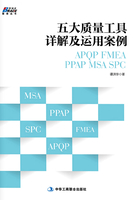
第五节 试产验证阶段
1.输入资料
1.1 包装标准
1.2 产品/过程质量体系评审
1.3 试产过程流程图
1.4 场地平面布置图
1.5 特性矩阵图
1.6 PFMEA
1.7 试生产控制计划
1.8 过程指导书
1.9 MSA计划
1.10 初始过程能力计划
1.11 包装作业规范
1.12 管理者支持
2.输出资料
2.1 试生产
试生产前,由研发工程部给各部门发出试产通知,各部门着手准备材料、设备、工装、工程资料,并召开试产前会议,由工程人员讲解新项目注意事项、工艺要求。试产结束后,由研发工程部进行试产总结,各部门报告问题,并针对异常,在会上制订具体改善方案,最后做出评审,决定试产是否通过。
试产的数量要满足客户的要求,如果客户没有要求,则各工序同步生产至少3小时或300PCS以上。
表1-56 试产申请单


表1-57 电镀试产报告


表1-58 量具重复性和再现性数据表GRR

2.2 MSA评价
MSA评价指利用试产的样品,对测量系统进行分析评价,输入是MSA计划。GRR判定标准是GRR百分比≤10%,NDC≥5。同时,X图50%以上的点落在控制线外,R图全在控制线内的GRR百分比分析才算合格,否则就要对测量系统进行改善。
表1-59 量具重复性和再现性分析表

以上测量系统如果单从数据分析方面来看就是合格的,但如果从图来看就不合格了,因为R图有三个点超过控制线。所以,这个测量系统仍需要进一步改善。
2.3 初始能力研究
初始能力研究是在MSA分析合格后进行,主要是针对特殊特性做PPK,具体测量样品至少30PCS以上,PPK要求≥1.67,才可通过试产。
表1-60 PPK数据分析(30PCS)

2.4 生产件批准
生产件批准是指试产通过后提交资料和试产样品给客户的环节,通常包括19份资料。试产评审通过后,APQP小组就要准备PPAP的提交,一般客户都是按等级3提交,也就是说,不但要提交资料,而且供应商现场也要发行并运用资料。如果客户有自己的提交标准就按照客户标准提交。PPAP需要得到客户的承认,待客户承认通过后方可量产和交货。客户一般会在PSW上签名才算通过。
表1-61 零件提交保证书



2.5 生产确认试验
根据试产控制计划,对产品的功能、性能、可靠性、尺寸进行测试。原则上,要进行全尺寸、全功能、全性能检测,但现在很多企业考虑到进度与成本,一般只针对重要的性能和尺寸进行测试。参见表1-62信赖性测试报告。
表1-62 信赖性检测报告


2.6 包装评价
包装评价一般指包装运输试验,试摔要按照客户要求进行,试摔高度、试摔角和试摔面都必须明确要求,下面是一位客户的试摔标准,表1-63为人次试样表。
客户试摔标准
1.所有产品(除需两人以上技工抬的产品)
(1)试摔测试
八次试摔,从无地毯的硬地面及规定高度摔纸箱的角、边及面:
表1-63 人次试摔要求


图1-12 试摔面1 图1-13 试摔面2
角1的定义为纸箱最易受损的部位
摔的顺序:
2.需两人以上技工抬的产品
摔的顺序:

图1-14 试摔面3

图1-15 试摔面与地面角度
(5)打开包装检查是否破损,是否影响使用和安全。
试摔结束后,要出试摔报告,下面是一家企业包装评价表。
表1-64 包装评价表


2.7 生产控制计划
PPAP提交的是量产控制计划,而不是试产控制计划,量产控制计划一般要把产品审核加进去。控制计划一定要与SPC、PFMEA保持一致,做到有失效的地方就有控制手段,特殊特性则要考虑用控制图。同时要明确,控制计划是多功能小组做出来的,不是品质部门或工程部门做的。参见表1-65注塑控制计划。
2.8 质量策划认定和管理者支持
APQP小组对项目的总认可,试产能否通过,参见表1-66,进行产品质量策划总结和认证,这个表就是评估是否可转量。这一阶段做完,还要进行阶段性评审,参见1-67第四阶段总结。
表1-65 注塑控制计划


表1-66 产品质量策划总结和认定

表1-67 第四阶段小结(项目阶段评审报告)

3.某汽车配件公司APQP第四阶段成功案例讲解
这家汽车配件公司专业做橡胶零件,最终用在凯迪拉克汽车门下面一个橡胶件,客户对品质要求严格。APQP第四个阶段主要目的还是验证工艺的可行性,产品性能的稳定性,包装物流的可行性。试产必须全部要用量产的人、机、料、法、环,工程部全程跟进,必要时进行工程变更。主要流程如下:

图1-16 APQQ第四阶段流程
主要表格如下:
表1-68 广州××橡塑科技有限公司

表1-69 全分析报告

表1-70 开炼日志

表1-71 密炼日志

表1-72 首检报告

表1-73 巡检日报表

表1-74 配料表

表1-75 制品流程卡

量具GRR报告-投影仪-1
表1-76 量具重复性和再现性数据表

量具GRR报告-投影仪-2
表1-77 量具重复性和再现性分析表

表1-78 尺寸检查报告


图1-17 过程能力分析均值极差(X-R)控制图
4.四阶段易犯的典型错误
4.1 试产没有认可直接转量产,如没有对PPM、PPK、成本等进行评估。
4.2 过程没有研究直接算CPK,实际试产过程不稳定,只能用PPK,而且在此阶段找不到控制线。
4.3 试产过程没有按客户要求进行包装试摔试验,试摔高度、试摔角度以及试摔面都不符合客户要求。
4.4 试产中没有进行过程审核,严格来讲是不符合要求的。过程审核的内容包括(产品开发、过程开发、供应商管理、物流等)。如果客户没有特殊要求,可只审核制造过程。
包装评价表
广州××橡塑科技有限公司
表1-79 包装评价表

表1-80 终检报告

表1-81 管理工程表






表1-82 项目阶段评审报告
