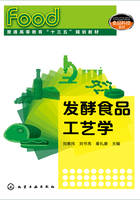
第一节 酱油
一、酱油概述
(一)酱油的定义
酱油是以大豆和/或脱脂大豆、小麦和/或小麦粉为原料,经微生物发酵制成的具有特殊色、香、味的液体调味品。酱油含有大豆多肽、大豆异黄酮、类黑精、大豆皂苷、呋喃酮类物质等生理活性物质。酱油是人们生活中不可缺少的调味品,在烹调时加入一定量的酱油,可增加食物的香味,调整色泽、增加鲜味、促进食欲。
(二)酱油的发展历史
酱油起源于中国,最初是从酱、豉衍变而来。我国人民早在周朝时(约公元前十一世纪到公元前三世纪)就有了酱的生产记载,所用原料为大豆,称为豆酱,酱油则是由豆酱演化而来。
酱的文字记载始见于《周礼·天官》篇:“醢人掌四豆之实,又酱用有百二十瓮。”“膳夫掌王馈,食酱百有二十瓮。”可见酱的生产和食用当时已相当普遍。此后,战国时代《论语·乡党》篇中又有“不得其酱不食”之说。在北魏末年贾思勰所著《齐民要术》中详细记载了豆酱、肉酱和鱼酱的制法,还把制酱用的曲与酒曲相区分,称为“黄衣、黄蒸”。黄衣是用整粒小麦做的曲,黄蒸则是用麦粉做的曲。
中国历史上最早使用“酱油”名称是在宋朝,林洪著《山家清供》中有“韭叶嫩者,用姜丝、酱油、滴醋拌食”的记述。此外,古代酱油还有其他名称,如清酱、酱汁、酱料、豉油、豉汁、淋油、套油等。
公元755年后,酱油生产技术随鉴真大师传至日本。至今日本酱油的生产和食用方法均与我国传统方法相符。目前,日本是仅次于我国的酱油生产、消费和出口大国。千百年来,随着我国侨民移居世界各地,也将酱油的生产和食用方法传播到全世界,使其成为当今全球深受欢迎的调味品。
从酱油出现到20世纪30年代,约三千年生产历史中,我国酱油生产工艺几乎没有改进,一直沿用传统的天然晒露酿造方法,即常压蒸煮原料,自然接种制曲,高盐低温长时间日晒夜露发酵,再压榨提取酱油。
到20世纪30年代初,陈陶声先生等试验成功酱油速酿法,改用廉价原料,以豆饼代替大豆,以麸皮、米糠代替小麦或面粉。选育出高蛋白酶活力的米曲霉菌种进行纯种制曲,缩短了制曲时间。采用保温发酵,大大缩短了发酵周期。将原来的木榨取油改为螺旋压榨机或水压机取油,降低了劳动强度。
1949年以来,酱油生产得到了大力发展。1956年,利用代用原料酿制酱油的方法,并拟定了一套比较完整的稀醪发酵工艺和固稀发酵工艺。1957年重点推广高蛋白酶活力米曲霉菌株中科3.863和固态无盐发酵工艺,并改用浸出法代替压榨法取油,彻底替代了自古以来笨重的取油方法。
1958年,低盐固态发酵工艺迅速推广至全国各地。此后,广东等地普遍采用加压蒸料。到了20世纪60年代末期,酱油生产工艺出现了两个重大改革:一是将传统的浅盘制曲改为厚层机械通风制曲;二是上海酿造一厂研制成功旋转式加压蒸煮锅。
1976年,上海市粮油工业公司酿造实验工厂(上海酿造科研所前身)以中科3.863号米曲霉为出发菌株,通过诱变育种,选育出蛋白酶活力更高、生长繁殖更快的变异株,定名为沪酿3.042号米曲霉,经中科院微生物所审核后统一编号为中科3.951米曲霉。该菌株在全国绝大多数厂推广应用至今。
进入20世纪80年代后,生物化学工程、酶工程和细胞工程、遗传工程以及自动化技术在发酵工业的应用加快了酱油生产工艺改革的步伐。如采用旋转圆盘式自动制曲机,液体深层发酵制液体曲,多菌种混合制曲,选育高蛋白酶活力、淀粉酶活力以及高肽酶活力和谷氨酰胺酶活力的优良菌株等,以提高酱油原料利用率和氨基酸生成率。分离出多株耐盐性乳酸菌和生香酵母菌菌株,并应用于酱油发酵,以提高酱油香气。
近年来,我国酱油产量总体平稳增长,龙头企业规模效益明显。根据中国调味品品牌企业百强统计结果显示,2012~2016年,全国酱油总产量分别为700.42万吨、758.13万吨、938.21万吨、980.21万吨 、1059.43万吨,2016年比2015年增加了8.08%。2016年中国酱油产量省份分布华东地区集中度最高,其次是华北、华中和华南等地。同时,随着市场发展和消费升级,酱油产品消费需求也得到进一步市场细分,目前市场上也出现了多种细分产品,定位于不同人群或不同用途,如儿童酱油、凉拌酱油、火锅酱油、烧菜酱油、寿司酱油、铁强化酱油、海鲜酱油、面条鲜酱油等。
今后,酱油生产在满足市场需要的前提下,应该进一步提高产品质量,降低粮耗和能耗。应用现代科学技术,继续选育优良菌种,深入开展酱油风味形成的基础研究,解决生产周期与酱油风味的矛盾;增加酱油品种,适应消费者需求变化。开展生产协作,将酱油生产工序分解,进行各工序专业厂接力生产,建立多层次的酱油工业体系,改变目前一些厂小而全的状况,以提高全行业的生产技术水平,获得最佳的经济效益和社会效益。
(三)酱油的分类
根据不同的分类标准,酱油有多种分类方法。
1.按酱油用途或颜色分类
根据酱油着色力不同,用途存在差异,酱油可分为生抽和老抽。
(1)生抽酱油 是以大豆、面粉为主要原料,人工接入种曲,经天然露晒、发酵而成。其产品色泽红润,滋味鲜美协调,豉味浓郁,体态清澈透明,风味独特。生抽味道较咸、颜色较淡,故一般用于炒菜或者拌凉菜,起调味的作用。
(2)老抽酱油 是在生抽酱油的基础上,把榨制的酱油再晒制2~3个月,经沉淀过滤而成,其产品质量比生抽酱油更加浓郁。老抽中大多加入焦糖色,颜色较深,呈棕褐色有光泽,味道较咸。一般用来给食品着色,比如做红烧等需要上色的菜时使用较好。
2.按发酵工艺分类
主要有高盐稀态发酵酱油和低盐固态发酵酱油。
(1)高盐稀态发酵酱油(含固稀发酵酱油) 是以大豆和/或脱脂大豆、小麦和/或小麦粉为原料,经蒸煮、曲霉菌制曲后与盐水混合成稀醪,再经发酵制成的酱油。高盐稀态酱油颜色较浅,呈红褐色或浅红褐色。高盐稀态酱油香味浓郁,具有酱香和酯香香气。
(2)低盐固态发酵酱油 是以脱脂大豆及麦麸为原料,经蒸煮、曲霉菌制曲后与盐水混合成固态酱醅,再经发酵制成的酱油。低盐固态酱油颜色较深,呈深红褐色或棕褐色。在香味上,低盐固态发酵酱油酱香香气突出,酯香香气不明显。
二、酱油生产的原料
酱油生产所需要的原料有蛋白质原料、淀粉质原料、食盐、水以及一些辅料。酱油生产的原料既要保证食品安全,又要保证生产能顺利进行,还要使产品具有必要的风味。因此合理选择原料是保证生产的重要环节。酱油生产的主要原料应符合食品安全国家标准GB 2715的规定。
(一)蛋白质原料
酿造酱油用的蛋白质原料以大豆为主。大豆中含有20%左右的油脂,对酱油品质的贡献甚微,几乎可以认为是被浪费在酱渣中,因此,除少数厂采用传统酿造法仍用大豆外,绝大部分厂都改用了大豆榨油后的饼粕。
