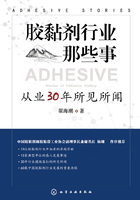
9 水基胶黏剂的历史与前景
水基胶黏剂(Water-based Adhesives)是指可溶于水的高分子物质溶解成适当浓度的水溶液,或不溶性高分子物质借助于表面活性剂的作用在水中分散成微粒子(乳液)配制成的胶黏剂的总称;简单来说,由能分散或溶解于水中的材料制成的胶黏剂就是水基胶黏剂,也常常被称为水性胶黏剂。水基胶黏剂可分为以下几类:①水溶液型,如淀粉或糊精、纤维素及蛋白质类天然胶黏剂,聚乙烯醇、酚醛树脂、脲醛树脂、三聚氰胺树脂等合成胶黏剂;②乳液型或水分散型,如PVAc、EVA乳液,聚丙烯酸酯乳液,环氧树脂乳液,丁苯、丁腈、氯丁胶乳,聚氨酯乳液等;③水性分散液,如水基再生胶或丁基胶等。
水性胶黏剂可以说是最古老一个胶黏剂品种,人类使用水性胶黏剂有着悠远的历史,我国数千年前就已开始使用以水为介质的胶粘物,如用水调和黏土、淀粉粘接石块,用骨胶、鱼胶粘接铠甲、刀鞘等。有许多水基胶黏剂都是从胶乳制得的,初期胶乳指来自橡胶树的天然橡胶分散液,这些早期的水性胶黏剂几乎都是天然材料。天然胶黏剂工业化生产是近代的事,英国在1700年建立了以生产骨胶为主的工厂;美国于1808年建成了第一家胶黏剂工厂,生产血纤蛋白和大豆蛋白胶。天然胶黏剂沿用了几千年,但由于其本身粘接强度不高,耐水、耐温、耐老化、耐介质等性能较差,其使用上受到很大的局限。随着合成高分子化合物的出现,人们开始研制出各种合成树脂胶黏剂,供各种粘接场合使用,这些天然水性胶黏剂便逐渐被取代。直到20世纪初,从美国发明酚醛树脂且发现其可以用作制作胶合板的胶黏剂开始,水基胶黏剂才得到了快速发展。下面主要介绍几个常用水性胶品种的发展历程。
脲醛树脂胶黏剂。脲醛树脂胶克服了溶剂型酚醛树脂的储存稳定性差、易变色、可燃、成本高等缺点,主要用于耐水胶合板、纤维板等。脲醛树脂于1844年由B.Tollens首次合成,1896年前后在C.Goldschmidt等的研究后首次使用,1929年IG公司开发了名叫Kanrit Leim并能在常温固化的脲醛树脂,并于1930年后投入生产。日本1937年开始生产脲醛树脂胶黏剂,1939年将其投放市场。中国自1957年开始生产脲醛树脂,1962年其已成为木材加工中最主要的胶种,占比80%左右。20世纪70年代末,由于脲醛理论的发展,人们采用反传统合成脲醛树脂的制备方法。合成具有Uron环链节的高分子,所合成的树脂有利于提高其胶接制品的耐水性和降低甲醛释放量,缩聚程度较高,树脂的初黏性较好,预压性能提高。脲醛树脂胶的消费主要集中在亚洲、西欧和北美等。
近年来,为了有效控制人造板的游离甲醛释放量,世界各国相继制定了一系列强制性标准和认证。2002年1月,我国颁布了标准《室内装饰材料、人造板及其制品中甲醛释放量》,脲醛树脂中游离甲醛的含量指标分别定为E0、E1、E2三个含量的等级标准。2004年,E0级首次正式出现在国家标准GB/T 9846.1~9846.2—2004《胶合板》中。强制性国家标准的推行,促进了低甲醛释放量人造板用脲醛树脂胶的研究推广工作。近十年来,环保型的低甲醛释放量脲醛树脂胶黏剂在国内大型人造板企业得到广泛的开发与应用。2006年到2015年,我国人造板工业用胶黏剂消耗量年均增长率为10.1%,脲醛树脂胶消耗量约为1392万吨,占人造板工业胶黏剂用量的91%。
