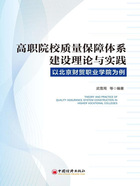
第一章 质量保障理论
第一节 全面质量管理理论
一、全面质量管理的起源与演变
在介绍全面质量管理之前,我们有必要明确一下有关质量的定义。国家标准(GB/T 19000—2016/ISO 9000:2015)对质量的定义为:一组固有特性满足要求的程度。更具象的定义是从用户的角度去定义质量:质量是用户对一个产品(包括相关的服务)满足程度的度量。质量是产品或服务的生命。质量受企业生产经营管理活动中多种因素的影响,是企业各项工作的综合反映。要保证和提高产品质量,必须对影响质量的各种因素进行全面而系统的管理。
全面质量管理(Total Quality Management)是一个专业的管理学领域,是以产品质量为核心,建立起一套科学严密高效的质量体系,以提供满足用户需要的产品或服务的全部活动。全面质量管理就是企业组织全体职工和有关部门参加,综合运用现代科学和管理技术成果,控制影响产品质量的全过程和各因素,较为经济地研制、生产和提供用户满意的产品的系统管理活动。其是通过让顾客满意和本组织所有成员及社会受益而达到长期成功的管理途径。这种管理途径是商品竞争的需要,也是科学技术发展共同作用下的结果,也随着科学技术、生产力水平及管理科学的现代化的发展而发展,各因素之间有着密不可分的关系。从工业发达国家解决产品质量问题涉及的理论和使用的技术预防方法的发展变化来看,它的发展过程大致可划分为3个阶段。
(一)质量检验管理阶段
质量管理的概念产生于19世纪70年代。在当时,科学技术落后,生产力比较低下,各手工作坊成为生产力的中坚力量。当时人们尚没有科学管理的概念,手工作坊无法将加工产品和检查质量进行合理的分工,这就导致了生产工人要同时扮演加工者及检验者的角色。这个阶段被称为“操作者的质量管理”。20世纪初,美国工程师泰勒(F.W.Taylor)首先提出了“科学管理”理论——“泰勒制度”。这套理论总结了18世纪末工业革命以来大工业生产的管理经验及实践,其主张计划与执行必须分开,于是检查产品质量的职责由工人转移到了工长手中,形成了“工长的质量管理”。这对当时的产品质量起到了很好的促进作用。到了20世纪30年代,随着资本主义大生产的蓬勃发展,工长已无力专门承担质量检查与质量管理的职责,因此,大多数企业都设置了直属于经理或厂长的专职检验人员和部门,由他们来承担产品质量的检验工作,负责全厂各生产部门的产品(零部件)质量管理工作,形成了计划设计、执行操作、质量检查三个方面都有专人负责的职能管理体系,那时的检验工作有人称为“检验员的质量管理”。至此质量管理还只限于对产品质量的检验,其主要手段是通过严格的检验程序控制产品质量,并根据预定的质量标准对产品质量进行判断。检验工作是质量管理工作的主要内容,其主导思想是对产品质量的“严格把关”。
质量检验管理阶段对于质量管理的创造在于,将计划、制造及检验分属在3个部门,达到了所谓“三权分立”的状态。设立专门的岗位负责制定标准(计划),有专人负责产品生产(制造),以及有专人按照标准检验产品质量(检验)。在这种状态下,产品质量标准就得到了有效的执行,各部门的责任也得到了严格的划分。
当然,这种质量检验管理也存在不足,主要集中在三点。第一点,质量检验管理对解决质量问题缺乏系统性,整个管理系统缺乏对质量问题的解决方法。第二点,质量检验管理只注重结果,而缺乏预防,对已完成的产品进行检验只产生了“把关”的作用,却无法“预防”和“控制”在生产过程中不合格产品的产生。一旦发现不合格品,很难进行补救,增加了生产成本。第三点,质量检验管理带来巨大的工作量。因为这种检验管理要求对产品进行100%的检查,对于大量产品的检验缺乏经济性和实用性。
(二)统计质量管理阶段
