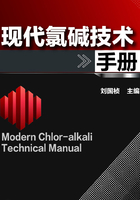
4.5 国产氯碱离子膜的研发
4.5.1 国产氯碱离子膜的发展和现状
我国离子交换膜研究工作起步较早,20世纪60年代中期,锦西化工研究院进行羧酸型离子交换膜研制,以苯乙烯、二乙烯苯、甲基丙烯酸为单体三元共聚得到了羧酸型离子交换膜。1976年三元共聚羧酸膜正式用于北京化工厂年产500t KOH装置中。1978年通过技术鉴定,使北京化工厂试剂级KOH由水银法转为离子交换膜法生产。1983年晨光研究院初步解决了磺酸树脂挤出造粒中的气泡问题。1984年通过挤塑法成功制备了全氟磺酸膜,制成的PTFE网布增强仿Nafion 400膜,同时完成了全氟磺酸膜表面羧酸化改性的实验室工作。
通过“七五”攻关,上海氟材所等单位确定了全氟磺酸及全氟羧酸树脂合成工艺路线与制膜工艺过程,建成了羧酸树脂装置和磺酸树脂装置,试制出小面积全氟磺酸与全氟羧酸增强复合膜,锦西化工研究院先后考核了280多张试验膜,其中最好的膜考核结果接近当时杜邦公司Nafion 901膜的水平,寿命长达151天,平均电流效率为96.2%,但重现性不好。实际上,全氟离子膜并非只是一个膜的问题,而是需要解决从原料、单体、中间体、功能单体、全氟材料增强网、全氟磺酸树脂、全氟羧酸树脂到复合增强离子膜的制备、功能化、涂层材料和涂装设备等一系列核心生产技术,是一个系统工程。
2004年开始,在“十五”国家“863”计划和“十一五”国家科技支撑计划项目的支持下,山东东岳集团和上海交通大学组成的氯碱离子膜研发团队密切合作,展开了漫长的攻关历程。2009年9月,氯碱离子膜团队经历数年攻关,终于突破了一系列关键技术,创造性地解决了项目所涉及的理论难题、技术难题、装备难题和工程难题,并建成了1.35m幅宽的连续化离子膜生产线,生产的离子膜成功应用到万吨级大规模氯碱生产装置中,结束了中国没有全氟离子膜的历史,为我国基础产业氯碱工业的安全运行和健康发展铺平了道路。
4.5.2 国产氯碱离子膜的结构、组成
4.5.2.1 全氟磺酸树脂
全氟磺酸离子交换树脂的分子主链为碳原子和氟原子组成的线性聚四氟乙烯结构,支链是末端基为磺酸或磺酰氟基团的全氟醚结构。由于碳—氟键的结构特点,富电子的氟原子可极化度小,通过分子链旋转,氟原子能紧密覆盖在碳—碳主链周围,形成具有低表面自由能的氟原子保护层,因此全氟离子交换膜具有较高的力学强度、优良的热稳定性和化学稳定性;支链通过醚键固定在全氟碳主链上,末端的磺酸基团由于受到氟原子强烈的吸电子作用而酸性增加,酸性与硫酸相当,在水中完全解离,增强了膜的离子导电性。目前常用的全氟磺酸膜对应的树脂结构如下:
东岳集团产品:x=4~12;y=1;z=0,1;n=2~5
从上述分子式可以看出:国内外全氟磺酸离子交换膜的化学结构都比较类似,只是共聚物链段比例和醚支链的长度略有差别,其中科幕、旭化成和旭硝子公司的膜产品同属长支链型,Dow公司和3M公司的膜产品为短支链型,东岳集团的膜产品既有长支链型也有短支链型。短支链型的优点是比长支链全氟磺酸膜具有更大的IEC值(每克干树脂所含摩尔磺酸基团数量,单位为mmol/g)和更高的电导率。但是,由于短支链单体合成工艺更加复杂,目前为止还没有得到大规模的使用。
山东东岳集团除了合成常规长支链磺酰氟烯醚单体外,还研发了一条不同于现有工艺的合成路线,避开了高温裂解、电解氟化的工艺,能够高转化率、高选择性地制备短支链磺酰烯醚单体CF2 CF—OCF2CF2SO2F。
常规长支链磺酰氟单体(与杜邦公司结构相同)的19F NMR测试结果如图4-43所示。