尽管脲醛胶有很多优点,但也存在一些明显缺点,主要是耐水性差、耐老化性差,最主要的是产品使用过程中存在甲醛释放超标问题,造成对环境的污染和危害。脲醛树脂胶的缺点非常明显,制约着其应用的范围,为了扩大其应用范围,必须根据不同用途采用不同方法对脲醛树脂进行改性,获得不同性能的脲醛树脂,所以其本身也处在不断的改进和完善之中。
聚乙烯醇缩醛胶。早在1924年,德国科学家 W.O.Herrmann和W.Haehnel发现聚乙烯醇在适当的介质中、酸的存在下,可与羰基化合物发生缩醛反应并申请了专利。不久,I.G.Farben公司合成了聚乙烯醇缩甲醛。1930年,加拿大开始小批量生产聚乙烯醇缩甲醛。1938年,美国成功研制出聚乙烯醇缩丁醛。中国1956年开始研制聚乙烯醇缩醛,参与研制的有天津有机化工实验厂、贵州有机化工厂等。商品化的聚乙烯醇缩醛主要有聚乙烯醇缩丁醛、缩甲醛及少量的缩甲乙醛等混合醛。聚乙烯醇缩醛具有很高的机械强度、卓越的电性能,是生产高韧性、可挠性、耐磨性及高介电度漆包线的重要材料。其生产工艺简单、价格低廉、性能较好,因而得到了迅速的发展,主要用于土木建筑、建筑装修、印刷装订、木材加工、标签粘贴、涂料制造、办公用品、工艺品制造、制鞋、箱包等行业。20世纪80年代后期,聚乙烯醇缩甲醛胶(107胶)在中国大量应用,有建筑行业的“万能胶”之称,但由于存在一系列缺点及游离甲醛刺激性大等问题,国家发改委《产业结构调整指导目录》(2013年修订版)中要求淘汰107胶的使用。
聚乙酸乙烯酯(PVAc)乳液。俗称白乳胶,一般是以乙酸乙烯单体(VAc)为主单体,水为分散介质,聚乙烯醇(PVA)为保护胶体,在引发剂作用下借助乳液聚合或其他聚合方法,均聚或与其他单体共聚制成的聚合物乳液,它具有单组分、使用方便、价格低廉、无毒无害、不易燃等优点,目前,聚乙酸乙烯酯乳液胶黏剂主要用于木材加工中的榫接合,细木工板的拼接,单板的修补及拼接,胶合板的修补以及人造板的二次加工等方面。此外,还用于纸张、布、皮革、陶瓷等多孔性材料的胶合,在建筑业中用作内部装修胶黏剂,或用作乳胶漆的基料。
1929年,德国的H.Plauson首先采用乳液聚合法制得聚乙酸乙烯酯乳液,于1937年实现了工业化生产。20世纪40年代,美国为弥补动物胶的不足,开发出了聚乙酸乙烯酯乳液胶黏剂,主要用于木制品和纸制品的加工,由于这种乳液的粘接性能优于动物胶,又具有良好的工艺性能,因此在家具工业及木制品加工工业中,逐渐代替动物胶,应用面也日益扩大,合成工艺日趋成熟;PVAc胶适应了当时造纸和包装领域的新型、高速机械,加之产品综合性能较好,虽然比动物胶贵,仍受用户的青睐。1950年,日本锤纺、大同化成实现PVAc乳液的商品化生产。20世纪70年代聚乙酸乙烯酯乳液在美国就达到22.7万吨,其中6.35万吨(1972年)用于胶黏剂工业。早期使用的PVAc乳液为聚乙酸乙烯酯均聚物,为了满足不断发展的应用和工艺技术需要,PVAc产品技术自20世纪50~60年代,开发了许多先进的均聚物与共聚物产品如VAE等。1965年,美国空气产品公司开发了乙烯-乙酸乙烯EVA共聚物乳液。1967年,Bayer公司发表了溶液自由基聚合法制备乙烯-乙酸乙烯共聚物。
