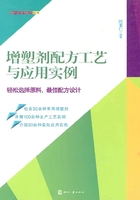
1.2 2-丙基-1-庚醇
一、概述
1950年,美国标准石油和杜邦公司将丙烯通过Mo(CO)6/Al2O3催化剂可以转化为乙烯和2-丁烯。1970年,法国石油研究院的Chauvin教授首次提出了M‖C金属卡宾物种引发,经过“金属四元杂环很好地解释了环烯烃与直链烯烃之间的歧化反应产物分布。
1980年,Schrock合成了第一个结构明确的卡宾配合物歧化反应催化剂。从此,Chauvin机理被科学家熟知并接受。20世纪60年代初,伊斯曼·柯达公司将两分子戊醛先缩合成2-丙基庚烯醛,然后加氢制得2-PH(2-丙基-1-庚醇)。
美国联碳公司于20世纪80年代开发了以双亚磷酸酯为催化剂配体,以混合丁烯为原料制备2-PH的新型工艺。产品的商品名为UNOXOL 10。
陶氏采用混合C4合成2-丙基庚醇的技术为低压羰基合成技术(LP OXOSM Technology),催化剂采用的是新型NORMAXTM型催化剂,该工艺技术由羰基化反应、羟醛缩合、加氢反应及醇精馏4个单元组成。
UCC/戴维开发的LPOxo工艺,是在一独立装置中生产2-丙基庚醇。原料来自裂解装置的抽C4烯烃或甲醇制烯烃(MTO)装置副产的混合C4烯烃。烯烃原料的成本是醇类产品生产中的主要成本之一;在四种增塑剂生产工艺中,2-PH是最廉价的一种,因为生产2-PH原料C4烯烃的价格低于丙烯,也低于丁烯二聚物及壬烯;2-PH工艺装置的投资也低于INA和IDA工艺装置。
以正丁烯为原料,经羰基合成得到正戊醛,加氢可以联产戊醇;正戊醛经缩合脱水得到2-丙基庚烯醛,加氢得2-丙基庚醇。但不同的正丁烯来源因价格的不同,从而决定了2-丙基庚醇生产的可行性。
2-丙基-庚醇的生产工艺流程与2-乙基-1-己醇相同,都采用低碳烯烃经低压羰基合成,得到相应的低碳醛。经醇醛缩合,得到高碳醛,再经加氢和精馏,得到产品醇。不同之处在于原料、催化系统及一些辅助工艺上的差异。
羰基合成法是使烯烃与一氧化碳、氢,经氢甲酰化反应生成醛,再经高压加氢得到直链和支链混合醇。
2-丙基-1-庚醇简称2-丙基庚醇(简称2-PH),英文名称:2-propyl-1-heptano;2-propylheptanol;2-Propyl-1-heptano。CAS:10042-59-8。分子式:C10H22O。分子质量:158.28。无色液体,呈鲜柠檬似香气和青草-草药气味,略有醚香和油香,沸点157~161℃,溶于乙醇和乙醚,微溶于水,沸点160~162℃,折光率1.420,密度0.817g/mL (25℃),闪点59℃。
二、生产技术
1.丙烯
烯烃歧化反应可以使用均相催化体系,也可以使用非均相催化体系,有时还添加第3组分做助催化剂。对于含有机金属的助催化剂体系,可以通过主催化剂与有机金属助催化剂的反应产生歧化反应最初的金属——卡宾引发物种。而对于不含有机金属助催化剂的非均相催化剂,通常认为歧化反应是通过活性金属中心与反应烯烃双键配合开始,其反应机理是:通过金属与一个烯烃分子的作用,使烯烃分子的1,2-氢发生转移而形成金属卡宾。
在烯烃歧化反应中,金属卡宾化合物(M‖CHR)与一个烯烃(RHC‖CHR′)的碳碳双键发生加成反应生成金属杂四元环(金属杂环丁烷)中间体,该四元环中间体不稳定,进行逆反应后生成一个新的烯烃分子(RCH‖CHR)和一个新的金属卡宾(M‖CHR')。新的金属卡宾再与另一个烯烃分子(RHC‖CHR′)发生类似的反应,最后生成另一个烯烃分子(R'HC‖CHR′),并生成原来的金属卡宾化合物。
负载型铼基催化剂主要由载体、活性组分组成,有时还添加其他碱金属、碱土金属等添加剂。载体一般采用具有高比表面的无机氧化物(Al2O3、SiO2等)或其复合氧化物。活性组分是铼的氧化物(Re2O3、ReO2等);催化剂的制备采用浸渍法,将载体浸渍在一定浓度的铼金属盐水溶液中,然后烘干,并在空气流下煅烧。在煅烧过程中,盐类分解,最终得到负载铼金属盐催化剂的前驱体,然后进行预处理得到负载型铼基催化剂。
