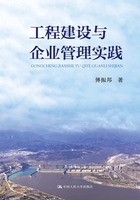
三峡工程施工质量控制的主要难点与对策*注11
三峡工程是我国也是世界最大的多目标开发的水利枢纽工程。国家领导人十分重视三峡工程的施工质量,对此曾多次作过重要指示。本文将对工程开工6年多以来的施工质量作一简要回顾,并探讨进一步改进的主要措施。
一、已建工程施工质量总体良好,满足设计要求, 但距世界一流水平尚有差距
三峡工程总工期17年,1993年开始施工准备,1994年12月正式开工。1997年11月8日成功实现大江截流,标志着第一阶段施工的顺利完成和第二阶段工程的开始。目前,第二阶段工程施工正在紧张进行中。
截至1999年5月底,三峡工程已完成固定资产投资384亿元。完成的主体工程和导流工程量如下:土石方开挖1.10亿m3,约占设计总工程量的95%;土石方填筑2.447万m3,约占设计总工程量的73%;完成混凝土浇筑578万m3,约占设计总工程量的20%。6年多以来,共进行单元质量评定76 647个,其中合格率100%,优良率78.5%;合同项目已竣工验收473项,其中优良189项,优良率40%。已竣工投入使用的永久建筑物和主要临时性建筑物,如西陵长江大桥、对外专用公路、导流明渠、二期围堰等,投入运行后状况良好。大江截流优质、安全完成,高度80余m的二期深水围堰仅在一个枯水期内就高速、优质地建成,随即在当年经受了8次洪峰的考验,这表明我国截流和围堰施工已达到世界先进水平。
但综合分析表明,三峡工程的施工质量距世界一流水平尚有差距。在已进行的工程建设中,出现过数起施工质量事故,例如,混凝土纵向围堰堰内段的混凝土曾出现裂缝和缺陷、左非11#坝段混凝土架空、右非5#坝段的混凝土低强,以及临时船闸闸门事故等。虽然已发生的事故均为局部性的,且发现后及时进行了严格的处理,不会留下影响工程安全的隐患,但在施工质量管理上已显露的薄弱环节,必须引起高度的重视。同时,过去6年多主要进行的是土石方工程施工,混凝土工程施工仅仅是开端,大规模的金属结构和机电安装尚未开始。面对今后更为艰巨、更为严格的施工任务,施工质量控制形势严峻。根据朱镕基总理“千年大计,国运所系”的重要指示,需要进一步努力提高全体三峡建设者的质量意识,采取更为有效的技术措施和管理措施,力争下一阶段施工质量能有新的更好的保障。
二、三峡工程施工质量控制存在诸多技术难点, 必须加大技术投入与技术创新
过去6年多三峡工程施工主要以大规模的土石方开挖和填筑为主。应该指出,国内对此本已具有与国外先进水平不相上下的技术和经验,三峡工程已完成的挖填工程,质量是优良的,特别是建筑物基础开挖和处理、大江截流、二期深水围堰等,均具有世界一流的施工质量。自1999年开始,三峡工程施工进入超世界水平的高强度混凝土施工阶段,2000年以后,又将面临特大型金属结构、巨型水轮发电机组安装的难题。为确保2003年首批机组发电、永久船闸通航,施工质量控制将经受更为严峻的考验。
1.大规模高强度混凝土浇筑问题
三峡工程混凝土现场浇筑施工强度是超世界水平的,1999—2001年混凝土浇筑的年强度均将超过400万m3,2000年强度必须达到500万m3以上。而目前世界最高年混凝土浇筑强度是304万m3(伊泰普水电站),国内曾经达到的最高年强度是203万m3(葛洲坝工程)。在超世界水平的持续高强度浇筑施工中,要确保一流的质量,难度大、任务艰巨。
