔体的非平衡凝固过程中的热力学及动力学参数,如研究合金溶液的过冷,利用枝晶间距来推算冷却速率,均匀形核率及晶体长大速率等。

图1-4 磁悬浮熔炼装置原理图
(2)静电悬浮熔炼
将样品置于如图1-5所示的负电极板上,然后在正、负电极板之间加上直流高压,两电极板之间产生一梯度电场(中央具有最大电场强度),同时样品也被充上负电荷。当电极板间的电压足够高时,带负电荷的样品在电场作用下将悬浮于两极板之间。用激光照射样品,可将样品加热熔化。停止照射,样品便冷却。该方法的优点在于样品的悬浮和加热是同时通过样品中的涡流实现的。样品在冷却时也必需处于悬浮状态,所以样品在冷却时还必须克服悬浮涡流给样品带来的热量,冷却速率不可能很快。

图1-5 静电悬浮熔炼设备原理图
(3)结晶材料转变法
由结晶材料通过辐照、离子注入、冲击波等方法制得非晶态固体。目前,离子注入技术在金属材料改性及半导体工艺中用得很普遍,在许多情况下是利用了注入层的非晶态本质。高能注入粒子被注入材料(靶)中的原子核及电子碰撞时,能量损失,因此,注入离子有一定的射程,只能得到一薄层非晶态材料。激光或电子束的能量密度较高(-100kW/cm2),用它们来辐照金属表面,可使表面局部熔化,并以4×104~5×106K/s的速率冷却,例如,对Pd91.7Cu4.2Si5.1合金,可在表面上产生400μm厚的非晶层。
(4)低熔点氧化物包裹
将样品用低熔点氧化物(B2O3)包裹起来,然后置于熔器中熔炼,氧化物的包裹起到两个作用:一是用来吸取合金熔体中的杂质颗粒,使合金熔化,这类似于炼钢中的造清;二是将合金熔体与器壁隔离开来,由于包覆物的熔点低于合金熔体,因而合金凝固时包覆物仍处于熔化状态,不能作为合金非均匀形核的核心。这样,经过熔化、纯化后冷却,可以最大限度地避免非均匀形核。
1.1.5 块体非晶态合金的制备
1.1.5.1 块体非晶合金的历史
自1960年美国加州理工学院的Duwez小组采用喷枪技术获得非晶态Au70Si30以来,为了克服非晶态合金制备过程中的形状与尺寸限制,人们在制备大块非晶合金方面做了长期不懈的努力。
1969年,非晶合金的制备有了突破性进展,Pond等用轧辊法制备出长达几十米的非晶薄带。由于受到极高的临界冷却速率的限制,在一段时期内,只能得到丝、粉末或箔材等非晶合金。假如定义毫米尺度作为“块体”,具有毫米级直径的非晶棒首先是由贝尔实验室的Chen于1974年在约103K/s的冷却速率条件下用Pd-Cu-Si熔体得到的。20世纪80年代前期,Turnbull等采用氧化物包覆技术以10K/s的速率制备出了直径为5mm的Pt40Ni40P20非晶锭。1984年,这个小组通过硼酸盐融覆处理Pt-Ni-P熔体将临界厚度增加至10mm,Pt-Ni-P可以被认为是人们开发出的第一块大块金属玻璃。20世纪80年代后期,A.Inoue等在日本东北大学成功发现了主要由普通元素组成的新多组元合金系可以在低冷却速率下形成块体非晶合金。1993年,Johnson等采用铸造的方法制备出Zr-Ti-Cu-Ni-Be合金系,其非晶形成能力已经接近传统氧化物玻璃,其非晶棒的直径最大可达到10多厘米,重达20多千克,临界冷却速率在1K/s左右,大大低于非晶急冷法106K/s的冷却速率。我国哈尔滨工业大学的沈军将Fe基块体非晶合金的尺寸提高到16mm,2004年Johnson在Pt基合金系中发现了具有高压缩塑性的块体非晶合金体系,他们研制的直径为3mm的Pt基合金的压缩塑性达到了20%,突破了过去块体非晶合金压缩塑性一般小于2%的瓶颈。最近,中国科学院金属研究所的Ma等发现了尺寸可达25mm的Mg-Cu-Ag-Pd非晶态合金。目前世界上尺寸最大的稀土基金属玻璃材料——直径为35mm的镧基金属玻璃体系,由浙江大学蒋建中等研制成功。
1.1.5.2 块体非晶合金的制备方法
下面介绍一下制备大块非晶合金的几种常用方法。
(1)粉末冶金法