图4-43 长支链磺酰氟烯醚单体的19F NMR谱图
对短支链磺酰氟烯醚单体的详细测试表征如下:采用BRUKER TENSOR 27型红外光谱仪对单体结构进行了测定;单体纯度在Agilent-6890N气相色谱仪上测定;19F NMR及13C NMR在BRUKER AVANCE Ⅲ 400 MHz全数字化核磁共振仪上测定。
在磺酰烯醚产品的红外光谱图中可以看到,在4000~1850 cm-1波数范围内无任何振动吸收峰,1840cm-1处有中等强度的单峰振动吸收峰,对应—CFCF2的伸缩振动;1464cm-1处有强的振动吸收峰,对应—SO2F的振动吸收峰;1400~1000cm-1对应C—F骨架的强振动吸收峰;1157cm-1处、1133cm-1处对应—C—O—C—强振动吸收峰。根据这些特征峰的存在,证明产品为具有双键结构且含有磺酰基团的全氟类物质,符合预期的化学结构。
通过Agilent-6890N气相色谱仪对产品纯度进行了分析,结果显示产品纯度为99.92%,完全满足聚合要求。
在以CDCl3为溶剂和内标的核磁共振测试谱图上可以得到如下信息(图4-44)。

图4-44 短支链磺酰氟烯醚单体的19F NMR谱图
采用LAP PERKIN ELMER 7 Series Thermal Analysis System(LAP PERKIN ELMER7系列热分析仪)测定了合成的全氟磺酸树脂的热稳定性,测试条件为N2气氛,测试温度30~800℃,升温速率20℃/min;测定结果如图4-45所示。

图4-45 三种不同离子交换容量磺酸树脂的TGA测试曲线
磺酸树脂的热分解温度超过400℃,保证了树脂在熔融挤出复合时稳定不分解,避免了加工生产过程中气体生成而导致的复合膜不可用。
采用德国Brabender公司的转矩流变仪测定树脂的流变性能,测试不同树脂在不同温度下转矩(N·m)随加工时间(min)的变化。测定条件:转速50r/min ,密练机容积49mL。测定结果如下所示(图4-46)。

图4-46 磺酸树脂(IEC=0.90mmol/g)在250℃、260℃、270℃时转矩随测试时间的变化
转矩流变测试能够真实地模拟聚合物在熔融挤出加工过程中所受到的各种剪切和摩擦等受力条件,并能够测得聚合物在加工过程中的转矩随加工温度和加工时间而变化的重要参数和规律曲线。根据这些参数间的变化关系可以确定全氟磺酸树脂在加工过程中熔体黏度的变化规律、熔体加工特性、熔体加工时的热稳定时间及聚合物加工时的降解温度等。这一系列参数都为全氟磺酸树脂实际加工工艺的控制提供了重要的指导依据。
4.5.2.2 全氟羧酸树脂
由于全氟羧酸树脂的应用范围比较窄,对于该树脂的结构及性能研究的相关资料很少,尤其是对于酯基侧基羧酸树脂的耐热性能、加工性能的研究几乎没有,因此全部数据来源于山东东岳集团的研究积累。
最具有实用价值的全氟羧酸树脂的制备方法是以四氟乙烯和带羧酸酯基侧基的全氟烯醚单体共聚合而成。目前可用的含有羧基官能团的烯醚单体主要有以下两种(表4-5)。
表4-5 两种全氟羧酸功能单体的结构

在BRUKER AVANCE Ⅲ 400MHz全数字化核磁共振仪上测定所合成的羧酸单体,19F NMR谱图及分析结果如下所示(图4-47)。

图4-47 酯基侧基羧酸烯醚单体的19F NMR谱图
全氟羧酸树脂的结构为:
图4-48给出了三种不同交换容量的全氟羧酸树脂热重测试曲线,随着IEC值的增加,树脂的热分解温度稍有降低,但热分解温度均高于400℃,可见全氟羧酸与全氟磺酸树脂同样具有优异的静态热稳定性。

图4-48 三种不同交换容量羧酸树脂的TGA(热重)测试曲线
图4-49给出了IEC=0.92mmol/g的树脂在250℃、260℃、270℃下转矩与捏合时间的变化曲线。随着加工温度的增加,羧酸树脂在加工过程中转矩达到平衡所需要的时间明显减少,且平衡转矩值也有所下降。另外,树脂在长时间高温、强剪切作用条件下,转矩均可以保持平衡,无明显降解或交联现象发生,说明全氟羧酸树脂同样具有良好的动态热稳定性。

