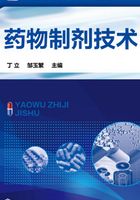
第二节 药物制剂的生产管理
药物制剂的生产管理是为了确保与药物制剂生产有关的各项技术标准及管理标准在生产过程中能具体实施,是药物制剂生产质量保证体系中的关键环节。药物制剂的生产管理包括生产文件管理、物料管理、批和批号管理、生产过程管理等。
一、生产文件管理
1.生产工艺规程
生产工艺规程是为生产一定数量成品所需起始原料和包装材料的数量,以及工艺、加工说明、注意事项,包括生产过程控制的一个或一套文件。
每个正式生产的制剂必须制定生产工艺规程,并严格按照生产工艺规程进行生产,以保证每批产品质量尽可能与原设计相符。生产工艺规程一般由车间技术负责人组织编写,企业生产技术部门组织有关部门会审,企业总工程师或生产负责人批准。
药物制剂生产工艺规程的内容一般包括品名,剂型,规格,处方,批准生产日期,批准文号,生产工艺流程,生产工艺的操作要求,物料、中间产品、成品的质量标准和技术参数及贮存的注意条件,物料平衡计算公式,产品的理论收得率、实际收得率以及计算方法,成品的容器、包装材料质量标准与检验方法等。
2.标准操作规程
标准操作规程(SOP)是指经批准用以指示操作的通用性文件或管理办法。标准操作规程是企业用于指导员工进行管理与操作的标准,是通用性的指示,如岗位操作标准、设备标准操作规程、清洁操作规程、厂房环境控制等。
标准操作规程的内容包括题目、编号(码)、制定人及制定日期、审核人及审核日期、批准人及批准日期、颁发部门、生效日期、分发部门以及份数、标题、正文等。
3.批生产记录
批生产记录是一个批次的待包装品或成品的所有记录,能提供该批产品的生产历史及与质量有关的情况。批生产记录内容包括产品名称、规格、批号,生产以及中间工序开始、结束的日期和时间,操作者与复核者签名,相关操作与设备、工艺参数、控制范围,相关生产阶段的产品数量、物料平衡计算,及特殊问题的记录等。
批生产记录是药品生产过程的真实写照,故应及时填写,字迹清晰、内容真实、数据完整,并由操作人和复核人签名;不得撕毁和任意涂改;更改时,应在更改处签名,并使原数据仍可辨认。
4.批生产指令
批生产指令是一批药品生产的启动性、规划性、证据性文件,往往根据市场需求下达。批生产指令单由生产部负责编制,一般一式四份,一份交质量管理部门,两份交物料管理部门和仓库,一份生产部归档。
批生产指令单包含的内容一般有:产品名称、规格、批号,生产日期,生产数量,生产地点,生产设备编号,各执行和参考的标准操作规程编号,生产过程中的控制及工艺操作要求等。
批包装指令一般与批生产指令分开下达。批包装指令单由生产管理部门根据中间产品检验合格报告单及生产计划编制,一式两份,经生产部门负责人审查,QA审批,于包装前一天下达生产车间与仓库。同品种不同包装规格,必须分别下包装指令。批包装指令的领料量应有理论用量、实际领料量,车间领料时应根据物料的检验报告单折算实际领料量,再开具领料单领料。
二、物料管理
物料管理是指企业对生产所需物料的采购、使用、储备等行为进行计划、组织和控制。
1.物料采购
物料采购是药品生产过程的第一步,也是药品质量保证体系中的第一环节。物料采购一般由供应商选择、生产计划制定、采购计划制定与实施等环节组成。
2.物料接收
物料到货后,物料接收员应对所有到货物料进行验收。验收时主要检查包装的外观,如包装是否完整,有无标签,有无昆虫、老鼠等入侵的痕迹。必要时,还应进行清洁,发现外包装损坏或其他可能影响物料质量的问题,应向质量管理部门报告并进行调查和记录。根据订货单核对标签及其内容,如供应商提供的物料名称、代码、规格等,并清点数量;确认供应商已经质量管理部门批准。一切正常后方可办理入库手续。
入库手续一般包括填写收货单、化验申请单和库卡。这些单据上必须有制药企业内部物料代码、名称、批号(供应商批号和本企业内部管理用的批号)、包装数量及重量等内容,便于识别该批物料的基本信息。
入库手续办好后即可将物料入库。在库卡上填写存放该批物料的库位号,同时将化验申请单交质量保证部,取样员根据化验申请单发放并贴好待检标签,同时根据包装数量按规定取样检验。检验完成后,根据检验结果签发合格或不合格证书并张贴到每个包装箱上。此时物料的状态由待检转变为合格或不合格。
3.物料贮存
物料的贮存应建立库卡,库卡上应用适当的标识。制定物料标识是为了防止物料使用过程中出现混淆和差错,并为文件的可追溯性奠定基础。物料标识的三个必要组成部分是物料的名称、代码及批号。所有物料均应有专一性的代码;同一物料名称但质量标准不同,也使用不同的代码。同代码一样,对每一次接受的物料和拟生产的每一批产品都必须给定专一性批号。