经过多年的反复比较研究,三峡大坝混凝土浇筑确定采用以塔带机为主,辅以高架门机、塔机和缆机的综合施工方案。为此,项目法人——中国长江三峡工程开发总公司已购置了一批特大型的混凝土浇筑施工机械。其中6台进口的塔带机,是一种将塔式起重机和皮带运输机相结合的新型混凝土浇筑机械,可实施从拌合楼到浇筑仓面连续作业的混凝土浇筑。塔带机可在控制半径100m范围内浇筑混凝土,生产率为常规起重机的2~3倍。三峡工程使用特大型的现代化混凝土浇筑机械,可以达到很高的生产率,但也要求有很高的运行操作、维护和管理水平。国内施工队伍面对这一大批进口大型施工设备,将其熟练掌握,使其持续高效运行,已成为混凝土施工进度和质量控制的最大难点。为此,现已制定了严格的施工设备操作规程和维护管理规则,强化了施工组织管理和施工操作人员的培训,选聘了专门的施工设备监理。同时,总公司还聘请对塔带机使用有一定经验的美国阿廷森公司技术人员作现场施工咨询。
为了确保高强度浇筑混凝土的质量,特别是提高混凝土的耐久性,总公司组织国内有关科研院所对混凝土设计指标和配合比进行了长达两年多的研究和试验,使混凝土设计及配合比均达到了较高水平。三峡工程混凝土耐久性设计指标高于一般工程,如大坝内部150#混凝土的最大水胶比为0.55,抗冻性指标要求为D100;外部200~250#混凝土的最大水胶比为0.45~0.55,抗冻性指标为D250。三峡工程混凝土原材料质量要求高,水泥选用525#中热大坝水泥,为防止混凝土碱骨料反应和有利于温控防裂,对其含碱量和氧化镁含量提出了较国标更严格的要求;掺和料选用一级粉煤灰,是国内外水利水电工程的首例;减水剂和引气剂等也在对多种产品反复试验的基础上选定了最优的产品。试验室150#人工骨料混凝土(四级配)的单位用水量可降至85kg/m3左右,为混凝土质量保证奠定了良好的技术基础。
2.混凝土温控防裂问题
三峡工程大坝混凝土浇筑块体尺寸大,温控条件更显苛刻。夏季气候炎热,且全年各季节均常有寒潮。根据进度安排的要求,高温季节也必须进行浇筑,包括基础约束区的混凝土浇筑。因此,混凝土温控防裂任务非常艰巨,其主要目标是:尽可能地减少一般性裂缝,力求避免产生危害性的裂缝,特别是迎水面的劈头缝和基础贯穿性裂缝。
截至1999年5月底,三峡工程已累计浇筑主体工程混凝土578万m3。已浇筑的混凝土中曾产生了一些裂缝,对已出现的裂缝,虽都已进行了处理,但这也充分反映了混凝土温控防裂任务的艰巨性。总结前一阶段温控防裂问题的经验教训,参照国内外混凝土温控防裂理论和实践,已经和将要采取的主要措施是:
(1)大坝采用设置两条纵缝的方案。设置两条纵缝后的浇筑块体尺寸仍较大,其中最大浇筑块体尺寸可达1 200m2以上。针对不同部位、不同季节的浇筑,设计时提出了严格的温控标准,包括混凝土出机口温度、入仓温度、浇筑温度、混凝土最高温升等。夏季浇筑混凝土时,除要求出机口温度为7℃以外,还需要采取初期通水冷却等相应措施。
(2)混凝土制备共设有5个混凝土拌合系统,共9座拌合楼,总生产能力约为2 400m3/h。混凝土拌合楼均配备了大容量的冷却设施,已试验成功的二次风冷和加片冰拌合的新工艺,能在夏季生产出7℃的低温混凝土,为混凝土温控防裂提供了必要的基础。同时,通过施工工艺和管理的改进,加快入仓速度,有效保温、降温,减少混凝土运输过程和仓面的温度回升。夏季混凝土要确保出机口温度为7℃,混凝土浇筑温度要求不高于14℃~16℃,力争更低。
(3)根据分析,三峡工程已浇混凝土出现的裂缝,大部分与浇筑块长间歇和寒潮冲击有关。据统计,混凝土层间间隙期超过15天,若遇较大气温骤降,又无良好的保温措施,则极有可能产生表面裂缝。表面裂缝如不及时处理,或原坝块温度应力已至极限,则表面裂缝很可能会发展成为危害性裂缝,因此力保浇筑短间歇和均匀上升,是三峡工程防止裂缝的关键措施之一。根据现场试验研究,今后建筑物基础将采用无盖重固结灌浆,可有利于避免基础块混凝土因等待固结灌浆而形成长间隙。河床厂坝段建基面总面积16.42万m2,如果全面铺开浇筑,现有的制冷混凝土供应和设备浇筑能力均难达到。为此,必须对大坝混凝土浇筑作出相应的细致的施工安排,力求做到短间歇均匀上升。
