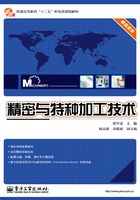
2.3 金刚石刀具
超精密切削加工属微量切削,切削深度可在0.075μm以内,相当于从材料晶格上逐个地去除原子,只有切削力超过晶体内部的原子结合力才能产生切削作用。目前,只有天然金刚石刀具能承受如此大的切削力,且具有较高的耐用度。在超精密切削加工中也可以采用高性能陶瓷刀具、TiN、金刚石涂层的硬质合金刀具以及CBN刀片,但由于其加工表面质量不如天然金刚石好,仅用于表面质量要求不十分严格的场合。
天然单晶金刚石被一致公认为理想的、不能替代的超精密切削刀具材料,是因为它有一系列优异的特性,如硬度极高、耐磨性和强度高、导热性能好、和有色金属间摩擦因数低、能磨出极锋锐的刀刃等。但是它与钢铁材料的亲和性很强,因而应用范围受到限制。人造聚晶金刚石也在逐步应用于超精密加工用刀具,但其性能远不如天然金刚石。
金刚石刀具有两个较重要的问题:一是晶面的选择,这对刀具的使用性能有着重要的关系;二是金刚石刀具的刃磨质量——切削刃钝圆半径rn,它关系到切削变形和最小切削厚度,因而影响到加工表面质量。
2.3.1 金刚石的结构与性能
1.金刚石的晶体结构
金刚石晶体属于立方晶系。天然单晶金刚石为规整的八面体、十二面体和六面体。金刚石晶体具有各向异性和解理现象。不同晶向的物理性能相差很大。
(1)金刚石晶体的晶轴和晶面
由晶体学原理知,立方晶系的金刚石晶体有三个主要晶面,即(100)、(111)和(110)晶面。用X射线垂直照射这些晶面对,形成的衍射图形呈现出四次、三次和二次对称现象,因此称与上述晶面垂直的轴分别为四次对称轴[垂直于(100)晶面]、三次对称轴[垂直于(111)晶面]和二次对称轴[垂直于(110)晶面]。规整的八面体、十二面体和六面体单晶金刚石晶体中均有三根四次对称轴、四根三次对称轴和六根二次对称轴。
以八面体为例,八面体由8个(111)面围成外表面,如图2-13所示。其中,两个对应四个外表面相交点的连线为四次对称轴,与四次对称轴垂直的各面均为(100)晶面(图2-13(a));(111)晶面的法线方向为二次对称轴(图2-13(b));每两相对棱边的中点的连续方向均为二次对称轴,与二次对称轴垂直的为(110)晶面(图2-13(c))。
(2)金刚石晶体的面网
晶体内部分布有原子的面称为晶面,也称面网。如上所述,金刚石属立方晶系,主要有(100)、(111)和(110)面网。三种面网上原子排列形式的不同、原子密度的不同及面网间距离的差异,决定了全刚石的晶体各向异性。晶体在不同晶向上,性能差异极大。

图2-13 八面体金刚石的晶轴和晶面
1)金刚石晶体各面网的原子排列形式——最小单元
金刚石晶体的(100)、(111)和(110)面网的最小单元如图2-14所示。(100)面网的最小单元为正方形,边长为D,有5个碳原子(图2-14(a));(110)面网的最小单元为矩形,边长分别力D和 - D,有8个碳原子(图2-14(b));(111)面网的最小单元为等边三角形,边长为 -
D,有6个碳原子(图2-14(c))。其中D(D=ao=0.35667nm)为刚石晶体中单位晶胞(六面体)的边长。

图2-14 金刚石不同晶面的面网的原子排列形式——最小单元
2)金刚石晶体的面网距
晶体面网之间的距离称为面网距。金刚石晶体的(100)、(111)和(110)面网之间的距离,如图2-15 所示。其中(100)面网和(110)网的分布是均匀的,(100)面网的面间距为D/4=0.089nm,(110)面网的面间距为 - D/4=0.126nm;而(111)面网的面间距则出现一宽一窄的交替结构;宽的面间距为 -
D/4=0.154nm,窄的面间距为 -
D/12=0.051nm。窄的面间距极小,实际中可以把这相邻两个面网看成一个加厚的面网。两个加厚面网的面间距,即(111)面的宽的面间距,成为(111)面的实际面间距。(111)面的宽的面间距(0.154nm)是金刚石晶体中所有晶面面间距中最大的一个。
3)金刚石晶体的面网密度
面网的单位面积上的原子数称为面网密度网密度决定了金刚石的硬度和耐磨性。
由图2-14所示的关系可得(100)、(110)和(111)的面网密度之比为
(100)密度:(110)密度:(311)密度:1:1414:1.154
由上述比例可以得到(110)面网密度最大的结论。但是实际的金刚石晶体结构中,(111)面网的面间距出现一宽一窄的交替,如图2-15所示,窄的面间距只有宽网面的1/3,因此,可以把相邻的两个面网看成一个加厚的面网,此时其密度应为两个面网密度之和,即(111)面网密度增加了一倍。因此,三个晶面的实际面网密度之比为
(100)密度:(110)密度:(111)密度:1:1414:2308
测试表明,金刚石晶体的(111)晶面的硬度和耐磨性均为最高证明了面网密度分析的正确性。

