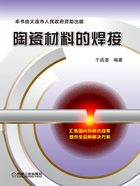
2.2 陶瓷与陶瓷及金属与陶瓷之间焊接性的改善
2.2.1 改善润湿性
金属对陶瓷的润湿性一般都很差,液态金属在典型陶瓷表面的接触角见表2-1。
1.活性金属法
(1)活性金属法焊接的机理 以前最重要的成果之一是采用了Cr、V、Nb、Ti、Zr等ⅣB族及ⅤB族金属或它们的合金用作钎料或过渡中间层,显著改善了润湿性及结合强度,人们把这类金属叫作活性金属。把这些元素加入Cu及Cu-Ag合金等的焊接方法叫作活性金属法。
活性金属的特征是对陶瓷元素有很强的亲和力,从而在钎焊或扩散焊的加热温度下,陶瓷能与这些活性金属之间发生化学反应形成一个反应层,作为媒介将陶瓷和金属连接为一体。还有所谓“楔子型”结构时也会有较高的结合强度。这个反应层的晶体结构、力学性能、厚度对金属与陶瓷焊接接头强度有影响,其厚度也有影响。厚度过大,反而会降低接头强度。如果产生的是脆性化合物,将对其结合强度产生不良影响。但减薄其厚度,就可以减轻这种不良影响。
Co虽然不是活性金属,但是,它与Si的化合物却具有良好的韧性。在SiC的钎焊中,采用Co-Si合金作为钎料,可以取得良好的效果。在1327℃以上的高温下,可得到高强度、耐热性、耐蚀性都很好的金属与陶瓷异种材料的焊接接头。
活性金属钎焊法,用得最多的是Ag-Cu系银钎料。银钎料中加入Ti或Zr作为活性金属(Ti最多),对于氧化铝、碳化硅、氮化硅、氮化铝等类陶瓷有良好的润湿性,可以用于多种金属与陶瓷的钎焊。这里就用银钎料钎焊碳化硅或氮化硅与金属的结合机构进行简单的说明。钎焊焊接接头的高温强度受到钎料熔点的支配。为了提高焊接接头的高温强度,应当选用Ni或Pd(钯)基的高熔点钎料,或者不用液相而用固相焊接。
表2-1 液态金属在典型陶瓷表面的润湿角

活性金属法焊接陶瓷是一种化学结合,它是利用在界面上发生扩散、固溶、化学反应等形成一种新物质,使之形成高强度的结合界面的一种材料连接方法。
元素向陶瓷的扩散对焊接工艺和焊接质量也有一定的影响,图2-6给出了一些元素在某些陶瓷中的扩散系数。

图2-6 陶瓷中一些元素的扩散系数
(2)焊接陶瓷所适用的活性金属的种类 最初以Al2O3陶瓷为代表的氧化物陶瓷采用活性金属法焊接。后来随着氮化物和碳化物等非氧化物陶瓷的应用,开发出不少相应的活性金属。焊接陶瓷所适用的活性金属,根据对陶瓷的分类列入表2-2。从表2-2可以看到,元素周期表中第Ⅳ族,特别是含Ti的活性金属占大多数,并加入Cu-Ag共晶成分,以降低熔点(如质量分数为2%的Ti-Cu-Ag为780℃),一般是作为硬钎焊的钎料;其次是第Ⅲ族Al及其合金也较多;另外,还有第Ⅴ族元素和少数其他元素也作为活性金属得到应用。这些活性金属元素在焊接材料中扩散,并在与陶瓷材料的交界面上与陶瓷发生反应而形成反应产物,以达到牢固的连接。
(3)活性金属中间层材料的形态 表2-2所给出的活性金属,会被制作成不同形态的中间层。表2-3为这些活性金属被制成中间层材料的形态。一般都呈箔片状、粉末状以及与其他金属混合。这些活性金属的含量可以根据需要随意控制,以得到最适宜的化学成分。
表2-2 陶瓷连接使用的活性金属(*为固相连接,其余为硬钎焊)

(续)

(续)