在Re2O7/Al2O3催化剂上,随着铼担载量的增加,催化剂表面的弱L-酸转变成为强L-酸,随着铼担载量增加和煅烧温度升高,烯烃歧化的活性也会增加。当担载量为2%~8%时,每克催化剂的活性位数量为0.6%~2.2%,而且在盐酸中制备的催化剂比在水溶液中制备的催化剂的活性位数量要多。
在Re2O7/Al2O3催化剂中铼氧化物的担载量较低时(<10% Re2O7),通过添加一定量的V2O5或WO3,催化剂的性能可以显著提高。
在Re2O7/Al2O3催化剂中添加四烷基锡可以显著提高催化剂的活性,原因可能是由于助剂的添加能改变催化剂活性位的形成方式。在烯烃歧化反应中,经过合适的预处理,烷基锗和烷基硅可以取代有毒的烷基锡作为铼基催化剂的助剂。
B酸能明显提高催化剂的歧化活性。在不同负载量Re2O7/Al2O3催化剂的丙烯歧化活性时,催化剂的酸性和歧化活性之间存在一种正向的关联。载体经过酸化或磷化处理提高酸性后, Re2O7/Al2O3催化剂的歧化活性有明显提高。
Re2O7/OMA(有序介孔氧化铝)催化剂具有更高的活性。孔径对歧化反应的活性和选择性有重要的影响,随着孔径的增加,反应初始的转换频率增加;对歧化反应选择性的影响表现为不同的孔径可以抑制烯烃分子的再反应,减少副反应的发生。
目前使用负载型铼基催化剂的工艺主要包括:德国BASF公司烯烃歧化工艺、法国石油研究院以及台湾中油公司开发的Meta-4烯烃歧化工艺。
生产实例一:OCT工艺
OCT工艺是ABB Lummus公司在Phillips石油公司开发的丙烯歧化制乙烯和丁烯技术的基础上开发的丙烯生产工艺。OCT工艺所用催化剂主要包括WO3/SiO2歧化催化剂及MgO异构化催化剂。其中WO3/SiO2催化剂基本组成为:①高比表面积SiO2载体(比表面积大于50m2/g),载体中SiO2质量分数大于90%; ②钨氧化物或其前体;③一定量的碱金属、碱土金属或稀土金属等,它们作为助剂或烯烃异构化催化剂组分。
新鲜及循环的C4和乙烯混合,通过预处理床层脱除原料中的微量杂质,然后经预热进入反应器,在反应器中1-丁烯异构为2-丁烯的同时,2-丁烯与乙烯歧化生成丙烯。反应流出物送入精制回收单元得到高品质纯丙烯(超过聚合级丙烯的纯度),同时未反应的乙烯及C4烯烃循环回反应器继续反应。在反应温度高于260℃、反应压力为3.0~3.5MPa的条件下,丁烯单程转化率为60%~75%,丙烯选择性大于95%,乙烯生成丙烯的总选择性接近100%,丙烯总选择性达到92%~96%。该工艺的催化剂可连续再生而且性能稳定。
生产实例二: BASF公司的C4烯烃歧化制丙烯工艺
BASF公司开发的C4烯烃歧化制丙烯工艺的专利技术一直在不断发展,水平也在不断提高。该工艺的特点是使用尽可能少的乙烯,以C4烯烃做原料高收率生产丙烯。
BASF公司开发的C4烯烃歧化制丙烯工艺所用的原料可以是来源于石油裂解或精炼过程中的C4物流,也可以是纯的C4烯烃,在使用前最好预先净化,以除掉可能存在的微量水分、氧或含氧化合物、硫或含硫化合物,以及氮、磷和卤素化合物。C4物流中至少含有70%以上的丁烯,1-丁烯与2-丁烯的原料配比是2∶1~1∶20。
生产实例三:Meta-4烯烃歧化工艺
Meta-4烯烃歧化工艺是法国石油研究院与台湾中油公司开发的乙烯和丁烯歧化生产丙烯的工艺。反应器可以使用固定床反应器,也可以采用移动床反应器。该工艺是将主要含丁二烯、1-丁烯、异丁烯和炔类化合物的C4烯烃转变为聚异丁烯和丙烯。首先原料要先进行选择性加氢异构化,使丁二烯和1-丁烯转变为2-丁烯,异丁烯要通过甲基叔丁基醚(MTBE)装置或分馏除去,富含2-丁烯的原料才能与乙烯一起送进Meta-4装置。过程包括:①丁二烯、炔类化合物选择性加氢,催化剂含有镍、钯或铂,温度20~200℃、压力1~5MPa、空速0.5~10h-1下同时将l-丁烯异构化为2-丁烯;②抽提或与甲醇反应除去异丁烯,在酸性催化剂存在及一定温度和压力的条件下,剩余的异丁烯聚合为聚异丁烯;③在铼基催化剂存在及温度为30~60℃、压力高于反应蒸气压条件下进行液相反应,2-丁烯和乙烯歧化生成丙烯。该工艺包括反应区和再生区。催化剂全部或部分失活后,送入再生器再生后可循环使用。该工艺对丙烯的选择性大于8%,2-丁烯转化产率90%,产物中乙烯和丙烯含量达到一定量后,催化剂表面的铼处于各种不同的价态,能有效提高催化剂的活性。在甲烷、正丁烷或环丙烷气氛下,γ射线照射处理后Re2O7/Al2O3上丙烯的转换率(TOF)能提高10~100倍。