图4-49 羧酸树脂在250℃、260℃、270℃下转矩随测试时间的变化
4.5.2.3 新型结构全氟磺酸树脂和全氟羧酸树脂
氯碱离子膜材料的开发是氯碱产业的安全运行基础,在全氟离子交换树脂合成方面,经过多年实验研究,东岳集团制备成功了独具特色结构的多元共聚产物全氟磺酸树脂和全氟羧酸树脂,这两类树脂结构通式如下所示:
其中,x,x'=4~12;y,y'=0,1;z=0,1;z'=1;n=2~5;n'=2。
通过聚合工艺调控,使全氟磺酸树脂分子结构内含有少量的酯基羧酸单体结构,也可以使全氟羧酸树脂内含有少量的磺酸单体结构,形成两类性能优异的离子交换树脂:当利用少量全氟羧酸单体与四氟乙烯和全氟磺酸单体共聚合得到新型全氟磺酸树脂时,共聚物的性质将随着全氟羧酸单体含量的增加而发生一系列变化,如聚合物成膜后阻挡氢氧根离子的反渗透能力提高,成膜后与全氟羧酸树脂的匹配度上升,膜层剥离和出现气泡的现象将减少。
4.5.2.4 全氟磺酸/全氟羧酸/全氟增强网复合膜成型制备过程
全氟磺酸树脂与全氟羧酸树脂存在一定的不相容性,当所用的两种全氟树脂的离子交换容量等电化学性能不相匹配时,在电解过程中由于两种基膜的离子迁移数差异过大,以及在两种基膜间水渗透量不平衡而产生较大的内应力,都会引起复合膜层的起泡与剥离。因此,应选用两种相容性匹配的全氟树脂薄膜进行复合,从而获得层间粘接强度较高的全氟离子复合膜。氯碱工业用的全氟离子膜的复合大致采用如下4种方法。
(1)浸胶涂渍法。将增强网布在树脂溶液中进行浸胶处理,使树脂液均匀涂布在增强网布上,然后将此预浸胶的增强网布在一定温度下进行热处理,使树脂胶液层与网布熔融粘接到一起,即制成一定规格的普遍性增强复合膜。
(2)真空转鼓层压法。该法是将膜的增强和复合在真空层压机上一次完成,采用4层层压,即全氟羧酸膜、全氟磺酸膜、PTFE网布、全氟磺酸膜的四层层压,一次完成。
(3)带式真空层压法。该法由Wether等人提出,其设备是两对不锈钢带,也采用四层层压,靠真空的作用将夹在膜中网布上的气体从边缘抽走,同时完成膜的增强和复合。
(4)热滚压法。在增强网布面上紧贴一层具有一定厚度的基膜,然后使之通过加热到基膜熔融温度以上的双滚筒间隙。经过滚筒压延后,将有大部分增强网布包覆在熔膜层内。夹杂在增强网布与熔膜层内部的微量气体,由未被熔膜包覆的痕量网布面层排出。根据所用增强网布与基膜的不同,可制成各种普通型增强复合膜。
以上几种制备全氟磺酸离子交换薄膜的方法均为美国科幕和日本旭硝子等几家大公司所垄断。
通过对大量文献、专利的仔细研究,东岳集团采用直接熔融共挤复合磺酸、羧酸两层全氟薄膜并在线复合增强网布的工艺路线,该工艺目前国外尚未详细报道,主要工艺流程如下:
①将性能相匹配的全氟磺酸树脂粒料、全氟羧酸树脂粒料分别加入共挤出设备不同的螺杆挤出机中,采用熔融挤出工艺将树脂塑化熔融,之后通过分配器进入衣架式机头流延成具有一定宽度和厚度的均匀性两层或三层复合熔膜,在三滚机的牵引和挤压作用下将高温熔膜与预处理过的PTFE增强网布进行在线复合。
②通过热真空装置将PTFE增强网布的节点全部嵌入全氟磺酸膜中,实现增强材质与基膜的紧密融合,之后经冷却、切边、收卷,即制得PTFE网布/全氟磺酸/全氟羧酸树脂增强复合膜。
③增强的复合膜在氢氧化钠溶液体系中转型处理,经水解转型后再双面喷涂亲水氧化物涂层,涂层固化后即得最终的离子膜产品。
图4-50是氯碱用离子膜的制备工艺流程图。