表2-3 活性金属中间层材料的形态

(4)适合的焊接加热方法 表2-4为结合能的供应方法,亦即适合的焊接加热方法。活性金属被加热到熔化,有利于促进界面反应。一般来说,几乎都是间接加热,即在真空或惰性气体保护下的电阻炉或高频炉内加热。最近出现了直流电结合(阳极结合)、有导电性能陶瓷的通电加热、摩擦加热等。
表2-4 结合能的供应方法

陶瓷与金属的焊接性取决于高强度结合界面的形成及其残余应力的下降。
(5)陶瓷与金属焊接结合界面的显微结构 如前所述,采用活性金属作为中间层来焊接陶瓷与金属,在陶瓷与活性金属界面上将会形成一种反应生成物而形成强固的结合。如采用Ag-Cu-2.2Ti活性金属作为中间层来焊接Si3N4陶瓷,Ti原子将在中间层熔液中扩散而偏析于Si3N4陶瓷侧,发生如下反应而形成化合物:

(6)活性金属法焊接接头的高温强度 活性金属法焊接陶瓷的接头强度,特别是高温强度是不令人放心的,尤其是硬钎焊。为了降低熔点,特别加入了降低熔点的元素。另外,为了充分利用陶瓷的耐热性,希望其焊接接头具有较高的高温强度。在实际的焊接接头中设计一个焊接残余应力缓和层,也能提高焊接接头的高温强度。
(7)典型活性金属钎料的性能
1)Ag-Cu-Ti活性金属钎料。
①Ag-Cu-Ti活性金属钎料与陶瓷的相互作用。Ag-Cu-Ti活性金属钎料已广泛用于陶瓷-陶瓷和陶瓷-金属的钎焊中,它不仅适用于Al2O3、ZrO2等氧化物陶瓷,也适用于SiC、BN、Si3N4等非氧化物陶瓷。表2-5为AgCu28Ti3活性金属钎料钎焊陶瓷-金属材料的接头抗拉强度。
表2-5 AgCu28Ti3活性金属钎料钎焊陶瓷-金属材料的接头抗拉强度

非氧化物陶瓷SiC、AlC、Si3N4等与氧化物陶瓷一样,靠活性元素Ti与陶瓷中的N、C扩散结合为TiN、TiC结合层,从而增强结合强度。图2-7给出了AgCu28Ti3活性金属钎料对几种陶瓷的润湿性。图2-8是AgCu28Ti3活性金属钎料与Al2O3陶瓷的结合界面。

图2-7 AgCu28Ti3活性金属钎料对几种陶瓷的润湿性

图2-8 AgCu28Ti3活性金属钎料与Al2O3陶瓷的结合界面
②Ti的活化作用。Ti与Al2O3、ZrO2陶瓷的活化作用并不是钎料中的Ti在结合界面上与Al2O3作用形成TiO,而是钎料在陶瓷表面发生了润湿行为,也就是说,并不是发生了氧化还原反应。因为即使在1800℃的高温,Ti与Al2O3、ZrO2陶瓷的反应自由能都是正值。
实际上,Ti与Al2O3、ZrO2陶瓷的活化作用是陶瓷中的失氧与Ti原子的扩散直接结合,即在钎焊温度下陶瓷中的氧化物分解的氧的扩散与Ti原子的扩散直接结合,其主要的能量是氧的扩散激活能。
2)高温含Hf活性钎料。北京航空工艺研究所研制了新的高温含Hf活性钎料,其化学成分为Ni-25.6Hf-18.6Co-4.5Cr-4.7W,其相组成见表2-6。它由γ(Ni固溶体)和NiHf相所组成,其固液相线分别为1195℃及1232℃。Hf是高温合金重要合金元素之一,可以提高中温强度的塑性;而且与其他金属间化合物不同,NiHf的显微硬度较低,具有一定的塑性。因此,这种钎料用于工程陶瓷与金属之间的连接是比较适宜的。
表2-6 新的高温含Hf活性钎料的相组成