粉末冶金法就是把非晶态粉末装入模具后,进行一定的工艺成型处理,如压制烧结、动力压实、爆炸成型、热挤压、粉末轧制等。采用粉末冶金法制备的块体非晶合金,不仅要密实,而且要避免晶化,其基本原理是利用非晶态固体在过冷液相区ΔTx(即玻璃转变温度Tg与起始晶化温度Tx的间隔)内有效黏度大幅度下降的特性。施加一定的压力使材料发生均匀流变,从而复合为块体。所制备的块体材料在纯度、致密度、尺寸和成型等方面受到很大限制。同时,由于非晶合金硬度高,粉末压制的致密度受到限制。压制后的烧结温度又不能超过非晶粉末的晶化温度(一般在600℃以下),因而烧结后的非晶材料整体强度无法与非晶颗粒本身的强度相比。有时在烧结时加入的黏结剂也会影响非晶合金块体。这些问题都使得粉末冶金大块非晶材料的应用遇到很大困难。
(2)水淬法
将母合金置于一真空石英管中熔化后直接淬入流动的水中,以实现快速冷却,从而制得球状的大块非晶态合金。这个过程可以在封闭的保护气氛系统中进行,也可将合金放在石英管中,将其抽成高真空并密封,利用高频感应装置或者中频感应装置将石英管中的母合金熔化,熔化的母合金和石英管一起快速置于水中急冷,从而形成块体非晶合金。该方法的冷却速率较低,只适于制备玻璃形成能力特别好的合金体系,如:Zr2Al2Cu2Ni、La2Al2Ni等。
(3)落管技术
将合金锭的表层氧化皮去除后,放于落管顶部的带喷嘴的石英坩埚内,落管连同石英坩埚一起被抽真空。使用加热炉将合金加热熔化,然后将熔态合金分散成液滴,使之自由下落(不与管壁接触),并在下落中完成凝固过程,下落样品由位于落管底部的装有冷却剂的容器收集。用落管技术已成功地制备出了Cu2Zr、Pd2Ni2P等块体非晶态合金。同时,可以用落管技术研究非晶相的形成动力学,以及过冷金属熔体的非平衡过程等。
(4)金属模铸造法
金属模铸造是首先采用感应电流将合金熔化,然后通过氩气将液态的合金直接浇入金属模中,利用金属模的导热性好而实现快速冷却,从而获得大块非晶合金。这种方法的特点是工艺过程简单,易于操作,是目前普遍采用的方法之一。但是,金属模的冷却速率有限,所以制备的大块非晶合金的尺寸也很受限制。
(5)电弧熔炼吸铸法
电弧熔炼吸铸法将电弧熔炼合金技术与铜模铸造技术融为一体,是制备大块非晶合金最常用的,也是最方便的一种方法。该方法在制备高熔点的大块非晶合金方面具有其他方法所不能比拟的独特优势。利用铜模优良的导热性能和高压水流强烈的散热效果,可以制备出各种体系的块体非晶合金。将电弧熔炼用的水冷铜盘下面连接铸造非晶棒材的水冷铜模。母合金完全熔化后,上端导入压力为P1的氩气,底部形成P0的负压,打开吸铸阀门,在重力和压力差ΔP=P1+P0的共同作用下,液态母合金从坩埚注入水冷铜模型腔中,从而形成所需形状的大块非晶合金。
(6)定向凝固法
定向凝固法是一种可以连续获得大体积非晶合金的方法。定向凝固有两个主要的控制参数,即定向凝固速率V和固液界面前沿液相温度梯度G。定向凝固法在制备块体非晶合金时,电弧炉包括一个钨阴极电极和一个水冷铜炉,采用电弧作为热源,通过控制钨阴极电极的移动速度,可以连续生产尺寸较长的非晶合金棒。此方法的冷却速率足以抑制Zr基合金中的非均匀形核,使其在较大的尺寸范围内形成非晶合金。Inoue等用此方法制备出Zr60Al10Ni10Cu15Pd5合金,其尺寸达到厚10mm、宽12mm、长170mm。定向凝固法为连续制备大块非晶合金提供了一种可行的方案。
(7)爆炸焊接
爆炸焊接是利用炸药爆炸的能量将多层非晶条带固结成块的高能率加工技术。爆炸焊接可有效清除氧化膜的影响,不必考虑非晶合金条带组成,有足够的冷却速率,可以保证条带的非晶态。同时可以应用于涂层技术,把非晶条带直接焊接到普通金属表面,用于制备耐磨、耐腐材料。爆炸焊接过程中能量大、释放率高,制备出的块体非晶合金易产生宏观裂纹,从而影响其质量,这也是下一步工作中应当解决的问题。
虽然近年来块体非晶合金的研究取得了很大进展,但它仍然属于一种新型材料,在理论研究及实际应用中还有诸多亟待解决的问题,例如:还没有一种成熟的理论指导如何寻找具有较高玻璃形成能力的合金成分;没有成熟的物理模型来解释块体非晶合金的长程无序结构及各组元之间的相互作用形式;块体非晶合金的制备工艺要求苛刻;如何在普通条件下制备块体非晶合金以降低成本;加强块体非晶合金的应用研究开发,等等。
近几十年,块体非晶合金的研究与应用取得了突破性的进展,然而如何在普通条件下制备大块非晶合金以降低制备成本,仍旧是研究人员面临的一个重要课题。目前还没有一种适用于工业生产的大块非晶合金的制备方法,因而开发新的非晶制备方法显得尤为重要。