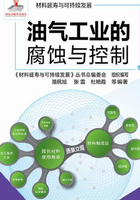
2.1 油气管材所处的内外腐蚀环境介质特点
2.1.1 内腐蚀环境介质特点
油气管材内腐蚀的介质环境有三个显著特点:一是气、水、烃、固共存的多相流腐蚀介质;二是高温和/或高压环境;三是H2S、CO2、O2、Cl-和水分是主要腐蚀物质。
(1)多相流
石油工业的多相流主要是气相、液相(包括水相和烃相)和固相(固体沙粒)多相共存且流动的多相流。与单相介质腐蚀相比,多相介质腐蚀情况比较复杂,以水-烃两相存在的情况为例,通常认为当油水比大于70%的情况时,一般存在油包水的情况,腐蚀速率较低;但当油水比小于30%的情况时,则会出现水包油的情况,腐蚀速率较高。即便当水包油时,也会出现两种情况:一是油中含有可起缓蚀剂作用的物质,这时油水两相介质腐蚀由于受到缓蚀作用,其腐蚀速率比单相水介质的腐蚀速率要低;二是当油中不含有缓蚀作用物质时,由于各相间的互相促进,其腐蚀性有时会比单相介质强得多。
多相流的腐蚀行为不仅由于多相介质对腐蚀的作用与单相介质不同,而且由于流动的作用会造成多相流冲刷腐蚀,而多相流冲刷腐蚀的行为又与流型、流速以及腐蚀反应物质和腐蚀产物在流体中的传质过程有关。
(2)高温和/或高压环境
对于油气井,石油管材多在高温高压的环境中服役,特别是随着石油工业的发展,其打井越来越深,例如我国西北地区的油气田,已经开始开采6000~7000m的深井,其井下温度超过150℃甚至接近180℃,压力甚至达到100MPa以上。对于地面集输管线和油气长输管线,也往往在较高压力下运行。高温高压环境材料的腐蚀规律和机理往往不同于室温常压。温度和压力是材料腐蚀行为的重要影响因素,例如对于CO2腐蚀,由于腐蚀产物膜对材料的保护性与温度和压力有关,而表现出在一定温度下和一定CO2分压下,材料的腐蚀速率达到最大值。所以尽管多数情况下,高温高压容易导致材料更严重的腐蚀,但有时高温状况对材料抗介质腐蚀是有利的,比如大于100℃时材料对硫化物应力腐蚀开裂的敏感性大大降低。
未来的石油工业将面临油井开采后期含水量的提高,深井、超深井的开发导致温度和压力的进一步提高,强腐蚀环境油井的开发和注CO2驱采油技术应用导致CO2、H2S和Cl-含量上升,这些都导致石油管的内腐蚀更趋严重。
(3)高含CO2-H2S
自然界中地质结构蕴藏着丰富的天然CO2气体,在石油、天然气勘探和开采过程中,CO2作为伴生气体同时产出。另外,CO2与原油混溶,可以使原油发生溶胀,CO2分子进入烃类分子中间降低烃类分子的内摩擦力,从而降低原油的黏度并提高其流动性。因此,将CO2加压注入油井中,可以明显提高原油采收率,增加原油产量,这是早期的CO2非混相驱油原理。由此可见,在石油、天然气开采与集输过程中广泛存在着CO2气体。一般来说,干燥的CO2对碳钢并没有腐蚀性或其腐蚀性极为轻微。然而,当这些伴生或回注的CO2气体溶于水形成H2CO3,则会对石油、天然气开采与集输过程中的油套管、输送管线造成严重的腐蚀,而且CO2溶于水所形成H2CO3可以在碳钢表面直接还原,因此在相同的pH值下,CO2水溶液的腐蚀性比强酸(如HCl)溶液还要严重[1,2]。
在石油、天然气开采和集输过程中,CO2作为伴生气对油套管及集输管线会造成严重的腐蚀。油气集输管道和设备往往由于CO2腐蚀而导致泄漏。CO2腐蚀是油气田生产中管材腐蚀失效的主要原因之一。随着油气田开发进入中后期,深层高压CO2油气田的开发,油气中的CO2含量和含水率上升,以及回注CO2强化采油工艺(EOR)的广泛应用,CO2腐蚀问题更趋严重。
