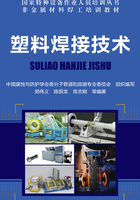
第二节 塑料焊接技术的发展历程
塑料焊接是现代工业重要的塑料加工成型工艺之一。常见的塑料加工成型工艺有挤出、注塑、压延、滚塑等,其特征是批量大、热成型。但是,一些产品往往还要进行机械加工、表面处理、机械连接等二次加工,塑料焊接就是一种重要的二次加工。本节主要介绍塑料焊接技术(包括塑料压力管道焊接)的现状与发展。
一、塑料焊接技术概述
(一)塑料
塑料焊接技术的发展是伴随着塑料的发展而发展的。今天所说的塑料,单指人工合成的塑料(又称合成树脂),是用人工方法合成的高分子物质。最早的塑料是用硝酸处理过的纤维素、由天然的纤维素加工而成的,并不是完全人工合成的塑料。人类历史上第一种完全人工合成的塑料是酚醛树脂,由美国人贝克兰在1909年用苯酚和甲醛制得的,并取得第一个热固性树脂——酚醛树脂的专利权,这带来了塑料突破性的进展。1920年以后塑料工业获得了迅速发展。20世纪40年代乙烯类单体的自由基引发聚合迅速发展,实现工业化的塑料包括氯乙烯、聚苯乙烯和有机玻璃等。在这一时期塑料工业处于飞速发展阶段。1983年起塑料工业超过历史最高水平,产量达72Mt。目前,以塑料为主体的合成材料的世界体积产量早已超过全部金属的产量。钢铁生产已有两千多年的历史,而塑料问世不过百多年,足可见塑料工业发展速度之惊人。
还有一种材料称为塑料合金,它是利用物理共混或化学接枝的方法而获得的高性能、功能化、专用化的一类新材料。它能改善或提高现有塑料的性能并降低成本,广泛用于汽车、电子、精密仪器、办公设备、包装材料、建筑材料等领域,成为塑料工业中最为活跃的品种之一。
塑料按其热行为的不同可分为热塑性塑料和热固性塑料。热固性塑料成型后再加热也不会变软、不熔化,因此这种塑料不能进行焊接,多用于开关、插座等。热塑性塑料成型后再加热仍可软化乃至熔化,具有良好的加工性能和可焊性。由于焊接时要求塑料能熔化和迅速冷却而将两塑料表面连接在一起,因此一般情况下塑料焊接就是指热塑性塑料的焊接。
(二)塑料焊接方法
塑料焊接是利用热作用,使塑料连接处发生熔融,并在一定压力下粘接在一起。塑料焊接可以使用焊条填充材料,也可以直接加热焊件而部使用填充材料。
塑料设备的性能主要取决于其连接接头的性能,大多数工程应用均要求接头与母材具有相同的性能,而焊接方法和焊接技术则对接头性能具有重要的影响。
由于塑料材质、种类及使用条件的不同,焊接时所采用的方法也不同。不同的塑料焊接方法不外乎加热方式的不同。除了大多与塑料的熔融特性及流动特性有关外,可能还遵循着各自特有的机理。
热塑性塑料的焊接方法大体可分为三大类,即热焊接、摩擦焊接、电磁焊接。热焊接包括热气焊、热压焊、挤出焊、加热工具焊和红外辐射焊接等;摩擦焊接可分为旋转焊、振动焊、高频焊和超声波焊接等;电磁焊接有电热丝焊接、感应焊接、电容焊接和脉冲焊等。目前常采用的塑料焊接方法有热风焊、挤出焊、热熔焊和电熔焊等。热风焊方法历史最长,应用广泛,适合于焊接大型设备或构件,如板材对接、角形焊缝,但只能用于手工操作,生产效率较低。挤出焊是20世纪60年代经过一系列的技术改造之后开发的一种加工工艺,它的出现大大缩短了焊接厚壁板材所需要的时间。
(三)塑料焊接方法的发展
塑料焊接最初的工艺是热熔焊接,就是通过加热把两块塑料的结合面熔化,并使其相互粘接的一种方法,也是在塑料大发展时期发展起来的。随后,发明了超声波焊接和高频焊接。它们的基本原理都是把一种能量(超声波动能、高频电场的电能)转变成可以使塑料熔融的热能,进而实现塑料的焊接。