1.大豆
大豆的蛋白质含量高达36%~40%(表2-1),酱油全氮中的3/4来自大豆蛋白质,仅1/4来自小麦等淀粉质原料。在大豆的氮素成分中,非蛋白质态氮(包括嘌呤、嘧啶等)含量很少,仅占5%~7%;95%左右都是蛋白质态氮,其中水溶性蛋白质为90%,可被蛋白酶水解,6%~7%的部分为非水溶性蛋白质,是各种酶及其他低分子量蛋白质,这部分蛋白质不能被蛋白酶水解。
表2-1 几种常用于酱油生产的蛋白质原料及其主要成分

2.豆粕和豆饼
豆子采用压榨法提取油脂后的副产物称为豆饼,采用浸出法提取油脂后所剩的副产物称为豆粕。和大豆相比,豆饼(粕)的脂肪含量显著降低,而蛋白质含量大幅度提高,高出20%~25%。经压榨处理后,大豆的细胞壁结构被破坏,豆饼(粕)的组织结构和大豆相比有了显著改善,可缩短润水和蒸煮时间,加快酶解速度,从而能缩短发酵周期,提高原料的全氮利用率。豆饼(粕)的价格比大豆便宜,生产成本有所下降,又避免了食用豆油的浪费。然而,豆饼(粕)对酱油酿造也有某些不利影响。热榨豆饼由于在加热蒸炒时,经长时间高温处理,部分蛋白质过度变性成为不溶性蛋白质,用于生产酱油时,降低了原料的全氮利用率。豆粕和冷榨豆饼因在生产时没有受到高温处理,蛋白质变性少,不溶性氮含量低,和大豆蛋白质性质类似。
3.其他蛋白质原料
我国幅员辽阔,各地作物种植结构不同,植物蛋白质资源多样,这些植物的种子及其加工副产物可作为蛋白质代用原料用于酱油生产。如花生仁榨油后剩下的花生饼;豌豆、绿豆等豆类;葵花籽饼、油菜籽饼和芝麻饼等油料作物榨油后的副产物等。但需注意的是,油菜籽饼和棉籽饼由于含有有毒物质菜油酚和棉酚,应先去毒后才能用作酱油原料。
(二)淀粉质原料
过去淀粉质原料多采用小麦和面粉,现在除沿用传统工艺的少数厂家仍然采用外,绝大多数厂家一般改用麸皮,或辅以面粉、小麦、玉米、碎米、薯干等富含淀粉的原料。淀粉质原料是生产酱油中糖分、醇类、有机酸、酯类、色素及浓度的重要来源,与酱油的色、香、味、体等感官指标有重要关系。
1.小麦
小麦是最为适宜的淀粉质原料。它不仅碳水化合物含量高,而且蛋白质含量也比较高(表2-2)。生产中常将小麦焙炒后粉碎用于制曲或直接磨粉后用麦粉或面粉进行制曲。
表2-2 小麦和麸皮原料的主要成分

小麦的碳水化合物(无氮浸出物)包括含量65%左右的淀粉,主要存在于胚乳中,以及少量的蔗糖、葡萄糖、果糖和糊精等,主要存在于胚芽和麸皮中。这些碳水化合物在制曲过程中是曲霉的良好碳源,在发酵过程中,被逐步糖化,能增加酱油的甜味和固形物,也能被酵母菌、乳酸菌等利用发酵产生酒精和乳酸等,是酱油生香物质的前体。
小麦的蛋白质组成主要是麸蛋白和麦谷蛋白,统称为谷蛋白(也称面筋),谷蛋白的高级结构松弛,即使不经加热变性,也能比较容易地被酶水解。而且谷蛋白中谷氨酸含量比其他氨基酸高出5倍多,是重要的鲜味来源。
2.麸皮
麸皮是小麦磨粉后的副产物。麸皮是比较理想的淀粉质原料。麸皮的成分因小麦的品种、产地以及制粉机械的不同而有一定差异。
麸皮的碳水化合物含量比小麦要低20%左右,生产中常用添加淀粉糖化液制醅发酵的方法以补充其不足。麸皮的碳水化合物中多聚戊糖的含量高达20%~40%,水解后生成大量的戊糖,非常有利于酱油香气物质和色素物质的形成。另外,麸皮的纤维素含量高,质地疏松,表面积大,有利于通风制曲和淋油;灰分(无机盐)和维生素的含量也显著高于小麦和面粉,能够满足霉菌生长繁殖需要,不必另加其他营养物质。然而,若麸皮的添加量过大,将降低酱油品质。因为麸皮中含有大约20%的多缩戊糖,这类五碳糖不能被酵母菌发酵,不能产生醇类物质,不利于改善酱油风味。特别是五碳糖形成的色素乌黑发暗,不及六碳糖(如葡萄糖)好。
3.其他淀粉质原料
除了小麦、麸皮之外,各地就地取材,凡是含有淀粉而又无毒无异味的谷物,均可作为酱油生产的淀粉质原料,例如碎米、玉米、甘薯干、小米、高粱、大麦、米糠等。常用的各种淀粉质原料的主要成分见表2-3。
表2-3 几种常用于酱油生产的淀粉质原料及其主要成分

(三)食盐
食盐是酱油生产不可缺少的主要原料之一,它使酱油具有适当的咸味,能提高鲜味口感,增加酱油的风味。食盐在发酵过程中相应减少杂菌污染,起到防腐的作用。酱油酿造用食用盐应符合GB 5461的规定。
(四)水
用于酱油生产的水必须符合生活饮用水卫生标准GB 5749。目前随着工业化的进展,酿造酱油用水多选用自来水,自来水需经过处理达到酿造水的要求方能使用。
三、酱油生产用的微生物及生化机制
酱油是曲霉、酵母和乳酸菌等微生物综合作用的产物。传统的酱油生产中,制曲是依靠野生微生物自然繁殖发酵,由于有杂菌的繁殖,曲的酶活力不高,原料利用率低,有的杂菌会使产品带有异味甚至产生有毒有害物质。20世纪30年代开始试用纯菌种制曲,50年代米曲霉优良菌株纯种发酵在全国推广之后,纯培养的耐盐酵母、耐盐乳酸菌也应用于酱醪发酵,用来增强酱油的风味。
(一)酱油酿造的主要微生物
1.曲霉菌
(1)米曲霉(Aspergillus oryzae)米曲霉是酱油常用的发酵菌种。米曲霉通常为黄绿色,成熟后为黄褐色或绿褐色。分生孢子头呈放射形,顶囊近球形。以无性孢子繁殖为主。生长最适温度是32~35℃,低于28℃或高于40℃时生长缓慢,42℃以上停止生长。28~30℃时有利于蛋白酶和谷氨酰胺酶的生成。生长和产酶的最适pH值为6.5~6.8。
米曲霉属于好氧微生物,当氧气不足时,生长受到抑制,菌体细胞呼吸所产生的CO2,少量时可能促进产酶,如果过多积聚于曲料中,对米曲霉的生长和产酶不利。故在选择米曲霉时,应考虑以下4个条件:①不产黄曲霉毒素或其他真菌毒素;②蛋白酶、淀粉酶活力高,有谷氨酰胺酶活力;③生长快速、培养条件粗放、抗杂菌能力强;④不产生异味,酿制的酱油香气好。目前国内常用的米曲霉菌株有AS3.863、AS3.951、UE328、UE336、渝3.811等,每个菌株都有自己的优缺点。
(2)酱油曲霉(Aspergillus sojae) 酱油曲霉是酱油生产常用的发酵菌种,是20世纪30年代日本学者坂口从酱曲中分离而得的,其分生孢子表面有小突起,孢子梗表面平滑,培养成熟的菌落(34℃培养7d)呈茶色、茶褐色、茶绿色。菌落直径60~70mm,通常反面有褶、着色。
与米曲霉相比有如下特征:成曲中的碱性蛋白酶活力较强,通常产生曲酸,α-淀粉酶、酸性蛋白酶、酸性羧基肽酶活性较米曲霉低;所制成曲的pH值高于米曲霉成曲,通常pH7以上;柠檬酸等有机酸含量少;制曲过程中碳水化合物的消耗量少;酱醪黏度低;生酱油中残留的各种酶系酶量少,加热后沉降物少;生酱油中,还原糖、乙醇、氨的含量高,pH值低;氧化褐变性强。