图4-50 国产氯碱离子膜制备示意图
4.5.2.5 东岳氯碱膜的结构与应用
东岳氯碱膜目前包括两种主要类型,一种是适合强制循环槽的高强度DF988膜,另外一种是适合高电流密度电解槽的DF2800系列膜。
DF988氯碱工业用离子膜是无牺牲芯材的离子膜,采用全氟磺酸/PTFE网布/全氟羧酸膜复合而成,其特点是强度高、使用安全性好、适用性强。由于采用具有自主知识产权的专利技术,全氟磺酸层和全氟羧酸层之间形成无界面融合状态,大大提高了两层之间的结合牢固度,具有不易脱层起泡的独特性能。同时,通过层间结构的优化设计和树脂匹配,赋予离子膜以突出的盐水杂质耐受性。
在蓝星(北京)化工机械有限公司的鼎力支持下,山东东岳氟硅材料有限公司建成年产1万吨的我国首套国产离子膜烧碱电解试验装置,使用DF988离子膜于2010年6月30日成功运行,成为中国氯碱工业发展的里程碑。该装置采用蓝星(北京)化工机械有限公司的复极式高电流密度自然循环电解槽,由两种单元槽组成,其中36组膜极距单元槽,36组窄极距高电密(电流密度)单元槽。
该套国产万吨离子膜电解装置为完全国产化的系统,是中国第一套国产离子膜专用生产试验装置,具有代表性和实用性,能够满足国产离子膜工业试验和应用的示范要求,可并入现有氯碱装置同步运行(见图4-51)。

图4-51 中国首套国产离子膜万吨氯碱装置
截至目前,国产DF988膜已成功应用于蓝星(北京)化工机械有限公司位于黄骅的离子膜装置试验基地、山东东岳氟硅材料有限公司、中盐常州化工股份有限公司、上海氯碱化工股份有限公司、山东鲁北化工股份有限公司、苏化集团张家港有限公司、赢创三征(营口)精细化工有限公司、江西赣中氯碱制造有限公司、甘肃中天化工有限公司、江西九江湖口新康达化工实业有限公司、青岛海晶化工集团有限公司、方大锦化化工科技股份有限公司、衡阳建滔化工有限公司和遵义氯碱股份有限公司等多家企业的20余台工业电解槽上,运行指标达到甚至超过国际同类产品水平。国际客户有泰国Siam PVS化学有限公司、泰国Nirankarn有限公司以及德国富玛科技有限公司等。主要适用槽型包括小单极槽、大单极槽、强制循环复极槽、自然循环复极槽以及高电密和膜极距电解槽等几乎目前行业所有槽型,既有钠碱生产也有钾碱电解,其中运行时间最长的是在中盐常州化工股份有限公司的一台F2装置,连续运行时间已经超过3年半,各项运行指标均达到预期效果,产品质量符合生产要求,证明国产氯碱膜在安全性、实用性和适应性方面已经达到工业大规模应用的要求。
DF2800系列氯碱离子膜是一种具有牺牲芯材的离子膜,适合高电密膜极距电解槽,具有最新的离子膜制造技术,是一种低电压、高电流密度离子膜,对盐水杂质具有更高的耐受性。2012年4月1日,DF2801膜(见图4-52)装备在中盐常州化工股份有限公司F2单极电解槽上并顺利开车运行,虽然部分性能指标未完全达到设计要求,但与DF988膜相比,结合槽电压和对杂质良好耐受性的测试结果,表明DF2801膜符合高电密、低电压和更好的杂质耐受性的设计理念和技术要求,为DF2801膜综合性能的进一步提高奠定了基础、指明了方向。