为了解决上述质量检验管理的不足,企业迫切需要找到控制不合格品的解决方案,而这就在客观上为数据统计的原理和方法引入质量管理领域创造了条件。早在20世纪20年代,就有一些统计学家和质量管理专家注意到了质量检验的弱点,并设法运用统计学的原理去解决这些问题。1924年,美国贝尔电话研究所的休哈特(W.A.Shewhart)提出了控制和预防缺陷的概念——“六西格玛”法则。这是一种改善企业质量流程管理的技术,以“零缺陷”的完美商业追求,带动质量大幅度提高、成本大幅度降低,最终实现财务成效的提升与企业竞争力的突破。根据“六西格玛”法则,人们逐渐发展完善了“质量控制图”和“预防缺陷”理论,其目的是预防生产过程中不合格品的产生,并确定了质量管理除了具有对产品质量检查监督的职能之外,还应具有预防产生不合格品的职能。
在随后的几年,陆续有更多的学者将数理统计方法引入了质量管理领域。例如,休哈特在1931年出版了《工业产品质量控制经济学》,贝尔电话公司的道奇(H.F.Dodge)和罗米格(H.G.Roming)在1929年发表了《挑选型抽样检查法》论文,瓦尔德(A.Wald)提出了“序贯抽样检验法”。然而,在当时这些理论和方法并没有引起重视,更没有被普遍推广。因为当时处于资本主义萧条时期,这种情况一直持续到第二次世界大战初期。
第二次世界大战初期,美国生产民用品的大批公司转为生产各种军需品,在这种情况下,质量检验管理的漏洞被无限放大,这也就导致了大批产品无法满足军方的要求,为军方提供的武器经常发生质量事故。为了解决这个问题,美国国防部联合上述学者一起制定和公布了《美国战时质量管理标准》,强制要求生产军需品的各公司、企业实行统计质量控制。实践证明,统计质量控制方法是在制造过程中保证产品质量、预防不合格品产生的一种有效工具,并很快地提高了美国军需品的质量。
统计质量管理阶段的主要特点是利用数理统计原理,预防不合格品的产生并检验产品的质量。质量管理职能在方式上由专职检验人员转移给专业的质量控制工程师和技术人员承担,质量管理由事后检验改变为预测、预防事故的发生。这标志着将事后检验的观念转变为预防质量事故发生的预防观念。这是质量管理理论的核心价值所在。
(三)全面质量管理阶段
20世纪50年代以来,随着社会生产力的迅速发展,科学技术及社会经济与文化的不断进步,质量管理环境出现了许多变化,主要体现在以下几个方面。
(1)人们对产品质量要求更高了。由于科学技术的发展,产品的精度和复杂程度大为提高,人们对产品质量的要求从仅注重性能指标转向可靠性、安全性、经济性等指标,对提高产品的可靠性等质量要求,仅靠在制造过程中应用数理统计方法进行质量管理是难以达到的。
(2)在生产技术和企业管理中广泛应用系统分析的理念,将质量管理看作处于较大系统中的一个子系统。
(3)管理理论有了新的发展和突破,在生产技术管理中广泛应用系统分析的理念和方法,并且越来越重视人的因素,出现了诸如“工业民主”“参与管理”“共同决策”等管理口号。这一切都促使质量管理从单一方法走向多种方法共存,从少数人参与走向公司全体人员共同参与。
(4)“保护消费者利益”运动的兴起,迫使质量管理方法进一步改进。
(5)随着市场竞争,尤其是国际市场竞争的加剧,各国企业都很重视产品责任和质量保证问题,因为大家都意识到质量关乎效益,更关乎企业的信誉。
统计质量管理相对于产品质量检验来说,无疑是质量管理发展史上的一次飞跃,但是,统计质量管理也有着其自身的局限性和不足之处。由于上述环境的变化,仅仅依靠质量检验和运用统计方法已很难持续保证与提高产品质量,把质量职能完全交给专业的质量控制工程师和技术人员去承担的方式也需要改进。因此,自20世纪50年代起,许多企业就开始了全面质量管理的实践(见图1-1)。

图1-1 全面质量管理实践