物料的贮存应分品种、规格、批号存放。各货位之间应有一定距离,设置明显标示,标明品名、规格、批号、数量、进货日期、收货人、物料状态(如待检验、合格、不合格)等。
物料应按规定的使用期限和条件进行贮存,并有防潮、防霉、防鼠及防止其他昆虫进入的措施。贮存期内如有特殊情况应及时复检。
4.物料发放
物料的发放应根据生产车间的领料单和包装指令单,按照药品出库“先进先出”、“近效期先出”的原则,由仓库保管员和领料人员共同检查物料的名称、批号、规格、数量等相关内容,并签名。并且必须执行出库验发制度。
仓库所发物料包装应完好,并附有合格证或检验报告单。发料后,库卡和台账上应详细填写物料去向、结存情况等。
5.不合格品处理
收料时,如发现包装破损、受潮、霉变或其他明显不符合标准的物料,仓管员应在收货单上详细记录检查情况,同时填写“物料破损报告”。接到报告后,质量部有关人员及采购人员对以上物料进行检查,确认不能用于生产的,质量部有关人员可在不经留检和检验的情况下做出“不合格”决定,并发放不合格标签,标签上应注明品名、代号、每件包装的装量和包装数、接收日期。仓库管理人员负责将不合格物料直接放入“不合格品”库或特定区域以待处理。
留检物料或(半)成品经质量部检验不合格时,由质量部门发出2份化检证书,分发物料部和仓库。质量部有关人员负责发放红色不合格品标签并贴签,仓库管理人员负责将不合格物料或(半)成品从留检区验转至“不合格品”库并填好相应库卡。
三、批和批号管理
1.批
批是指在规定限度内具有同一性质和质量,并在同一生产周期中生产出来的一定数量的产品。可见“批”反映的最根本问题是在允许限度内的质量均匀性。
据药品生产质量管理规范的规定,各类药品的“批”划分原则如下。
(1)大、小容量注射剂是以同一配液罐一次所配制的药液所生产的均质产品为一批。
(2)粉针剂是以同一批原料药在同一批连续生产周期内生产的均质产品为一批。
(3)冻干粉针剂以同一批药液使用同一台冻干设备在同一生产周期内生产的均质产品为一批。
(4)口服或外用的固体、半固体制剂是以在成型或分装前使用同一台混合设备一次混合量所生产的均质产品为一批。
(5)口服或外用液体制剂是以灌装(封)前经最后混合的药液所生产的均质产品为一批。
2.批号
批号是用于识别不同批次的数字和(或)字母的组合,具有唯一性,可用于追溯和审查该批药品的生产历史。应注意批号不可代替药物制剂的生产日期。
关于批号的编制,国内多数企业采用如下编制方法。
(1)正常批号:年+月+流水号;采用一组数字或字母与一组数字联合使用。如160321,即2016年3月生产的第21批;BX1636,B代表车间,X代表剂型,B车间X剂型2016年第36批。
(2)返工批号:返工批号可在原产品批号后加代号,如“R”。
(3)混合批号:可在批记录中的正常产品批号后加代号,如“M”。
四、生产过程管理
1.生产前准备的管理
生产前准备的管理除检查操作人员是否按进入洁净区的要求进行洗手、更衣外,还包括生产场地的检查、生产前物料的检查、计量用具的检查、设备和器具的检查。
(1)生产前场地的检查:①检查是否有“清场合格证”副本,并核对是否填写完整,是否在有效期内;②检查生产车间的温度、湿度、压差是否符合生产要求;③检查是否有与本次生产无关的物料、用具、文件等。
(2)生产前物料的检查:①生产管理部门根据企业的生产销售情况安排生产计划,并编制生产指令发到生产、物料及质量管理等相关部门,同时将相应的批生产记录发放至生产车间;②生产车间根据批生产指令、生产工艺规程、标准操作规程制定生产指令,由车间工艺技术员向各工序下达生产计划,各工序根据生产计划向仓库领取物料;③领料时,必须根据生产领料单仔细核对物料的名称、代码、规格、批号、生产厂家、数量、检验合格报告单等,并填写领料记录。
(3)计量用具的检查:①检查计量用具是否清洁,是否符合生产要求;②检查是否有计量合格证,是否在校准周期内。
(4)设备和器具的检查:①检查设备是否有已清洁、完好标志,是否在清洁有效期内;②检查设备的各部件是否正常;③检查器具是否清洁,是否完好。
2.生产过程的管理
药物制剂的生产过程应严格按生产工艺规程、标准操作规程进行。在生产过程中要做好以下几个方面。
(1)工序关键控制点的监控及复核:①计算、称量和投料要双人操作;②需严格按生产工艺规程所定的各项工艺参数、标准操作规程规定的操作方法和生产指令进行操作;③严格按生产工艺规程中各工序的质量控制要点进行自检、互检,保证质管员的有效监控;④各关键工序均需进行物料平衡计算,符合规定的范围方可递交下道工序继续操作;⑤各岗位的操作及中间产品的流转都必须在质管员的严格监控下,各种监控凭证均需纳入批生产记录;⑥各关键工序如起草生产指令、投料、灌装、灭菌、灯检、外包装等均要严格复核,防止差错或混淆。
