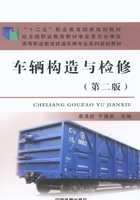
第五节 轮对的故障与检修限度
一、车轴的故障
车轴故障主要有车轴裂纹、车轴磨伤、碰伤和车轴弯曲三种形式。这些故障能引起车辆脱轨、颠覆或燃轴等事故。因此,必须认真检查处理,才能保证行车安全。
(一)车轴裂纹
1.车轴裂纹
车轴裂纹分为横裂纹和纵裂纹。横裂纹是裂纹与车轴中心线夹角大于45°时的一种裂纹;夹角小于45°时的称为纵裂纹。车轴的横裂纹将减小车轴的有效面积,从而影响车轴强度,容易扩展引发断轴事故,危害极大。车轴各部位都可能产生横裂纹,以出现几率来说,多发部位如图2-21所示,轮座周围发生裂纹概率占全部车轴裂纹概率的97%,且多数发生在轮对内外侧边缘。
2.车轴断裂的原因
(1)热切
滚动轴承车轴由于滚动轴承的内圈崩裂、滚子破碎或保持架脱落等原因,引起轴箱激热,产生高温,致使轴颈变形,磨耗剧增,当轴颈截面减少到不能支撑车体载荷时,车轴发生折断现象。

图2-21 车轴裂纹部位
(2)疲劳断裂(冷切)
车辆在长时间的使用过程中都可能产生疲劳裂纹,统计资料表明,一般在使用12年左右车轴宜发生疲劳裂纹。有些车轴过早地产生疲劳裂纹,常常是由于车轴材质不好,或在制造和使用过程中车辆表面造成伤痕,致使疲劳极限下降所致。车轴裂纹发展的过程中,先是金属组织结构发生变化,然后发展成裂纹,所以裂纹末端的金属虽未折断但已受到影响。一般车轴裂纹至折断往往需要一段时间,如果及时检查处理则可以防止车轴折断。车轴出现裂纹时,应将裂纹旋去后,再旋去一定深度的影响层,如果剩余直径符合限度则可以继续使用。
(二)车轴磨伤
(1)轴颈及防尘板座上的纵、横向划痕、凹痕、擦伤、锈蚀、磨伤等。
(2)轴身的磨伤、碰伤、打痕
轴身磨伤常常是由于制动拉杆、杠杆等组装不良而与车轴接触造成的。车轴磨伤处易引起应力集中,造成车轴裂纹。当磨伤深度在2mm以下时,可以将棱角消除,打磨光滑后继续使用;在2mm及以上时,须将缺陷旋除,旋除后的轴身(包括轴中央部)尺寸允许比原型公称尺寸减少4mm。
(三)车轴弯曲
车轴弯曲主要是毛坯车轴锻造时发生的弯曲,其次是由于车辆重车脱轨,使车轴受到剧烈冲击,或组装轮对时车轴与轮对不垂直而造成的。车轴弯曲时,车辆运行振动增大,能造成轴箱发热、轮缘偏磨,甚至发生车辆脱轨事故。沿车轮圆周测量轮对内侧距离时,如果任两处相差超过3mm,则车轴弯曲过限,必须更换轮对。车轴加修时,可将弯曲处旋除,旋除后的轴身尺寸允许比原型公称尺寸减少4mm。
二、车轮的故障
车轮的故障主要有轮缘及踏面磨耗,其次是踏面擦伤、剥离及局部凹下、车轮裂纹等,这些故障直接威胁着行车安全,因此必须认真检查,及时发现,妥善处理。
(一)轮缘故障
1.轮缘厚度磨耗
轮缘厚度磨耗是由于轮缘与钢轨正常摩擦或是由于转向架车轴之间不平行,使转向架出现菱形,承重中心将偏向车轴之间距离较小一侧,使其轮缘与钢轨贴近,加剧轮缘与钢轨的磨耗。轮缘厚度磨耗超限会使轮轨间横向窜动量增加,在通过曲线时,减小了车轮在内轨上的搭载量,容易脱轨;在通过直线时,增加了车辆的横动量,使运行平稳性变差。轮缘厚度过薄,还降低轮缘的强度,易造成轮缘根部裂纹。轮缘厚度检修限度见表2-15。
表2-15 轮缘厚度检修限度(mm)

