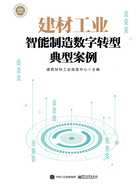
壹 应用篇
智能工厂
01 玻璃纤维智能制造示范工厂——巨石集团有限公司

企业简介
巨石集团有限公司位于浙江省桐乡市,是中国建材股份有限公司玻璃纤维业务的核心企业,以玻璃纤维及制品的生产与销售为主营业务。该公司在浙江桐乡、江西九江、四川成都、埃及苏伊士、美国南卡罗来纳州设有五个生产基地,在美国、加拿大、南非、法国、意大利、西班牙、日本、韩国、印度等地设立了14家海外销售公司,已建成玻璃纤维大型池窑拉丝生产线20多条,玻纤纱年产量达200万吨。公司玻纤产品品种较多、品类齐全,有100多个大类近1000个规格的品种,主要包括无碱玻璃纤维无捻粗纱、短切原丝、短切毡、方格布、电子布等玻纤产品。该公司拥有具备自主知识产权的大型无碱池窑、环保池窑的设计和建造技术。
案例实施情况
总体设计
巨石集团有限公司玻璃纤维智能制造生产线,总体设计以产品全生命周期的相关数据为基础,在计算机环境中,对整个生产过程进行仿真、评估和优化,并进一步扩展到整个产品生命周期的新型生产组织方式。以“年产30万吨玻璃纤维智能制造生产线扩建项目”为实体,项目实行一次规划、分期建设。该公司根据“横向到边、纵向到底”的架构设计,进行了基础数据的一致性管理;打通各层级系统间数据;设备自动化数采;研发、建立工艺模型;实现生产运营模拟仿真,优化生产运营。项目信息端横跨SAP、ERP、MES、SRM等系统,与海关、银行、保险、税务、物流等外部平台无缝衔接,实现运营、制造、控制一体化管理。

总体架构设计图
实施内容与路径
1.系统模型建立与运行
该公司开展了包括工艺模拟、产品研发、设备运行建模、生产装备建模等多个方面的仿真模拟。
工艺模拟方面:从设计上采用了自行研发的工艺数字化中心系统,将各个工序的工艺进行模块式的建模维护。
研发结合工艺数据和小试产品进行结果验证,开展多层次试验,观测此工艺对其他玻纤性能指标的影响。

研发模拟与试验说明图
设备运行方面:在正式生产环境中,依据正式量产的工艺参数,对比实时在线采集的生产数据,模拟校准与预警,修正个别精度与量产误差。

生产监控与模型执行图
生产装备配有大量数字传感设备,收集位置、温度、风速、流体等数据,结合仿真软件,进行在线监控和可视化展示。

热力流体图
其他工序的主要设备,同样以传感器采集的数据为基础,构建模拟依据。以大型短切机为例,模拟的内容主要包括刀片与皮辊接触量、短切长度、喷雾压力等关键指标,以可视化界面进行展示。
2.数据采集与监控系统建立与运行
数采建设以MES为核心,整合生产、执行、质量、工艺数据,向上与ERP等系统集成,向下与SCADA系统集成。SCADA主职生产执行层,通过对玻纤生产工序的设备与通信改造,在车间集控室进行反向控制。MES主职业务控制层,支持包括生产计划、执行进度、工艺标准、制造监控等功能。
3.先进控制系统建设与运行
(1)工业大数据集中控制中心
工业大数据集中控制中心,通过对每个工序和作业点的可视化监控及生产实时数据的采集和分析,实现了集生产状态远程监控、产量报表自动生成、质量数据实时监视、订单实时跟踪等功能为一体的统一管控平台。

工业大数据集中控制中心
(2)工段分布式控制管理
与上述工业大数据集中控制中心进行对接,实现分工段详细控制,通过大屏对标看板,分析生产过程中的不足,营造工厂内部良性竞争环境,提高生产、制造、创新的积极性。

络纱效率对标看板
物料方面,通过对原料的数控管理,建立自动化投料模型,提高原料投入的合理性和科学性。

化工原料
4.生产研发数字化协同建设与运行
(1)产品研发
玻璃纤维产品,以玻璃纤维的各项性能指标为主要产品价值。该公司依托玻璃纤维国家级实验室,以虚拟工艺数据库为核心,将各项影响产品性能的指标进行分类定标,下达试样工艺,结合检验记录投入模拟。
(2)计划调度
通过ERP系统实现生产计划与销售计划的协同、物料需求计划(MRP)、工艺控制、生产调度、生产领料、生产消耗报工、产品入库及生产进度信息跟踪等工作的系统管控。

