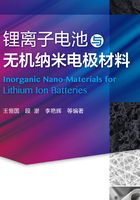
4.3 多孔Fe2O3纳米管的结构表征和形成机理
4.3.1 多孔Fe2O3纳米管的形貌分析
图4-1展示了电纺制备的纳米纤维和多孔Fe2O3纳米管的扫描电镜图。由图4-1我们可以看出,电纺制备的纳米纤维直径约为520nm,具有光滑的表面,其表面没有任何的孔洞和次级结构[图4-1(a)和图4-1(b)]。而高温煅烧后,得到的材料虽然保持着一维结构,但表面出现了大量的孔洞和内部中空的多孔管状结构,而且其直径缩小至400nm[图4-1(c)和图4-1(d)]。实际上,煅烧过程中,聚乙烯吡咯烷酮、有机盐的分解以及Fe2O3的形成导致了直径的缩小,多孔管状结构的形成。

图4-1 煅烧前纳米纤维和多孔Fe2O3纳米管的扫描电镜照片
透射电子显微镜被用来进一步观察多孔Fe2O3纳米管的形貌。图4-2清晰地证实了多孔Fe2O3纳米管的存在,这与扫描电镜的观察结果是一致的。高分辨率的透射电镜也证实了多孔Fe2O3纳米管是由相互连接的纳米颗粒组成的。而且分析其高分辨透射电镜,可以证实0.37nm的晶格间距是Fe2O3(012)面的晶格间距。以上的结果完全可以证实由许多相互连接的纳米颗粒组成的多孔Fe2O3纳米管的存在。

图4-2 不同分辨率的多孔Fe2O3纳米管的透射电镜照片
4.3.2 多孔Fe2O3纳米管的结构分析
图4-3为所制备的多孔Fe2O3纳米管的X射线衍射(XRD)谱图,我们给出了其中典型的晶面峰的晶面参数。从图4-3中可以看出,衍射角2θ为24.15°、33.3°、35.8°、40.6°、49.4°、54.1°、57.4°、62.3°、63.9°和71.9°分别属于(012)、(104)、(110)、(113)、(024)、(116)、(122)、(214)、(030)和(220)晶面的衍射峰。该样品的衍射峰与斜方六面体的赤铁矿(JCPDSNo.33-0664)相对应。由此可知,该方法可以制备赤铁矿(Fe2O3)。从图4-3中还可以看出,没有杂相存在,所制备的多孔Fe2O3纳米管的衍射峰强度较高,说明制备的多孔Fe2O3纳米管的结晶度较高。

图4-3 多孔Fe2O3纳米管的XRD谱图和煅烧前纳米纤维的TGA谱图
热失重分析被用来观察乙酰丙酮铁/聚乙烯吡咯烷酮纳米纤维的重量随煅烧温度变化的关系曲线,其测试温度范围为室温~900℃,升温速率为1℃/min。明显地,在整个温度升高的过程中,由于乙酰丙酮铁和聚乙烯吡咯烷酮的分解导致了电纺纤维膜的重量损失。其失重过程主要包括以下3个阶段:①20~200℃:这个阶段的失重损失可以被归因于水和N,N-二甲基甲酰胺等溶剂的挥发;②200~400℃:这是由于乙酰丙酮铁和聚乙烯吡咯烷酮的分解所导致[25];③400~500℃:这个阶段主要是聚合物分解的残留物被进一步氧化,这与诸多文献报道的结果是一致的[26]。当温度超过500℃时,失重损失则是α-Fe2O3晶体结构改变所导致的,所以本实验中选用500℃作为制备多孔Fe2O3纳米管的煅烧温度。
接下来,我们用XPS来进一步表征样品的纯度、成分和精细结构。由图4-4(a)可以看出,XPS谱图中存在典型的Fe 2p和O 1s峰,可以证实样品中含有铁和氧元素。图4-4(b)中位于711.3eV和724.7eV处出现了铁的Fe 2p3/2和Fe 2p1/2峰,而位于719eV处则是Fe3+的典型特征峰,从而证实了α-Fe2O3的形成。而图4-4(c)中不对称的O1s光谱被分裂成位于529.7eV和531.0eV的两个峰,可以被归因于晶格氧OFe-O和羟基OH-O[27]。为了进一步证实样品的比表面积和孔径分布,我们利用N2-吸附脱附技术对其进行测试。由图4-4(d)中的N2等温吸脱附曲线可知,制备的样品的比表面积为23m2/g。由插图中的BJH孔径分布曲线可知,孔径分布较宽,而且具有明显的介孔结构。