我国PVAc乳液的研制工作始于20世纪50年代,北京有机化工厂于1965年8月引进日本技术建成我国第一套乙酸乙烯装置,1975年6月自行设计建成了聚乙酸乙烯乳液生产装置。1987年,从日本引进的20个品种聚乙酸乙烯乳液项目建成投产;1988年,我国又引进美国技术建成投产了国内第一套乙酸乙烯-乙烯共聚乳液(VAE乳液)生产装置,极大地推动了我国白乳胶生产技术和市场应用的发展。乙烯的引入,使VAc均聚物高分子链中无规则的嵌段共聚了乙烯软单体,活性增加,产生了内增塑作用,改善了聚乙酸乙烯胶黏剂的粘接性、柔韧性及耐水性等。长期以来,人们一直致力于聚乙酸乙烯酯乳液的改性研究,通过共聚、共混、交联、互穿网络等方法来克服聚乙酸乙烯酯乳液聚合物固有的缺点,改善聚合物的性能,大大拓宽了其应用领域。目前,聚乙酸乙烯酯及其共聚物水性胶黏剂相当廉价易得,它们具有良好的起始胶接强度,有广泛的相容性,易与各种添加剂混溶,可以调节黏度,可配制性能多样的品种而成为用途广泛的通用胶黏剂。1980年世界VAE乳液产量达22万吨,1988年产量已达50万吨,到现在,全球VAE乳液产量已达到300多万吨。国内在2016年VAE乳液产量达到48.5万吨,PVAc乳液产量达到76万吨。随着我国经济的快速发展,VAE乳液的市场前景将一片光明,VAE的应用领域必然将不断拓展。同时相关企业不断努力提高产品质量性能,不断提高固含量满足高速施胶应用;提高乙烯含量,改善对低表面能物质的粘接力;采用多元共聚,适应不同条件下的粘接需求等。
丙烯酸酯水基胶。丙烯酸酯类胶黏剂是由多种丙烯酸酯类单体共聚所得到的一类乳液型胶黏剂。由于丙烯酸酯类单体容易发生自聚或与其他乙烯基单体发生共聚反应,因此可通过分子设计来制备不同性能的丙烯酸酯乳液。作为水性胶黏剂的一种,丙烯酸酯乳液具有安全无公害、合成容易、聚合时间短、使用方便、聚合物分子量较高以及对多种材料具有较好的粘接性能等优点,因而有巨大的商业价值。
1901年,H.V. Pechmann和O. Rohm报道了丙烯酸酯的系统研究;1927年,Rohm & Haas 在德国开始了溶液聚合的聚甲基丙烯酸酯的生产;1928年,有丙烯酸树脂用于生产压敏胶标签及标价条等的报道。1929~1930年,德国的Badische Anilin & Soda Fabrik AG 公司开始首先生产聚甲基丙烯酸酯类分散体,当时以商品名“Corialground”在皮革领域出售。自1930年以来,已有大量关于丙烯酸酯单体、溶液和乳液聚合方法的报道,同时,丙烯酸酯树脂作为胶黏剂的原料也迅速增长,乳液型丙烯酸酯系列胶黏剂在许多应用领域代替天然胶乳。1940年,H.Frikentscher 和 R.Gath报道了用丙烯酸共聚物分散体粘接皮革、木材、纸张。1954年,织物层压用丙烯酸酯树脂胶黏剂就为人所知,到1965年,不少于80%的织物层压胶黏剂是用丙烯酸树脂胶生产的。在1960年前后,丙烯酸分散体作为建筑胶黏剂就站稳了坚实的脚跟。1980年后,丙烯酸乳液(主要为共聚物型)逐步占领市场,而聚乙酸乙烯酯乳液则逐步衰退。1984年,我国第一套从日本引进的丙烯酸溶液和乳液装置在北京东方化工厂建成投产,从此结束了国内该产品长期依赖进口的局面。进入20世纪90年代,北京东方工厂又扩大规模,陆续引进第二和第三套丙烯酸及酯类装置,使其近20个产品在同类产品中名列前茅。1993年,北京东方化工厂又与美国罗门哈斯合资成立东方罗门哈斯有限公司,大大促进了我国丙烯酸酯乳液的发展。