工艺计调排产协同图
(3)生产制造
通过对ERP与工艺、MES、SCADA等制造执行系统的集成,实现将工艺指导文件、生产配方的集中管理、统一下发,同时通过自动化改造,实现生产设备的反向控制,工艺参数及生产指令可自动下发到现场生产设备。

生产作业流程图
通过SCADA系统对生产数据的实时采集,建立数据分析模型,实现对生产作业、生产资源、制造过程等关键数据的动态监测,并进行优化分析。

数采与动态控制图
案例特点
该公司开创了玻璃纤维的“采购—订单—排产—工艺—生产—出入库”全流程数字化生产模式;充分发挥信息系统横向集成、纵向贯通的优势,实现销售订单全过程跟踪、生产进度全程跟踪、生产调度优化排程、生产工艺自动匹配、产品质量管理追溯、物流状态实时可见的目标;完成人、财、物等核心业务的集约化、标准化管理,落实集团一体化管控模式,全面提升管理水平;以“经营模式专业化、核心业务集中化、业务流程标准化、资源能力共享化”为目标,为国际化发展战略提供有效的系统支撑。该公司围绕网络化、数字化、智能化等方面开展的玻璃纤维行业新型智能生产模式探索,为我国乃至全球玻璃纤维行业的发展树立了标杆和典范。
实施效果
经济效益
(1)提高管理水平和工作效率,用工人数大幅减少,每年节省人工成本1000万元以上。
(2)实现产、销、研的科学整合,集团的产品创新能力得以提升,产品生产成本降低12.03%,产品研发周期缩短9.8%,生产效率提高23.55%,不良产品率降低54.92%,吨纱能耗下降20.69%,并实现了对现有产品的持续完善。
(3)智能化工厂的建设,改变了集团传统的生产模式,生产力明显提高,生产成本随之降低。
(4)总部统一控制ERP系统,统一操作权限、统一管理流程、统一管理综合业务和信息门户,使企业的管控模式进一步转变,管控能力进一步增强。
(5)随着信息化系统与现场工控系统的整合对接,集团各业务单位工作数据准确率在原有基础上有效提高,数据准确率在99.9%以上,工作质量有效提高。
(6)产、销、研的智能整合,质量系统的综合应用,实现了新材料的替代,排放物质量的有效控制,大大减少了生产过程中污染物的排放,产品优等品率持续提高。
社会效益
(1)该公司水、电、气等能源得到实时监控,使用量得以有效控制,为国家节能减排做出了贡献。
(2)通过信息化系统的实时自动管理,提高了一线工作的舒适性和安全性,员工幸福感进一步提升。
(3)该公司与利益相关方、国家财政部门建立了良好的业务关系和业务生态系统,实现了产业链的良性循环。
(4)以两化融合为手段的全新生产经营管理模式,为同类企业,特别是跨国集团管控型企业提供了宝贵的经验。
(5)全面落实“四个全面”的发展要求,加快了企业两化融合的发展,提高了员工素质,加快了企业精神文明建设的步伐。
指标提升
(1)生产成本降低12.03%。2017年公司其他生产线吨纱生产成本为3050.72元/吨,2019年项目生产线吨纱生产成本为2683.62元/吨,生产成本与公司平均水平相比降低了12.03%。
(2)产品研制周期缩短9.8%。研发周期的大幅度缩短得益于生产工艺仿真及优化的实施,在研发中借助生产工艺仿真与优化的新技术、新方法,在减少研发费用的同时,实现了研发周期的大幅缩短。
(3)生产效率提高23.55%。该公司2019年的生产效率与2017年相比提升了23.55%,生产效率的提升得益于智能制造新技术的大规模应用,在提高产能和工业总产值的同时减少了用工人数。
(4)产品不良率减低54.92%。通过实施以网络化、数字化等新技术为基础的智能制造新模式,以数据为支撑,以数字化改造为手段,在提高效率的同时提高了产品合格率,2019年不良品率与2017年相比降低了54.92%。
(5)能源利用率提高20.69%。该公司2019年项目生产线单位产量消耗能源与2017年其他生产线相比降低了20.69%。能源利用效率的提高,得益于对生产流程中各种能源消耗等数据的实时采集,并经过集团大数据中心的分析,优化生产工艺与流程,在降低能耗的同时降低生产成本,提升经济效益。