2.轮缘垂直磨耗
轮缘垂直磨耗是在轮缘外侧垂直方向磨耗,使踏面不保持原弧线形状。其产生的原因基本上与轮缘厚度加剧磨耗的原因相同,但横向力的影响更大些。轮缘垂直磨耗的危害是车轮通过道岔时,轮缘外侧磨耗面容易和基本轨密贴,轮缘顶部更易压伤或爬上尖轨造成脱轨。而且由于磨耗面外形与钢轨内侧面的形状一致,使两者的接触面大大增加,不仅加大了运行阻力,还会使轮缘和钢轨加速磨损。轮缘外侧磨耗面与轮缘顶部未磨耗部分的交点叫做“角点”,如图2-22所示,角点到轮缘根部的竖直距离叫做垂直磨耗高度。运用中车轮垂直磨耗高度大于15mm时,必须更换轮对。定期检修时,发现有垂直磨耗就要旋修车轮。
3.轮缘顶部锋芒
轮缘外侧磨耗使角点与轮缘顶点重合,在轮缘顶点处形成的尖端叫做锋芒。当通过道岔时,轮缘锋芒可能豁开道岔的尖轨而造成脱轨,如图2-23所示。

图2-22 轮缘垂直磨耗

图2-23 锋芒
4.轮缘碾堆
车轮材质过软时,在轮缘磨耗的过程中,轮缘受到钢轨的挤压作用,在轮缘外侧靠近轮缘顶部形成的突起叫做碾堆,如图2-24所示。轮缘产生碾堆后,其危害同垂直磨耗的情况相似,在通过道岔时容易脱轨,发现碾堆即须更换轮对旋修处理。
5.轮缘内侧缺损
轮缘内侧缺损主要原因是意外冲击或事故脱轨造成。其缺损沿圆周方向长度不得超过30mm,宽度不得超过10mm,如图2-25所示。轮缘内侧缺损超限更换轮对。

图2-24 碾堆

图2-25 轮缘内侧缺损
(二)踏面故障
1.踏面圆周磨耗
车轮踏面圆周磨耗是指车轮踏面在运行过程中车轮直径尺寸减小,并改变了踏面标准轮廓。踏面圆周磨耗是一种不可避免的自然磨耗。踏面磨耗的速度随车轮的材质、运用及线路情况而不同。在一般情况下,新旋修车轮在使用的开始阶段(磨合阶段)走行5000km左右,会形成0.5~1mm的磨耗,以后每走行5000km磨耗0.1mm左右。
车轮在钢轨上运动的主要形式是滚动,但在通过曲线等情况下,轮轨间存在着相对滑动,因此,轮轨间发生的是一种滚滑混合的复杂摩擦。在制动时闸瓦与踏面也发生滑动摩擦,引起磨耗。根据这些情况分析,引起踏面磨耗的原因有:当车轮滚动时,踏面与钢轨接触处的材料受挤压和剪切,经多次反复作用,使表层金属疲劳磨耗;制动时,闸瓦与车轮间产生大量摩擦热,当缓解时闸瓦离开踏面后,摩擦热迅速向整个车轮传导而使踏面速冷,如此的时冷时热,易使表面材料变化而造成破坏。实际观察与分析结果表明:车轮踏面的磨耗是踏面表层不断形成厚度在0.05~0.2mm的白硬层和白硬层不断脱落的过程。
踏面圆周磨耗过大,将破坏踏面的标准外形,使踏面与钢轨经常接触部分的锥度变大,使轮对蛇行运动的波长减小,频率增高,影响车辆运行的平稳性。当车辆通过道岔时,车轮由基本轨向尖轨过渡时,车轮产生上下跳动,易砸伤尖轨,并易对基本轨产生瞬间横向力,如图2-26所示;还会使轮缘相对高度增加,易与线路上鱼尾板螺母相碰或切断螺栓造成轨距扩大,引起脱轨,如图2-27所示。车轮踏面圆周磨耗检修限度见表2-16,车轮踏面擦伤深度限度见表2-17。