C4烯烃裂解需开发高选择性的催化剂,以抑制芳烃和低碳烷烃等副产物的生成,使反应向有利于提高丙烯选择性及丙烯收率的方向进行。1-丁烯及混合C4在ZSM-5分子筛催化剂上的裂解规律显示,尽管原料中丁烯的含量有差异,但裂解产物中C2~C5烯烃的质量分数与热力学规律的变化趋势一致。
Lurgi公司的Propylur工艺是一种以不含双烯的烯烃(丁烯、戊烯、己烯)为原料的最大量生产丙烯的固定床工艺。该工艺对原料中C4烯烃的含量没有要求。原料中可含有一些链烷烃、环烷烃、环烯烃和芳烃,这些化合物几乎不影响催化剂的性能。另外,对于烯烃组成不同的原料,最终产物分布基本相似。原料中二烯烃的质量分数应限制在1.5%以下,以防止生成胶质及结焦,影响催化剂寿命。
生产实例四: Propylur工艺的ZSM-5分子筛催化剂
Propylur工艺采用的ZSM-5分子筛催化剂(硅铝摩尔比为10~200)是德国Süd-Chemie公司定制的,在约500℃、0.1~0.2MPa、空速1~3h-1、水蒸气与烃的质量比0.5~3.0的条件下进行反应,轻烯烃的总转化率约为83%,丙烯单程质量收率为40%~45%。若未反应的丁烯循环使用,可使丙烯和乙烯的质量收率分别提高到60%和15%。可将蒸汽裂解装置与带有反应分离段的Propylur工艺联合,将丙烯与乙烯产率进一步提高到0.688,但投资费用相对较高。
Atofina公司和UOP公司联合开发的工艺特点是原料中不加稀释气,因而反应器的体积小,设备投资少。专用的ZSM-5分子筛催化剂,在500~690℃、1~0.5MPa、较高空速的反应条件下,固定床反应器中和催化剂接触发生催化裂解反烯选择性及收率都较高。
OCP工艺的生产方式灵活。当该工艺与裂解装置结合时,可获得较高的丙烯与乙烯产量比。采用该联合装置制备烯烃时,可使乙烯和丙烯的总收率提高到80%~90%以上,丙烯收率由30%~50%提高到60%。
日本旭化成公司成功开发出Omega工艺是使ZSM-5分子筛催化剂,在温度530~600℃,0~0.5MPa、空速3~10h-1及没有稀释气体的反应条件下,原料在可切换的固定床上进行绝热催化裂解反应,获得较高的丙烯选择性,吸收烯烃质量分数87%的抽余C4进料时,丙烯单程收率高达46.6%,丙烯与乙烯产量比接近4。反应器2~3天切换一次,失活催化剂原位再生。
MOI工艺是Mobil公司在甲醇制汽油(MTG)工艺的基础上衍生而来的。该工艺以蒸汽裂解装置副产的C4烯烃为原料,也可采用轻质汽油作为原料。MOI工艺的产物中烯烃的分布不受原料烯烃碳链长短和结构的影响。该工艺的反应条件与FCC装置相似,采用带有催化剂连续再生系统的单一流化床反应器。
MOI工艺的技术关键是ZSM-5分子筛催化剂。ZSM-5分子筛独特的酸性和择形性可使烯烃通过低聚、裂化、歧化反应进行内部转化,且抑制了多环芳烃和焦炭的生成。通过加工250kt/a混合C4烃和裂解汽油,可使乙烯和丙烯产量分别达687kt/a和515kt/a,即产物中丙烯与乙烯的质量比由0.58提高到0.75。
2.戊醛
在德国专利DE-A-10118634,欧洲专利EP-A-74 2195和742 234中描述的是可以经济地利用C4馏分,C4馏分典型成分包括1,3-丁二烯、1-丁烯和2-丁烯。
美国专利2842514描述使用获得“氧代”的过程通过醛类反应得到醇的混合物。其中,所述的烯烃与一氧化碳和氢是在钴催化剂存在下,在升高温度和恒定的压力下合成的。