图2-15 金刚石晶体不同晶面的面网距
(3)金刚石晶体的解理现象
解理现象是金刚石晶体的一个非常重要的特性。它是指晶体受到定向的机械力作用时,可以沿平行于某个平面平整地劈开的现象。金刚石晶体中碳原子在(111)面分布的情况如图2-16所示。图中面网与图面垂直(水平直线),原子间的直线表示共价链的结合方向,可看到一宽一窄交替出现的面间距。由于(111)面网的宽面间距比(100)和(110)面网的面间距都大,并且其连接共价键数最少(只有一个),所以在面间距大的(111)而网之间,只需击破一个共价键就可以使其劈开。实际中金刚石内部的解理劈开,在绝大多数情况下得到的是与(111)网面平行的很平的劈开面。

图2-16(111)面网的碳原子分布示意图和解理劈开面
2.金刚石的性能
金刚石是人类所知的最硬的材料,由很多特殊的优异性能,在工业中得到广泛的应用。约在5000年前在印度就首先发现了天然单晶金刚石,而人造金刚石是美国通用电器公司于1954年首先研制成功的。我国于1963合成第一颗人造金刚石,1965年投入工业生产。
超精密切削加工刀具用金刚石需要大颗粒(0.5~1.5克拉,1克拉=0.2g)优质(一级品)的单晶金刚石。优质天然单晶金刚石多说为规整的8面体或菱形12面体,少数为6面立方体或其他形状,浅色透明,无杂质,无缺陷。大颗粒人造单晶金刚石是在超高压高温下由子晶生长而成,其性能和天然金刚石相近,但制造技术复杂,价格仍较昂贵。
尽管金刚石价格昂,在超精密加工领域采用天然金刚石刀具无论在价格上还是在精度上都比传统加工方法具有明显优势。
金刚石由于其晶体各向异性,在不同方向其物理力学性能是有明显差别的。金刚石的物理力学性能如表2-6所示。
金刚石的硬度和热导率都较高,和有色金属间的摩擦系数低,开始氧化温度较高,因此非常适合作为超精密切削加工的刀具。此外,单晶金刚石可以研磨达到极锋利的切削刃(rn可以小到0.05~0.01μm),没有其他材料能磨到如此锋利并能长期切削而磨损较小。
表2-6 金刚石的物理力学性能