(2)生产过程中的状态标志管理:生产过程中状态标识的使用可以防止生产过程发生混淆、差错、污染等质量事故;也能保证对设备、仪器进行正确操作,防止发生安全事故。故此药物制剂生产过程中应严格遵守生产状态标识使用的各项规定,从而保证药品质量和安全生产;生产企业应有文件规定各状态标志的颜色、状态词、含义等,并全企业统一。
生产状态标识有:①物料标识有待检、合格、不合格;②设备标识有完好、运行、维修、停用、闲置;③管线标识应有管内物料名称、流向,并标识在显著位置;④计量标识有合格、限用、禁用;⑤清洁标识有已清洁、待清洁;⑥生产操作间标识有生产状态卡、清场合格证,生产状态卡上应有所生产产品的名称、批号、规格、数量、操作人、生产日期等信息,清场合格证应有岗位或操作间名称、清场人、清场日期、清场有效期、发证人等信息。
(3)中间站的管理:①中间站存放的物品有中间产品、待重新加工产品、清洁的周转容器等;②应按中间站清洁规程进行清洁,并随时保持洁净,不得有散落的物料;③中间站物品的外包装必须清洁,无浮尘;④中间产品在中间站要有明显的物料状态标记,并注明品名、规格、批号、数量等;⑤中间产品应按品种、批号摆放整齐,不同品种、不同规格、不同批号之间要有一定距离;⑥中间站的管理应参照物料管理,有专人负责;⑦出入中间站必须有传递单,并且填写中间产品进出站台账;⑧中间站必须进行上锁管理,上锁后管理人员方可离开。
(4)生产过程中,应随时注意设备运行情况。若设备出现自己不能排除的故障时,应立即通知维修人员进行维修。
(5)生产过程中若出现停电、通风系统故障、层流操作台故障,应采取正确应急措施,使生产过程中处于受控状态。一般不要打开层流罩门;不要打开通往洁净级别低的门或传递窗;除立即向上级汇报外,应尽可能减少人员走动等。
(6)及时准确地填写生产过程中的各项操作记录。
3.生产结束的管理
生产结束时的主要管理内容有如下几方面。
(1)生产产品的管理。将产品装入周转桶,贴上标签,标签上应注明品名、规格、批号、重量等,并将产品送入中间站。
(2)设备、场地的清洁、清场。操作人员按设备、场地的清洁标准操作规程进行;清场内容包括物料清理、文件清理、用具清理等。
(3)及时填写清场记录。清场记录内容有操作间编号、产品名称、批号、生产工序、清场日期、检查项目及结果、清场负责人及复核人签名等。
(4)清场结束,由QA检查并发放清场合格证。“清场合格证”内容有生产工序名称(或房间)、产品名称、规格、批号、日期和班次、清场人员和检查人员签名等。“清场合格证”副本作为下一品种(或同品种不同规格、不同批号)的开工凭证并纳入批生产记录中。未取得“清场合格证”副本不得进行另一品种或同一品种不同规格、不同批号产品的生产。
(5)批生产记录、批包装记录的审核。批生产记录的审核时应看填写是否完整、规范;是否做到字迹清晰、内容真实、数据完整;是否有操作人及复核人签名;更改处是否签名,原数据是否仍可辨认等。
批生产记录审核的内容有产品名称、规格、批号,生产日期,质量(检验报告书),操作人及复核人签名,有关操作设备,相关生产阶段的产品数量,物料平衡的计算,生产过程中的控制记录及特殊问题的记录等。
每批产品均有批包装记录。批包装记录审核的内容有待包装产品的名称、批号、规格;印有批号的标签和使用说明书及产品合格证;待包装产品和包装材料的领取数量,发放人、领用人、核对人签名;已包装产品的数量;前次包装操作的清场合格证(副本)及本次清场记录及清场合格证(正本);本次包装操作完成后的检验核对结果,核对人签名,生产操作负责人签名等。
(6)产品放行前的审核。药品质量管理部门对物料和中间产品的使用、成品放行有决定权。产品放行前应对有关记录进行审核,审核内容有配料与称重过程的符合情况、各生产工序的检查记录、清场记录、中间产品质量检验结果、偏差处理、成品检验结果等。以上内容符合要求并有质量授权人签字后才可放行。
案例4-1
某药品生产企业生产小容量注射剂,在药液中间产品检验时发现含量偏低,调查结果发现是工人投料时,把“注射用水加至×××mL”看成了“注射用水加×××mL”。
案例4-2
某企业的2名化验人员某日下午进行无菌检查后,次日眼睛患急性结膜炎及手臂皮肤受损脱皮。调查结果发现是他们在进行无菌检查时,忘记关紫外线灯。
根据上面两个案例,思考并讨论:
1.你如何看待这两个事故?
2.如何避免出现类似的事故?