美国专利4426542描述的方法,是用混合丁烯转化为的C10增塑剂醇。例如,生产2-丙基庚醇,这是一种非常适用的增塑剂醇。
美国专利7345212,7186874,7148388,7081554,7081553, 6982295,6969736,6969735,6013851,5877358在实例中,将衍生来自直链或支链酸的至少一个或更多C4~C13轻质烯烃的羰基化缩合反应的醛后加氢,这种羰基合成法是众所周知的。
直链或支链的醛可以采用固体磷酸沸石催化剂。通过C3~C12烯烃,如丙烯、丁烯或戊烯的加氢甲酰化低聚反应过程来完成。例如,美国专利7253330和7145049的羰基化过程产生的是醛和醇的混合物,这取决于所使用的催化剂和加工条件。特别是,Ru催化剂更有选择性。示例性的金属选自Rh和Co的催化剂,也可以使用有机配位体,以进一步提高催化剂的活性和选择性。用于羰基化过程中的原料可以是丙烯、丁烯、戊烯和它们的混合物,由固体磷酸或沸石实现烯烃的二聚化。
将所得的C4~C13醛通过分馏,除去未反应的烯烃和相应的醇。然后,这些C4~C13醛可以依次被氧化,使用空气或富氧空气作为氧源,即避免了以前的分馏步骤,所述一个或多个C4~C13直链或支链烷基的醛/醇可被氧化成相应的酸和醇,然后将未反应的醛纯化蒸馏。已分离的未反应的醛加醇氧化成其相应的酸。当在羰基化过程中使用Ru催化剂是最佳选择。
生产实例五:丙烯加氢甲酰化催化剂
反应使用的催化剂是铑-二亚磷酸盐配合物(铑的浓度为500mg/L, P/Rh摩尔比为8),用二亚磷酸盐做配位体。通过导管以167620kg/L的量输入。
将丙烯通过管道连续地输入反应器内和催化剂液循环,与逆流含有0.4%(质量分数)的水的氧代气体(H2/CO=1.0)以7620kg/h的量接触,反应器1的反应器温度为90℃,总压力为10kg/cm2。将丙烯和含氧气体的进给量进行了调整,使得该反应器的压力保持在10kg/cm2,其结果,丙烯的进入量为1200kg/h,含氧气体的进入量为900kg/h,未反应的烯烃、未反应的气体、醛产物和水的部分被作为混合的蒸汽流从反应器气相中取出,由冷凝器冷却至40℃,所得到的冷凝液以1730kg/h的速率通过导管,催化剂可予以回收。所得到的冷凝水进行净化,并将残余物以5000kg/h的速度通过导管循环进入反应器。引入逆流塔2的反应产物液通过管道和含氧气体紧密接触将未反应的丙烯气体汽提,然后导入到气-液分离器,并降低压力。气-液分离后,将反应混合物引入到催化剂分离柱,醛产物从塔顶部蒸出,从塔底部的催化剂液体通过水洗涤回收催化剂,然后通过导管再循环到反应器的出口处,此时,反应器中水的浓度为1.0%(质量分数)。
生产实例六:用混合丁烯为原料
将石脑油经乙烯工程裂解工艺,得到混合裂解气,经分馏,得到C4馏分。
粗馏C4的石脑油裂解装置在选择性氢化后,余下的组分有异丁烯(30.8%),1-丁烯(30.8%),2-丁烯(30.8%),1,3-丁二烯(80ppm),其余的是丁烷。在第一阶段,用于选择性羰基化的1-丁烯的转化率为90%,2-丁烯和丁烷分别为3%。
MTO工艺副产的混合C4除含大量的C4烃外,还含少量的C3、C5、C6烃,C4烃在混合C4中占的比例在80%以上。
C4馏分经丁二烯抽提工艺,分离出丁二烯;得到抽余液1(简称R-1),直接进行选择性加氢,得到R-1,得到的抽余液-1与甲醇反应,抽余液-1中的异丁烯转化为甲基叔丁基醚(MTBE),用作汽油添加剂,同时得到抽余液-2,简称R-2。R-2含1-丁烯、顺2-丁烯、反2-丁烯、丁烷及少量的异丁烯,含量70%以上。抽余液-2即可作为生产2-丙基庚醇的原料。采用Rh复合催化R-2,经过氢甲酰化反应,在100℃下与合成气(H2/CO)反应2h,得到以正戊醛为主的混合戊醛。
生产实例七:烃组分原料