(4)加强新浇混凝土的养护和保温,防止寒潮冲击,对防止裂缝有很大的作用。这是一道较为常规但却往往被忽视的工序。根据前一阶段执行中存在的问题,已明确要求监理和施工单位,对混凝土的保温和养护要像钢筋、模板等工序一样将其作为一项专项工程对待,设专门人员和专业队伍负责,并将其纳为工程质量检查评价的重要项目。为了防止上游面产生劈头缝,我们正拟采用模板内侧贴聚苯乙烯板作为永久保温层。
3.永久船闸高边坡稳定的质量安全问题
三峡工程双线五级连续式永久船闸最大水头达113m,为当今世界规模最大、技术难度最高的通航建筑物,建成后将成为长江航运的控制性工程。永久船闸系在枢纽左岸山体中作深切开挖修建,其中主体建筑物段长1 607m,将形成最大坡高170m、下部高约60m直立墙的高陡边坡。永久船闸闸室采用薄混凝土衬砌结构,需依靠岩体自身维持结构稳定。确保深挖后高陡岩石边坡的稳定性,并控制变形量(特别是开挖完成后的残余变形量),是三峡工程最具挑战性的项目。根据多年研究的成果,已决定采用岩体排水、控制爆破、喷锚及预应力锚索加固等一系列措施,以确保高边坡的稳定性和安全性。
永久船闸闸室部位两侧山体内,各布置有7层贯通全长的排水洞,各层排水洞间设有排水孔帷幕。目前排水洞及排水帷幕已施工完毕,排水效果良好。在永久船闸近4 000万m3总开挖量中,需进行爆破开挖的坚硬岩石约2 000万m3。在实地爆破试验的基础上,对爆破程序、爆破参数作了严格的控制,并规定采用预留保护层和预裂爆破、光面爆破等防震工艺,同时严格控制梯段爆破的单段起爆药量。为了保证高边坡的稳定和限制其变形,除施工期及时进行锚杆和喷混凝土支护外,船闸边坡还设有系统结构锚杆和大量的预应力锚索。
目前,永久船闸高边坡开挖已接近尾声,混凝土浇筑已开始进行。1999年4月,国内一批著名岩石力学专家、院士汇集三峡工地,对永久船闸高边坡的稳定安全性问题进行了一次全面的分析和鉴定。其结论为:从现有的监测资料分析,高边坡的总体稳定情况是好的,但鉴于已发生的局部块体塌落和相当数量的不稳定楔形块体,局部稳定和安全问题仍需要引起特别的重视,应予专门研究、解决。已观测到的高边坡最大变形值列示于表1。
表1永久船闸不同部位累计最大变形表
(截至1999年4月底)
4.大批量特大型金属结构制造安装问题
三峡工程二期施工金属结构总重量达24万t,需安装各类闸门共282扇,各类启闭机135台,以及14条压力钢管等。其中,设计总水压为63 000kN的大坝泄洪深孔弧形门、单扇门重867t的船闸人字门、114台大容量液压启闭机、直径12.4m的压力钢管,都是国内外罕见的特大型金属结构。二期金属结构总量大,而且多数结构尺寸大,受力条件复杂,技术要求高,制造、安装难度很大。由于整个金属结构安装时间仅两年左右(包括与混凝土浇筑互相交叉作用的工期),安装施工强度极高。为了确保金属结构制造和安装的质量,将采取如下措施:
(1)慎重选择设备制造厂商。对主要设备制造厂商的选择,着重比较其信誉、加工制造能力和实际业绩,并兼顾报价。目前,永久船闸和河床大坝、电站的闸门采购招标都已经完成,经过公开竞标,最后选择了武昌造船厂和江南造船厂等大型制造厂家。对启闭机及其拖动、控制设备的制造供应,将采取适当集中且由主设备供应厂家总负责的方式,并正在研究由设备供应厂家负责安装、调试运行的方案。
(2)加强对金属结构制造的监造和安装监理。根据临时船闸部分金属结构设备出厂时就存在缺陷的教训,已确定按合同项目聘任有资质的监理单位,统一负责金属结构设备制造过程中的驻厂监造和现场安装过程的监理。