该钎料中的Ni、Cr、Co均是高温合金的组成元素,且不含B、Si等脆性相形成元素。所以,钎料与高温合金的冶金相容性较好。钎料中的18.6%Co和4.7%W(质量分数)可显著提高钎焊接头的热强度。Hf在γ′相中的溶解度为7%(质量分数),Hf的加入有利于在钎缝金属中形成γ′相,从而提高其强度;另外,Hf又是碳化物形成元素。钎焊过程中,Hf与来自母材的C及Al形成MC2型碳化物和γ′相。它们的熔点分别为1260℃和1230℃,比NiHf相的熔点高。它们的形成消耗了一部分Hf,使钎料发生等温结晶,重新熔化的温度提高,这意味着钎焊接头使用温度提高。
(8)活性金属化的应用举例 表2-7给出了一些典型材料钎焊的主要工艺参数,表2-8给出了活性金属化的应用。
表2-7 一些典型材料钎焊的主要工艺参数

表2-8 活性金属化的应用

(续)

2.陶瓷烧结粉末金属化法
陶瓷烧结粉末金属化法种类繁多,采用较多的是Mo-Mn法。此外,还有Mo-Fe法、MoO2法、Mo-Ti法、W-Fe法、WO2-MnO2-Fe2O3法和MoO3-MnO2-Cu2O法,还有纯Mo、纯W、W-Y2O3、熔液金属法及氧化铜法等。
(1)Mo-Mn法陶瓷烧结粉末金属化法
1)金属粉末的配制。这种方法就是在陶瓷材料表面预先进行金属化的方法,也是最古老的一种方法。一般采用Mo-Mn、W-SiO2作为焊接材料。Mo-Mn法陶瓷烧结粉末金属化法是先在Mo粉中加入质量分数为10%~25%的Mn粉(在Mo粉中加入质量分数为10%~25%的Mn粉可以改善金属镀层与陶瓷的结合)混合后,加入适量的硝棉溶液、醋酸丁酯或草酸二乙酯等,经过球磨稀释后用毛刷刷涂或喷涂在陶瓷表面上,在高温氢气流中进行烧结,以使其表面形成一层Mo层(表2-9为常用的Mo-Mn法陶瓷烧结粉末金属化法的配方和烧结工艺参数)。金属化层厚度以20~35μm为宜,过厚的金属化层容易漏气,过薄的金属化层容易使强度下降。然后,为了改善钎料的润湿性而电镀Ni或Cu,再进行钎焊。镀镍层厚度一般为4~6μm,镀镍后的陶瓷应在1000℃氢气炉中保温15~25min而进行金属化。还有以W为主要成分的糊膏剂涂布于新鲜的氧化铝薄片上进行烧结而金属化的方法,制造出陶瓷外壳。采用陶瓷烧结粉末金属化法进行陶瓷表面金属化的工艺流程如图2-9所示。
表2-9 常用的Mo-Mn法陶瓷烧结粉末金属化法的配方和烧结工艺参数


图2-9 陶瓷表面金属化的工艺流程
2)粉末配方的调整。
①提高Mn含量。提高Mn含量可以降低烧结温度或者缩短保温时间。如将Mn含量从质量分数20%提高到50%,可以将烧结温度降低100℃。
②加入Ti。加入Ti可以降低Mn含量,也可以取代Mn而成为Mo-Ti法。Ti可以以TiO或者TiH的形式加入。由于Ti是一种活性元素,它可以提高钎焊过程的润湿性和接头强度。
③以Ni代替部分Mn。以Ni代替部分Mn,可以降低烧结温度或者缩短保温时间。
④以Si代替部分Mn。可以加入SiO2,其配方见表2-10。
表2-10 Mo-Mn-Si法陶瓷烧结粉末金属化法