CO2腐蚀往往引起油气田管道和设备的腐蚀失效,给油气田造成重大的经济损失,包括灾难性事故和生态环境的污染。1943年美国得克萨斯州油田气井以及1945年路易安那州油井首次认为出现了CO2腐蚀问题[3]。1961~1962年苏联开发克拉斯诺尔边疆区油气田时也发现CO2腐蚀。1988年英国阿尔法平台因腐蚀破坏而发生爆炸,造成166人死亡,导致北海油田年减产12%[4]。美国Mississipi的LittleGreek油田采用回注CO2强化驱油技术(EnhancedOilRecovery,EOR),在没采取抑制CO2腐蚀措施的情况下,油管使用不到5个月就腐蚀穿孔,其腐蚀速率达到12.5mm/a。美国另一个Sacroc油田也采用了CO2EOR采油技术,井口虽然采用了AISI410不锈钢,但仍遭受严重的CO2腐蚀[5]。国内油气田的CO2腐蚀破坏在20世纪80年代中期明显突出,中国石油工业每年所耗费的石油管材价值约100亿元,其中大部分因腐蚀而报废。在1971年5月~1986年2月期间,四川天然气管网因腐蚀导致爆炸事故83次,其中第一次事故就造成24人伤亡[4]。华北油田馏58井,曾日产原油400t,天然气100000m3,其N80油管仅使用了18个月,就被腐蚀得千疮百孔,不得不报废,并造成井喷,被迫停产[6]。塔里木雅克拉气田一口气井由于油管腐蚀使天然气由油套管的环空窜入地面着火72天,造成直接经济损失3000万元。吉林油田万五井由于油管遭受严重的CO2腐蚀,800m油管掉落井下[5]。其他油田如胜利、大庆、中原等油田均面临着严重的CO2腐蚀。另外,因腐蚀所造成的原油泄漏还破坏水资源、破坏生态环境并造成资源浪费。
随着我国能源结构的改变,对石油、天然气的需求日益增加,越来越多腐蚀环境复杂的高含硫油气田逐渐开发,诸如川东北罗家寨和普光等高含硫气田,部分区块H2S和CO2含量甚至超过10%,而地面管线的防腐措施大都采用碳钢加缓蚀剂的方法,碳钢在高温高压H2S/CO2共存条件下的腐蚀问题突出,腐蚀造成的材料损伤不仅给国家造成巨大的经济损失,而且一旦因腐蚀导致管道泄漏或开裂,引起爆炸或剧毒的H2S气体扩散,将造成重大安全事故、人员伤亡和环境污染。
国内外对于CO2腐蚀、H2S腐蚀、HIC和SSC已经开展了较长时间的研究,获得了许多有益的结果。在CO2腐蚀环境里,碳钢的腐蚀产物通常是由FeCO3组成的膜,具有良好的附着性,较高致密性,一定条件下可以抑制碳钢的进一步腐蚀[7~9]。在H2S的腐蚀环境里,碳钢通常形成Fe-S化合物的腐蚀产物,Fe的硫化物腐蚀产物膜控制着整个腐蚀过程,对基体起到保护作用,但在可能破坏腐蚀产物膜的环境介质中会发生局部腐蚀[10]。H2S与CO2共存条件下,二者的腐蚀机理存在竞争与协同效应。虽然单纯CO2造成的腐蚀减薄比H2S严重,但一旦存在H2S,其腐蚀又往往起控制作用。H2S的存在既能通过阴极反应加速CO2腐蚀,又能通过硫化物腐蚀产物膜减缓腐蚀。
2.1.2 外腐蚀环境介质特点
石油管材的外腐蚀主要是由土壤、地下水、海水及微生物所造成的腐蚀。由于土壤腐蚀更为量大面广,下面着重介绍土壤腐蚀。土壤腐蚀属于电化学腐蚀范畴,其腐蚀机理可用电化学腐蚀的理论描述。但是由于土壤的组成与结构复杂多变,土壤的腐蚀性表现出很大的差异。埋地管道可以在一年内腐蚀穿孔,也可以数十年无明显变化。同一根输油管道在某些地段腐蚀极为严重,但在另一些地段却完好无损[11]。
(1)土壤的特性