近年来,丙烯酸酯乳液胶黏剂发展逐渐成熟,应用范围也逐步扩大,广泛用于木材加工、材料包装、织物印花、压敏胶、建筑用胶、皮革以及纸张制造等各行业。压敏胶作为丙烯酸酯乳液胶黏剂的一个重要应用,它具有聚合物分子量较大、安全性、经济性等优点,在美国和欧洲,丙烯酸酯乳液型压敏胶在卫生、标贴、日用、保护等方面所占比例较大,但在一些高质量的胶带方面仍难取代溶剂型的胶黏剂。在我国的包装、卫生及标贴方面,丙烯酸酯乳液型压敏胶的用量也是很大的。到2007年,我国生产的各类压敏胶中,丙烯酸酯乳液型压敏胶占总压敏胶市场份额的79.4%。
丙烯酸酯乳液胶黏剂行业不仅有广阔的市场,而且是一个急需发展的行业。目前聚丙烯酸酯乳液胶黏剂正朝着制备工艺精细化、应用多样化的方向发展,具有耐水性、耐候性、耐光性、耐低温、柔韧性的新型聚丙烯酸酯乳液胶黏剂有待进一步开发,重点是通过多元共聚、添加助剂、改进聚合技术等方法。中国胶粘剂和胶粘带工业协会统计,2016年我国聚丙烯酸酯乳液的产量达到304万吨,随着用量的逐日递增,部分企业扩张规模或新建生产线等,陶氏化学计划在四川投资8000万美元建设两条丙烯酸酯乳液生产线,上海东方罗门哈斯拟在上海松江投资1亿元,建设生产用于涂料、胶黏剂等领域的丙烯酸酯聚合乳液,产能提升至5.5万吨/年。
橡胶乳液胶黏剂。氯丁胶乳水性胶是一种常用的水基产品,1965年前后,杜邦公司将水性氯丁橡胶胶黏剂商业化,1972年日本小西公司开始有这类商品出售。水性氯丁橡胶的机械强度与溶剂型氯丁橡胶相近,但存在干燥速率慢与适用时间不当等问题。20世纪70年代,杜邦公司开始销售含羧基氯丁胶乳,它固含量高,可以加少量溶剂改进其干燥性与接触性,此外,还有双组分的胶黏剂,它是将氯丁橡胶胶乳和凝结液两组分用喷枪进行喷雾混合,使之凝胶。20世纪90年代,汽车和木工家具为水性氯丁胶黏剂提供了良好的发展机遇,这时为了改进干燥性与接触性,开发了高固含量、低乳化剂量的胶黏剂,固含量由20世纪50年代的50%~60%提高到了60%~70%。近年来,杜邦公司又推出新产品,如Aquastik 2161氯丁胶乳,它的固含量达58%,其特点是耐高温性、后成型性、触黏性和储存稳定性都好,可粘接金属材料。CR胶乳特别适合制备皮鞋绷帮胶,它可粘接鞋底、鞋尖、帆布、合成纤维,2016年水性氯丁胶乳的用量大约为0.33万吨。天然胶乳来自于橡胶树上流出的胶乳,是一种以异戊二烯为主要成分的天然高分子化合物,天然胶乳具有很好的粘接性,又是优良的弹性体,是各类橡胶中最适合做胶黏剂的,因而在胶黏剂领域得到广泛应用。
聚氨酯水基胶黏剂。1942年,德国人P.Shlack首次成功制备了水性阳离子型聚氨酯,但当时因成本高、稳定性差并未引起重视,直至20世纪60年代末才因环保因素开始迅速发展起来。聚氨酯型水分散体的特点是黏度与分子量无关,具有无毒、无污染、不可燃的性质,且足够高的分子量可以使它形成性能优良的粘接膜,对多种材料具有良好的粘接性。Bayer公司的Dieterich博士发明了内乳化法,合成聚氨酯乳液稳定性提高,成膜性优良,具有极大的工业价值。1967年,聚氨酯乳液首次实现工业化并在美国市场问世。