Mo粉也可以以MoO3的形式加入。
金属化烧结条件也是影响金属化质量的重要因素。图2-10给出了表2-10中2、3号配方的金属化条件的曲线。

图2-10 表2-10中2、3号配方的金属化条件的曲线
3)涂(镀)Ni。涂(镀)Ni是金属化烧结之后很重要的一个工序,其主要作用是改善钎焊时的润湿性及缓解接头的残余应力。
镀Ni的方法很多,电镀、化学镀皆可,但是电镀比较方便。
常用的电镀液配方为NiSO4·7H2O140g/L、Na2SO4·10H2O50g/L、MgSO4·7H2O30g/L、H3BO320g/L和NaCl5~8g/L。镀Ni液的pH值一般为5~6。如果偏离此值,可以加入3%(指质量分数)的H2SO4溶液或者3%的NaOH溶液进行调整。阳极采用99.9%的纯Ni板。电流密度为0.5A/cm2,时间为40~50min,陶瓷零件电镀厚度约为4~6μm,金属零件电镀厚度约为10~20μm。
电镀Ni之后就可以进行钎焊。
4)影响Mo-Mn法金属化层质量的因素。金属化层质量直接关系到陶瓷材料钎焊接头的质量。影响金属化层质量的因素很多,除了金属化过程的条件之外,金属化粉末质量和陶瓷材料的质量也有明显的影响。
①陶瓷的影响。
a.陶瓷晶粒度的影响。以Al2O2陶瓷为例,其晶粒度在一定范围内,随着晶粒度的增大,烧结比较容易,钎焊接头强度提高。但是随着晶粒度的继续增大,钎焊接头强度又下降,存在一个最佳晶粒度。
b.陶瓷成分的影响。在晶粒度大体不变的情况下,陶瓷成分对接头强度也有明显的影响。图2-11给出了这种影响,表2-11为其化学成分。
c.金属化温度的影响。如图2-11所示,在一定温度范围内,金属化温度升高,接头强度也提高。

图2-11 Al2O2陶瓷成分和Mo-Mn法金属化温度对钎焊接头强度的影响
d.陶瓷表面状态的影响。陶瓷表面状态对金属化层质量有很大的影响。表2-12给出了表面状态对Al2O2陶瓷接头强度的影响。
表2-11 图2-11采用的Al2O2陶瓷成分(质量分数)和晶粒度

表2-12 表面状态对Al2O2陶瓷接头强度的影响

②粉末的影响。
a.Mo含量的影响。以Al2O2陶瓷为例,Mo-Mn法烧结金属化中Mo含量对金属化层质量具有明显的影响。试验表明,Mo粉质量分数为56%,其他质量分数在44%(MnO50-SiO230-Al2O320),在空气中进行烧结,烧结温度为1400℃,保温45min,可以得到满意的金属化层。
b.Mo粉末粒度的影响。Mo粉末粒度越小,接头强度越高。这可能是由于粒度小,堆积的表面能增大,烧结温度降低,有利于提高接头强度。
c.烧结前粉末涂层厚度的影响。烧结前粉末涂层厚度对Al2O2陶瓷钎焊接头强度有影响,存在一个最佳厚度。
③金属化烧结温度的影响。图2-12所示为质量分数94%的Al2O2陶瓷金属化烧结温度对钎焊接头强度的影响(图中烧结温度为Al2O2陶瓷的烧结温度)。

图2-12 94%的Al2O2陶瓷金属化烧结温度对钎焊接头强度的影响
1—1500℃ 2—1600℃ 3—1650℃ 4—1700℃
④金属化层的缺陷。金属化层出现缺陷的特征、原因和解决措施见表2-13。
表2-13 金属化层出现缺陷的特征、原因和解决措施

(续)

(2)Mo-Fe法陶瓷烧结粉末金属化法 此法可以用于滑石陶瓷、镁橄榄石陶瓷和Al2O3陶瓷等的金属化,其配方有Mo98-Fe2、Mo96-Fe4、Mo70-Fe30等。表2-14给出了Mo-Fe法陶瓷烧结粉末金属化法配方及烧结工艺参数。
表2-14 Mo-Fe法陶瓷烧结粉末金属化法配方及烧结工艺参数

(3)W-Fe法陶瓷烧结粉末金属化法 W-Fe法陶瓷烧结粉末金属化法是在Mo-Mn法陶瓷烧结粉末金属化法基础上发展起来的,其金属化工艺程序也与Mo-Mn法基本相同。W-Fe法配方比较简单,主要是W90-Fe10,再配以硝棉、醋酸乙酯等,混合后涂于陶瓷表面,厚度为25~50μm。
在这个配方中还可以加入Mn、TiO2、MgO等,用这些配方进行BeO陶瓷表面金属化的条件见表2-15。
表2-15 BeO陶瓷表面金属化的条件