烃组分原料含有50%~70%(质量分数)的丁烯和0~10%(质量分数)的丙烯与1~25ppm的2,4,6-吡啶,原料中水的浓度是575~625ppm,进料温度为30~50℃。催化剂ZSM-23的制备在美国专利5026933中已做了说明。低聚温度200~225℃,压力1100psig(7584kPa)~1400psig(9653kPa),空速约1.75~2.25h-1。低聚过程的产物组分为40%~50%(质量分数)的C8烯烃, 30%~40%(质量分数)的C12烯烃,5%~15%(质量分数)的C16烯烃。
生产实例八:ZSM-22催化剂
丁烯低聚商业ZSM-22催化剂是负载在氧化铝上的ZSM-22,在空速6.8h-1下将60%~65%丁烯、35%~40%的丁烷原料在40℃下水合。反应器流出物用气相色谱(GC)分析,对进料和产物的烯烃/链烷烃的比率进行比较,以确定转换率。
生产实例九:丁烯加氢甲酰化
丁烯的加氢甲酰化用的是钴催化剂,反应在300mL的带搅拌器的高压釜内进行,用0.3%(质量分数)的羰基钴作为催化剂,溶剂为100mL甲苯,利用5mol的丁烯,主要是1-丁烯与2-丁烯,在CO∶H2为1∶1的合成气作用下,将反应器的压力调节至表压为2400psi,加热至100℃。反应5.2h后,没反应的烯烃含量为6%,产物中正戊醛和2-甲基丁醛比例为2.0∶1,反应混合物中的戊醛为66.8%,反应速率为2.1gmol/(L·h)。
3.2-丙基-庚醇
在优选的实施方案中,所述至少一个C5~C10,优选C6~C9,酸轻质烯烃的加氢甲酰化的C5~C8烯烃产物称为“含氧酸”。通常情况下,轻质烯烃的加氢甲酰化生产醛可被氢化成醇。
本工艺的实例说明,丙烯用作原料的低聚反应可以是连续、间歇或半间歇。蒸馏的作用是除去未反应C3烯烃和回收产物。回收作为底部产物与侧流并发送到羰基化反应所需的二聚体己烯三聚体和四聚体。羰基化反应通过可选的原料进行调整,如使用线性烯烃、1-己烯或1-辛烯、一氧化碳和氢气,合成气可方便地提供到反应器中,然后通过分馏分离,选择性地回收低碳烯烃。在实例中,C7醛与空气氧化,和未反应的醛和重质组分被分离出来。
在前面的步骤中,醛可通过加氢甲酰化的C4~C9高级烯烃,采用沸石催化剂催化丙烯或丁烯,通过低聚或二聚产生丁烯-1、戊烯-1、己烯-1、庚烯-1、辛烯-1、壬烯-1后可直接羰基化。
所得C5~C10,优选C6~C9醛可以氢化成相应的醇,再从粗羰基化产物中分馏除去未反应的烯烃和相应的醇及其他副产品。
生产实例十:低压羰基化技术
以混合C4为原料,1-丁烯、2-丁烯充分转化为2-PH的技术商有BASF和陶氏。
陶氏的低压羰基合成技术转化率在80%以上,是比较经济的。该技术要求混合C4原料中的正丁烯含量在70%~80%(转化率最高), MTO工艺副产的混合C4中正丁烯的含量可以满足该工艺技术的要求。
以1-丁烯为原料,在甲苯、铑催化剂和三苯基膦存在下于95℃进行氢甲酰化反应1.0h得正戊醛,然后在NaOH存在下于90℃缩合30min。再在镍催化剂存在下,120℃条件加氢3h得到2-PH。
利用低压羰基化技术将混合C4烯烃中的丁烯-1和丁烯-2转化成戊醛,进而转化成2-丙基庚醇,可使混合C4烯烃的利用价值实现最大化。对于已有生产辛醇(2-EH)的低压羰基化装置,也可经过改造以混合C4烯烃作为原料生产2-丙基庚醇(2-PH)。
生产实例十一:缩合加氢
UCC/KPT的戊醛经缩合和加氢转化为2-PH的工艺称为Unoxol10工艺,其中戊醛与氢氧化钠水溶液在适中的温度和压力下进行液相缩合反应,得到的不饱和C10醛包括2-丙基-2-丁基丙烯醛(PBA)和其他异构体。第一步气相加氢是在传统的固定床反应器中进行,第二步为液相加氢。两步加氢后得到的C10醇混合物,2-丙基庚醇含量大约85%~90%。实际上,脱除轻组分和重组分后,产品C10醇质量含量最低在99.5%,而其中2-丙基庚醇含量至少为87%。
生产实例十二:二步氢化工艺
第一步气相加氢在传统的固定床反应器中进行,第二步为液相加氢。两步加氢后得到醇混合物,2-丙基庚醇含量大约85%~90%。实际上,脱除轻组分和重组分后,产品C10醇质量含量最低在99.5%,而其中2-丙基庚醇的含量至少为87%。