20世纪70~80年代,美国、德国、日本等国的一些水性聚氨酯产品已经从研究试制阶段发展为实际生产和应用。1972年,Bayer公司正式将聚氨酯乳液用作皮革涂饰剂,水性聚氨酯开始成为重要商品。其水性聚氨酯胶黏剂的发展速度明显快于其他的胶黏剂产品,且品种多、产量大。国内水性聚氨酯的研究工作始于1972年,最初目的是用于水性电泳漆的研制,随后开始了皮革涂饰剂、织物整理剂等方面的水性聚氨酯开发。直到20世纪90年代,水性聚氨酯才在中国快速发展。现在水基聚氨酯胶黏剂已开始用于汽车一些零部件的粘接,如汽车内饰件PVC人造革、仪表板、挡泥板、门板、地毡和顶棚内衬粘接等,还可以用于制鞋。复合薄膜及、水性聚氨酯鞋用胶黏剂的使用,近年来一直呈上升趋势。研究表明,若聚氨酯水基胶固含量提高到50%以上,在40~60℃下其干燥速度与普通溶剂型聚氨酯胶黏剂相当。
据报道,2004年Bayer公司的Dispercoll U系列水性聚氨酯胶黏剂用作旅游鞋胶黏剂原料在世界约粘接了2.05亿双旅游鞋(其中中国1.6亿双)。在2006年举办的第十一届世界皮革和鞋材展览会上,2005年中国主要外资合资出口旅游鞋厂几乎全部应用水性聚氨酯胶黏剂,用量已超过万吨。德国是水性聚氨酯胶黏剂用量最多的国家,预计今后水性聚氨酯胶黏剂的用量,每年会增加8%~10%。新型汽车的出现,大大提高了塑料的使用,内饰物上胶黏剂的用量也在增加,荷兰ZENECA RESINS估计,为了满足汽车工业新型塑料零部件粘接的需要,欧洲市场每年需要水性聚氨酯胶黏剂6000多吨。水性聚氨酯胶黏剂是一种极有发展前途的新型复合薄膜胶黏剂。2016年我国聚氨酯水分散体的产量已达到3.7万吨。
水基(性)胶黏剂具有突出的优点,主要是无毒害、无污染、不燃烧、使用安全、易实现清洁生产工艺等,因此有着广泛的应用前景。随着社会的进步和科技的不断发展,水性胶黏剂在建筑业、汽车业、制鞋业、包装业等方面都将得到很大的发展。水基(性)胶黏剂的缺点也非常明显,干燥速度慢、耐水性差、防冻性差。目前水基胶还不能完全取代其他胶黏剂。需要指出的是,现在水基胶黏剂也并非是100%无溶剂的,为了控制水基胶黏剂的流动性,方便现场施胶,往往添加挥发性有机化合物作为其水性介质的助剂。部分水基胶有游离甲醛释放,也并非都环保。
20世纪90年代以来,欧洲生产商更注重产品的高品质,由于欧盟禁止在胶黏剂中使用溶剂,许多公司转向研制新型的高效水基胶黏剂,这也促使了近代胶黏剂和粘接技术的迅速发展。近年水性胶黏剂在产量增长的同时,产品质量也在不断提高,品种增多,一些技术含量高、性能较好的水基胶黏剂不断出现。“十三五”时期,我国水性胶黏剂行业仍处于重要发展机遇期,2016年7月,工信部、财政部联合发布《重点行业挥发性有机物削减行动计划》,要求低(无)VOC胶黏剂产品比例到2018年达到85%以上,这必将对中国胶黏剂行业带来巨大影响,一大批环保不过关的胶黏剂企业将面临淘汰出局的命运,而以水性胶黏剂为代表的环保型胶黏剂产品将获得迅猛发展的机会。相信在可预见的将来,水性胶黏剂等环保型胶黏剂产品将迎来快速发展的春天。2013年,水性胶黏剂在国际市场中占主导地位,占到总销售量的46%。2013年,我国水基型胶黏剂销量持续增长至360.6万吨。预测从2014到2020年,水性胶黏剂市场的年均增长率达5.4%。