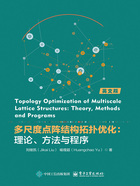
Chapter 1 Introduction to Topology Optimization for Additive Manufacturing
1.1 Introduction
Additive manufacturing (AM), also known as 3D printing, refers to the technology to fabricate parts layer by layer that has been greatly developed since 1980s. Compared with subtractive and formative manufacturing, AM has advantages in several aspects[1]. First, AM could fabricate parts with complicated details and the fabrication cost would not increase along with the complexity. Second, AM could compile with multiple materials, indicating the ability to fabricate parts with complex material compositions. Third, the fabrication procedure is totally automatic which makes it convenient to use AM. Users only need to focus on design of 3D models and their transition to AM machines. Due to these superiorities, AM has been widely applied to many fields such as biomedical, automobile and aerospace, etc.[2] For example, A cable mount on the front spar of the vertical stabilizer for Airbus A350 XWB was fabricated using AM[2]. Compared with the conventionally produced counterparts, the new design for AM [Fig.1-1(a)] is more integrated and compact through part consolidation and computational optimization. The assembly and installation time can be saved and a 30%weight reduction is achieved. Another case is demonstrated in Fig.1-1(b). A 3D printed patient-specific craniofacial implant designed by topology optimization is tested under masticatory forces to simulate chewing. The results show that the optimized shapes provide adequate load-transfer mechanism[3] while being lightweight.

Fig.1-1 AM application examples
To make full use of the advantages of AM technology, a series of design for additive manufacturing (DfAM) methods have been developed. Current DfAM can be categorized into three phases: system, part and process design[4]. System design includes assembly-level design of components and determination of manufacturing methods for the individuals. Part design refers to drawing the structural interior and exterior details for a single component. Part consolidation that simplifies multiple components into a single unit is also categorized to the part-level design. Process design refers to manufacturing process arrangement and optimization which may not be a typical design activity. Among the above three phases, part design is more focused by the design community since the product innovation generally happens at this phase and a number of novel structures demonstrating great physical and lightweight performances have been created through part-level computational optimization. In this book, some of the recently developed topology optimization methods for part-level design will be introduced.
Topology optimization can be used for creating novel structures for maximizing the physical performances under given conditions[5]. The optimized structure is described by element-wise topological variables which provides an extremely large design space. The gradient-based optimization method drives the topological variables towards the optimal solution. Conventionally, designs by topology optimization perform excellently but the organic structural geometries raise difficulties to manufacturing. Both subtractive and formative manufacturing can hardly deal with the interior structural details from topology optimization. The advent of AM technology unleashes the creativity of topology optimization and leads to the prosperous topology optimization research and applications. Hence, AM-oriented topology optimization research results are focused in this book and the manufacturability characteristics will be introduced alongside the technical contents.
The fundamentals of density-based and homogenization-based topology optimization[6] will be illustrated below to build the methodology foundation. Annotated MATLAB codes will be presented for the convenience of interested readers.