加氢:在液相加氢技术中,可在单一的加氢反应器中生产正丁醇、异丁醇、2-EH和2-PH。辛醇和2-丙基庚醇可在同一低压羰基化装置上实现联产。根据原料和市场的需求,可在同一装置上生产辛醇和2-丙基庚醇,既可以两种产品进行切换生产,也可同时生产;辛醇和2-丙基庚醇的产量可在0~100%之间进行调节;采用LPOxo工艺和NORMAX催化剂的专利技术,可应用于改造现有辛醇装置来生产高质量2-丙基庚醇。
工艺采用的催化剂为钴、铱或铑与三苯基膦。2-丙基-庚醇的生产工艺流程与2-乙基-1-己醇相同,都采用低碳烯烃经低压羰基合成,得到相应的低碳醛,经醇醛缩合,得到高碳醛,再经加氢和精馏,得到产品醇。不同之处在于原料、催化系统及一些辅助工艺上的差异。
生产实例十三:铑催化剂
UCC/KFF以第四代铑催化剂为基础的合成工艺,同样包括丁烯的氢甲酰化和戊醛的缩合。其中戊醛合成的特点是产物直链度高(94%),丁烯中不仅1-丁烯可参与反应,2-丁烯同样可参与反应,从而提高了产物收率。原料进行净化,以脱除影响羰基合成催化剂的有害物质,如聚异丁烯、痕迹量的卤化物。羰基合成在液相以亚磷酸盐改性的铑催化剂体系中进行,适中的反应温度为100℃,反应压力为1.02~1.36MPa。
反应生成的醛类混合物通过蒸发系统从反应产物中闪蒸出来,并经冷凝和汽提。在戊醛缩合反应之前,正戊醛和异戊醛不必分离。蒸发系统残留催化剂可返回羰基合成反应器循环使用。产物中含94%正戊醛、5% 2-甲基丁醛和1% 3-甲基丁醛。
其中戊醛与氢氧化钠水溶液在适中的温度和压力下进行液相缩合反应。得到的不饱和醛包括2-丙基、3-丁基丙烯醛(PBA)和其他异构体。
过程以裂解副产C4馏分抽提丁二烯和异丁烯后的抽余液-Ⅱ与合成气为原料,首先在保护床中对原料进行净化,以脱除影响羰基合成催化剂的有害物质,如聚异丁烯、痕迹量的卤化物。羰基合成在液相以亚磷酸盐改性的铑催化剂体系中进行,适中的反应温度为100℃,反应压力为1.02~1.36MPa。
反应器出口的醛类混合物通过蒸发系统从反应产物中闪蒸出来,并经冷凝和汽提。在戊醛缩合反应之前,正戊醛和异戊醛不必分离。蒸发系统残留催化剂可返回羰基合成反应器循环使用。产物中含94%正戊醛、5%2-甲基丁醛和1%3-甲基丁醛。
生产实例十四:醛醇反应
在装有搅拌器、加料漏斗、回流冷凝器和氮气流中的1L圆底烧瓶中进行,将100mL氢氧化钾溶液加入到烧瓶中,加热到85℃。将正戊醛和2-甲基丁醛以3∶1的比例混合后进行蒸馏纯化,在搅拌下逐渐加入到反应烧瓶中。搅拌超过1h,加入300mL含有正戊醛187.7g和60.8g2-甲基丁醛的混合物,用分液漏斗进行分离;分出下层水相87g,分离出有机层用水洗涤4次,达213.5g。起始醛的气相色谱分析表明初始大约比例为3∶1的2-甲基丁醛与正戊醛,在反应过程中正戊醛被大量消耗,该产物含有70.5%的烯醛缩合产物和25.3%的起始醛。产物丙基庚醛与2-丙基-4-甲基己烯醛的比约9∶1。
将110.89g的产品进行加氢,采用11g的Co硅藻土催化剂与4.4mL的H2O为促进剂在300mL带搅拌器的高压釜内,将高压釜用氢气加压至1000psi,逐步氢化并在40℃下加热约1h至压力降至480psi,将高压釜再次加压至1000psi,2h后进一步加氢,在压力为1510psi、温度为160℃下连继氢化共16h。
将所得产物用硅藻土过滤以除去催化剂,用正己烷洗涤之后在真空下除去n-己烷,将所得88g产品在10mmHg下进行蒸馏,收集30~100℃产品。气相色谱分析表明,2-甲基丁醇66.4%,戊醇27.5%,2-丙基庚醇4.1%。
额外的38.99g产品,收集103.5~105℃的馏分,为11.3%的2-丙基-4-甲基己醇和87.7%的2-丙基庚醇,上述过程生成的产物为2-丙基庚醇,只有很微量的醛醇缩合醇产物支链醛。由此产生的2-丙基庚醇很容易通过蒸馏分离。
生产实例十五:醛醇缩合反应