溶解于土壤中的氧和二氧化碳等气体都可以成为土壤腐蚀的腐蚀剂。但电解质的存在是产生土壤电化学腐蚀的必要条件。在土壤体系中,土壤胶体往往带有电荷,并吸附一定数量的负离子,当土壤中存在水分时,土壤即成为一个带电胶体与离子组成的导体,因此土壤可认为是一个腐蚀性多相电解质体系。这种电解质不同于水溶液和大气等腐蚀介质,有其自身的特点,主要表现在以下几个方面。
①土壤的多相性。土壤是一个由固、液、气三相组成的多相体系。其中固相主要由含多种无机矿物质以及有机物的土壤颗粒组成;液相主要指土壤中的水分,包括地下水和雨水等;气相即为空气。土壤的多相性还在于不同时间、不同地点各相的组成与含量也是不同的。土壤的这种多相性决定了土壤腐蚀的复杂性。
②土壤的不均一性。土壤性质和结构的不均匀性是土壤电解质的最显著特征。这种不均一性使得土壤的各种理化性质,尤其与腐蚀有关的电化学性质也随之不同,导致土壤腐蚀性的差异。钢铁在理化性质较一致的土壤中平均腐蚀速率是很小的,NBS(美国国家标准局)长期土壤埋件的试验结果表明,较均一土壤中金属的平均腐蚀速率仅为0.02mm/a,最大为0.064mm/a。而在差异较大的土壤中,腐蚀速率可达0.46mm/a。
③土壤的多孔性。在土壤的颗粒间存在着许多微小孔隙,这些毛细管孔隙就成为土壤中气液两相的载体。其中水分可直接填满孔隙或在孔壁上形成水膜,也可以溶解和吸附一些固体成分形成一种带电胶体。正是由于水的这种胶体形成作用,使土壤成为一种由各种有机物、无机物胶凝物质颗粒组成的聚集体。土壤的孔隙度和含水量又影响着土壤的透气性和电导率的大小。
④土壤的相对稳定性。土壤的固体部分对于埋设在土壤中的管道,可以认为是固定不动的,仅有土壤中的气相和液相作有限的运动。例如,土壤孔隙中气体的扩散,以及地下水的移动等。
(2)土壤腐蚀的影响因素
土壤腐蚀速率的大小与土壤的各种物理、化学性质及环境因素有关,这些因素间的相互作用,使得土壤腐蚀性比其他介质更为复杂。在众多的因素中,以土壤的含水量、含氧量、含盐量、酸碱度及电阻率等因素与土壤腐蚀性之间的关系最为密切。
①含水量。土壤中含水量对腐蚀的影响很大。土壤的水分对于金属溶解的离子化过程及土壤电解质的离子化都是必需的,土壤中若没有水分,则没有电解液,电化学腐蚀就不能进行。土壤是由各种矿物质和有机质所组成的,因而总含有一定量的水分,所以金属在土壤中的腐蚀是不可避免的。但含水量不同,其腐蚀速率也不一样。一般而言,土壤含水量高,有利于土壤中各种可溶盐的溶解,土壤回路电阻减小,腐蚀电流增大。但含水量过高时,由于可溶盐量已全部溶解,不再有新的盐分溶解,而土壤胶粒的膨胀会阻塞土壤孔隙,使得空气中氧不能充分扩散到金属表面,不利于氧的溶解和吸附,去极化作用得到减低,腐蚀速率反而会减小。土壤中的水分除了直接参与腐蚀的基本过程,还影响到土壤腐蚀的其他因素,诸如土壤的透气性、离子活度、电阻率,以及细菌的活动等。如土壤含水量增加,土壤电阻率将减小,透气性降低,从而使得氧浓差电池作用增大。实际观察到的埋地管道底部腐蚀往往比上部严重,就是因为管道底部接近地下水位,湿度较大,含氧低,成为腐蚀电池的阳极而遭到腐蚀。而顶部因埋得较浅,含水少,成为腐蚀电池的阴极而不腐蚀。
②含氧量。氧不仅作为腐蚀剂成为影响土壤腐蚀的一个重要因素,而且还在不同的土壤与管道接触部位形成氧浓差电池而导致腐蚀。就管道材料而言,含氧量愈高,腐蚀速率则愈大,因为氧的去极化作用是通过吸氧反应实现的,并随到达阴极的氧量增加而加快。但同时,如果与管道接触的土壤介质中氧含量存在差异,含氧量高的部位以阴极反应即氧的还原反应为主,而相邻的含氧量低的部位以阳极反应即金属失电子而离子化反应为主,由此在管道不同部位间形成腐蚀电池,造成氧含量低的部位显示出显著的局部腐蚀特征。
