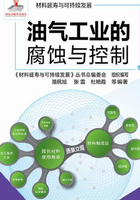
2.2 油气管材腐蚀的复杂性和不同层次
油气管材的腐蚀问题由于其接触介质的多样性,腐蚀形式复杂,往往给工程技术人员带来诸多疑问,因此,有必要从多层次认识油气管道和设施的腐蚀风险。
2.2.1 从腐蚀发生的部位认识油气管材的腐蚀失效
根据管道发生腐蚀的部位直观分辨腐蚀问题,可以分为管道内腐蚀和外腐蚀。内腐蚀主要是管体内部由于输送的油气水多相流动介质所导致的腐蚀。外腐蚀主要是管体外部遭受的土壤、地下水和微生物引起的腐蚀,包括由于土壤宏观电池引起的腐蚀和由于交直流电干扰引起的杂散电流腐蚀等[11~14]。
除此之外,还可以根据管道环向上发生腐蚀的部位进一步区分。例如,对于水平输送管线,往往在管道底部发生腐蚀,对于未脱水的海底湿天然气,则可能在管道顶部发生腐蚀[15]。管道底部腐蚀多在管道5点~7点位置,往往由于管道底部形成连续的水相引起,既可能表现为均匀腐蚀减薄,也可能形成大量蚀坑。管道顶部腐蚀多发生在管道10点~2点位置,一般由湿气冷凝液膜引起,此时由于管道内部的缓蚀剂只能对底部水相起作用,而作用不到顶部液膜,导致腐蚀问题。
在这个层次判断,实际上看到的是腐蚀发生的部位。
2.2.2 从腐蚀的宏观后果认识油气管材的腐蚀失效
从人肉眼可直观区分的腐蚀失效宏观形态上来看,油气管材的腐蚀包括均匀腐蚀和局部腐蚀,广义上还包括以氢致开裂和应力腐蚀开裂为代表的环境敏感断裂。
均匀腐蚀是腐蚀的最常见形式,是由以可预测的腐蚀速率进行的相对均匀的电化学反应所造成。即使腐蚀发生在某个独立的局部区域,腐蚀也均匀地分布于金属表面,随着腐蚀的扩展,管材逐步均匀地变得更薄。这种均匀性意味着其腐蚀速率可进行预测,并可以通过留出足够的腐蚀裕量用于合理的管材壁厚设计。均匀腐蚀导致管道壁厚逐渐减小和管道强度损失,在超压情况下可能引起管道破裂。这种形式的腐蚀既可以发生在管道内部环境也可以发生在管道外部环境中。油气管材典型的均匀腐蚀包括管道外部土壤和海水引起的生锈,某些环境中CO2、H2S引起的导致腐蚀减薄等。
在石油天然气管材应用过程中,局部腐蚀种类很多,包括在碳钢甚至不锈钢表面形成的小孔状点蚀、台地腐蚀,螺纹丝扣、法兰面、沉积物下方等间隙结构引起的缝隙腐蚀等。点蚀具有自催化特点,在某些情况下,几个点蚀坑可能会相互连通造成管道失效,而这些管道的其他部位都完好无损。油气工业中引起局部腐蚀的典型代表是CO2腐蚀和细菌腐蚀,往往导致管道穿孔和泄漏风险。显然,在考虑CO2引起的腐蚀时,既有全面腐蚀问题,也有局部腐蚀问题。除了CO2以外,即使浓度极低的溶解氧,也会导致严重的点蚀破坏。介质中的氯离子可以促进点蚀、缝隙腐蚀等局部腐蚀,对于不锈钢腐蚀失效具有极强的促进作用。
环境敏感断裂是指正常的韧性材料由环境中腐蚀或氢的作用导致的脆性断裂,管道的内部环境或者外部环境均有可能引起此种类型的失效。石油天然气工业中典型的环境敏感断裂包括:氢脆(HE)、氢致开裂(HIC)和应力腐蚀开裂(SCC)。腐蚀过程或阴极保护中的阴极如果发生析氢反应,由氢离子还原形成的原子氢渗透进入材料会引起氢脆或氢致开裂,导致材料的韧性损失或形成阶梯状裂纹或鼓泡开裂。应力腐蚀开裂是指材料在腐蚀过程和拉伸应力联合作用下导致的低应力水平脆性断裂。应力的来源可能包括外部载荷、内部压力或残余应力(如焊接残余应力)。石油管材可能遭受的典型应力腐蚀开裂往往由H2S和氯化物引起。
在这个层次判断,实际上看到的是腐蚀给管材带来的直观后果。
2.2.3 从腐蚀发生的局部环境认识油气管材的腐蚀失效
