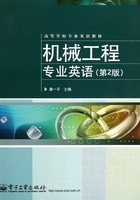
4.4 Precision Forging
For economic reasons the trend in forging operations today is toward greater precision, which reduces the number of additional finishing operations. Operations in which the part formed is close to the final dimensions of the desired component are known as near-net-shape or net-shape forging. In such a process, there is little excess material on the forged part, and it is subsequently removed (generally by trimming or grinding).
In precision forging, special dies produce parts having greater accuracies than those from impression-die forging and requiring much less machining. The process requires higher capacity equipment, because of the greater forces required to obtain fine details on the part. Because of the relatively low forging loads and temperatures that they require, aluminum and magnesium alloys are particularly suitable for precision forging; also, little die wear takes place and the surface finish is good. Steels and titanium can also be precision-forged. Typical precision-forged products are gears, connecting rods, housings, and turbine blades.
Coining. Coining essentially is a closed-die forging process typically used in minting coins, medallions, and jewelry; the slug is coined in a completely closed die cavity.[5] In order to produce fine details, the pressures required can be as high as five or six times the strength of the material. On some parts, several coining operations may be required. Lubricants cannot be applied in coining, because they can become entrapped in the die cavities and, being incompressible, prevent the full reproduction of die-surface details.
The coining process is also used with forgings and with other products, to improve surface finish and to impart the desired dimensional accuracy. This process, called sizing, involves high pressures, with little change in part shape during sizing. Marking of parts with letters and numbers can be done rapidly by a process similar to coining.