土壤中氧的来源主要是空气的渗透,另外雨水及地下水中的溶解也会带来少量的氧。因此,土壤的密度、结构、渗透性、含水量及温度等都会影响到土壤中的氧含量。在通常情况下,就宏观电池腐蚀和细菌腐蚀而言,黏性较大的土壤比透气性好的土壤腐蚀性要强,但如果发生腐蚀的原因是由氧浓差腐蚀电池引起的,则两种土壤都对腐蚀不利。
③含盐量。通常土壤中可溶盐含量一般在2%以内,为80~1500mg/kg,是形成土壤电解液的主要因素。含盐量愈高,土壤电阻率愈小,腐蚀速率愈大。土壤中可溶盐的种类很多,与腐蚀关系密切的阴离子类型主要有:碳酸根,氯和硫酸根离子。其中以氯离子对土壤腐蚀促进作用较大,所以海底管道在防护不当时腐蚀十分严重。阳离子主要有钾、钠、镁、钙离子,一般来说对腐蚀的影响不大,只是通过增加土壤溶液的导电性来影响土壤的腐蚀性。但在非酸性土壤中钙、镁的离子能形成难溶的氧化物和碳酸盐,在金属表面上形成保护层,能减轻腐蚀。如埋在石灰质土壤中管道腐蚀轻微,就是很典型的例子。
④酸碱度。土壤的酸碱度取决于土壤中H+浓度的高低。H+来源较多,有的来源于土壤的酸性矿物质的分解,有的来自生物或微生物的生命活动形成的有机酸和无机酸,但其主要来源还是空气中的CO2溶于水后电离产生的H+。土壤酸碱度对腐蚀的影响非常复杂。一般认为,随着土壤pH值降低,土壤对管道的腐蚀速率增加。因为介质酸性愈大,氢的过电位就愈小,阴极反应愈易进行,因而金属腐蚀速率也愈快。管道在中性土壤中的氢过电位比在酸性土壤中要高,故中性土壤中金属的腐蚀速率一般比在酸性土壤中要慢。但在近中性土壤中,管道有可能发生应力腐蚀开裂(SCC)。加拿大油气输送管线事故调查及研究表明,随着管道服役时间的延长,在近中性pH土壤环境中,管道发生土壤应力腐蚀开裂的可能性会不断增大。
⑤电阻率。土壤电阻率是表征土壤导电能力的指标,在土壤电化学腐蚀机理研究过程中是一个很重要的因素。在长输地下金属管道的宏电池腐蚀过程,土壤电阻率起主导作用。因为宏电池腐蚀中,电极电位可达数百毫伏,此时腐蚀电流大小将受欧姆电阻控制。所以,在其他条件相同的情况下,土壤电阻率愈小,腐蚀电流愈大,土壤腐蚀性愈强。土壤电阻率大小取决于土壤中的含盐量、含水量、有机质含量及颗粒、温度等因素。由于土壤电阻率与多种土壤理化性质有关,因此许多情况下,土壤电阻率被用作评价土壤腐蚀性的强弱。一般来说,电阻率在数千欧姆·厘米以上,土壤对管道金属的腐蚀较轻微,而当电阻率低至几百甚至几十欧姆·厘米以下时,其腐蚀性相当强。所以管道通过低洼地段时,产生腐蚀的可能性很大。
另外,土壤电阻率对阴极保护电流的分布影响很大,当土壤电阻率均匀,管道电阻忽略不计时,与阳极距离最近点电流密度最大,距阳极愈远,电流愈小。如果沿管道土壤电阻率分布不均,则对管道电流分布产生较大影响,电阻率小的部位,保护电流较大,从而使保护电位下降,造成腐蚀。
除了土壤的特有性质外,管道服役的外部环境诸如杂散电流和人为施加的外部环境如阴极保护不当等,都会引起一些特定的腐蚀形式。
我国现有油气输送管线长度已经突破10万千米,近十年是油气管线建设的高潮期,同时也随着油气输送管线服役时间的延长,逐渐暴露出各类腐蚀问题,甚至造成严重的失效事故,严重威胁油气生产安全。因此,全面了解油气管线内部和外部的各类腐蚀形式和问题,发展针对性的腐蚀控制技术,是提升油气管材服役安全的重要途径。