(4)WO2-MnO2-Fe2O3法陶瓷烧结粉末金属化法 采用配方WO392.7-MnO26.2-Fe2O31.1折算为W94-Mn5-Fe1,进行陶瓷烧结粉末金属化时,可以制成膏剂,配方折算为WO3100g、MnO26.7g、Fe2O31.2g,配以硝棉溶液2.5mL,环烷酸2.5mL,再加入丁基溶液(相对分子质量为118.7,沸点为170.6℃)65mL。将此膏剂研磨成2μm的微粒在氢气环境中进行900~1150℃的烧结,无须镀镍,就可以直接进行钎焊。
(5)MoO3-MnO2-Cu2O法陶瓷烧结粉末金属化法 采用此法的材料配方为MoO395-MnO25-Cu2O0.1,研磨MoO3为4μm,MnO为1μm,混合后加入硝棉溶液及草酸二乙酯制成膏剂,涂在陶瓷表面35~50μm的厚度。可以将选择的钎料直接加在这一涂层上。根据钎料的熔点确定金属化烧结温度。如果采用Ag基钎料,其金属化烧结温度可以为900~1150℃,保温1~1.5h。
采用此法钎焊94%~99.5%的Al2O3陶瓷,其抗拉强度可达80~100MPa。采用MoO3-MnO2-Cu2O法进行陶瓷烧结粉末金属化的条件和接头抗拉强度的试验结果见表2-16。
(6)氧化铜法 它是将Cu2O94.2-Al2O35.8的粉末在空气中加热1250℃保温0.5h进行烧结,冷却后粉碎,然后喷涂到陶瓷表面上,再与金属化涂层一样,加热到涂层熔点以上的温度在氧化性气氛中进行烧结,冷却凝固后,在还原性气氛中加热到1000℃,便在陶瓷表面形成一层铜的金属化层,可以直接进行钎焊。
(7)硫化铜法 此法是将硫化铜+高岭土制成膏剂,涂在陶瓷表面,在空气中加热到1200~1300℃。在加热过程中还可以在涂层上添加Ag2CO3,而使之表面银化,其钎焊接头强度可达48MPa。
(8)纯Mo、W法 纯Mo、W粉末烧结法是一种采用纯金属Mo粉、W粉对陶瓷进行金属化的方法。
表2-16 采用MoO3-MnO2-Cu2O法进行陶瓷烧结粉末金属化的条件和接头抗拉强度的试验结果

①抗拉件本身断裂值。
以Mo为例,将纯金属Mo粉加入硝棉溶液和醋酸乙酯混合后涂在Al2O3陶瓷表面,在露点40℃的氮气+氢气氛围下,加热到1450~1500℃,保温1h,就可以得到牢固的金属化层。镀镍后,采用Ag-Cu共晶钎料,在氢气中加热到790℃,保温5min,可以得到抗拉强度为47MPa的接头。
(9)MoO3法 钎焊Al2O3陶瓷时,将MoO3用黏结剂调和后涂在陶瓷表面,在氢气中进行1750℃、保温5min的烧结,可以获得多孔的Mo金属层。镀Ni后,即可进行钎焊。
采用MoO3法进行陶瓷表面金属化比用纯Mo的效果好。
(10)WO3法 此法与MoO3法相似,在氢气中进行1850℃、更长时间保温的烧结,比采用纯W的效果好。
表2-17给出了采用金属粉末烧结法进行陶瓷表面金属化的配方和工艺。
3.蒸气附着法
蒸气附着法是在真空(4×10-3Pa)条件下先将陶瓷焊件预热(300~400℃保温10min),再在陶瓷材料表面用金属蒸气或离子气使陶瓷材料表面金属化。可以作为蒸发材料的有Mo、Ti、Al等的单层蒸发和Ti/Mo/Cu的多层蒸发。多层蒸发是先蒸镀钛,再蒸镀钼,在钛、钼镀层上再镀0.2μm厚度的镍。最后在真空炉中用无氧纯铜片或者AgCu28钎料与陶瓷进行钎焊。蒸气附着法的优点是金属化温度低,能适于各种陶瓷的金属化,陶瓷不会有变形及破裂的危险。表2-18给出了部分金属材料的蒸发温度。
4.溅射沉积法
它是将陶瓷放入真空容器中并充以一定压力的氩气,然后在电极之间加上直流电压,形成气体辉光放电,利用气体辉光放电产生的正离子轰击靶面,把靶面材料溅射到陶瓷表面上形成金属薄膜,从而实现金属化。沉积到陶瓷的第一层金属化材料是钼、钨、钛、钽或铬等;第二层金属化材料是铜、镍、银或金。在溅射过程中,陶瓷的沉积温度应保持在150~200℃。
表2-17 采用金属粉末烧结法进行陶瓷表面金属化的配方和工艺