(3)黑曲霉(Aspergillus niger) 黑曲霉是曲霉属黑曲霉群的霉菌,菌丝厚绒状、呈白色,初生孢子为嫩黄色,2~3d后全部变成褐黑色孢子,生长温度37℃。在麸皮培养基上生长迅速,其抑制细菌能力强于米曲霉。黑曲霉具有较强的糖化酶及果胶酶、纤维素酶活力,并具有较强的酸性蛋白酶活力。黑曲霉还产生大量的纤维素酶以及能分解有机质生成多种有机酸。目前我国应用较多的黑曲霉有AS3.350黑曲霉和AS3.324甘薯曲霉。
2.酵母菌
酵母菌对酱油风味和香气的形成有重要作用,能够适用于酱油发酵并给予酱油良好风味的酵母菌并不多,最常见的有鲁氏酵母(Zygosaccharomyces rouxii)和球拟酵母(Torulopsis)。在高盐稀态发酵工艺生产酱油时,在发酵初期,基质内存在多量糖分,pH值在适宜生长的范围时鲁氏酵母迅速生长繁殖,进行旺盛的酒精发酵,产生乙醇和甘油。一般在制醅45d左右,鲁氏酵母菌体可达最大量。随着基质内糖分降低及含氮量的增多,鲁氏酵母已不适合生长,超过90d后几乎死亡和自溶,此时球拟酵母大量繁殖。球拟酵母产生的聚乙醇和4-乙基愈创木酚对增强酱油风味有较大作用。
(1)鲁氏酵母(Zygosaccharomyces rouxii) 酱醅中典型的鲁氏酵母是大豆接合鲁氏酵母(Zygosaccharomyces sojae)和酱醪接合鲁氏酵母(Zygosaccharomyces major),它们都是耐盐性的非产膜酵母,在分类上是非常近缘的种属,其形态学和生理学差别较小;适宜生长温度为28~30℃,最适pH值为4~5。耐盐性强,能抗高渗透压,在含食盐5%~8%的培养基中生长良好,某些菌株在18%食盐浓度下仍能生长。在高食盐浓度下,其生长的pH值范围很窄,仅为4.0~5.0。培养基中食盐浓度不同,其发酵糖类的能力也不同。在不添加食盐的基质中,能利用葡萄糖和麦芽糖发酵。食盐浓度18%的培养基中,能发酵葡萄糖,但几乎不发酵麦芽糖。
鲁氏酵母出现在主发酵期,属于增香酵母,约占酵母总数的45%,对酱油酿造的影响最为重要。由于酱醪中糖含量高,pH值适宜,酵母的酒精发酵旺盛,酱醪的酒精体积分数可达到2%以上,同时生成少量甘油、琥珀酸以及其他多元醇、呋喃酮类等风味物质。此外,鲁氏酵母还能发酵糖类物质生成琥珀酸等,与嗜盐片球菌联合作用生成糠醇,产生特殊的酱油香气。鲁氏酵母的谷氨酰胺酶能转化底物生成谷氨酸而增强酱油的鲜味。另外,自溶后释放胞内物质也为酱油增添了鲜味。在发酵后期,随着发酵温度升高,鲁氏酵母开始自溶,促进了球拟酵母的生长,自溶的酵母又增添了酱油的鲜味。鲁氏酵母的添加,使成品酱油的风味纯正浓厚,即使添加量过大也不会造成负面影响。
(2)球拟酵母(Torulopsis) 球拟酵母属于酯香型酵母,能生成酱油的重要芳香成分。如4-乙基苯酚、4-乙基愈创木酚、2-苯乙醇、酯类等,与酱醅的香味有关。酱醅中重要的球拟酵母有易变球拟酵母(Torulopsis versatilis)、埃契氏球拟酵母(Torulopsis etchellsii)、蒙奇球拟酵母(Torulopsis mogii)。
3.乳酸菌
乳酸菌是一类能利用可发酵糖生成乳酸的细菌的总称。酱油乳酸菌是指生长在酱醅特定环境中的特殊的乳酸菌,此环境中生长的乳酸菌是耐盐的。乳酸菌的耐乳酸能力不强,因此不会因产生过量乳酸使酱醪pH值过低而造成酱醪腐败。天然发酵的酱醪中存在大量乳酸菌,对酱油品质的提升有着重要的作用。主要表现在以下几个方面:
(1)改变发酵体系的pH值,促进酵母菌生长繁殖 鲁氏酵母和球拟酵母的发酵能够显著提升酱油的香味。当酱醅或酱醪pH值降低至5.2以下时,这些酵母能在高盐量的酱醪中生长,乳酸菌的繁殖促进了酱醪pH值下降,使之达到酵母活动的pH 5.2以下,从而促进酵母的繁殖。
适量的乳酸是构成酱油风味的重要因素之一,乳酸本身具有特殊香气而对酱油有调味和增香作用,而且与酵母产生的乙醇生成乳酸乙酯,也是一种重要的香气成分。一般酱油中乳酸含量在15g/L。
(2)在制曲和发酵阶段抑制杂菌污染 乳酸菌是厌氧菌,在制曲过程中它生长在曲料团粒内部,而米曲霉、酱油曲霉是好氧菌,首先生长于曲料团粒的表面。随着曲霉的繁殖、产热,品温逐渐升高,乳酸菌的生长被抑制,在制曲过程中乳酸菌产生的乳酸能有效抑制小球菌、枯草芽孢杆菌、纳豆菌等不耐酸的杂菌生长繁殖。同时,乳酸菌随成曲进入酱醪,同样抑制杂菌的生长,对于发酵生香效果显著。
酱油酿造过程中具有代表性的乳酸菌有嗜盐片球菌(Pediococcus halophilus)、酱油四联球菌(Tetracoccus sojae)、植物乳杆菌(Lactobacillus plantarum)。
(二)酱油酿造的生化机制
在酱油生产过程中,主要原料经浸泡、蒸煮后,利用特定的微生物,通过对发酵参数如通气量、温度、湿度和微生物群落等有效控制,使成熟的酱醅中富含微生物酶系,利用这些酶使原料中大分子物质降解并进行生物转化。因此说,酱油酿造的生化机制实质是曲霉、酵母和乳酸菌等微生物酶协同作用的过程。
1.蛋白质的分解
酱醅中的蛋白水解酶在制曲时由米曲霉产生。米曲霉可分泌3种蛋白酶:酸性蛋白酶(最适pH值为3)、中性蛋白酶(最适pH值为7左右)、碱性蛋白酶(最适pH值为8)。酱醅中的蛋白酶以中性和碱性蛋白酶为主,酸性蛋白酶较弱。
在发酵过程中,原料中蛋白质经微生物所产生的蛋白酶分解,生成分子量较小的氨基酸和小分子多肽等物质,成为酱油的营养成分和鲜味来源。某些氨基酸如谷氨酸、天冬氨酸等构成酱油的鲜味;某些氨基酸如甘氨酸、丙氨酸和色氨酸具有甜味;某些氨基酸如酪氨酸、色氨酸和苯丙氨酸产色效果显著,能氧化生成黑色及棕色化合物,形成酱油的颜色。因此蛋白质原料对酱油的色、香、味、体的形成至关重要,是生产酱油的主要原料。由于各种因素的影响,原料蛋白质在发酵过程中并不能完全分解为氨基酸,成熟酱醅中除含氨基酸外,还存在着、胨和肽等。成品酱油中氨基氮的含量应达到全氮的50%以上。
2.淀粉糖化
制曲过程中,曲霉会分泌一系列的淀粉水解酶系,如α-淀粉酶、淀粉1,4-葡萄糖苷酶、β-淀粉酶、淀粉α-1, 6-糊精酶和麦芽糖酶等,这些酶共同作用淀粉生成糊精和葡萄糖。生成的单糖构成酱油的甜味,有部分单糖被耐盐酵母及乳酸菌发酵生成醇和有机酸,成为酱油的风味成分。除葡萄糖外,还有果糖和五碳糖。果糖主要来源于豆粕(饼)中糖的水解,五碳糖来源于麸皮中的多缩戊糖。这些糖与酱油的色、香、味、体的形成密切相关。糖化作用的结果对酱油的风味有重要影响。糖化作用完全,酱油的甜味好,体态浓厚,无盐固形物高。