(3)总公司已与水利部和国家电力公司所属的两个金属结构质量检测中心签订协议,由两中心派出人员,在工地建立三峡工程金属结构质量监督检测中心,统一负责全工地的金属结构设备出厂和安装过程中的检测工作,以确保其质量。
5.大型水轮发电机组的制造安装问题
三峡工程机组单机容量为700MW,不仅是世界上最大的水轮发电机组,而且因防洪的需要,在汛期需降低水位运行,故其运行水头变幅达52m,最大水头与最小水头的比值达1.85,使其设计、制造和安装难度超过世界上已有的任何大型机组。设计和制造的主要难点是,如何既确保机组运行的稳定性,又获取较优的能量指标和气蚀性能。在经过长期科学研究并选定机组基本参数后,通过国际招标,总金额达7.4亿美元的三峡电站左岸14台机组制造合同已于1997年9月正式签订,由世界著名制造厂商组成的两家跨国集团联合体,将承担机组制造任务。我国国内水轮发电机组制造厂商,将通过分包部分制造任务和技术转让,以掌握三峡机组的制造技术,为今后承担另外12台机组的制造任务打下基础。
机组采购合同签署已近两年,合同执行情况一直良好。由于三峡工程首批14台水轮发电机组将在9个国家的17家制造厂内加工制造,监造难度很大。为了确保机组的制造质量,总公司通过国际招标,已与由法国技术监督局和法国电力公司组成的联合体(BV/EDF)签订了机组监造合同。监造工作即将在各制造厂家全面展开。
三、强化质量管理,建立严密的质量保证和 监控体系,确保施工质量
为了确保三峡工程第一流的施工质量,除在技术上采取措施外,更重要的是加强质量管理和控制。由于三峡工程本身的规模和特点,在质量管理和控制方面同样面临着一系列的难题和挑战。
1.为了提高施工承包商素质,必须既严格要求,又适当支持
三峡工程与国内在建的二滩、小浪底工程不同,其施工任务全部由国内的施工企业承担。目前在三峡工地参加建设的主要有5家施工承包商,施工总人数约2万人。通过国内公开招标选定的参建施工队伍都是来自国内优秀的大型水电专业施工企业。由于我国的社会主义市场经济尚处在发展形成的初级阶段,国内水电施工企业尚未经过完全市场形态下激烈竞争的洗礼,而且大多背有沉重的历史包袱,因此其管理水平与世界一流施工企业相比尚有较大的差距。通过前一阶段三峡工程的施工实践,国内承包商在施工质量管理上已显露出的主要问题是:施工工艺作风粗糙,虽有管理制度但不能严格执行,特别是质量意识薄弱。此外,对三峡工程引进的大型现代化施工设备不熟悉、承包商自身经济状况不佳等,对施工质量均有较大影响。针对这些情况,我们主要采取了以下措施:
(1)严格按市场法规执法,禁止工程转包和无序分包。虽然三峡工程从开工之始即坚持实行招标投标制和合同管理制,所有施工队伍都是经过招标签订合同后才进入三峡工地施工的,但仍有某些施工企业在中标后,为降低成本,将任务分包或转包给资质和能力较差的小型企业或个体户,大量使用不熟悉施工项目的民工,一度造成对施工质量的不良影响。经过自1994年末以来几次大的整顿,三峡工地的建筑市场逐步规范。新的合同条款已规定:严禁转包;分包须经总公司同意;劳务合作中招用的民工,仅限于非技术工种,且必须经培训后才能上岗。
(2)根据一期工程验收中提出的问题和相应建议,近一年多以来,各施工承包商都在质量管理和控制上加大了工作力度,具体包括:大力开展队伍培训,努力提高全员的质量第一的意识;配备、训练各级质检人员,各级质检人员必须持证上岗;建立健全三级质量控制责任制,完善质量保证体系;加强混凝土施工全过程的质量控制。当前各承包商虽都已建立了各自的质量保证体系,但仍存在具体执行监控不严的问题。因此,在质量控制上,已实行承包商自身和监理单位的双重监控,要求在各个施工环节上,都能严格执行有关质量控制的规定。