(续)


(续)


(续)


(续)


(续)

注:1.所收集的是生产实用的或者经经验证明是较好的配方。
2.表中列出的相应工艺条件是较好的条件,具体试验过程及工艺条件的范围请查阅有关参考资料。
3.表中所列连接强度一般指抗拉强度,若为其他强度则加以注明。
4.配方组成后面有时列出微米数,是涂层厚度数值。
5.列表顺序大体是按金属化温度高低排列的。1600℃以上为高温,1200~1600℃为中温,1200℃以下为低温金属化。
表2-18 部分金属材料的蒸发温度

与蒸镀法相比,溅射法操作简单,涂层厚度均匀,与陶瓷结合牢固,可涂覆大面积的金属膜,还能制造合金或氧化物薄膜,能在降低的沉积温度下沉积高熔点金属层,可适合任何种类的陶瓷。
表2-19给出了不同溅射沉积材料和溅射金属化层厚度对钎焊接头强度的影响,表2-20所示为陶瓷表面状态对钎焊接头强度的影响。
表2-19 不同溅射沉积材料和溅射金属化层厚度对钎焊接头强度的影响

表2-20 陶瓷表面状态对钎焊接头强度的影响

溅射沉积法有直流溅射、高频溅射和磁控溅射等;直流溅射又可以分为二极溅射、三极溅射和四极溅射,其中,二极溅射最为简单,也最为常用。
图2-13和图2-14所示分别为二极溅射和四极溅射装置示意图。四极溅射除了阳极和阴极之外,还有一个辅助阳极和磁场线圈。

图2-13 二极溅射装置示意图
5.热喷涂法
图2-15所示为低压等离子弧热喷涂系统示意图,是在Si3N4陶瓷表面喷涂两层Al的方法。喷涂第一层时将陶瓷预热到略高于Al熔点的温度,以获得Al对Si3N4陶瓷(因为形成了AlN的缘故)较强的吸附,此时喷涂的Al层不会太厚,约2μm。在此基础上再喷涂第二层200μm的Al层。喷涂Al层后的Si3N4陶瓷就以Al层在700℃×15min、加压0.5MPa的条件下进行钎焊。

图2-14 四极溅射装置示意图

图2-15 低压等离子弧热喷涂系统示意图
6.离子涂覆法
图2-16所示为低真空离子涂覆法装置原理图。作业时,将陶瓷放在阴极上,涂覆材料作为阳极,成为蒸发源,通以3Pa的氩气,加上1~5kV的高压。先轰击工件5~15min,使之表面光滑清洁,然后再蒸发活性金属Ti、Al等进行离子涂覆,达到250~500Å之后,再蒸发一层Cu或者Ni,达到一定厚度并对表面进行处理后,就可以进行钎焊工序。

图2-16 低真空离子涂覆法装置原理图
7.离子注入法
由于活性钎料中的活性元素一般是Ti,它会使钎料变硬、变脆,而且,接头中也会出现脆性相。为克服这些缺点,可采用离子注入法直接将活性元素Ti注入陶瓷(如Al2O3陶瓷)中,使陶瓷形成可以被一般钎料所润湿的表面。以高纯Al2O3陶瓷为母材,MEVVA离子源的发射电压为40kV,当离子注入范围为2×1016~3.1×1017个/cm2时,Ti的注入深度可达50~100nm。经过离子注入后的陶瓷表面显著改善了非活性钎料的润湿性,用Ag-Cu非活性钎料对陶瓷表面的润湿性可以达到与活性钎料相同的程度。离子注入后的陶瓷表面改善非活性钎料的润湿性的原因有三:一是离子注入Al2O3陶瓷表面后更加金属化,导电性提高,并呈现金属光泽,减少了陶瓷与金属之间的电子不连续性;二是离子注入陶瓷表面产生缺陷,使陶瓷表面能提高,可以促进润湿;三是离子注入陶瓷表面形成了改善导电性及促进润湿的新相。