3.有机酸的形成
有机酸是酱油的重要呈味物质,也是香气的重要组成成分。酱油中总酸在15g/L左右时,酱油风味柔和。酱油中含有多种脂肪酸,其中最重要的有乳酸、醋酸、琥珀酸、葡萄糖醛酸等。乳酸菌利用五碳糖(阿拉伯糖和木糖)发酵生成乳酸和醋酸;琥珀酸可经TCA循环产生,也可经谷氨酸氧化产生;葡萄糖醛酸则由葡萄糖经醋酸菌氧化生成。发酵过程中,米曲霉分泌的解脂酶使少量油脂水解生成脂肪酸和甘油。而甲酸、丙酸、丁酸、异戊酸、香草酸等是由相应的醛类物质氧化而成。
4.酒精发酵
酒精发酵主要是酵母作用的结果。成曲入池后,酵母菌的繁殖情况与发酵温度密切相关,10℃时酵母菌只繁殖不发酵,30℃左右最适合酵母菌的繁殖和发酵,发酵温度超过40℃时酵母菌会发生自溶。酵母菌利用糖生成酒精和CO2,并有少量副产物生成,如甘油、杂醇油、有机酸等。发酵产生的酒精并非完全存在于酱油中,其中一部分氧化生成有机酸类;一部分挥发散失;一部分与氨基酸及有机酸等化合生成酯类;微量残存在酱醪中构成酱油的香气。 在固态低盐后熟发酵过程中,成曲接入鲁氏酵母和蒙奇球拟酵母,产生酒精、异戊醇、异丁醇和各种有机酸,可显著改善酱油的香气。
5.酱油色香味体的形成
(1)酱油色的形成 酱油色素形成的主要途径有两条:一是通过美拉德反应最终形成褐色的类黑色素,这是最主要的生成途径;二是酶促褐变反应,由曲生成的多酚氧化酶将酪氨酸氧化成黑色素。与美拉德反应相比,通过酶促褐变反应生产的色素量则要少得多。酶促褐变在有氧条件进行,所生成的黑色素颜色要比非酶促褐变生成的要深。色素的形成,与原料的种类、配比、制曲和发酵温度、酱醅含水量等条件有关。
(2)酱油香气的形成 酱油的香气是决定酱油风味的重要因素。酱油的香气是各种香气成分的综合,成分复杂,香味包括烃类、醇类、酯类、醛类、醛缩醇类、酮类、酸类等。其中与酱油香味关系密切的有:①酒精。日本酿造酱油中酒精体积分数有高达2%以上的,一般也在1%左右。②酵母分解亮氨酸和异亮氨酸,生成的戊醇、异戊醇等各种醇,同时与有机酸经酯化生成酯类。③小麦和麸皮经曲霉和球拟酵母等微生物作用产生酚类后,转化为4-乙基愈创木酚(4EG)和4-乙基苯酚(4EP)。④ 呋喃酮类化合物4-羟基-2(5)-乙基-5(2)-甲基-3(2H)-呋喃酮(HEMF),在酱油中以互变体形式存在。它的同族物4-羟基-2,5-二甲基-(2H)-呋喃酮(HDMF)和4-羟基-5甲基-3-(2H)-呋喃酮(HMMF)都是酱油的呈香物质。HEMF是酵母代谢产物,给酱油带来柔和的咸味,它是酱油中特殊香味成分。
(3)酱油味的形成 酱油是多种味调和的咸味调味品。主要包括:①咸味。酱油的咸味来自于食盐。②鲜味。 谷氨酸、盐、天冬氨酸和部分甜味氨基酸的协同作用,是酱油鲜味的主要来源。鲜味物质主要来源于蛋白质的分解,有少部分由微生物代谢生成。霉菌、酵母菌和细菌中的核酸水解后生成鸟苷酸、肌肽酸和黄苷酸等呈味核苷酸,也是强鲜味物质。③甜味。甜味来源于常见的糖,如葡萄糖、果糖、麦芽糖等,以及一些氨基酸和多元醇。④酸味。 酱油应在感官上不能感觉到酸味,但是有机酸对酱油的风味起着重要的调和作用。酱油中的有机酸以乳酸为代表,还包括乙酸、丙酮酸、琥珀酸、柠檬酸酸、α-酮戊二酸等。⑤苦味。苦味在酱油中含量少因而感觉不到,来源于酪氨酸和缬氨酸等苦味氨基酸及部分二肽,发酵过程中产生的乙醛,食盐中带入的MgCl2、CaCl2等杂质。
(4)酱油体的形成 酱油的体指酱油的浓稠度,俗称为酱油的体态,由各种可溶性固形物构成。酱油固形物是指酱油水分蒸发后留下的不挥发性固体物质,主要有食盐和无盐固形物。无盐固形物包括可溶性蛋白质、氨基酸、维生素、矿物质、糊精、糖类和色素等。无盐固形物的含量高低也是酱油质量指标之一,最低控制在80g/L以上,优质酱油无盐固形物含量达到200 g/L以上。
四、酱油现代生产流程及技术参数
经过数千年的生产演变,尽管目前酿制酱油的方法各有不同,但是酱油生产的工序基本一致(图2-1),均需经原料处理、菌种选择与种曲制备、成曲制备、发酵、取油及加热调配等过程。

图2-1 酱油酿造的一般工序
(一)原料处理
原料处理是酱油酿造的第一道重要工序。原料处理是否得当将直接影响到制曲的难易,成曲的质量的好坏,酱醅和酱醪的成熟,淋油及压榨的速度及出油率的多少等。
原料处理包括原料预处理、粉碎、润水、蒸煮,经过充分润水和蒸熟,使蛋白质达到适度变性,淀粉充分糊化,以利于米曲霉的生长繁殖和酶系、酶量的分泌及酶解作用。同时,通过蒸煮杀灭附着在原料上的杂菌,排除其在制曲过程中对制曲微生物生长的干扰。
1.原料粉碎
不同的原料有不同的处理方法。如采用豆饼为原料,需要预先粉碎。豆粕、麸皮原料呈片粒状,一般不需要粉碎,如有较多团块,拣出或筛去即可。豆饼、小麦和玉米等原料一般需粉碎成粗粉状或破碎颗粒表皮,使淀粉暴露,以利于吸水蒸煮。粉碎后的原料颗粒大小要均匀,利于原料吸水和蒸熟程度均匀,同时有利于增大米曲霉繁殖的比表面积,使制曲过程大量分泌酶系。如果颗粒度太细呈粉末状,则会造成制曲时密度过大,不利于通风制曲,易污染厌氧细菌,影响米曲霉好氧生长,且在发酵时增加酱醅、酱醪黏度,影响出油率。
原料粉碎常采用锤式粉碎机,筛孔直径为9mm。小麦原料破碎前一般需要经过焙炒,简易的可采用平锅,规模生产则采用炒麦机。炒熟小麦的淀粉达到糊化,易被酶解,对增色生香有利。炒熟的小麦再经破碎,与蒸熟的豆粕混合后进入下一道工序。
2.加水润料
向原料中加入适量的水分,原料均匀而完全地吸收水分的过程称为润料或润粮。加水润料的目的是使原料中蛋白质含有一定量的水分,以便于在蒸煮时迅速达到适度变性,同时使原料中淀粉易于充分糊化,为曲霉生长提供碳素养分。另外还为曲霉生长繁殖提供必要的水分。
(1)加水量的确定 加水量的确定是酱油制曲过程中的关键步骤,直接关系到成曲的质量。微生物的生长繁殖要求基质中有一定的水分活度(Aw)。曲霉所需的Aw值较低,而细菌一般较高。因此,当曲料中的水分含量控制在曲霉能够生长,而又低于细菌生长所需要的最适Aw时,曲霉的孢子在短时间内就能吸水萌发长出菌丝,占据生长优势,抑制细菌的侵染。但水分过多,则不利于米曲霉的生长繁殖和酶的分泌,反而招致杂菌的繁殖,消耗掉大量的淀粉和蛋白质,产生较多的游离氨等不良气味,影响酱油的品质。如果水分较少,同样不利于曲霉的生长和酶的分泌,蒸煮时,也不利于原料蛋白质的变性。