(3)既严格以合同为依据,又实事求是地灵活处理合同经济问题,为承包商创造较为宽松的经济环境,建立合同执行全程激励约束机制。具体做法包括:适当延长预付款的回收时间;采用无息垫资的方式,支持施工承包商自行购买能与塔带机等高效设备相适应的配套设备;设立阶段目标进度质量奖,变终端控制为过程控制。
2.强化施工监理,充分授权,在质量控制上严格“执法”
朱镕基总理在去年年末视察三峡工程时,曾反复强调发挥监理作用的重要性,并要求提高监理的地位,使其真正在质量控制中发挥监督和保障的作用。三峡工程建设从开工之日起,即全面实行了工程监理制度,通过招标选定了几所大型水电设计院作为监理单位,目前在现场执行监理任务的约有600人。几年来,各监理单位在质量、进度、投资控制方面都起了重要的作用,但也确实存在监理不严、监督失控的问题,特别是没有实行重要部位和工序的现场旁站监理制度,致使发生了一些本可避免的施工质量事故。
实行工程监理制,是国外工程建设的成功经验。我国引进监理制的时间还不长,经验也不多。目前,监理业务多作为水电设计院的副业,监理本身尚未形成社会化服务的独立产业。现有担负监理工作的多数是设计人员,他们室内工作能力较强,而现场施工经验不足。鉴于一期工程监理的经验教训,在三峡总公司与监理单位签订的二期施工监理合同中,已提高了监理费用的标准。同时要求各监理单位强化培训措施,优化监理人员构成和知识结构,提高监理人员的素质;根据监理单位应能独立评价质量的要求,支持各监理单位加强监测手段的配备,如建立独立的混凝土试验室等;明确规定二期施工期间,监理人员必须对隐蔽性工程和混凝土浇筑实施严格的旁站监理,切实杜绝重大质量事故的发生。
3.工程业主(项目法人)实行项目管理,落实分级责任制,并应用先进信息手段提高质量管理水平
三峡工程规模特大,国内没有一家施工企业能够独立承担全部工程的施工任务,也没有一家设计院有能力承担全部施工监理任务。为此,三峡工程一开始就确定了将整个工程建设划分为多个合同项目,实行分合同分项目管理。实际上,三峡工程每一个主要合同项目的规模和合同金额,均大于或相当于一个常规大型水利水电项目,故工程业主——三峡总公司必须以合同项目管理为基础,建立分级责任制,这是总结6年多的实践所形成的基本管理模式。二期横向围堰工程工期紧、强度高、技术复杂、风险大,施工中围堰的业主项目部、设计、施工、监理均有明确的责任人,且人员现场到位,密切合作、配合,创造了高质量、高速度完成工程项目的成功经验。据此,总公司决定推广二期围堰的管理模式,在明确界定各方职责的前提下,又要求不可以替代各方的责任和权限,特别是要保证监理对质量监控的权威性。
根据三峡工程项目同时施工和分项目管理模式,总公司在三峡工地设有工程建设部,负责全工地的统一组织和协调。总公司与主要参建单位共同组成三峡工程质量管理委员会,全面领导三峡工程的质量管理,负责具体检查、监督、协调、指导各参建单位开展质量管理工作。质量管理委员会负责制定、颁发对整个工程施工具有约束作用的质量标准、规程规范、验收规程、质量评定标准等。执行中,具体的质量管理工作则仍然以合同为基础,由各方对应的项目部门归口解决。至今,三峡工程质量管理委员会已制定了《混凝土单元工程质量检测及评定标准》、《永久船闸岩石地基开挖单元工程质量评定标准》等23个质量标准和技术规定。这些标准和规定均以国家有关规范为依据,并结合三峡具体条件再予细化,使混凝土的浇筑质量控制及有关施工工艺环节的管理更加规范化,更具有可操作性。
为了提高现代化管理水平,总公司在工程建设中还大力推进信息管理技术,与加拿大Monenco 公司共同开发了以施工成本、进度、质量为核心的三峡工程管理系统(TGPMS),在设计、施工、监理、业主单位之间建立了计算机网络,实现了各种工程信息的快速传递与共享。管理的信息化也为质量控制创造了良好的条件。