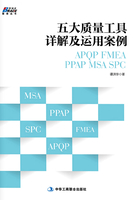
第三节 设计制样阶段
1.输入资料
1.1 设计目标;
1.2 可靠性和质量目标;
1.3 初始材料清单;
1.4 初始过程流程图;
1.5 初始产品和过程特殊特性清单;
1.6 产品保证计划;
1.7 管理者支持。
以上7项资料都是第二阶段的输入,第二阶段工作的基础就是依据第一阶段的输出。同时第二阶段有些工作可与第一阶段同步进行,这样可以减少时间浪费,确保准时交样。
2.输出资料
2.1 DFMEA
DFMEA是设计FMEA,根据产品特点一般需要制作系统DFMEA、子系统DFMEA、部件DFMEA。如果产品简单,直接制作系统DFMEA就可以了。做DFMEA之前,首先要做一个方块图,以便了解零件与零件之间的关系。DFMEA是研发部门组织多功能小组共同制订的。

图1-3 失效模式和后果分析方块图
表1-16 潜在失效模式及后果分析

2.2 可靠性和装配特性
第二阶段输出的可靠性一般指可靠性测试结果,如老化、寿命、耐恶劣气候等测试或试验结果报告。
表1-17 可靠性检测报告

可装配性就是对零件与零件之间尺寸设计的合理性进行试装测试,特别注意公差上下限可能导致的组装困难或间隙大的情况。
表1-18 内部/顾客装配可行性报告

2.3 设计验证
第二阶段的设计验证主要是对功能性能、可靠性、环保、安全进行的测试或试验。设计验证在做样品的时候就可验证,一般由测试工程师或研发人员进行测试。
表1-19 设计验证报告

2.4 设计评审
第二阶段的设计评审指验证之后的评审,评审内容主要有:设计输出是否满足输入的要求、存在的问题及解决的方案。评审是APQP小组成员的集体会议,都要参加。另外注意设计评审过程中必不可少的环节,如评审前一定要明确评审的内容、参与人员,评审后一定要有决议和结论。
表1-20 新产品开发评审表

表1-21 控制计划表


2.5 样件制造——控制计划
样品控制计划一般不做,如果客户有特殊要求就要做。样品控制计划的输入是一阶段的产品保证计划、客户要求和法律法规要求和DFMEA。在样品控制计划中,要明确样品制作流程、责任人、验证项目等内容。样品控制计划与设计验证报告和设计验证计划要保持一致,如文件有策划,一定要实验或测试。
2.6 工程图
工程图主要指结构图、线路图、组装图、电性图等,图纸必须要有公差、版次、制作、审批人员、修改履历等信息。
2.7 工程规范
工程规范主要指产品规格书和制造规格书。产品规格书要明确产品的功能、性能、可靠性等。制造规格书指每个工序的质量加工要求。
××部品规格书
适用范围:适合于816系列光电耦合器。
一、外型尺寸图
1.LTV-816光耦尺寸图

图1-4 LTV-816光耦尺寸图
2.LTV-816S光耦尺寸图

图1-5 LTV-816S光耦尺寸图
二、光耦实物图

图1-6 光耦实物图
三、测试电路图

图1-7 测试电路图
四、输出波形图

图1-8 输出波形图
五、光电特性
表1-22 光电特性

CTR=IC/IFX100%
六、传输特性
表1-23 传输特性

七、光耦检测项目
1.包装标识
2.外观
3.尺寸
4.可焊性
5.电性能
表1-24 新产品开发任务书

6.万用表检测光电耦合器
7.半导体特性图示仪检测

图1-9 半导体特性图示仪
8.耐压测试
9.盐雾试验:检测光耦管脚是否生锈
案例:制造规格书
表1-25 制造规格书


八、材料规范
范围
引用标准:
材料的选择:
表1-26 材料性能要求

表1-27 本体、盖、法兰、套管和油管悬挂器本体材料的成分要求(%)

2.8 图样和规范更改
指APQP中的变更履历表,在每个阶段的评审,验证中如有变更,都要填写变更履历表,在试产前可不要变更通知书。量产中的变更必须要有变更通知书。参见表1-28。
表1-28 产品变更履历表

2.9 新设备、工装和设施要求
填写这个项目的设备清单和工装清单,明确设备的编号、名称、等级等。具体包括与这个项目相关的设备、工装、设施,不相关的就不要填写进来。参见表1-29。
表1-29 设备一览表

2.10 产品/过程特殊特性
这里包括产品特殊特性和过程特殊特性,要有指定符号标示。如没有指定符号,公司在APQP程序中就要明确符号。特殊特性可能是客户指定,也可能是本公司APQP成员评审出来的。特殊特性不仅包括产品特殊特性,也包括过程特殊特性。产品的特殊特性一般在原材料、半成品、成品上表现出来,如尺寸等。过程的特殊特性则一般由设备工装表现出来,如温度、压力、时间、转速等。如表1-30所示:
表1-30 特殊特性清单

2.11 量具和有关试验设备要求
要列出量具和实验设备的编号、名称、型号、量程。参见表1-31测量和实验设备清单。
表1-31 测量和实验设备清单

2.12 小组可行性承诺和管理者支持
二阶段结束前,APQP小组要开会进行评审,总结这一阶段的工作,以便排除问题、制订改善方案,以及确定下阶段的工作是否可以正常进行(注意:最高管理层必须参加会议)参见表1-32第二阶段小结。
表1-32 第二阶段小结(项目阶段评审报告)


3.某汽车配件公司二阶段案例讲解
某汽车配件厂没有产品研发,所以没有方块图,DFMEA。但二阶段的样品验证动作还是有做,有一些性能由客户自己验证。这家企业二阶段的流程大体如下:首先排查是否需要采购设备、工装模具、材料、测量设备,列出设备清单、模具清单、测量实验设备清单,如果需要申购,则立即提出申请。其次,待材料采购回来之后,再由采购部交工程部制作样品,然后将制作的模具进行试模验收,由工程部下发样品制作通知单给生产部和品管部。最后,在生产样品制作完成之后,先经由品管部检验,交样给工程部进行确认,然后工程部再交业务部送样,并提供相关资料。
主要表格如下:
表1-29 设备一览表
表1-31 测量和实验设备清单
表1-33 供应商提交要求
表1-34 送样通知书
表1-35 样品制作通知单
表1-36 模/治具验收报告
表1-37 成型参数表
表1-38 样品规格确认单
表1-39 信赖性测试报告
表1-33 供应商提交要求

表1-34 送样通知单

表1-35 样品制作通知单

表1-36 模/治具验收报告


表1-37 成型参数表


表1-38 样品规格确认单


表1-39 信赖性测试报告


4.二阶段易犯的典型错误
错误1:公司没有根据客户要求和法律法规要求进行测试或试验,也提供不出第三方测试报告,比如REACH检测。
错误2:样品测试或评审中产生的一些变更,没有登记在变更履历表中。
错误3:工程图上某些较重要的尺寸没有进行测试或其他手段的验证。
错误4:生产工艺条件与量产工艺不一致,但并没有对变更的原因进行任何具体说明。