挤出焊是20世纪60年代经过一系列的技术改造之后开发的一种加工工艺,它的出现大大缩短了焊接厚壁板材所需要的时间。
超声波金属焊接是19世纪30年代偶然发现的,塑料超声波焊接也是借鉴金属技术发展而发展的。所需热量是用超声波激发塑料作高频机械振动而产生的。超声焊是目前热塑性材料使用得最广泛的焊接方法之一,其操作简单,不需要填充焊料,生产效率高,焊接周期短,易于实现自动化,适于大批量生产,焊接强度高且一致性好,焊后外观无任何印痕,无需修复。对于一些特异材料,只能采用超声焊。但超声波焊只能焊接小焊面,且设备成本高。对于较大部件,虽可采用多头焊机,但结构复杂且价格昂贵,不太适宜低模量热塑性材料。超声焊适于焊接几乎所有热塑性塑料材料,尤其适于刚性较大的材料,因不受待焊面污染的限制,广泛用于医药制品、食品工业的自动化焊接。
激光技术是从20世纪70年代开始应用在塑料焊接中的。激光作为一种焊接用热源,具有准直性优良、光束能量密度高、作用区域小等优点。在焊接过程中,通过光路系统,将激光器产生的光束聚焦于待焊接区域,形成热作用区;在热作用区中的塑料被熔化;在随后的凝固过程中,已熔化的材料形成接头,待焊接的部件即被连接起来。激光焊接塑料具有低成本、高速度、加工方便、易实现精密数控容易、原材料适用范围广、接合性和工艺性好等综合优势,随着塑料焊接工艺研究和塑料激光焊接设备的逐步商品化,塑料激光焊接的应用必将越来越广泛,技术越来越成熟。同其他塑料焊接方法相比,它具有非接触、不透气、不漏水、焊接速度低、精度高、焊缝强度高、无飞边、无残渣、热应力最小等优点。
最近几年还出现了塑料冷焊接,广泛应用于聚氯乙烯管道的连接,它的工艺机理和技术还在发展完善之中。塑料冷焊接是将塑料管材和管件的承插连接口通过溶剂溶合固化,又粘接固化在一起的工艺。冷焊接与热焊接的区别:普通塑料焊接属于加热焊接,冷焊接不通过加热方式进行。
二、塑料压力管道焊接技术现状与发展
塑料压力管道具有质量轻(密度是钢的1/7)、耐腐蚀性强、流体阻力小、热导率低(约为钢的1/100)、施工方便且寿命长等特点,广泛用于燃气、给水输送等各个领域。在塑料管道系统的制造和使用过程中,管道之间的连接是影响其结构完整性及持久强度的重要因素。由于管道输送的流体中不乏危险介质,如天然气和煤气等,结构一旦破坏后果不堪设想,因此管道的连接技术是影响塑料管道是否广泛应用的关键技术之一。目前公认焊接是一种高质量、高效率的塑料管道连接技术,聚乙烯、聚丙烯和聚丁烯压力管道均采用电熔或热熔技术连接。
(一)电熔焊技术的发展
电熔焊技术是利用电流产生的热效应使塑料熔化,由于聚合物分子的扩散、冷却后连接在一起,达到焊接的目的。当前,随着高密度聚乙烯管道在燃气和给排水等领域应用的不断深入,电熔焊技术也得到了飞速发展和广泛应用,主要体现在以下几个方面:
(1)电熔管件的材质紧随管道材质的发展,电熔管件的结构得到不断改进。国际上已有多家电熔管件制造商开发生产出PE100材料的电熔管件。
(2)电熔焊设备实现了多功能化,可以在现场进行焊接质量的控制,并且确保设备和安装的可追溯性。
(3)电熔管件的自动识别系统实现了标准化,识别系统有数字识别系统、机电识别系统和自调节系统3种类型。目前大多数电熔管件采用的是数字识别系统。
聚乙烯燃气管道的应用发展到20世纪90年代,产生一些明显的变化。如电熔连接多功能控制器的采用,以及管网安装中独立承包商的介入,需要明确界定责任。而这首先要求的是可靠的数据记录。采用电子数据处理的焊接控制器可在现场自动记录所需要的各种数据,提高统计分析的效率,同时也有助于评价产品供应商和安装队伍的表现。如果发生质量事故,详细的数据在质量分析中非常有用。可追溯性延伸了电熔管件数据载体的数据范围,因此要求采用磁卡或24位的条形码来记录施工数据。