将246.3g的正戊醛和82.1g的2-甲基丁醛混合用于醛醇缩合反应,将100mL氢氧化钾溶液加入到烧瓶中,加热到85℃。如生产实例十四中所述醛加成反应20min后,将混合物在89~89.5℃下回流1h,气相色谱分析表明50%的醛发生了反应,在反应混合物中含有20.7% 2-甲基丁醛,28.6%的戊醛,4.8%的2-丙基-4-甲基己醛和37.9%的2-丙基-2-庚醛。因此,反应结果表明n-戊醛(valealdehyde)与本身的反应速度比与2-甲基丁醛、2-丙基庚醛更快。将粗品除去下层的水相和上部的有机相,在20mmHg真空下蒸馏挥发性物质,包括水、正戊醛、2-甲基丁醛、戊醇。共收集78g产品。
生产实例十六:钴化合物催化剂
将2L的直径为1.2mm,长度为2~10mm的圆柱形挤压物的氢化催化剂H14154 1400g,放置在一个吸附塔管内(直径50mm)的102cm吸附剂区内。羰基化异壬醛混合物使用的催化剂为钴化合物,含量75ppm(质量份),泵送空速61m/h,在温度70℃和3.1MPa压力下通过吸附剂从顶端向下流动。283m3的羰基化混合物流经吸附剂,总共含有17.025g的钴化合物,在实验过程中与羰基化混合物导入吸附塔,15.322g被吸附,保留率为90%。实验结果表明钴化合物可以用作加氢催化剂,转化率高达97.5%,适合工业化生产。
生产实例十七:氢化方法1
将980.0g 2.5%的NaOH溶液在氮气氛下加热到60℃与272.8g的正-戊醛,181.8g 2-甲基丁醛混合,用20min的时间加入45.5g的正丁醛混合物,然后将混合物加热到88~90℃。在回流温度下加热1h后,将物料冷却至30℃分开有机相和水相。
醛醇缩合产物的氢化是在镍催化剂存在下,在压力为10MPa和温度为140℃的条件下反应,反应完成后过滤出催化剂,得到粗醇混合物,用气相色谱法测得下列组分(质量分数)。
第一馏分为0.2% 2-甲基丁醇,30.2%正戊醇,0.3% 2-乙基己醇,1.6% 2-乙基-4-甲基己醇,2.1% 2-丙基己醇,6.4% 2-乙基庚醇,6.2% 2-丙基-4-甲基己醇,14.7% 2-丙基庚醇,38.3%终馏分。
蒸馏除去戊醇和2-乙基-己醇得醇混合物,包含下列组分(质量分数):
2-乙基-4-甲基己醇3.2%,2-丙基己醇9.9%,2-乙基庚醇9.6%,2-丙基-4-甲基己醇22.6%,2-丙基庚醇54.7%。
生产实例十八:氢化方法2
将980.0g 2.5%的NaOH在氮气氛下加热到60℃与214.3g的正-戊醛,143.0g 2-甲基丁醛和用超过20min的时间加入142.8g的正丁醛混合,然后将混合物加热到89~92℃。在回流温度下加热1h后,将物料冷却至30℃分开有机相和水相。
醛醇缩合产物的氢化是在镍催化剂存在下,在压力为10MPa和温度为140℃的条件下反应,反应完成后过滤出催化剂后,得到粗醇混合物,用气相色谱法测出有下列组分(质量分数)。
第一馏分:0.2% 2-甲基丁醇,20.9%正戊醇,0.2% 2-乙基己醇,10.9% 2-乙基-4-甲基己醇,5.2% 2-丙基己醇,13.9% 2-乙基庚醇,13.5% 2-丙基-4-甲基己醇,10% 2-丙基庚醇, 22.3%终馏分。
蒸馏除去戊醇和2-乙基己醇得醇混合物,包含下列组分(质量分数)。
8.0% 2-乙基-4-甲基己醇,21.4% 2-丙基己醇,20.8% 2-乙基庚醇,15.4% 2-丙基-4-甲基己醇,34.4% 2-丙基庚醇。
三、应用技术
增塑剂在塑料及薄膜中的应用
应用实例一:邻苯二甲酸酐二异癸酯
含PHO(正戊醛)98.3%(质量分数)、MPHO(甲基-丁醛) 1.6%(质量分数)、MEHO(二甲基-2-乙基-1-己醇)0.0021%(质量分数),混合醇的制造方法如下。
氢甲酰化反应:前体溶液中二羰基乙酰丙酮铑含铑250ppm (前体溶液中约2%),2,2,4-三甲基-1,3-戊二醇单异丁酸酯溶液含催化剂前体溶液20mL,将氮气置换装置插入到玻璃反应器中进行氢甲酰化反应。