图4-52 DF2801离子膜的牺牲纤维与截面结构
从2014年开始,经过树脂优化、网布升级、结构创新、设备改造等多项科技研发和装置升级,新型号DF2806离子膜问世,并具有更加优异的机械性能。经过改进的DF2806膜陆续应用于营口三征新科技化工有限公司、山东铝业有限公司、上海氯碱化工股份有限公司和陕西金泰氯碱化工有限公司等单位,取得了良好的效果。
4.5.2.6 影响氯碱膜性能的主要因素
(1)膜自身结构的影响。槽电压主要由膜电压决定,膜电压首先由膜本身的结构所决定,较低的膜电阻可以带来较低的膜电压降。一般影响膜电阻的主要因素有:组成膜的复合层的化学结构、复合层的物理结构、复合层的厚度等。另外,磺酸树脂层的膜电导率要高于羧酸树脂层,但同样是相同厚度的磺酸层,膜电阻又随其交换容量的下降而上升。
由于羧酸膜层的电导率较低,因此在保证电流效率的条件下,尽可能减少羧酸层的厚度,有助于降低离子膜的电压降,从而可以降低槽电压。
增强层在膜中可以提高氯碱膜的力学性能,但是因为增强层不导电,而且会影响膜内电流密度的分布,并带来离子杂质在膜面阴极侧的沉积,所以应当尽可能减少增强层的面积,并使增强材料在膜中的分布优化。
(2)表面涂层的影响。氯碱膜两侧的气体释放涂层对膜性能的影响也很重要。缩小电极间的距离,溶液的电压降也随之降低,电解槽的槽电压也会随之减小,从而使能耗更小。但是,当极距缩小到一定程度时,槽电压反而有上升的趋势,这是因为在膜的表面会附着一定数量的气泡,降低膜的导电能力,随着极距的减小,膜与电极之间的距离和空间缩小,附着的气泡会难以除去而越来越多,从而导致膜电压的升高。但是随着膜两侧性能良好的涂层的出现,气泡聚集的问题得以解决,电极间的距离已达到膜的厚度水平,也更对涂层提出了越来越高的要求。氯碱膜两侧的涂层必须是多孔的,以促进溶液主体和涂层之间的传质,若涂层质量不高,则会带来气体难以释放、电压升高、羧酸层脱水、羧酸层过热、水传递下降、降低杂质的溶解以及对外部环境的变化更加敏感等诸多不良的影响。
(3)外部条件的影响。提高温度有利于膜电导率的提高,从而降低膜电压和槽电压;溶液中的杂质会在氯碱膜内部和表面沉积,使膜的电压降升高,槽电压随之升高,能耗增大。
4.5.2.7 氯碱膜国家标准
为更好地保护自主知识产权,规范国产离子膜的科研、生产及应用,山东东岳高分子材料有限公司于2010年提出制定《氯碱工业用全氟离子交换膜》系列国家标准,国家标准化管理委员会审查公示后正式纳入国家标准制修订计划,并经由[2011]11号文件下达《氯碱工业用全氟离子交换膜 通用技术条件》等3个标准的制定任务和计划编号。2013年12月31日,国家质量监督检验检疫总局、国家标准化管理委员会通过2013年第27号公告发布 GB/T 30295—2013《氯碱工业用全氟离子交换膜 通用技术条件》等3项国家标准(表4-6),并于2014年8月1日开始正式实施。该系列标准的制定有助于规范国内离子膜生产、检验、流通和使用,促进国内离子膜产品质量水平的提高,消除相关行业对离子膜通用技术条件无法可依的状态,支持氯碱企业建立监测评价手段,为争取更多权益打好基础。
表4-6 氯碱离子膜相关国家标准

该标准由山东东岳高分子材料有限公司组织起草,同时联合国内多家氯碱企业及离子膜电解槽生产企业共同起草,其中包括上海交通大学、蓝星(北京)化工机械有限公司、中盐常州化工股份有限公司、沧州大化集团黄骅氯碱有限责任公司、沈阳化工集团有限公司、山东东岳氟硅材料有限公司、青岛海晶化工集团有限公司、营口三征新科技化工有限公司等。起草单位中既包括国产氯碱离子膜生产及应用企业,也包括有丰富氯碱离子膜应用和测试经验的单位,这些单位为该标准的制定提供了规范实际的应用经验。
氯碱离子膜目前尚无可供参考的相关国际标准。同时,国产氯碱离子膜的技术在持续进步,应用过程中也待进一步积累经验。但出于对我国氯碱工业安全运行和健康发展的考虑,适时地制定、颁布氯碱离子膜的国家标准,必将促进我国氯碱离子膜产业技术、应用水平和产品质量不断提高,保证氯碱离子膜产品的研发、生产与应用在技术标准的指导下进行。在此系列标准的支撑下,将为氯碱离子膜提供通用的测试方法和应用规范,进一步推动国产氯碱离子膜的应用与推广,有力地支撑我国基础产业的安全运行和健康发展。