(二)热熔对接焊技术的发展
塑料压力管道热熔对接焊技术的应用时间已有40多年。实践证明,该方法可以焊出高质量的焊接接头。热熔对接焊的发展方向也是全自动化。这样不仅可消除人为因素的影响,并且可实现可追溯性。这主要是针对大口径管道,因为传统焊接设备用于直径大于315mm的管道时已出现问题。
近年来,热熔对接焊在改善焊接质量和可用性方面有新的进展,主要是计算机数字控制技术在塑料焊接技术中得到了成功的应用。热熔对接焊的工艺参数较多,动作过程也较复杂,因此焊接质量的好坏受人为因素的影响也较大。但利用计算机控制焊接的工艺参数和工艺过程,可避免由于人为因素的影响。它控制精度高,重复准确性好,操作简便实用,且焊接结果独立于设备的操作者,即影响焊接质量的人为因素几乎为零。由于所有焊接工艺参数的理论值和实际值都被储存在计算机中,随时可以调用,因此焊工在焊接时不必手工操作,而使整个焊接过程都按程序自动进行,从而不但提高了焊接接头的质量,而且减少了工作时间、降低了费用、同时实现了可追溯性。热熔对接焊自动控制系统分为预置参数控制和自动调节参数控制两种。
(三)塑料管道焊接新方法
塑料压力管道的发展方向是大直径、厚管壁,并且输送介质的压力也向高压方向发展,这为热熔对接焊的发展带来了契机,可以充分发挥热熔对接焊的优越性。塑料压力管道焊接技术也一直向自动化、智能化和信息化方向发展,能自动适应环境的变化以及自动调整在新材料上焊接的焊接参数;具有记忆功能,自动记录所采用的焊接参数;采用磁卡作为数据载体;对塑料焊机采用ID卡进行授权管理;按ISO 9000质量体系规范管理等。随着网络技术的发展,将对焊机利用网络进行辅助管理、远程故障诊断及远程参数设置,充分利用网络的快捷、方便,使塑料焊接技术向前发展。
国外也有机构研究了一些新的方法。美国天然气研究所开发了一种用于连接和修理输送天然气的聚乙烯管线的新方法。该方法使用了自调、恒温加热的技术。该技术能较好地控制温度,且装配费用低。该产品于1995年在美国开始商业销售。
热熔对接焊和电熔焊在聚乙烯管道的焊接中得到了广泛应用,但其焊接时间较长。因此,20世纪80年代后期有人提出了利用红外线辐射的方法焊接聚乙烯管道焊。其焊接过程与热熔对接焊基本一致,只是加热工具是用钨丝或镍铬丝制成,利用钨丝或镍铬丝加热时产生的红外线对管道端面辐射加热。这种方法主要优点是减少了焊接时间、加热板不用与管道端面直接接触、可以避免热源污染等。但非接触加热不易消除管道端面的不平度的影响;采用钨丝或镍铬丝作为发热元件也使加热板造价高。研究表明,利用红外辐射焊接可以形成比热熔对接焊更高的焊接强度,而焊接时间可以减少50%。该方法目前仍停留在试验室中使用,没有在工程中推广应用。
(四)我国塑料压力管道焊接技术的发展现状
与发达国家相比,我国在塑料压力管道焊接技术方面仍旧存在一定的差距。就热熔对接焊机而言,全自动焊接设备应用仍不普遍,焊接质量受人为因素影响较大。电熔焊技术只在小管径管道上使用效果比较好;在大直径管道上使用时仍旧存在难以保证焊接质量问题;同时,国内使用的电熔管件大都依赖于进口或中外合资生产,没有自主知识产权的电熔管件。
随着科学技术的发展,塑料管道焊接技术将向自动化、智能化和信息化方向发展。塑料压力管在我国大规模的应用将为我国广泛开展塑料压力管道焊接基础理论、焊接技术规范及质量控制体系的研究提供条件,开发性能优良、价格合理、操作简便的焊接设备将会使管道焊接更加方便、直接,这些具有重大的社会效益和经济效益。