图2-26 车轮踏面圆周磨耗超限后通过道岔时的几种情况

图2-27 轮缘易与螺栓相碰
表2-16 车轮踏面圆周磨耗检修限度

表2-17 踏面擦伤深度限度

2.踏面剥离
踏面剥离是车轮踏面金属剥落的一种损伤。踏面剥离产生原因主要为车轮材质不良、有夹渣,在运行中经反复辗压,材质疲劳而出现鳞片状剥落,称为疲劳型剥离;另外由于制动抱闸产生高温,在冬天又急剧冷却,经常反复热胀冷缩而在表面出现细小裂纹,经辗压,使金属剥落称为热剥离。踏面剥离会使车辆在运行中产生过大的振动,为了限制踏面剥离对车辆振动的影响,对踏面剥离长度规定了限度,见表2-18。
表2-18 踏面剥离长度限度(mm)

3.踏面缺损
踏面缺损是由于车轮材质不良,外侧辗堆,意外打击及机械化调车作业碰撞等原因造成。其运用限度为自轮缘外侧至缺损处之距离,客车不得小于1505mm,货车不得小于1508mm,缺损部分长度不得超过150mm。
(三)车轮裂纹
车轮裂纹多发生在使用时间过长,轮辋较薄的车轮。裂纹的部位多在辐板孔周围及辐板与轮辋交界处、轮辋外侧、踏面及轮缘根部。车轮裂纹会导致车轮破碎,造成重大事故。对车轮裂纹应认真细致检查,借助锤敲声音及外观象征进行判断。声音清脆为良好,闷哑可能为裂纹;表面有透油黑线、透锈道痕、铁粉附着等都为裂纹外观象征。一旦发现车轮存在裂纹,须停止使用,更换车轮。车轮制造时辗压的重皮可铲去,铲槽深度及长度不超过限度时可继续使用。车轮同一半径断面上铲槽不得多于3条,铲槽两端应平缓过渡,全轮铲槽总长度不得大于300mm。轮辋内侧面上不准有铲槽,辐板沿圆周方向铲槽深度不得超过3mm,轮辋及辐板上均不准有径向铲槽。
(四)轮辋过薄
车轮踏面磨耗超过限度或因其他故障多次旋修车轮,车轮轮辋厚度随之变薄。轮辋过薄时,会降低其强度,引起裂纹;同时由于车轮直径变小,会使转向架等高度降低,影响各部分配合关系。轮辋过薄超过限度时,应更换车轮。轮辋厚度的检修限度见表2-19。
表2-19 车轮轮辋厚度检修限度(mm)

(五)车轮轮辋外侧碾宽
这种故障是由于车轮材质过软引起的。轮辋外侧碾宽的危害是过道岔时,碾宽部分挤压基本轨而造成车辆脱轨,与踏面磨耗的情况相似。运用时车轮碾宽超过5mm时旋修或换轮。
(六)轮毂松弛及轮对内侧距离不合标准
轮毂松弛主要原因是压装时过盈量过小以及振动力过大等,其外观象征有透锈等现象。轮毂松弛易造成轮对内侧距离改变而发生脱轨的危险。当发现轮毂松弛或轮对内侧距离不合标准时,须停止使用。轮对内侧距离的段修限度为轮辋宽127~135mm者最大1359mm,最小1354mm;轮辋宽135mm及以上者最大1356mm,最小1350mm。