原料加水量受原料水分、原料性质及配比、气候条件、蒸煮设备、制曲方法及保温通风等众多因素的影响。原料加水量的计算公式(未考虑蒸汽带入的冷凝水)如下:
式中 w——要求熟料水分, %;
m水—— 加水量,kg;
m1—— 豆粕的质量,kg;
m2—— 麸皮的质量,kg;
m3—— 小麦粉的质量,kg;
w1—— 豆粕的水分, %;
w2—— 麸皮的水分, %;
w3—— 小麦的水分, %。
本计算公式未考虑蒸汽带入的水分,视蒸汽质量作适当扣除,一般蒸汽中的水分约为总原料的5%~10%。
(2)润料设备 润料设备是与蒸料设备相匹配的。中小型厂多用常压蒸料,将原料加水后用扬料机扬料1~3遍,将料和水拌匀,然后静置润水半小时左右。采用旋转式蒸煮锅蒸料,加水润料均在旋转式蒸煮锅内进行。采用连续蒸煮装置蒸料,在连续蒸煮装置的洒水绞笼中加水润料。
3.蒸料
(1)蒸料的目的及要求 蒸料的目的首先是使原料中的蛋白质完全适度地变性,使原料的细胞组织松散,有利于制曲微生物所产生的蛋白酶系分解。其次,蒸料过程可使淀粉吸水膨胀而达到糊化程度,并产生少量糖类供制曲微生物生长繁殖利用。同时,蒸料过程的高温处理可杀灭附着在原料上的微生物,提高制曲的安全性。
蒸料并不是一个简单的加热蒸煮过程,必须精确掌握蒸煮压力、温度和时间,才能使原料蛋白质完全适度变性,提高原料蛋白质利用率和酱油质量。如果加水不足或压力偏低或时间过短,原料未蒸熟,其中的部分蛋白质还未达到适度变性,这部分蛋白质不能被蛋白酶水解,保留在生酱油中,一旦生酱油加水稀释或加热,就会出现浑浊,静置一段时间析出淡黄色或白色沉淀,一般称此现象为N性,此浑浊或沉淀物称为N性物质。如果高温长时间蒸料,原料中的蛋白质则会发生过度变性,即松散紊乱状态的蛋白质又重新组织,因而也不能被蛋白酶水解,并且不溶于(盐)水和酱油。同时在高温长时间蒸料过程中,原料的糖类与肽、氨基酸等含氮化合物发生复杂的美拉德反应,使熟料呈深红褐色。这些也都会降低原料蛋白质的利用率。
蒸料要求达到一熟、二软、三疏松、四不粘手、五无夹心、六有熟料固有的色泽和香气。蒸料质量常用熟料的消化率表示,消化率是熟料中能被蛋白酶水解的蛋白质的量占熟料总蛋白质的量的百分含量。蒸料质量与蒸料温度、时间、压力变化等密切相关。目前许多厂采用“高短法”蒸料,即高温短时间蒸料,短时间内脱压降温。和原来的低温长时间蒸煮相比,消化率大大提高,原料蛋白质基本上达到了完全适度地变性。
(2)蒸料的设备及方法 目前我国酱油生产厂采用的蒸料设备可分为3类,中小型厂仍然使用常压蒸煮设备,大多数厂家采用旋转式蒸煮锅,少数厂家开始采用更为先进的连续蒸煮装置。
① 常压蒸煮设备 最简易的常压蒸煮设备就是用木质蒸桶或多节蒸笼,置于大锅上,利用锅内的水沸腾后产生蒸汽进行蒸料。有蒸汽供应的工厂,采用蒸桶或方形铁箱,底部装有蒸汽盘管,盘管上安装假底,侧面开有卸料门,上加木盖或麻袋布保温。常压蒸煮设备结构简单,便于操作。但是曲料蒸熟不易均匀,有未变性的蛋白质存在,原料蛋白质利用率最高仅70%左右,而且耗能多,进出料劳动强度大。
② 旋转蒸煮设备 旋转蒸煮设备的特点是可做360°旋转,原料可以通过真空泵吸入锅内,润料、蒸煮均在旋转状态中进行,所以润料、蒸煮均匀,不易产生N性物质。而且操作基本上能实现机械化,减轻了劳动强度,目前被国内大多数企业所采用。
旋转蒸煮锅的锅体以立式双头锥为主,也有球形的。其容积一般为5~6m3。旋转装置由电动机、变速箱、实心轴和空心轴组成(如图2-2所示),可使锅体做360°旋转运动,促使锅内曲料蒸煮均匀。冷却排气管和水力喷射器相连,蒸料毕,利用水力喷射器抽真空,使锅内压力迅速下降,锅内水分在低压下大量蒸发,带走大量热量,曲料在短时间内被脱压冷却。

图2-2 旋转式蒸煮锅(无假底)装置示意图
1,3—真空泵;2—水过滤器;4—旋风分离器;5—贮尘桶;6,26—电动机;7—水泵;8—给水管阀;
9—压力表;10—水力喷射器;11—单向阀;12—安全阀;13—加水管;14—压力真空表;15—蒸汽管;16—贮水池;
17—排气管阀;18—空心轴及填料匣;19—闸门阀;20—喷水及喷汽管;21—转锅体;22—温度计;
23—正齿轮;24—实心轴;25—涡轮变速箱;27—冷却排气管;28—进料软管;29—进料斗;30—蒸料锅盖
③ FM连续蒸煮设备 FM连续蒸煮设备是20世纪70年代由日本藤原酿造机械有限公司研发成功,目前在国内已有制造和使用。原料通过第1节洒水绞龙润料,进入第2节预蒸不锈钢金属网绞龙,然后进入第3节由回转阀随着金属网的移动进行加压蒸煮,最后通过减压室脱压出料。料层厚度约20cm,压力0.18~0.20MPa,蒸煮时间为3min。该设备的特点是连续润料、蒸料,机械化程度高,原料蛋白质达到适度变性,适用于大型企业。
FM连续蒸煮设备示意图见图2-3。该装置生产能力为2t/h脱脂大豆,所用锅炉蒸发量21t/h,传热面积49.7m2,常用压力800kPa。

图2-3 FM连续蒸煮设备示意图
1,9—蒸汽管;2—水管;3—流量计;4—温水装置;5—原料入口;
6—洒水管;7—第1次浸渍绞龙;8,12—温度计;10—喷射冷凝器;11—第2次浸渍绞龙;
13—旋转阀;14—横置圆筒蒸煮罐;15,17—旋转阀;16—减压室
由于蒸煮温度高,大豆组织异常软化而发黏,尤其采用150%洒水量时最为明显,很难采用螺旋输送装置。FM连续蒸煮装置采用了网状传送带式连续蒸煮装置,其主要运行参数如表2-4所示。
表2-4 FM连续蒸煮装置主要运行参数

这套设备的脱脂大豆浸渍采用70℃温水,每6h用水量为2600L。全部操作只需1人完成。洒水量一般采用130%,实际含水量达64%。FM连续蒸煮罐与旋转蒸煮罐的蒸料方法比较见表2-5。
表2-5 FM连续蒸煮罐与NK式旋转蒸煮罐的蒸料方法比较

(二)菌种选择与种曲制备
种曲即酱油酿造制曲时所用的种子,它是由生产所需要的菌种,例如米曲霉、酱油曲霉、黑曲霉等经培养而得的含有大量孢子的曲种。制种曲的目的是要获得大量纯菌种,要求菌丝发育健壮、产酶能力强、孢子数量多、孢子发芽率高、杂菌少。
1.菌种的选择
在种曲制备过程中,选择性状优良的菌种十分关键。酱油种曲制备所需要的优良菌种应具备以下条件:①安全性好,不产生黄曲霉毒素等真菌毒素及其他有毒成分;②酶系全、酶活力高,其中蛋白酶(尤其是酸性蛋白酶)、淀粉酶(糖化酶)活力高,具有高谷氨酰胺酶活力;③繁殖力旺盛,抗杂菌能力强;④菌种纯,性能稳定;⑤制曲过程中碳水化合物消耗少;⑥香味好,不产生异味,酿制的酱油风味好,产率高。