控制反应压为11kg/cm2、氢、一氧化碳和1-丁烯的分压为4.4kg/cm2、0.21kg/cm2及2.1kg/cm2,剩下氮和醛,原料气(一氧化碳、氢、丁烯-1、N2)由流量计单独调整流动速率,反应温度为71℃。用毛细管气相色谱对生成C5醛结果进行分析,正戊醛(以下简称nVLA)和2-甲基-丁基醛(以下简称2MBA)产物的比例是35.2∶1。
醛醇缩合是在一个配有磁性搅拌器、缩合冷凝器、滴加装置和热电耦温度计的3L不锈钢高压釜中进行。将得到的C 5醛-醇缩合液351.2g(nVLA97.2%、2MBA2.8%)在搅拌下滴入装置内,于敞口瓶中用59min时间在25℃下滴入1.25% NaOH水溶液355.5g,滴完后反应的内温达到60℃,之后开始加热,温度达85℃,在此温度下继续搅拌反应4h后停止将物料冷却至室温进行油水分离得292.1g油(水分0.57%)。
氢化反应按醛醇缩合反应制备中相同的方式进行,在一个配有磁性搅拌器、缩合冷凝器、滴加装置和热电耦温度计的3L不锈钢高压釜内缩合液油1602.5g与80.4g的阮内镍催化剂,系统用氢气置换三次后,将氢气压力调节到50kg/cm2,将该混合物在500rpm下搅拌。约95℃反应开始,氢化吸收3.5h,继续氢化最高温度达到165℃。停止搅拌并吸收氢气,将物料放置一夜,用膜过滤器滤去催化剂得1617.3g油,使用一个25级蒸馏装置在30℃减压下蒸馏,控制蒸馏初期压力30~60mmHg,之后将压力调节为10~30mmHg,收集塔顶温度为105℃/15mmHg~106℃/17mmHg的馏分。用毛细管气相色谱法对结果进行分析,醇混合物中含有98.3%的2PHO,0.002%的混合醇。
酯化在SUS300L的反应器中进行,向反应器加入邻苯二甲酸酐62kg与上述的混合醇163kg,在氮气氛下搅拌物料,加热控制反应溶液的温度为60℃时加入催化剂钛酸四异丙氧酯,同时搅拌溶液,进一步将混合物加热至220℃。使用油水分离器连接到反应器中,未反应的醇与生成的水返回到系统中。反应液温度达到220℃,每隔1h进行取样检测,约5h后待酸值小于0.3时停止加热,采用通常的中和、水洗等后处理操作,得所需产物174.7kg邻苯二甲酸酯的混合物(以下简称为DXP-1),此时酸值为0.021,在减压下蒸去溶剂。残醇量为100ppm以下,水0.07% (质量分数)。
本工艺增塑剂的配方如下。

在175℃辊测试机内滚动混炼5min制成厚度为1.3mm的片材在185℃预热2min,于压力150kg/cm2加压下制成厚1mm的片材,进行拉伸试验,测定重量变化,进行耐油性、耐水性测试,并测定温度、硬度和体积电阻率。
应用实例二:邻苯二甲酸酐酯化
邻苯二甲酸酐的酯化是在硫酸催化剂存在下,环己烷作为脱水剂共沸除去反应生成的水后进行中和、脱醇及干燥得邻苯二甲酸酯的混合物,在20℃下密度为0.967g/mL,黏度138mPa·s。
典型的钛酸酯催化剂包括钛酸四甲酯、钛酸四乙酯、钛酸四异丙基酯、钛酸四丁酯、钛酸四辛酯、钛酸十四烷基酯、钛酸十八烷基酯和钛酸四苯酯等。
本法提供了一种可稳定储存的增塑剂组分,包括邻苯二甲酸C6~C13酯。催化酯化用量为钛小于1ppm,抗氧化剂0.1%~2.0% (质量分数)。含量的测定通常采用ICP-AES法(电感耦合等离子体原子发射光谱法)。抗氧化剂含量的测定用高效液相色谱法。
生产过程是向酯化反应器内加入计量好的精苯酐、2-PH、钛酸四异丙酯及其他轻组分,在氮气的保护下进行反应,控制一定的反应温度(210~220℃),从分水器中收集反应生成的水,2-PH经冷却和分层后回流到反应器中继续反应,当分水器中收集的水达到一定量时,反应接近于终点,测定酸值合格后冷却至100℃,中和水洗后在170℃和真空20kPa条件下进行减压脱醇。在测定醇含量和水分含量合格后,加入一定量的高品级活性炭吸附脱色,减压过滤。
工艺条件为:催化剂用量为投料总量的0.1%,控制酯化反应温度为220℃,2-丙基庚醇与苯酐的摩尔比为2.5∶1,反应时间为4h。在此优化工艺条件下,苯酐转化率达到99%以上。