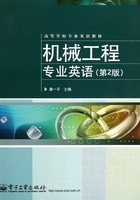
4.5 Die Manufacturing Methods
Various manufacturing methods, either singly or in combination, are used in making dies. These processes include casting, forging, machining, grinding, and electrical and electrochemical methods of die sinking. Dies are usually heat treated for greater hardness and wear resistance. If necessary, their surface profile and finish are improved by finish grinding and polishing, either by hand or by programmable industrial robots.
The choice of a die manufacturing method depends on the particular operation in which the die is to be used and on its size and shape. Cost often dictates the process selected, because tool and die costs can be significant in manufacturing operations. For example, a set of dies for automotive body panels can cost $2 million. Even small and relatively simple dies can cost hundreds of dollars. On the other hand, because a large number of parts are usually made from the same die, die cost per piece is generally only a small portion of a part’s manufacturing cost.
Dies may be classified as male and female; they may also be classified by their size. Small dies generally are those that have a surface area of 103mm2-104 mm2, whereas large dies have surface areas of 1 m2 and larger, such as those used for pressworking automotive body panels.
Dies of various sizes and shapes can be cast from steels, cast irons, and nonferrous alloys. The processes used range from sand casting (for large dies weighing many tons) to shell molding (for small dies). Several die materials, such as tool and die steels, high-speed steels, and carbides, are often used to make dies. Cast steels are generally preferred for dies for large workpieces, because of their strength and toughness and the ease with which their composition, grain size, and properties can be controlled and modified.
Most commonly, dies are machined from forged die blocks by processes such as milling, turning, grinding, and electrical and electrochemical machining. Typically, a die for hot working operations is machined by milling on computer-controlled NC machines. Machining can be difficult for high-strength and wear-resistant die materials that are hard or heat treated.
These operations can be time consuming. As a result, nontraditional machining processes are used extensively, particularly for small- or medium-sized dies. These processes are generally faster and more economical, and the dies usually do not require additional finishing. Diamond dies for drawing fine wire are manufactured by producing holes with a thin rotating needle coated with diamond dust, using oil as a lubricant.
For improved hardness, wear resistance, and strength, die steels are usually heat treated. Improper heat treatment is one of the most common causes of die failure. Heat treatment may distort dies through the action of micro-structural changes and of uneven thermal cycling. Particularly important are the condition and composition of the die surfaces.
After heat treatment, dies are subjected to finishing operations, such as grinding, polishing, and chemical and electrical processes, to obtain the desired surface finish and dimensional accuracy. The grinding process, if not controlled properly, can cause surface damage from excessive heat and can induce harmful residual tensile stresses on the surface of the die, which will reduce its fatigue life.[6] Scratches on a die’s surface can act as stress raisers. Likewise, commonly used die-making processes, such as electrical-discharge machining (EDM), can cause surface damage and cracks, unless the process parameters are carefully controlled.