目前我国酱油生产使用菌株主要为米曲霉沪酿3.042,即AS3.951。该菌种分泌的蛋白酶和淀粉酶活力很强,繁殖较快,发酵时间仅为24 h;对杂菌有非常强的抵抗能力;用其制造的酱油质量十分优良;不会产生黄曲霉毒素等,不易变异。此外,还有一些性能优良的菌株,也逐渐被酿造厂采用,如上海酿造科学研究所的UE336,重庆市酿造科学研究所的3.811,江南大学的961等。近几年采用黑曲霉AS3.350或F27与米曲霉混合制曲也逐渐得到推广。混合制曲可丰富酶系,提高原料利用率。
2.试管菌种培养与种曲制备
(1)试管菌种培养 制备豆汁或米曲汁培养基,灭菌后分装制成试管斜面,将米曲霉接种入斜面。斜面培养基接种后,30℃恒温培养3d,长满茂盛的孢子即可。斜面菌种如不及时使用,可置4℃冰箱保存1~3个月。对于长期保存菌种,可采用石蜡保藏法、砂土管保藏法或麸皮管保藏法。如果菌种出现退化现象,如菌丝变短,颜色改变,孢子生长不整齐或明显减少甚至不能形成,酶活力降低等,应进行分离复壮。生产中一般在传代3~4次后就要进行分离复壮。
(2)种曲制备 采用麸皮培养基在三角瓶中进行菌种扩大培养。培养基配方为:麸皮80g、面粉20g、水95~100mL,或麸皮85g、豆饼粉15g、水95mL。将培养基原料混匀后,分装于在250mL三角瓶内,料厚度约1cm,121℃湿热灭菌30min,灭菌后趁热把曲料摇散。
待曲料冷至室温后,在无菌操作环境下接种试管菌种孢子1~2环,充分摇匀后,于30℃培养36~48h,菌丝充分生长结块后进行扣瓶,即将三角瓶斜倒,使底部曲料翻转悬空在三角瓶中,与空气充分接触。继续培养1d,待全部长满黄绿色孢子即可。培养好的种曲及时使用,如果短时间保存,可置于4℃冰箱中,但放置时间不宜超过10d。
三角瓶培养的种曲质量要求孢子发育肥状、整齐、稠密、布满培养料,米曲霉呈鲜艳黄绿色,黑曲霉呈新鲜黑褐色;有曲霉特有的香味,无异味,无杂菌,内无白心。孢子数(个/g干基,血细胞计数板测定)米曲霉沪酿3.042达90亿个/g, 黑曲霉F27达80亿个/g以上,黑曲霉AS3.350达200亿个/g;且孢子发芽率在90%以上。
一些小型酱油生产厂由于产量小,所用种曲量也少,可将三角瓶种曲直接作为种曲使用。但对大中型酱油厂而言,三角瓶种曲不够量,因此常以三角瓶种曲为菌种进一步扩大培养。目前大多数大型酱油生产企业采用通风曲箱制作种曲。在长方形通风曲箱(3.5m×1.6m×0.4m)中,曲料厚度可达到12cm,间歇通风培养70h制成种曲,其种曲质量稳定,杂菌少,酱油出品率提高,并减轻了工人劳动强度。
(三)成曲制备
成曲的制备过程简称制曲。制曲是我国酿造工业的一项传统技术,其实质是固体发酵过程,即创造曲霉菌适宜的生长条件,促使曲霉充分生长繁殖,分泌出高活力的蛋白酶、淀粉酶等酶系,为制醅发酵打下良好基础。
制曲多采用纯种制曲。根据制曲方式,分为液体曲和固体曲。液体曲研究开始于20世纪50年代,是采用液体培养基接入曲霉进行培养的一种方法,适合于管道化和自动化生产,生产周期短。但液体曲酿制的成品风味欠佳、色泽浅。固体曲使用广泛,制曲方法有厚层机械通风制曲、曲盘制曲、圆盘式机械制曲等。其中使用最为广泛的是厚层机械通风制曲法,它具有曲层厚、设备利用率高、节约人力、操作适合于机械化、成曲酶活力高等优点。
厚层机械通风制曲的主要设备见图2-4。

图2-4 厚层机械通风制曲示意图
将接种后的物料送入曲池,曲料厚度一般为30cm左右。利用风机供氧,调节温湿度,米曲霉经过4个阶段:孢子发芽期→菌丝生长期→菌丝繁殖期→孢子着生期,在较厚的曲料上生长繁殖和积累酶系,培养22~26h时曲呈淡黄绿色即可出曲。
旋转圆盘式自动制曲机最初是由日本人设计生产的。主要结构包括圆盘曲床、保温室、顶棚、夹顶、进料器、刮平装置、翻曲装置、出曲装置、测温装置、空调通风以及电器控制等。以多孔圆板的旋转体为培养床,四周有一圈挡板,防止曲料散落。曲料的加入、摊平、通风、测温和出曲均可实现自动化,单人操作即可。全机为封闭式,因而成曲杂菌少,质量高。旋转圆盘式自动制曲是今后制曲发展的方向。
(四)发酵
酱油的发酵是指将成曲拌入盐水,装入发酵容器内,采用保温或者不保温方式,利用曲中的酶和微生物的作用,将酱醅(醪)中的物料分解、转化,形成独特色、香、味、体成分的过程。如果成曲拌入盐水量多,呈浓稠的半流动状态的混合物,称为酱醪;如果成曲拌入盐水量少,呈不流动状态的混合物,称为酱醅。
我国的酱油生产工艺繁多。根据发酵加水量的不同分为稀醪发酵、固态发酵、固稀发酵;根据加盐量的不同分为有盐发酵、低盐发酵、无盐发酵;根据发酵时保温方式不同分为自然发酵和保温速酿发酵;根据发酵过程物料状态和含盐量多少分为低盐固态发酵、高盐稀态发酵和固稀发酵等。目前国内酱油酿造厂普遍采用的有低盐固态发酵工艺和高盐稀态发酵工艺。传统的天然晒露发酵工艺因其酿造的酱油酱香浓郁、风味醇厚、色泽饱满,近几年来各大酱油生产企业又恢复使用此工艺生产。
1.低盐固态发酵
低盐固态发酵工艺是20世纪60年代初,我国研究的一种发酵工艺,它综合了几种发酵工艺的优点,具有管理方便、蛋白质利用率高、产品质量稳定等优点,但产品风味和色泽不及天然晒露法和高盐稀态法酱油。目前我国大多数酱油生产企业仍采用低盐固态发酵法进行酱油酿制。由于不同地区不同厂家使用的设备、原料等不同,低盐固态发酵又可分为低盐固态发酵移池浸出法、低盐固态发酵原池浸出法和低盐固态淋浇发酵浸出法。
(1)低盐固态发酵移池浸出法 发酵池不设假底,发酵结束后,把酱醅移至淋油池淋油。我国北方地区应用较多。
① 工艺流程 低盐固态发酵移池浸出法工艺流程见图2-5。

图2-5 低盐固态发酵移池浸出法工艺流程
② 操作要点
a.盐水调制 将食盐溶解, 调整到11~13°B,盐浓度过高会抑制酶的作用,影响发酵速度;浓度过低则可能污染杂菌,使酱醪pH下降,抑制中性、碱性蛋白酶的作用,甚至引起酱醪酸败,影响发酵正常进行。
b.拌曲盐水温度 夏季盐水40~45℃,冬季50~55℃。入池后,酱醪品温控制在40~45℃。 盐水温度过高会使成曲中的酶活性降低,甚至失活。
c.拌曲盐水量 拌曲盐水量一般控制酱醪水分在50%~53%。拌水量的多少对分解率与原料的利用率关系密切。拌水量少,酱醅温度升高快,对酱油色泽的提高很有效,但对原料水解率与原料的利用率不利;拌水量多虽对水解率与原料的利用率有利,但酱醅不易升温,酱油色泽淡。拌曲盐水量可根据以下公式计算:
d.保温发酵 发酵前期,使温度控制在40~45℃,此温度是蛋白酶的最适作用温度,维持15d左右,水解完成。如后期补盐,使酱醪含盐量达15%以上,后期发酵温度可以控制在33℃左右,此时酵母菌和乳酸菌生长发酵。整个发酵周期为25~30d。国内一些工厂由于设备条件限制,发酵周期多在20d左右。为使发酵在较短时间内完成,可适当提高酱醪温度,但不宜超过50℃,否则会破坏蛋白酶,肽酶和谷氨酰胺酶也会很快失活。
e.倒池 倒池可以使酱醪各部分温度、盐分、水分以及酶的浓度趋向均匀,并可使酱醪内部产生的有害气体挥发,增加酱醪含氧量,防止厌氧菌生长,以促进有益微生物繁殖。倒池的次数依据总体的发酵情况而定。发酵周期为20d时,只需在9~10d倒池一次;发酵周期为25~30d 时,可倒池2次。
(2)低盐固态发酵原池浸出法 该方法发酵和淋油在同一池中进行,发酵池下设置阀门,发酵完毕,放入冲淋盐水浸泡后,打开阀门即可淋油。其他步骤与移池操作基本相同,不必考虑移池操作对淋油的影响。酱醪含水量可增大到57%左右,这样的含水量有利于蛋白酶的水解作用,提高全氮利用率。同时,由于醅中水分较大,酱醅不易焦化而产生焦煳气味,有利于酱油质量的提高。
(3)低盐固态淋浇发酵浸出法 淋浇即在发酵前期,将积累在发酵池假底下的酱汁,用泵抽回浇于酱醅表面,使酱汁布满酱醅整个表面均匀下渗,将渗漏的酶液再回到酱醅中充分发挥其作用,还可以补充表面水分,减少氧化层,及时凋节酱醅温度使上下层温度一致。发酵后期通过浇淋可向酱醅中补加浓盐水、耐盐性乳酸菌和酵母菌培养液,迅速把品温降至30℃左右,以促进发酵作用和后熟作用。因而能在较短的发酵时间内,增进酱油风味,能够很好地解决固态低盐发酵工艺酱油风味差的问题。
其具体操作方法:制醅入池(制醅方法同移池淋油发酵),表面不进行盐封。发酵前期14~15d,保持品温40~45℃。从酱醅入池次日浇淋一次,以后每隔 4~5d浇淋一次,前期共需浇淋3~4次。转入发酵后期,通过浇淋,补加浓盐水和乳酸菌、酵母菌培养液,使酱醅含盐量达15%以上,品温降至30℃左右,维持此品温进行后期发酵。第2天及第3天再分别浇淋一次,使菌液分布均匀,品温达到一致。后期发酵14~15d,酱醅成熟即可出油。
2.高盐稀态发酵
高盐稀态发酵法是指成曲中加入较多盐水,使酱醪呈流动状态进行发酵。由于酱醪中含水量高,原料组分溶解性好,酶活性强,有益微生物的发酵作用以及后熟作用进行得比较充分,所以原料利用率和酱油风味均优于固态发酵。另外酱稀醪保温输送方便,适于大规模机械化生产。但由于发酵周期较长,需要较多的发酵设备,以及输送、搅拌和压榨取油设备,酿造出的酱油色泽较淡。在20世纪40~50年代,国内大型厂曾采用过稀醪保温发酵工艺,后来都改用了固态低盐发酵工艺。70年代后期,在稀醪保温发酵工艺的基础上演变出的稀醪低温发酵新工艺被国内外不少厂家采用,以酿制高级酱油。高盐稀态低温发酵酱油香味浓郁、口味醇厚,将是我国优质酱油的主流生产工艺。
根据发酵温度不同,高盐稀态发酵又分为稀醪常温发酵、稀醪保温发酵和稀醪低温发酵。常温发酵的酱醪温度随气温高低自然升降,酱醪成熟缓慢,发酵时间较长。
(1)稀醪常温发酵(日晒夜露法) 稀醪常温发酵是历史上最早使用的酱油生产方法。一般在低温的春季制醪发酵,随气温逐步上升,至三伏季节处于高温阶段,发酵达到最高峰。到秋季进入后熟阶段。在稀态发酵期间,采用日晒夜露的方法,酱醪温度随气温高低自然升降,发酵期3~6个月。该工艺在日照时间长、年平均气温高的南方广泛应用。如广东的生抽王、老抽等产品多是采用这种工艺生产。其生产工艺如图2-6所示。

图2-6 稀醪常温发酵工艺流程
成曲加入220%~250%、19~20°B',e的盐水,搅拌均匀后送入发酵池或露天发酵罐(为全密封式)进行自然晒露发酵,时间4~6个月。在第一周内,每天用压缩空气或人工搅拌2次,使酱醪浓度、温度一致,酶体溶出,促进反应。以后可根据发酵情况,每日或间隔一日搅拌1次,直至酱醪成熟。
(2)稀醪保温发酵 稀醪保温发酵亦称温酿稀发酵,成曲加入220%~250%、19~20°B',e的盐水,搅拌均匀后送入发酵池或露天发酵罐。根据保温温度不同,又可分为消化型、发酵型、一贯型和低温型。
① 消化型 酱醅发酵初期温度较高,一般可达到42~45℃,保持15d,酱醅主要成分全氮及氨基酸生成速度基本达到高峰,然后逐步降低发酵温度,促使耐盐酵母大量繁殖进行酒精发酵,同时使酱醪成熟。发酵周期为3个月,产品口味浓厚,酱香气较浓,色泽比其他类型深。
② 发酵型 温度是先低后高。酱醅先经过较低温度缓慢进行酒精发酵,然后逐渐将发酵温度上升至42~45℃,使蛋白质分解作用和淀粉糖化作用完全,同时促使酱醅成熟。发酵周期为3个月。
③ 一贯型 酱醪发酵温度始终保持42℃左右,耐盐耐高温的酵母菌也会缓慢地进行酒精发酵。发酵周期一般为2个月,酱醪即可成熟。
④ 低温型 酱醅发酵温度在15℃维持30d。目的是抑制乳酸菌的生长繁殖,同时保持酱醅pH7左右,使中性和碱性蛋白酶及谷氨酰胺酶能充分发挥作用,有利于谷氨酸生成和提高蛋白质利用率。30d后,发酵温度逐步升高开始乳酸发酵。当pH下降至5.3~5.5,品温到22~25℃时,鲁氏酵母菌开始酒精发酵,温度升到30℃是酒精发酵最旺盛时期。下池2个月后pH降到5以下,酒精发酵基本结束,而酱醅继续保持在28~30℃ 4个月以上,酱醅达到成熟。在此时期,球拟酵母大量繁殖,分解五碳糖生成4-乙基愈创木酚,使酱油具有特殊的酱香。
3.固稀发酵
固稀发酵是以脱脂大豆和小麦为主要原料,经过前期固态发酵和后期稀发酵两个阶段酿造酱油的工艺。
将蒸熟的脱脂大豆与焙炒破碎的小麦混合均匀,冷却到40℃以下,接入种曲。种曲用量为2%~3%,混合均匀后移入曲池制曲,曲层厚度为25~30cm,品温控制在30~32℃,最高不得超过35℃,曲室温度28~32℃,曲室相对湿度在90%以上,制曲时间3d。在制曲过程中应进行 2~3次翻曲,获得成曲。成曲与温度为45~50℃、浓度为12~14°B',e盐水按1∶1均匀混合入发酵池进行固态发酵。为防止酱醅氧化,应在酱醅表面撒上盖面盐。固态发酵时间14d后,加入二次盐水,进入稀态发酵。二次盐水浓度为18°B',e,温度为35~37℃,二次盐水加入量为成曲原料的1.5倍,加入二次盐水后酱醅成稀醪状,然后进行保温稀发酵。保温稀发酵保持品温 35~37℃,发酵时间 15~20d。后期发酵温度28~30℃,发酵时间30~50d。
在保温稀发酵阶段,应采用压缩空气对酱醪进行搅拌。
(五)酱油的提取