2.3.2 金刚石晶体的定向
金刚石晶体属于平面立方晶系,由于每个晶面上原子排列形式和原子密度的不同,以及晶面之间距离的不同,造成天然金刚石晶体的各向异性。因此,可以利用这个特性对金刚石晶体进行定向。用于刀具的金刚石晶体的定向原则就是正确地确定刀面及刀刃的位置,使切削刀具承受切削力的方向在某一确定的基本晶面上,并与该晶面硬度最大的方向一致,以使刀具磨损最大的方向具有最高的耐磨性。但是,在定向时必须注意:刀具的受力方向不能与金刚石的解理面平行,同时还应该考虑到每个面在研磨时的磨向。
晶体定向主要有三种方法:人工目测晶体定向、激光晶体定向和X射线晶体定向,各种定向方法都有优缺点。
2.3.3 金刚石刀具的结构
衡量金刚石刀具质量的好坏,首先看其能否加工出高质量的超光滑表面(Ra0.005~0.02μm),其次是看它能否有较长的切削时间保持切削刃锋锐(一般要求切削长度数百千米),切出极高质量的加工表面。
为要满足上述要求,设计金刚石刀具时最主要问题有三个,即确定切削部分的几何形状、选择合适的晶面作为刀具的前后面、确定金刚石在刀具上的固定方法和刀具结构。
1.金刚石刀具切削部分的几何形状
(1)刀头形式
金刚石刀具刀头一般采用在主切削刃和副切削刃之间加过渡刃——修光刃的形式,以对加工表面起修光作用,获得好的加工表面质量。若采用主切削刃与副切削刃相交为一点的尖锐刀尖,则刀尖不仅容易崩刃和磨损,而且还在加工表面上留下加工痕迹,从而增加表面粗糙度值。
修光刃有小圆弧修光刃、直线修光刃和圆弧修光刃之分。国内多采用直线修光刃,这种修光刃制造研磨简单,但要求对刀良好,即直线修光刃应严格和进给方向一致,才能得到令人满意的加工表面。直线修光刃的长度一般取0.1~0.2mm。国外金刚石刀具多采用圆弧修光刃。国外标准的金刚石刀具,推荐的修光刃圆弧半径R=0.5~3mm。因为超精密切削时进给量甚小(一般f<0.02mm/r),即使圆弧修光刃留下一定的残留面积,对表向粗糙度也没有太大影响。采用圆弧修光刃时,对刀容易,使用方便。但刀具制造研磨困难,所以价格也高。
金刚石刀具的主偏角一般为30°~90°,以45°主偏角应用最为广泛。几种石同的刀头形式如图2-17所示,但一般不采用如图2-17(a)所示的形式。
(2)前角和后角
根据加工材料不同,金刚石刀具的前角可取0°~5°,后角一般取αp=5°~6°。因为金刚石为脆性材料,在保证获得较小的加工表面粗糙度前提下,为提高刀刃的强度,应采用较大的刀具楔角β,所以宜取较小的刀具前角和后角。但增大金刚石刀具的后角αp,减少刀具后面和加工表面的摩擦,可减小表面粗糙度值,所以,加工球面和非球曲面的圆弧修光刃刀具,常取10°。

图2-17 金刚石刀具的刀头形式
2.选择合适的晶面作为金刚石刀具前、后面
单晶金刚石晶体各方向性能(如硬度和耐磨性、微观强度和解理碎裂的概率、研磨加工的难易程度等)相差极为悬殊。因此,前面和后面选择是金刚石刀具设计的一个重要问题。目前国内制造金刚石刀具,一般前面和后面都采用(110)晶面或者和(110)晶面相近的面(±3°~5°)。这主要是从金刚石的这两个晶面易于研磨加工角度考虑的,而未考虑对金刚石刀具的使用性能和刀具耐用度的影响。
目前关于国外的金刚石刀具前、后面的晶面选择资料很难找到,但从相关报道可以看出,有选用(100)晶而作为前面或后面的,也有选用(110)晶面作为前面或后面的。选用的理由说法不一,也不够详尽。但是选用(111)晶面作为前面或后面者极少,其主要原因在于(111)晶面硬度太高,而微观破损强度并不高,研磨加工困难,很难研磨加工出精密金刚石刀具所要求的锋锐的刃口。
3. 金刚石刀具上的金刚石固定方法
对于金刚石车刀,通常是把金刚石固定在小刀头上,小刀头用螺钉或压板固定在车刀刀杆上,或将金刚石直接固定在车刀刀杆上。
金刚石在小刀头上的固定方法如下:
(1)机械夹固
将金刚石的底面和加压面磨平,用压板加压固定在小刀头上。采用这种固定方式时,需要较大颗粒的金刚石。
(2)用粉末冶金法固定
将金刚石放在合金粉末中,经加压在真空中烧结,使金刚石固定在小刀头内。采用这种固定方法可使用较小颗粒的金刚石,较为经济,因此,目前国际上多采用该方法。
(3)使用黏结或钎焊固定
使用无机黏结剂或其他黏结剂固定金刚石。但黏结强度有限,金刚石容易脱落。钎焊固定方法是一种很好的办法,但技术不易掌握。
金刚石刀具的加工研磨和用钝重磨,是一项难度很大的技术。国内外的金刚石刀具使用者一般都不自己磨刀,而将金刚石刀具送回原制造厂重磨。重磨收费很高且很不方便。Sumitomo公司推出一次性使用不重磨的精密金刚石刀具,即将金刚石钎焊在硬质合金片上,再用螺钉夹固在车刀杆上。刀片上的金刚石由制造厂研磨得很锋锐,用钝后不再重磨。这种刀具使用颗粒很小的金刚石,因此,价格比较便宜,具有很好的推广价值。