从腐蚀发生的局部环境可以更细致深入地了解油气管材的腐蚀问题。绝大部分腐蚀问题发生的前提条件是有液态水(即构成腐蚀原电池中的电解质溶液)的存在,水相存在的状态直接影响了腐蚀发生的机制和形态,由此带来许多腐蚀类型的分支。一方面这些分支使得认识腐蚀过程更为容易,另一方面也给工程技术人员带来一定的困惑。
以管道内腐蚀为例,根据管道内部水的存在形式不同,腐蚀类型以不同的形态体现。如果管道输送介质中含水率较高且为层流,或者由于含水的输气管道在管道底部形成积水,均使得管道底部金属内壁接触连续的水相,为介质中的CO2、H2S等腐蚀性物质提供了腐蚀环境。如果管道输送过程中,在管道底部存在结垢、砂沉积或细菌菌落的附着滋生,则此时水相往往处于垢下环境或类似缝隙环境,往往引起严重的垢下腐蚀或细菌腐蚀。又如,当管道输送介质流速过高或者遇到弯头、三通等过流部件时,由于腐蚀介质和液相冲刷的联合作用,容易引起冲刷腐蚀。除此之外,还有发生在油水两相界面的类似水线腐蚀的形态,某些液相滞留严重的盲管或死水管线发生的腐蚀,法兰面间隙、螺纹丝扣间隙等渗入液体引起的缝隙腐蚀等,都是根据水的存在形式加以划分或区分的腐蚀形态。
从这个层次判断,实际体现了腐蚀发生的真实局部环境和环境促进腐蚀的机制。
2.2.4 从导致腐蚀的直接原因和机理认识油气管材的腐蚀失效
基于上面的讨论,当腐蚀过程具备适宜的环境时,腐蚀的发生就依赖所谓的“腐蚀剂”,也称为“去极化剂”,即能够引起腐蚀反应或夺取金属电子的物质。这也是许多文献和经验中经常论及的腐蚀概念,如CO2腐蚀、H2S腐蚀、溶解氧腐蚀、元素硫腐蚀、有机酸腐蚀、微生物腐蚀(或细菌腐蚀)等,实际上这种定义或命名方式,体现的是什么直接导致了腐蚀。从腐蚀的各类层次角度,有可能腐蚀是CO2直接导致的,但由于处于垢下或缝隙环境,有时也可以说是垢下腐蚀,这并不矛盾,只是看待问题的角度有所不同。
同时,还有一些物质实际上并非直接参与腐蚀阴极或阳极反应的得失电子过程,而是以不同的方式加速了腐蚀或引起严重的局部腐蚀。如常说的氯离子腐蚀,实际上是氯离子对腐蚀的显著促进作用,破坏不锈钢钝化膜或碳钢腐蚀产物膜,引起点蚀甚至应力腐蚀开裂。又例如细菌腐蚀中的硫酸盐还原菌(SRB)腐蚀,实际上只是参与了对阴极反应形成的氢原子的消耗,促进了腐蚀过程,但由于其菌落繁殖和生物膜结痂附着于管道内壁表面,往往诱发严重的点蚀。
还有一种情况是电偶腐蚀,电偶腐蚀实际上也需要具体的腐蚀剂,但由于异种金属联接、焊缝部位与母材的差异、涂层或腐蚀产物膜覆盖不均匀、垢下或SRB菌落内外等形成的大面积阴极-小面积阳极的电偶对出现,也会导致阳极区严重的局部腐蚀。
在油气工业中,更为突出的促进腐蚀问题的原因还在于油套管或管道内部“高温高压”的环境,简单而言,温度的升高可以极大促进腐蚀过程,压力的升高使得溶解在水中的腐蚀性介质的量增加,都会显著促进腐蚀过程。
2.2.5 从实际工况的综合层面认识油气管材的腐蚀失效
油气管材某一部位腐蚀的发生,多数情况下是由多个因素或者机制协同作用产生。例如,管道底部发生腐蚀,首先是由于管道底部存在积水,提供了腐蚀的环境;其次,要存在能够引起腐蚀的物质,也就是CO2或者H2S的存在;再次,管道底部细菌的滋生、垢的形成或者砂的沉积,提供了更加适合局部腐蚀发展的局部环境,例如所谓的细菌腐蚀、垢下腐蚀,这些局部环境促使了蚀坑的形成和快速发生,并引起严重后果;最后,腐蚀控制措施如果失效,例如缓蚀剂无法有效作用到微生物膜或者砂沉积的区域,则导致蚀坑形成,直至穿孔。
因此,综合考虑各层次的腐蚀问题和腐蚀因素,在腐蚀选材、腐蚀预测和腐蚀控制各环节综合应对腐蚀风险,是控制腐蚀的关键。