酱油的提取方法根据生产规模和生产工艺不同而不同,天然晒露发酵、稀醪发酵和固稀发酵一般采用压榨法取油。而固态低盐发酵和固态无盐发酵一般采用浸出法取油。
1.浸出法
浸出法是我国1959年根据怡糖生产中“淋缸”的原理开发的一种酱油提取技术,取代了传统的杠杆式压榨工序。
浸出法包括浸泡和滤油两大步骤。浸泡的目的是使酱醅中的可溶性物质尽可能多地溶入浸提液中。影响浸提效率的主要因素包括浸出物的分子量、浸泡温度和被浸出物质在浸提液中和酱醅中的浓度差等。酱醅中的糖、盐分等小分子物质很容易溶出,而含氮大分子溶出的速度较慢,需要长时间浸泡。浸泡温度越高,浸出物越容易溶出。浸提液量大,浓度低,则浸出物量多,需要的浸泡时间短。影响滤油的因素主要有过滤面积、酱醅阻力等。酱醅阻力主要与酱醅的疏松程度和厚度有关。酱醅越疏松,酱醅层越薄,过滤速度越快。如果成曲质量差,或发酵不彻底,酱醅发黏,则大大减慢过滤速度。
酱油的浸出工艺流程如图2-7所示。

图2-7 酱油的浸出工艺
酱醅成熟后,如果是原池淋油发酵,在发酵池中直接加入上批二淋油浸泡。如果是移池淋油,先将酱醅移入淋油池。淋油池的结构和带假底的发酵池相似,但面积更大。移池时要注意轻取轻放,过筛入池。醅面应平整,以保证淋油池各处疏密一致,浸泡均匀。二淋油的加入量视产品规格、原料出品率而定。二淋油先预热至 80℃左右,以保证浸泡温度在60℃以上。加入二淋油时,注意水流要缓慢分散,以免破坏醅层的疏松结构。
浸泡2h左右,酱醅慢慢上浮,然后逐步散开。如果酱醅整块上浮后,一直不散开,则说明发酵不好,酱醅发黏,滤油会受到一定的影响。浸池 6h左右,淋出头油流入酱油池内。池内预先加入食盐,流出的头油通过盐层将食盐逐渐溶解。
当头油即将滤完,酱渣刚露出液面时,加入80℃左右的上批三淋油,浸泡2h左右,淋出入二油池,按同样的方法溶解食盐,即为二淋油,70℃保温保存,以供下批淋头油用。
待二淋油即将滤完,再加入上批四淋油,浸泡2h左右,淋出得三油。最后加入清水, 浸泡1h,淋出得四油。淋出的三油、四油同样应保温保存,以免污染杂菌,影响下批生产。
淋油完毕,要求酱渣(干基)中食盐及可溶性无盐固形物含量均不得高于1% (原料配比是豆饼∶麸皮为6∶4)。酱渣主要用作饲料,也有些厂用于生产种曲。
2.压榨法
随着生产规模扩大,压榨取油逐渐兴起,最早使用的压榨设备为杠杆式压榨机。此后又经历了螺旋式压榨机、水压式压榨机。从结构或滤布材质上都有很大改进,生产效率更高,劳动强度也逐步降低。
(1)杠杆式压榨机 杠杆式压榨机是早期使用的酱油压榨设备,将成熟的酱醅装入布袋置于木榨箱中,利用杠杆一端悬挂重石榨取酱油。其结构主要有支架、支脚、杠杆、底板、榨箱、盖板、拉杆及加压架。取成熟豆酱置于缸内,加入母油和匀,灌入布袋内,压榨后得套油。套油中再加成熟豆酱轧出双套油。由头渣及二渣加盐水套榨母油。该设备劳动强度大,生产能力小。
(2)螺旋式压榨机 螺旋式压榨机的榨箱有木制的,也有用钢筋水泥的。榨袋用布袋或麻袋。将成熟的酱醅加入相同数量的盐水混合成酱醪后浸泡1d,榨出头油,头渣中加入盐水用量约为酱的80% (根据出品率而定),搅匀后,压榨出二油,加盐至20°B',e左右,作为下次榨头油用。二渣再加入淡水,用量约为酱的70%,压榨出油,加盐至17°B',e,作为下次榨二油用。经过第3次压榨后,残渣从袋中取出。
(3)水压式压榨机 水压式压榨机的榨箱全部采用钢筋水泥。将酱醪灌入榨袋压榨,初淋出来的酱油比较浑浊,用此酱油冲洗榨箱(袋)壁酱醪,待淋出酱油清澈后,开始逐渐加压,直至榨干后,从麻袋中取出头渣。头渣很坚硬,须以机械轧碎,再放置于贮醪池内,加入三油浸泡,并以压缩空气不断翻拌使之成稠厚的酱醪状,再次装袋榨干。一般稀醪发酵的酱醪要压榨2~3次。
(六)酱油的加热调配
1.加热
从酱醅中浸淋或压榨出的酱油称为生酱油,生酱油需经加热灭菌和调配后才能成为各种等级的成品酱油。通过加热,杀死某些耐盐微生物,如耐盐酵母;破坏微生物所产生的酶,特别是脱羧酶和分解核酸的磷酸单酯酶,避免继续分解氨基酸而降低酱油的质量;除去悬浮物;调和香气;促进氨基酸、糖等化合物发生反应生成色素,从而增加酱油的色泽。
酱油的加热温度,因品种不同而异。高级酱油具有浓厚风味,且固形物含量高,因为加热会使有些风味成分挥发,甚至产生焦煳味而影响质量,因此加热温度不宜过高。而对于固形物含量低、香味差的酱油,加热温度可适当提高。一般采用65~70℃处理30min;也可采用80℃连续杀菌。高温长时间的处理容易导致酱油中低沸点的风味物质损失,因此酱油的灭菌也常采用高温瞬时杀菌。
2.调配
由于生产过程中原料、操作、管理等的差异,每批酱油的质量不尽相同,各有优劣。但要求出厂的成品酱油应不低于国家质量标准的等级所规定的各项指标,并保持本厂产品的风格。所以,要根据国家质量标准和本厂标准,将不同批次质量不同的酱油进行调配(俗称拼格),同时调配过程中添加某些添加剂,可调整产品的风味,提高产品的保质期。常用于调整鲜味成分的有谷氨酸钠(味精)、鸟苷酸、肌苷酸等;调整甜味成分的有砂糖、甘草、饴糖等;调整芳香成分的有花椒、丁香、桂皮(浸提液)等;用作防腐剂的有苯甲酸钠、山梨酸钾等。
(七)酱油的贮存及包装
已经配制合格的酱油,在进入包装工序之前,要经过一定时间的贮存期。贮存对于改善风味和体态有积极作用。一般把酱油静置存放于室内地下贮池中,或露天密闭的储罐中,这种静置可使酱油中细微的悬浮物质缓慢下降而进一步澄清。酱油中的挥发性成分在低温静置期间,能进行自然调节,各种香气成分在自然条件下部分保留,对酱油起到调熟作用,使滋味适口、香气柔和。
包装前要明确产品等级,计量准确。包装好的产品要做到清洁卫生,标签整齐,并标明包装日期。成品库要保持干燥清洁,包装好的成品避免日光直接照射或雨淋。
五、酱油成品质量标准
目前我国酿造酱油的质量主要依据国家标准GB 18186《酿造酱油》,该标准对高盐稀态发酵酱油和低盐固态发酵酱油的感官特性和理化标准做了详细规定。
(一)感官特性
国家标准GB 18186—2000规定的酿造酱油的感官标准见表2-6。
表2-6 酿造酱油的感官标准

(二)理化指标
国家标准GB 18186—2000规定的酿造酱油的理化指标见表2-7。
表2-7 酿造酱油的理化指标

(三)铵盐
铵盐的含量不超过氨基酸态氮含量的30%。
(四)卫生指标
卫生指标应符合酱油卫生标准GB 2717的规定。
思考题
1.酱油酿造过程中主要有哪些微生物参与?它们的作用分别是什么?
2.酱油酿造的常用原料包括哪些?对原料进行蒸煮处理的目的是什么?
3.简述酱油酿造的生化机制。