图4-4 多孔Fe2O3纳米管的XPS谱图(a,b,c)和比表面积测试谱图(d)
4.3.3 具有不同形貌的Fe2O3纳米材料的形成机理
为了详细地说明不同形貌的Fe2O3纳米材料的形成机理,我们考察了一系列由含有不同质量乙酰丙酮铁的前驱纤维煅烧后得到样品的形貌。图4-5揭示了由纳米带到纳米管的形貌转化过程。明显地,电纺的纳米纤维应具有光滑的表面,而不具有多孔或者中空的结构。然而,当将这些纤维至于空气中煅烧,随着聚乙烯吡咯烷酮和乙酰丙酮铁的受热分解,氧化生成CO2以及Fe2O3纳米粒子的形成等过程的发生,导致纤维发生了明显的变化。首先,生成的CO2在向外扩散的过程中产生的力迫使形成的Fe2O3纳米粒子移到纤维的表面,从而形成了中空的管状结构。同时,由于乙酰丙酮铁的分解和氧化,导致了相互连接且具有一定空隙的Fe2O3纳米粒子的形成,从而最终呈现出多孔纳米管状结构[28~30]。但是,低浓度的乙酰丙酮铁在煅烧过程中生成较少的Fe2O3纳米粒子,则无法保持管状结构的框架。随后管状框架的坍塌就导致如图4-5(a)所示的带状结构的产生。为了证明这种假设的成立,我们增加乙酰丙酮铁的含量,当含量增至0.3g时,形貌没有发生变化,仍然以纳米带的形貌存在[图4-5(b)]。然而,当含量增至0.4g时,样品则以纳米带和纳米管共存的形貌存在,说明进一步增加乙酰丙酮铁的含量有利于纳米管的形成[图4-5(c)]。继续将含量增至0.5g后,则出现了均匀的纳米管状形貌。显然,我们的假设是成立的。基于以上的分析,不同形貌的Fe2O3纳米材料的形成可以通过调节前驱溶液的含量来实现[图4-5(d)]。低含量时,产生的Fe2O3纳米颗粒不足以支撑管状结构,则形成了带状结构。而高含量时,则可以形成管状结构。

图4-5 由含有不同质量乙酰丙酮铁的前驱纤维煅烧后得到样品的扫描电镜图
4.3.4 多孔Co3O4纳米管的形貌和结构表征
为了进一步验证纳米管的形成机理,并且扩大该方法的应用范围,我们尝试利用该方法制备其他氧化物纳米管。在其他条件不变的情况下,用乙酰丙酮钴代替乙酰丙酮铁,同样可以得到如图4-6(a)和图4-6(b)所示的多孔纳米管。为了进一步表征其多孔管状结构,透射电子显微镜被应用。明显地,得到的材料是由细小的纳米颗粒组成的多孔纳米管[图4-6(c)],这与扫描电子显微镜测试的结果是一致的。为了证明该多孔纳米管的晶体结构,我们测试了其XRD谱图。从图4-6(d)中可以看出,衍射角2θ为31.35°、36.98°、44.93°、59.52°和65.36°分别属于(220)、(311)、(400)、(511)和(440)晶面的衍射峰。该样品的衍射峰与立方体的Co3O4(JCDPS,card no 42-1467)相对应。由此可知,该方法可以制备多孔Co3O4纳米管。从图4-6(d)中还可以看出,没有杂相存在,所制备的多孔Co3O4纳米管的衍射峰强度较高,说明制备的多孔Co3O4纳米管的结晶度较高。

图4-6 多孔Co3O4纳米管不同分辨率的扫描电镜图片、透射电镜图片和XRD图谱